What Is Powder Coating
Powder coating is applied to the surface finishes of various metal parts to provide a durable and attractive finish. Under the action of static electricity, the powder will be evenly adsorbed on the surface of the workpiece to form a powdery coating; the powdery coating will be leveled and cured after high-temperature baking to become a final coating with different effects (different types of powder coating effects); The spraying effect of powder spraying is better than that of spraying process in terms of mechanical strength, adhesion, corrosion resistance, and aging resistance, and the cost is higher than that of the spraying process.
Powder Coating Effects
Matte Finishes
Matte finishes in powder coating have a low-gloss or non-reflective appearance. They provide a flat or satin-like finish with minimal shine. These finishes are achieved using specially formulated powder coatings containing additives or pigments to reduce the gloss level. Matte finishes are famous for their understated and contemporary look. They can create a smooth, uniform appearance on surfaces while minimizing reflections and glare.
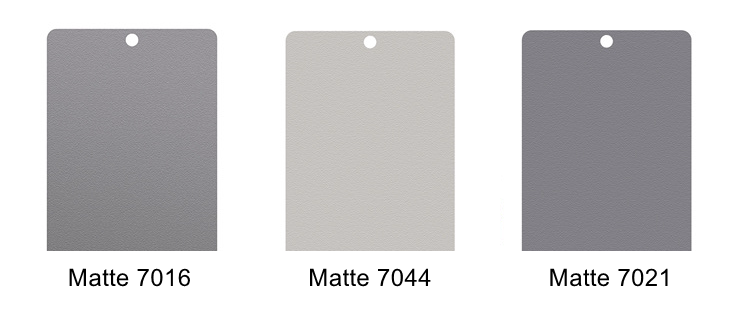
Orange Peel Texture
The term "orange peel" is commonly used in powder coating to describe a specific surface texture or appearance resembling an orange peel. It refers to a textured surface finish characterized by small, dimpled bumps or waves. The orange peel effect can occur during the powder coating process and is typically considered undesirable.
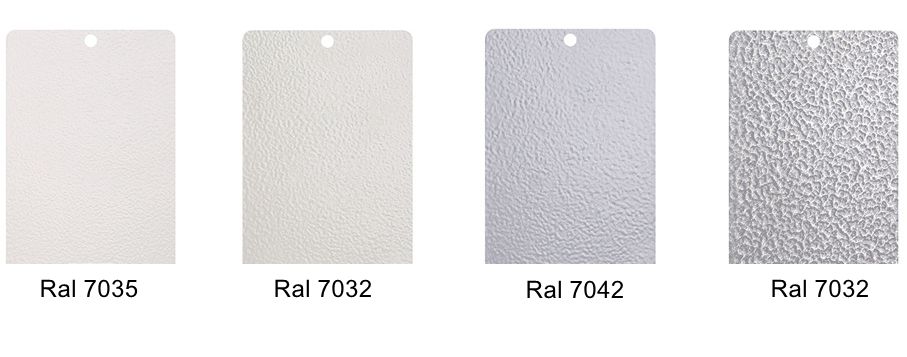
Glossy
Using a high-gloss powder formulation can result in a glossy appearance directly from the powder coating process. High-gloss powders contain special additives that promote a shiny finish.
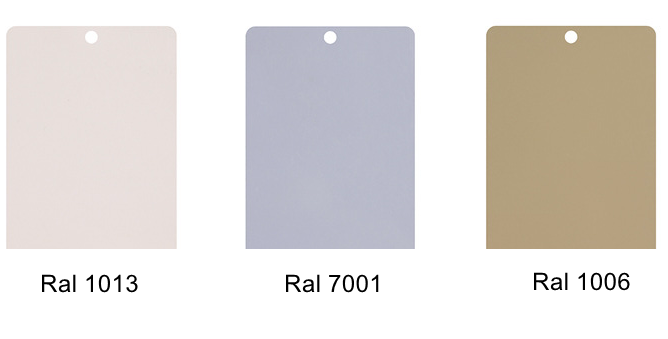
Benefits of Powder Coating
The primary function of powder coating is to provide a protective and decorative finish to various metal surfaces. Here are some specific functions and benefits of powder coating:
Protection
Powder coating forms a durable barrier that protects metal surfaces from corrosion, rust, abrasion, and wear. It provides a robust layer that helps extend the coated object's lifespan.
Aesthetics
Powder coating offers a wide range of colors, textures, and finishes, allowing for customization and enhancing the appearance of the coated item. It can create smooth, glossy, matte, metallic, or textured finishes, adding visual appeal.
Durability
Powder coating is known for its toughness and resistance to chipping, scratching, fading, and chemicals. The cured powder coating creates a hard, resilient surface that can withstand harsh environmental conditions.
Environmental friendliness
Unlike liquid coatings, powder coatings do not contain solvents that emit volatile organic compounds (VOCs) into the atmosphere. It is considered more environmentally friendly and complies with stricter environmental regulations.
Efficiency
The electrostatic powder coating application allows for high transfer efficiency, minimizing waste and reducing overall material usage. Excess powder can be collected and reused, making the process cost-effective.
Fast curing time
Powder coating generally has a relatively quick curing time compared to traditional liquid coatings. Once the powder is heated, it melts and fuses rapidly, reducing processing time.
Versatility
Powder coating can be applied to various metal substrates, including steel, aluminum, iron, and galvanized metals. It suits various industries, from automotive and appliances to furniture and architecture.
Inspection of Powder Coating Parts
Film thickness test
The film thickness test is an important quality control measure conducted on powder-coated parts to ensure that the applied coating meets the desired thickness specifications. It determines the thickness of the cured powder coating film on the part's surface.
The film thickness is typically measured using specialized instruments called coating thickness gauges. Two common types of gauges used for powder coatings are magnetic induction and eddy current gauges. These gauges are designed to measure the thickness of non-destructive dry film.
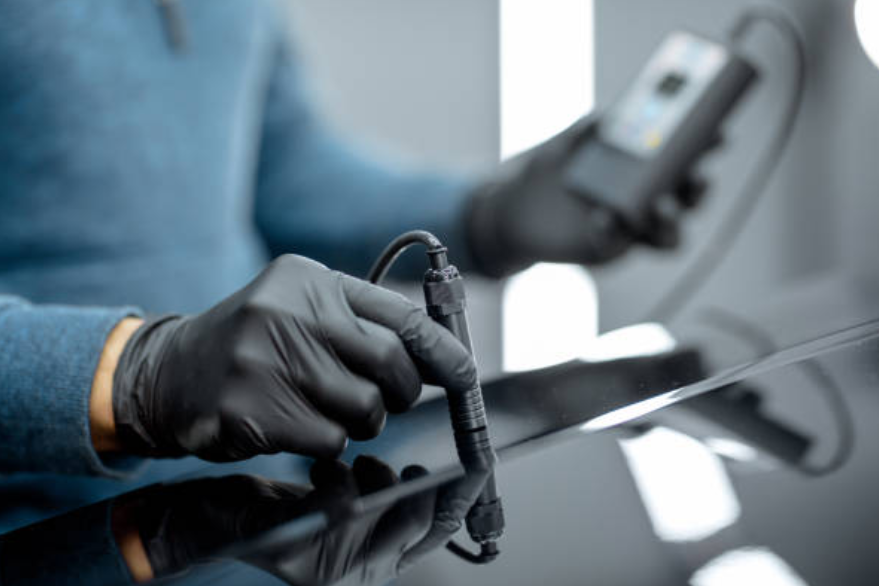
100 Grid test
Use a utility knife to draw a line every 1mm in 100m㎡ (see the substrate for depth), draw 100 squares crosswise, and stick 3M#600 Scotch adhesive tape 10-13mm or compatible adhesive tape to the test area. Instantly and quickly tear off the paint on the test surface in a vertical direction without falling off 5%
Hardness test
A 2H pencil applies a force of 1KG at a 45-degree angle, pushing the front ruler 15-30MM. After the eraser is erased, it is qualified, and there is no leak. Slight traces are allowed. For the test surface along the direction of 45 degrees, apply a force of 1KG to draw a straight line of 8 cm on the surface of the baking paint. The surface should not be damaged or scratched, and slight traces of paint are allowed. Reference room temperature hardness: above 3H.
Solvent resistance test
Dip a cotton swab with 99.8% anhydrous alcohol back and forth 50 times with one force. Except for a slight change in gloss, the coating must not change color, swell, or peel off; or use a clean cotton cloth to moisten a clean solvent (industrial alcohol) 95%); Wipe the test surface back and forth 50 times with a force of 500g. The test surface must not be discolored, peeled off, lifted, or tarnished; the gloss may vary slightly.
Impact test
A 500g weight with a cross-sectional area of 1/4 falls freely from 500mm, and the coating is qualified if it does not fall off or crack. Also helpful in falling ball test: falling ball test (use a solid ball with a diameter of 1.5CM and a hollow rod with a length of 1.5M to test the strength and adhesion of the paint). Or carry out on the QCJ type paint film impactor (1 kg heavy hammer falls freely at the height of 500mm and impacts, and there must be no cracks or peeling off of the sprayed layer).
Wear resistance test
use a sponge brush; brush 5000 times; do not expose the hard side of the material. Add a width of 30mm, a load of 500g, a distance of 55mm, and brush back and forth 60 times/min; or Great Wall Eraser 500g Back and forth 50 times with no bottom leakage.
Corrosion resistance: no change in salt spray resistance for 1000 hours; no change in heat and humidity resistance for 500 hours; or salt water spray without bubbles and rust (5% salt water at 35 degrees Celsius, continuous spray for 400 hours)
评论
发表评论