Explosion-proof lamps are essential in hazardous environments where flammable gases, vapors, or dust could lead to catastrophic accidents. These lamps are designed to prevent the ignition of surrounding explosive materials, making them crucial for safety in mining, oil and gas, chemical processing, and more.
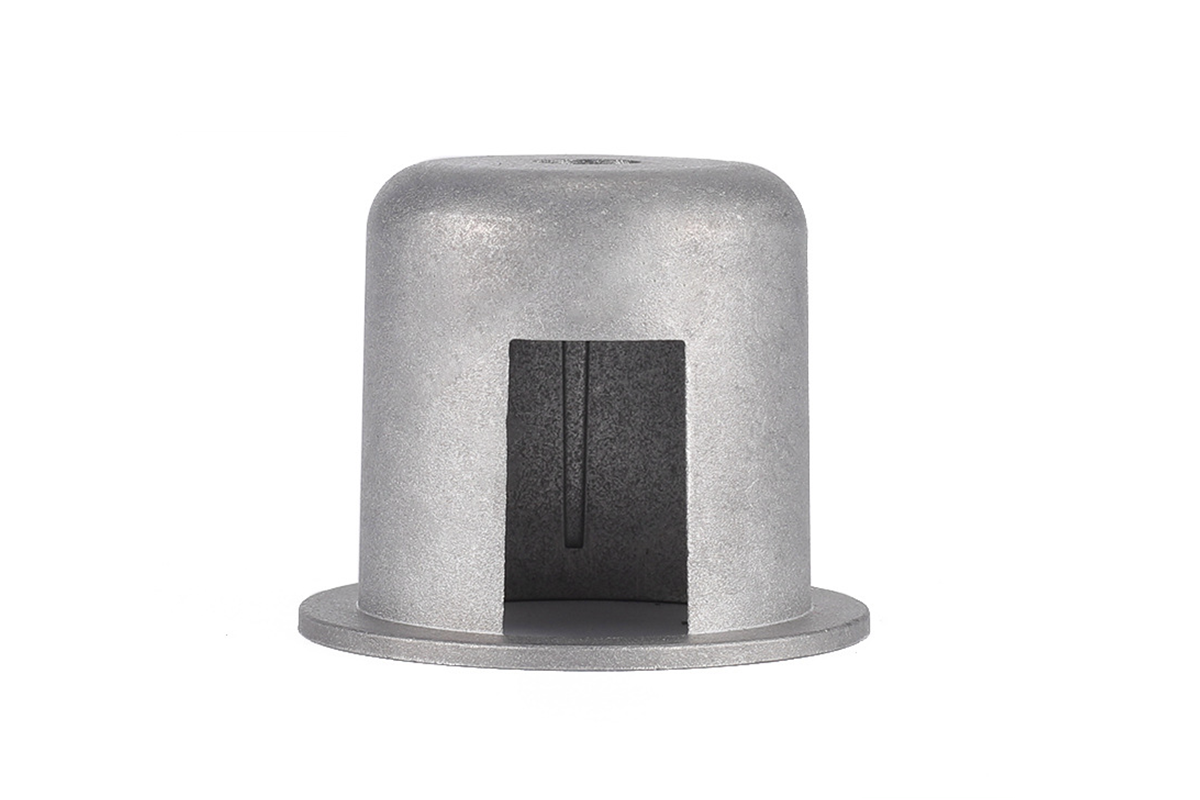
Aluminum ADC12 is a popular choice for manufacturing explosion-proof lamp accessories due to its favorable properties. This alloy is known for its excellent castability, high corrosion resistance, good thermal conductivity, and lightweight nature. These characteristics make ADC12 suitable for producing durable, reliable components that withstand harsh conditions.
Gravity die-casting is a preferred method for manufacturing these aluminum components. This casting process involves pouring molten aluminum into a mold under the force of gravity. It is known for producing parts with high dimensional accuracy, excellent surface finish, and superior mechanical strength. However, like any manufacturing process, gravity die-casting of ADC12 aluminum comes with its challenges.
Understanding ADC12 Aluminum
ADC12 aluminum, also known as A383 in the United States, is a widely used alloy in the die-casting industry. Its composition typically includes 10-12% silicon, 1-3% copper, 0.5-1% magnesium, and trace amounts of iron, zinc, and manganese, with aluminum balance. This specific blend of elements gives ADC12 unique properties, making it a preferred choice for various applications, including explosion-proof lamp accessories.
Composition and Properties of ADC12 Aluminum
Silicon (10-12%): Enhances fluidity during casting, reducing shrinkage and improving the overall quality of the cast.
Copper (1-3%): Increases strength and hardness, providing durability to the final product.
Magnesium (0.5-1%): Improves corrosion resistance and mechanical properties.
Iron, Zinc, and Manganese (trace amounts): Contribute to the alloy's strength and castability without significantly impacting its other properties.
Advantages of Using ADC12 in Explosion-proof Lamp Accessories
Lightweight: ADC12 is lighter than many other metals, making it easier to handle and install explosion-proof lamp accessories without compromising structural integrity.
Corrosion Resistance: The alloy's composition, particularly the presence of magnesium and silicon, provides excellent resistance to corrosion, ensuring longevity even in harsh environments.
Good Thermal Conductivity: ADC12 efficiently dissipates heat, preventing heat buildup in explosion-proof lamps and reducing the risk of component failure.
High-Dimensional Stability: The alloy maintains its shape and dimensions under varying temperatures and pressures, which is crucial for the precise fit and function of lamp accessories.
Excellent Castability: ADC12's composition allows it to flow easily into molds, filling intricate details and reducing defects in the final product.
Comparison with Other Aluminum Alloys and Materials
Versus ADC10: While similar, ADC10 has slightly lower silicon content, making ADC12 better for applications requiring intricate designs and reduced shrinkage.
Versus A380: ADC12 offers better corrosion resistance and thermal conductivity than A380, though A380 may have slightly better mechanical properties.
Versus Zinc Alloys: Zinc alloys provide higher strength and impact resistance but are heavier and less corrosion-resistant than ADC12.
Versus Steel: Steel offers superior strength but is significantly heavier and more prone to corrosion than ADC12 aluminum, making ADC12 a more practical choice for explosion-proof lamp accessories.
Gravity Die-Casting Process
Gravity die-casting is a highly efficient and precise manufacturing method for producing complex aluminum parts, including explosion-proof lamp accessories. The process involves pouring molten aluminum into a mold using gravity to fill the cavity. This section will detail the steps involved in gravity die-casting and highlight its benefits.
Detailed Explanation of the Gravity Die-Casting Process
Mold Preparation
Design and Construction: The mold, typically made from steel or cast iron, is designed to the specifications of the desired part. It comprises two halves: the cavity (female) and the core (male).
Coating and Preheating: The mold is coated with a refractory material to prevent the molten aluminum from sticking and to enhance the mold's lifespan. It is then preheated to a specific temperature to ensure uniform filling and solidification.
Melting and Pouring of Aluminum
Melting: Aluminum ADC12 ingots are melted in a furnace at temperatures around 660°C (1220°F) until a consistent molten state is achieved.
Pouring: The molten aluminum is carefully poured into the mold cavity through a gating system, which directs the flow and minimizes turbulence to prevent defects.
Solidification and Cooling
Controlled Cooling: The aluminum cools and solidifies once the mold is filled. Controlled cooling rates are essential to avoid internal stresses and ensure uniform grain structure.
Solidification Patterns: Proper cooling process management helps achieve desired mechanical properties and reduce defects like porosity and shrinkage.
Ejection and Finishing
Mold Opening: After sufficiently solidifying aluminum, the mold is opened, and the casting is ejected using ejector pins.
Finishing Processes: The casting undergoes various finishing processes such as trimming, machining, and surface treatments to remove excess material, enhance surface quality, and achieve precise dimensions.
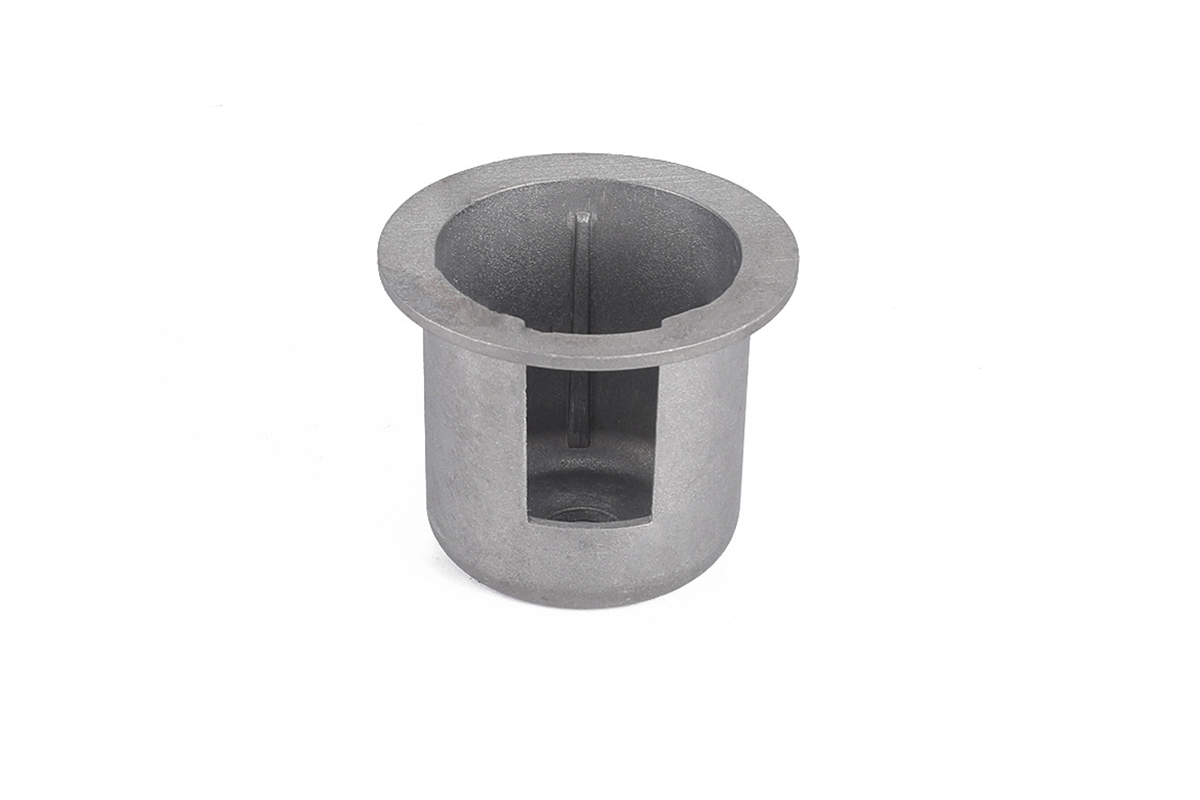
Benefits of Gravity Die-Casting for Manufacturing Lamp Accessories
Dimensional Accuracy
Gravity die-casting offers high dimensional accuracy, which is essential for producing complex shapes and intricate designs required in explosion-proof lamp accessories. Tolerances can be maintained within ±0.1 mm, ensuring a perfect fit and reliable performance.
Surface Finish Quality
The process provides excellent surface finish quality, reducing the need for extensive post-processing. Surface roughness values typically range between Ra 1.6 to Ra 3.2 micrometers, enhancing the aesthetic and functional aspects of the components.
Mechanical Strength
Due to the controlled solidification process, gravity die-cast parts exhibit superior mechanical strength, resulting in a dense and uniform grain structure. ADC12 components can achieve tensile strengths up to 310 MPa and 3-5% elongation, making them robust and durable.
Efficiency and Productivity
The gravity die-casting process is highly efficient, allowing for high production rates and repeatability. Automated systems can further enhance productivity, reducing lead times and manufacturing costs.
Gravity die-casting combines precision, efficiency, and versatility, making it an ideal method for producing high-quality aluminum components for explosion-proof lamp accessories. Manufacturers can achieve exceptional results by understanding and optimizing each process step, ensuring safety and reliability in hazardous environments.
Challenges in Gravity Die-Casting of ADC12 Aluminum
While gravity die-casting offers numerous advantages for manufacturing explosion-proof lamp accessories, it also presents several challenges. These challenges can impact the quality and performance of the final product. Understanding these issues is the first step in developing effective solutions. This section explores the common problems encountered in the gravity die-casting of ADC12 aluminum.
Common Issues Encountered During the Casting Process
Porosity and Gas Entrapment
Problem: Porosity refers to tiny voids or cavities within the cast metal, often caused by trapped gas. It can weaken the part's structural integrity and lead to failures in critical applications.
Cause: Porosity is typically caused by air entrapment during pouring, inadequate molten aluminum degassing, or excessive turbulence.
Shrinkage Defects
Problem: Shrinkage defects occur when there is a volume reduction in the aluminum as it solidifies, leading to voids and cracks. These defects compromise the strength and durability of the cast part.
Cause: Insufficient feeding of molten aluminum into the solidifying casting, improper mold design, and uneven cooling rates can lead to shrinkage defects.
Incomplete Filling and Cold Shuts
Problem: Incomplete filling results in areas of the mold not being filled with aluminum, while cold shuts are formed when two streams of molten metal do not fuse properly. Both defects create weak spots in the casting.
Cause: Low pouring temperature, slow speed, and poor mold design can contribute to incomplete filling and cold shuts.
Warping and Distortion
Problem: Warping and distortion occur when the cast part deforms during cooling, leading to dimensional inaccuracies and assembly issues.
Cause: Uneven cooling rates, residual stresses from solidification, and improper mold design can cause warping and distortion.
Factors Contributing to These Challenges
Alloy Properties and Composition
The specific properties of ADC12, such as its high silicon content, can influence fluidity and solidification behavior, affecting the casting process.
Mold Design and Material
The design of the mold, including gating and riser systems, plays a crucial role in controlling the flow and solidification of the molten aluminum. The material of the mold also impacts heat transfer and cooling rates.
Pouring Temperature and Speed
The temperature at which the aluminum is poured and the speed of pouring are critical parameters. Incorrect settings can lead to defects such as porosity, incomplete filling, and cold shuts.
Cooling Rate and Solidification Pattern
The rate at which the casting cools and solidifies affects the final microstructure and mechanical properties. Controlled cooling is essential to minimize defects and ensure consistent quality.
Solutions to Overcome Casting Challenges
Addressing the challenges in gravity die-casting of ADC12 aluminum requires a combination of process optimization, advanced techniques, and precise control over various parameters. This section explores effective solutions to common casting issues, ensuring the production of high-quality explosion-proof lamp accessories.
Techniques to Reduce Porosity and Gas Entrapment
Proper Degassing of Molten Aluminum
Solution: Utilize techniques such as rotary degassing, where an inert gas (e.g., argon or nitrogen) is injected into the molten aluminum to remove dissolved hydrogen and other gases.
Impact: Reduces the likelihood of gas entrapment, resulting in fewer porosity defects and improved mechanical properties.
Use of Vacuum Casting or Low-Pressure Die-Casting
Solution: Implement vacuum casting or low-pressure die-casting methods to minimize air entrapment during pouring.
Impact: Enhances the density and integrity of the cast parts by reducing the presence of gas pockets.
Optimizing Pouring Temperature and Speed
Solution: Carefully control the pouring temperature and speed to maintain a smooth and steady flow of molten aluminum into the mold.
Impact: Minimizes turbulence and air entrapment, leading to higher-quality castings with reduced porosity.
Strategies to Minimize Shrinkage Defects
Design Modifications in Mold Gating and Risers
Solution: Optimize the design of the gating system and risers to ensure adequate feeding of molten aluminum during solidification.
Impact: Reduces shrinkage defects by providing a continuous supply of molten metal to compensate for volume reduction.
Controlled Cooling and Solidification
Solution: To manage the solidification rate, implement controlled cooling techniques, such as cooling channels or external cooling devices.
Impact: Ensures uniform cooling, preventing the formation of shrinkage cavities and improving overall casting quality.
Use of Chills and Insulating Sleeves
Solution: Place chills (metal inserts) and insulating sleeves in strategic locations within the mold to direct the solidification process.
Impact: Promotes directional solidification, reducing shrinkage defects and enhancing the mechanical properties of the cast parts.
Methods to Ensure Complete Filling and Prevent Cold Shuts
Improved Mold Design for Better Flow Dynamics
Solution: Optimize the mold design to enhance the flow dynamics of molten aluminum, ensuring complete filling of the mold cavity.
Impact: Prevents incomplete filling and cold shuts, resulting in defect-free castings with uniform properties.
Proper Venting and Gas Evacuation
Solution: Incorporate venting systems within the mold to allow trapped gases to escape during pouring.
Impact: Reduces gas entrapment and enhances the flow of molten aluminum, preventing cold shuts and improving casting quality.
Use of High-Quality Lubricants and Coatings
Solution: Apply high-quality lubricants and mold coatings to reduce friction and facilitate smooth molten aluminum flow.
Impact: Enhances mold filling and reduces the risk of cold shuts, leading to higher-quality castings.
Approaches to Prevent Warping and Distortion
Uniform Cooling and Temperature Control
Solution: Ensure uniform cooling of the casting by using controlled cooling techniques and maintaining consistent mold temperatures.
Impact: Prevents differential cooling rates that can cause warping and distortion, ensuring dimensional accuracy.
Stress-Relief Treatments Post-Casting
Solution: Perform stress-relief treatments, such as annealing, to alleviate residual stresses in the cast parts.
Impact: Reduces the risk of warping and distortion, improving the stability and dimensional accuracy of the components.
Precision Machining and Finishing
Solution: Utilize precision machining and finishing techniques to achieve the desired dimensions and surface finish.
Impact: Corrects minor distortions and ensures the final parts meet stringent quality standards.
Gravity Die Casting Case Studies
To illustrate the practical application of the solutions discussed, let's delve into a few real-world examples and case studies. These techniques have been successfully implemented in manufacturing explosion-proof lamp accessories using ADC12 aluminum gravity die-casting.
Successful Gravity Die-Casting Project for Explosion-Proof Lamp Accessories
Initial Challenges Faced
Porosity Issues: The initial batches of castings exhibited significant porosity, compromising the structural integrity of the lamp housings.
Shrinkage Defects: Several parts showed signs of shrinkage cavities, particularly in thicker sections of the castings.
Incomplete Filling: Some components had areas where the aluminum did not fill the mold, resulting in weak spots and cold shuts.
Solutions Implemented
Enhanced Degassing: Introduced rotary degassing to remove dissolved gases from the molten aluminum, significantly reducing porosity.
Optimized Mold Design: Redesigned the gating system and added risers to ensure adequate feeding of molten aluminum during solidification, minimizing shrinkage defects.
Controlled Cooling: Implemented controlled cooling techniques using cooling channels and chills to manage the solidification rate, ensuring uniform cooling and reducing defects.
Improved Pouring Technique: Adjusted the pouring temperature and speed to enhance the flow of aluminum into the mold, preventing incomplete filling and cold shuts.
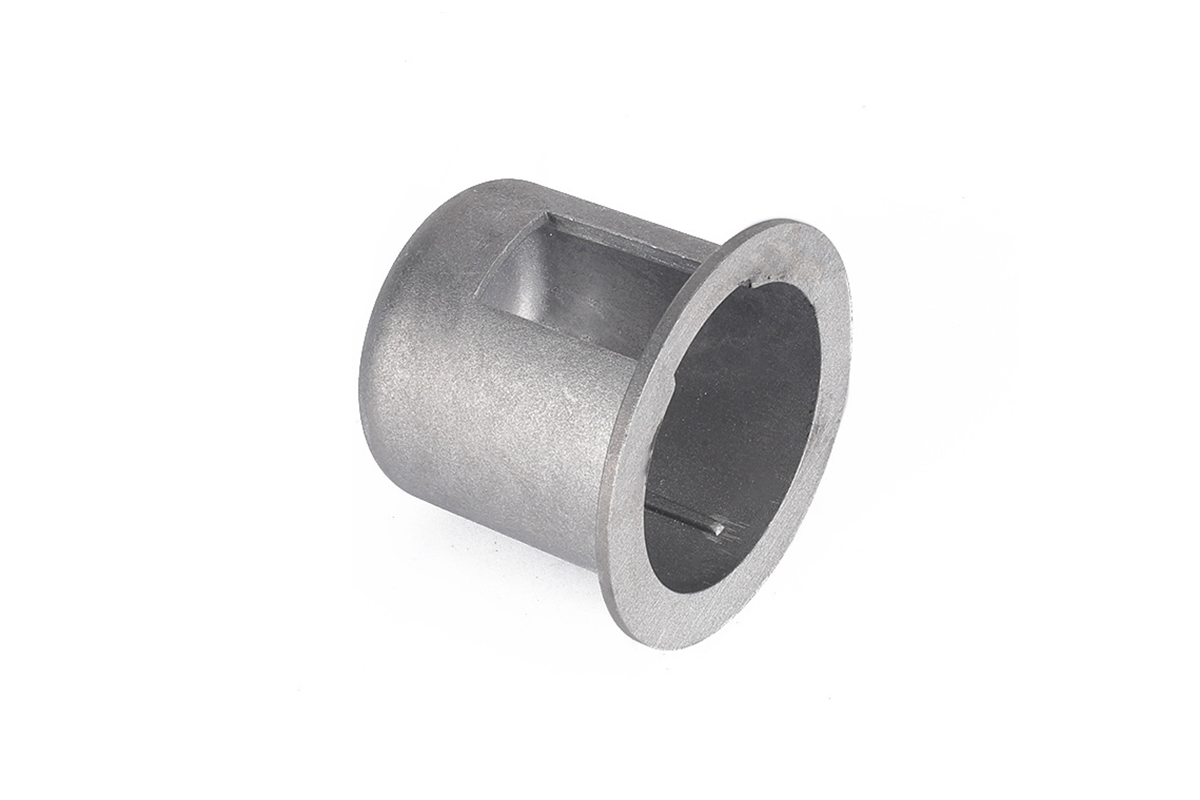
Results Achieved
Improved Quality: The quality of the castings improved dramatically, with a significant reduction in porosity and shrinkage defects.
Enhanced Mechanical Properties: The mechanical properties of the parts met the required specifications, ensuring durability and reliability in hazardous environments.
Increased Production Efficiency: The optimized process reduced cycle times and improved production efficiency, saving costs.
评论
发表评论