Brief Overview Of Progressive Die Stamping
Progressive die stamping is a high-speed, high-volume sheet metal stamping process that produces intricate metal parts. It involves using a series of dies (or tools) arranged in a sequence along a single strip of material. As the strip advances through the die, different operations like cutting, bending, punching, and shaping are performed at each station. It allows for the simultaneous creation of multiple features in a single pass, enhancing efficiency and precision.
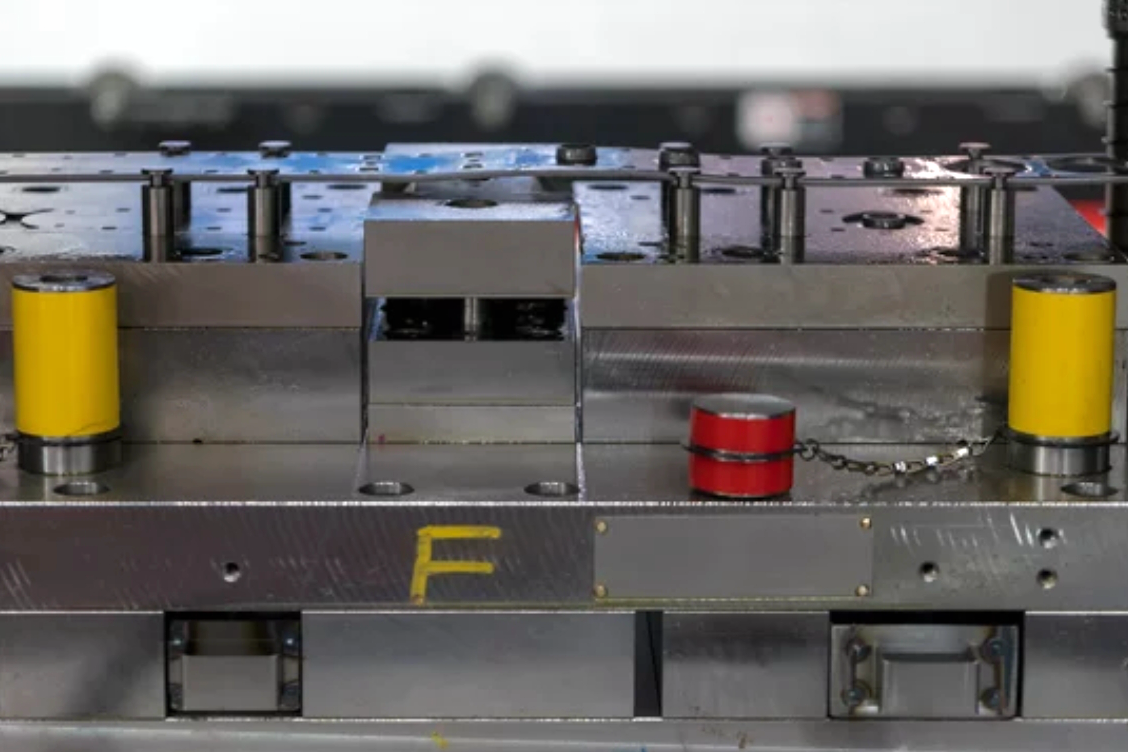
The process begins with a coil or strip of metal being fed into the progressive die. Each station performs a specific operation on the material as it moves through the die. For instance, one station might cut the material to a particular shape, while the next might bend or punch holes. It continues until the final product is fully formed.
Progressive die stamping offers several advantages, such as high-speed production, consistent part quality, and cost-effectiveness for high-volume runs. Additionally, it enables complex parts to be manufactured with tight tolerances and minimal waste.
Neway, leveraging its expertise in sheet metal fabrication, employs progressive die stamping as part of its one-stop service for creating custom metal parts. This method aligns with the company's commitment to delivering precision-engineered components efficiently and accurately to meet diverse customer requirements.
Importance Of Progressive Die Stamping In Manufacturing
Progressive die stamping is pivotal in modern manufacturing, offering several advantages that contribute to its widespread adoption in various industries. Understanding the importance of progressive die stamping is crucial for manufacturers and clients seeking efficient and cost-effective solutions.
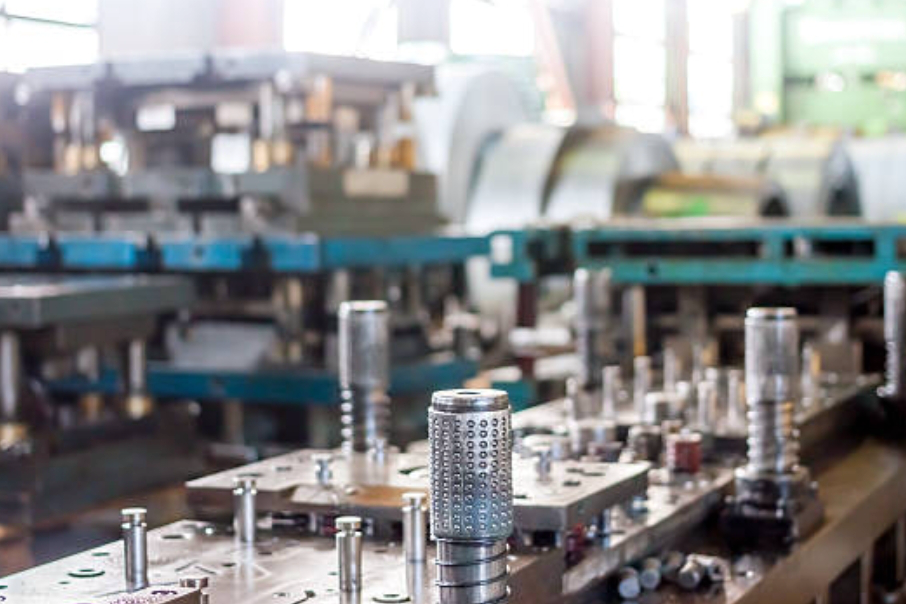
High Efficiency and Speed:
Progressive die stamping is known for its high-speed production capabilities. The sequential nature of the process, with multiple operations co-occurring, leads to significantly reduced cycle times. This efficiency is vital for meeting enormous production demands within tight timelines.
Precision and Consistency:
The progressive die setup ensures precise control over each operation, resulting in consistent part quality. The ability to perform multiple tasks in a single pass minimizes variations, contributing to the production of accurate and uniform components.
Cost-Effectiveness for High Volumes:
Particularly advantageous for high-volume manufacturing, progressive die stamping reduces per-unit costs. The efficiency of the process, combined with minimized material waste, enhances cost-effectiveness and makes it an economically viable option for mass production.
Complex Part Production:
Progressive die stamping is well-suited for creating complex parts with multiple features. Its ability to integrate various operations seamlessly allows for fabricating intricate components that might be challenging or time-consuming using other methods.
Minimized Material Waste:
The process optimizes material usage as the strip progresses through each station with minimal scrap generation. It aligns with sustainable manufacturing practices, reducing material waste and contributing to a more environmentally friendly production process.
Versatility in Material Selection:
Progressive die stamping is adaptable to various materials, including metals like steel, aluminum, and copper. This versatility allows manufacturers to choose materials based on specific application requirements without compromising the efficiency of the stamping process.
Enhanced Automation and Consistent Output:
The progressive die stamping process lends itself well to automation, ensuring a streamlined and repeatable manufacturing workflow. Automation improves production speed and reduces the likelihood of errors, resulting in a consistently high output quality.
Neway leverages the importance of progressive die stamping in custom metal parts manufacturing as part of its comprehensive service. The company's commitment to efficiency, precision, and cost-effectiveness aligns with the inherent benefits of progressive die stamping. It is an integral component of Neway's one-stop solution for clients seeking quality custom parts at scale.
Basics Of Progressive Die Stamping
Progressive die stamping is a highly efficient metal forming process employed in manufacturing, and it plays a crucial role in the production of custom metal parts, aligning with Neway's expertise. This method falls under the umbrella of sheet metal fabrication, showcasing the diversity of Neway's capabilities.
Definition and Key Features
Progressive die stamping is a precision metalworking technique where a continuous strip of material passes through multiple stations within a die. Each station performs a specific operation, such as cutting, bending, or shaping, resulting in the gradual formation of the final part. The strip advances through the die incrementally, undergoing successive operations until the desired part is fully formed.
The Progressive Die Stamping Workflow
Step-By-Step Explanation Of The Process
Design and Engineering:
The process is initiated with meticulous design and engineering. Engineers at Neway utilize advanced CAD software to create detailed blueprints of the progressive die. This crucial step ensures precision and accuracy in the final product.
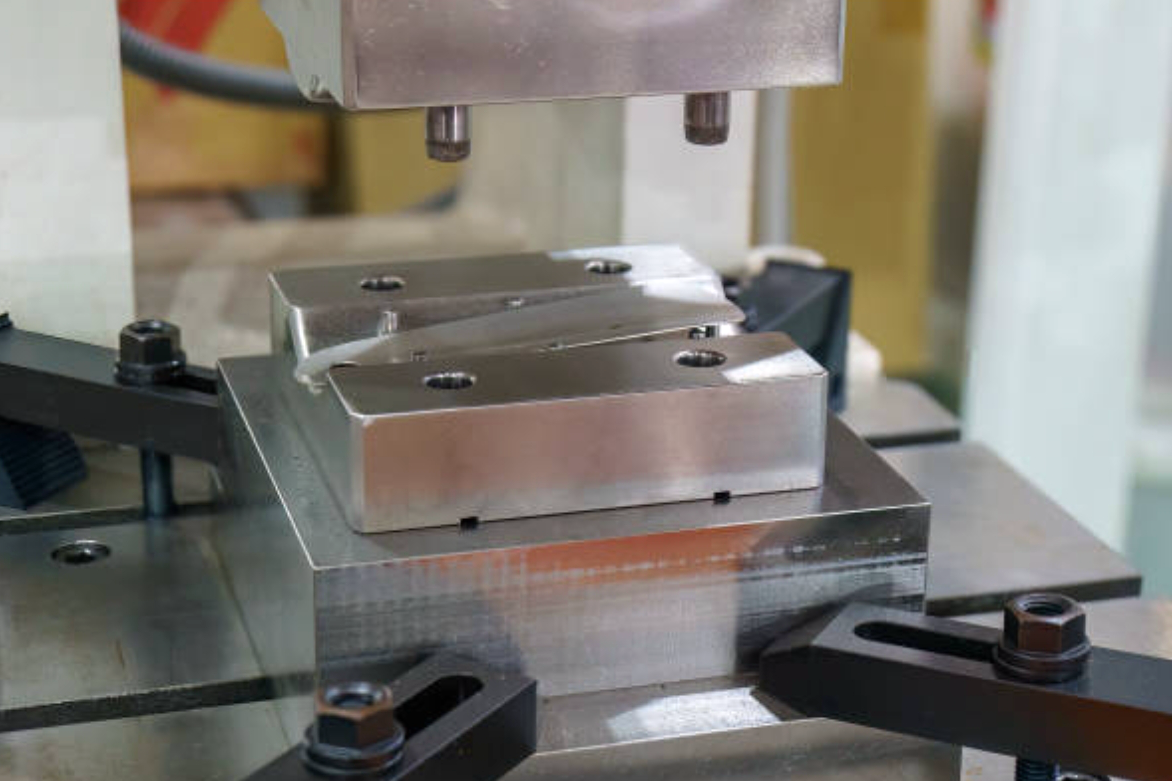
Material Selection:
The next step involves selecting the appropriate material for the specific part. Neway's expertise lies in working with various metals, ceramics, and plastics, offering various options to meet diverse requirements.
Tool and Die Creation:
The tool and die are crafted once the design is finalized and materials are chosen. This progressive die tool is a specialized metal block with multiple stations. Each station performs a specific cutting, bending, or shaping task.
Setup of Press Machine:
The progressive die is mounted onto a press machine. Neway's state-of-the-art facilities boast advanced machinery capable of high-speed and precision stamping. The setup is crucial for seamlessly executing the progressive die-stamping process.
Feeding Material into the Die:
Raw material, typically in the form of a coil or sheet, is fed into the press. The progressive die functions step-by-step, with each station performing a specific operation as the material advances through the die.
Progressive Stamping Operations:
Various operations occur as the material progresses through the die stations, such as cutting, bending, and shaping. This progressive approach enables the creation of complex and intricate parts in a single pass.
Quality Control:
Neway prioritizes quality at every stage. Throughout the progressive die stamping process, rigorous quality control measures are implemented to ensure that each part meets the specified standards and tolerances.
Final Inspection and Finishing:
Once the stamping process is complete, the parts undergo a final inspection. Neway's commitment to excellence ensures that the finished products are defect-free and adhere to the required specifications. Any necessary finishing touches, such as coating or deburring, are applied.
Packaging and Delivery:
The final step involves careful packaging of the stamped parts for safe transportation. Neway's streamlined logistics ensure timely delivery to clients, completing the end-to-end workflow of progressive die stamping.
Comparison Between Four Types of Stamping Processes
Deep Drawn Metal Stamping
Progressive die stamping and deep-drawn metal stamping are two distinct yet efficient methods in metal part manufacturing. Each process has its unique characteristics, applications, and advantages, contributing to the versatility of Neway's one-stop service.
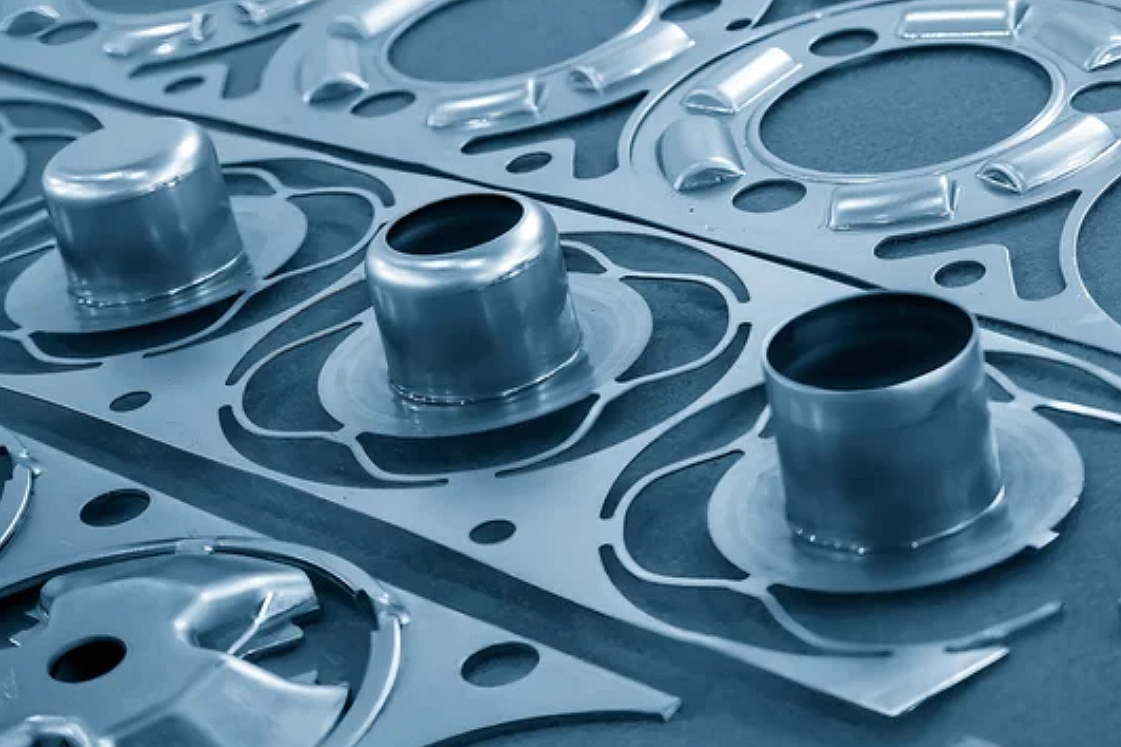
Progressive die stamping is a precision metal stamping method that involves a series of stations with different operations. The metal strip advances through these stations, gradually forming the desired shape with each step. This process is ideal for high-volume production runs, offering speed and cost-effectiveness. Neway's expertise in progressive die stamping ensures accurate and consistent results, making it a preferred choice for various industries.
On the other hand, deep-drawn metal stamping is a specialized technique used to create cylindrical or box-like parts with depths more significant than their diameter. This method is particularly suitable for components requiring a seamless and uniform finish. Neway's proficiency in deep-drawn metal stamping ensures high precision production of intricate and complex parts.
When comparing the two, progressive die stamping excels in scenarios where high production volumes are crucial, thanks to its efficiency and speed. It's well-suited for creating parts with intricate features and tight tolerances. In contrast, deep-drawn metal stamping is the go-to choice for applications requiring deep, uniform shapes, making it indispensable for enclosures, containers, and automotive components.
Neway's commitment to delivering quality in both progressive die stamping and deep-drawn metal stamping positions the company as a reliable partner for diverse manufacturing needs. Focusing on precision, efficiency, and versatility, Neway ensures clients receive optimal solutions tailored to their specific requirements.
In the competitive landscape of custom parts manufacturing, Neway stands out by seamlessly integrating progressive die stamping and deep-drawn metal stamping into its one-stop service. This comprehensive approach not only enhances production efficiency but also underscores Neway's dedication to meeting the varied demands of its clients.
Transfer Die Stamping
Progressive and transfer die stamping are methods used in metal stamping processes, each with unique characteristics and advantages.
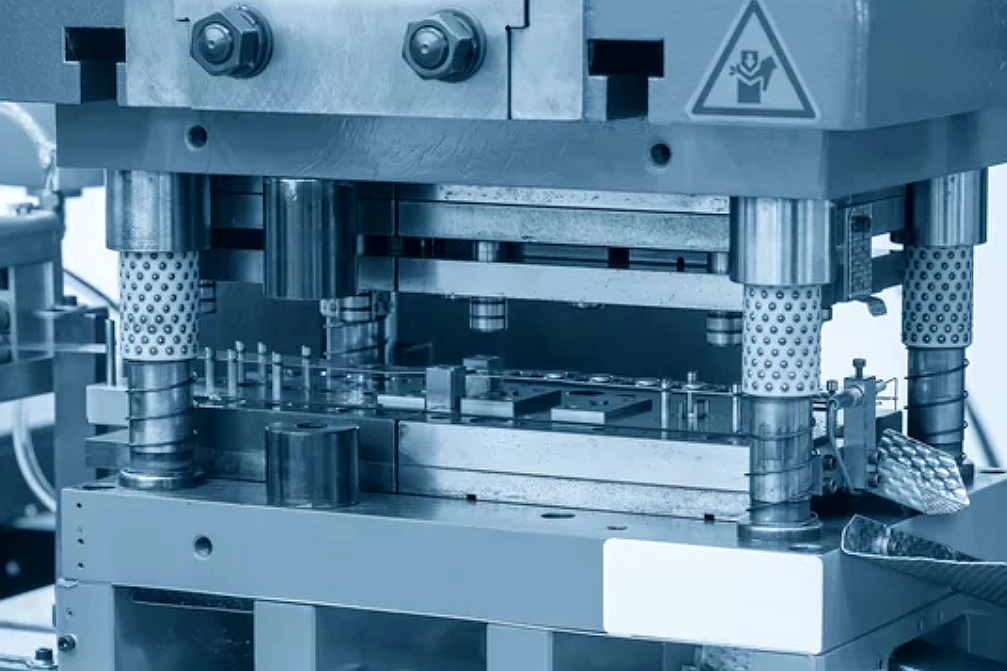
Progressive Die Stamping:
Process: This method involves feeding a strip of material through multiple stations within a single die to perform various operations, such as cutting, punching, bending, or coining, sequentially.
Efficiency: It's highly efficient for high-volume production due to its continuous process, enabling multiple operations in a single stroke.
Complexity: Suitable for intricate parts with several features, as each station in the die performs a specific operation.
Setup: Initial setup costs can be higher due to the complexity of the die and tooling required.
Accuracy: Offers high precision and consistency in part production.
Material Usage: It's efficient in material usage as it minimizes scrap.
Transfer Die Stamping:
Process: Transfer the part from one station to another using a mechanical transport system. Each station in the die performs a specific operation before transferring the part to the next station.
Flexibility: Well-suited for parts that require multiple operations but may not be suitable for continuous processing as in progressive stamping.
Speed: Slower than progressive die stamping due to the intermittent nature of the process.
Tooling: Requires less complex tooling than progressive dies, resulting in lower initial setup costs for certain part types.
Material Handling: This can be advantageous for larger, more complex parts or materials that are difficult to handle in continuous strip form.
Both methods have their strengths depending on the type of part produced, the required volume, complexity, and material considerations. Each is tailored to specific manufacturing needs, and the choice between them often depends on factors such as production volume, part complexity, cost considerations, and material characteristics.
Multi-Slide Metal Stamping
Progressive Die Stamping and Multi-Slide Metal Stamping are two distinct sheet metal fabrication processes with advantages and applications. Let's delve into a brief comparison to shed light on their differences.
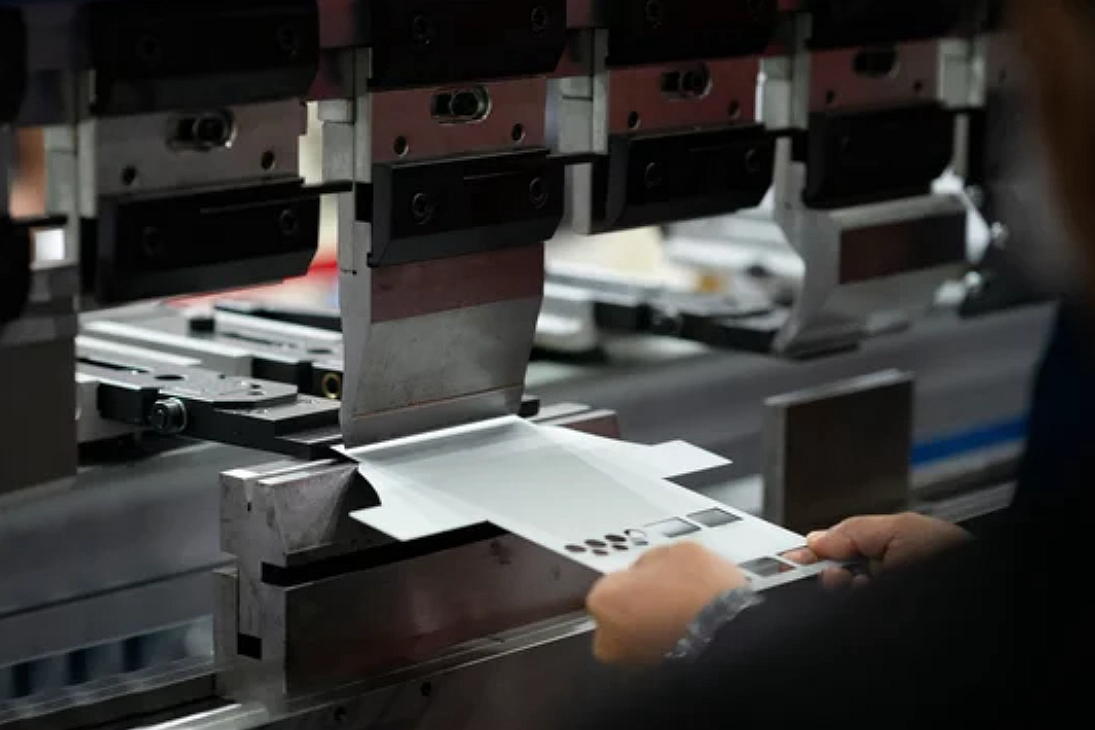
1. Precision and Complexity:
Progressive Die Stamping: Known for high precision and the ability to produce intricate parts with tight tolerances. It's an ideal choice for complex parts that require multiple operations.
Multi-Slide Metal Stamping: Offers excellent precision as well, but it excels in manufacturing simpler parts with fewer operations. Ideal for components that do not demand intricate detailing.
2. Tooling and Setup:
Progressive Die Stamping: A comprehensive and intricate die set for each process stage is required. Initial setup costs can be higher due to the complexity of tooling.
Multi-Slide Metal Stamping: Utilizes a single die set that moves horizontally, minimizing the need for intricate tooling. Setup costs are often lower compared to progressive die stamping.
3. Production Speed:
Progressive Die Stamping: Generally faster for high-volume production runs due to the simultaneous processing of multiple operations in a single stroke.
Multi-Slide Metal Stamping: Suited for high-speed production as well, particularly for simpler parts, but may have slightly lower output rates compared to progressive die stamping.
4. Material Usage and Waste:
Progressive Die Stamping: Efficient material utilization as the process minimizes waste. Scrap is often reduced, making it a cost-effective option for large production quantities.
Multi-Slide Metal Stamping: This can also be efficient in material usage, but the complexity of some parts may lead to slightly higher scrap rates compared to progressive die stamping.
5. Flexibility:
Progressive Die Stamping: Tailored for consistent and repetitive production of specific parts. Changes in design or specifications may require modifying the entire die set, impacting flexibility.
Multi-Slide Metal Stamping: Offers greater flexibility for smaller production runs or parts with frequent design changes. Adjustments are relatively more straightforward, making it suitable for versatile manufacturing needs.
In conclusion, Progressive Die Stamping and Multi-Slide Metal Stamping have their merits, and the choice depends on the project's specific requirements. With its expertise in sheet metal fabrication, Neway can seamlessly adapt to either method, ensuring optimal results for its clients.
What Neway Can Do In Progressive Die Stamping Process
Neway, a leading custom parts manufacturer, delivers precision and efficiency in progressive die stamping. This process is a cornerstone of our sheet metal fabrication capabilities. Here's a concise breakdown of what Neway can achieve in progressive die stamping:
Material Expertise:
Neway utilizes various materials in progressive die stamping, including metals like steel, aluminum, and copper. This versatility allows us to meet varied client requirements.
Customization and Complexity:
Our expertise lies in crafting intricate and highly customized components. Progressive die stamping enables the production of complex parts with tight tolerances, showcasing our commitment to precision manufacturing.
High-Speed Production:
Neway's advanced equipment and streamlined processes in progressive die stamping ensure high-speed production without compromising quality. This results in efficient and cost-effective manufacturing.
Tool and Die Design:
We invest in cutting-edge tool and die design to optimize the progressive stamping process. This approach enhances tool life, reduces downtime, and ultimately contributes to the overall productivity of our manufacturing operations.
Quality Assurance:
Quality is non-negotiable at Neway. Our progressive die stamping process is accompanied by rigorous quality control measures, ensuring that each stamped part meets or exceeds industry standards.
Scalability:
Whether it's prototyping or large-scale production, Neway's progressive die-stamping capabilities are scalable to meet the demands of different projects. This adaptability underscores our commitment to providing a one-stop solution for custom parts manufacturing.
Cost-Effective Solutions:
By leveraging the benefits of progressive die stamping, we offer cost-effective solutions to our clients. The efficiency of the process and the ability to produce intricate parts in a single operation contribute to cost savings.
In summary, Neway's prowess in progressive die stamping lies in its material expertise, customization capabilities, high-speed production, advanced tool and die design, stringent quality assurance, scalability, and cost-effective solutions. These aspects collectively position Neway as a reliable partner for clients seeking top-notch custom parts manufactured through progressive die stamping.
评论
发表评论