Aluminum die-casting is a highly efficient and versatile manufacturing process widely used in producing complex and lightweight parts. This technique involves forcing molten aluminum into a mold cavity under high pressure, producing parts with excellent dimensional accuracy and surface finish. While aluminum die-cast parts are inherently strong and durable, applying a protective and decorative coating can significantly enhance their performance and longevity.
Surface finishing is a critical step in the production of aluminum die-cast parts. Among various finishing techniques, painting or spraying is particularly popular due to its ability to provide both functional and aesthetic benefits. By applying a spray coating, manufacturers can protect aluminum parts from environmental damage, improve their appearance, and add specific properties tailored to the needs of different applications.
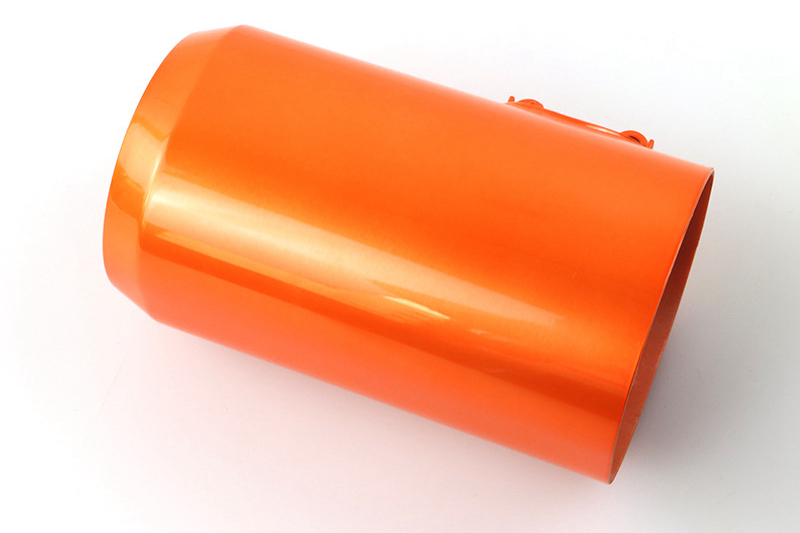
Functions of Spraying on Die-Cast Parts
1.1 Protection
One of the primary functions of spraying on aluminum die-cast parts is to provide a protective layer that shields the metal from various environmental factors. This coating is a barrier against humidity, temperature fluctuations, and UV radiation, which can cause oxidation and corrosion over time. By preventing these elements from directly contacting the metal surface, the spray coating significantly enhances the longevity and reliability of the parts.
1.2 Aesthetic Enhancement
Spray coatings can drastically improve the visual appeal of aluminum die-cast parts. They offer a wide range of finishes, including matte, glossy, and textured surfaces, allowing customization to meet specific design requirements. Manufacturers can choose from an extensive palette of colors and effects, making the parts functional and visually attractive. It is essential for consumer-facing products where appearance is crucial to marketability.
1.3 Durability
Another critical function of spray coating is enhancing the durability of die-cast parts. The coating adds a layer of hardness to the surface, making it more resistant to wear and tear from mechanical interactions. It is essential for parts subjected to frequent handling or movement, such as those used in automotive or machinery applications. The added durability ensures that the parts maintain their integrity and functionality over extended periods.
1.4 Functional Coatings
Beyond protection and aesthetics, spray coatings can impart specific functional properties to aluminum die-cast parts. For example, certain coatings can provide non-slip surfaces, making them suitable for components that require secure handling. Others can offer anti-static properties, crucial for electronic components to prevent static electricity damage. Additionally, some coatings provide electrical insulation or conductivity, expanding the range of applications for die-cast parts.
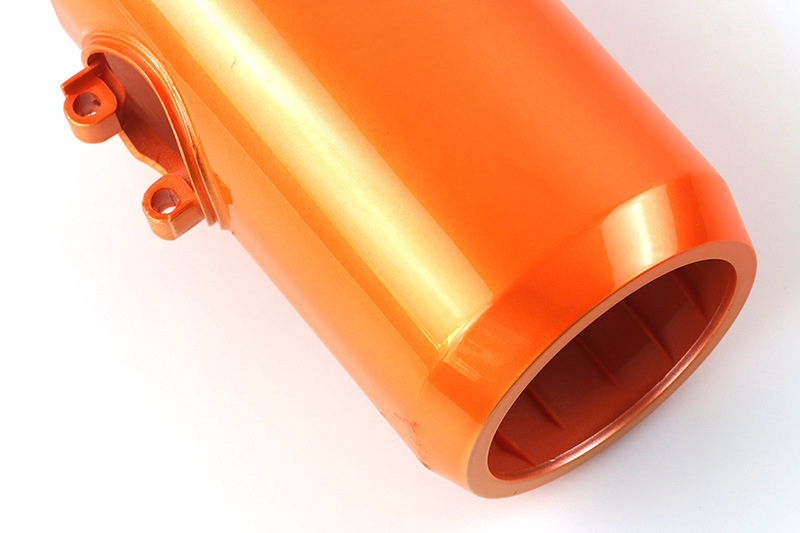
Resistance of Spray Coating to Scratches and Corrosion
2.1 Scratch Resistance
Scratch resistance is a vital attribute for spray coatings applied to aluminum die-cast parts, particularly in applications where the parts are exposed to frequent handling or abrasive environments.
Overview of Scratch-Resistant Coatings Scratch-resistant coatings are formulated to enhance the surface hardness of aluminum die-cast parts, making them less susceptible to damage from mechanical contact. These coatings often incorporate hardeners and advanced materials such as ceramic particles or polymers to create a rigid, resilient surface layer.
Performance Metrics and Testing StandardsThe effectiveness of scratch-resistant coatings is measured using various standardized tests. One standard test is the ASTM D3363, which assesses the coating's hardness using pencils of different hardness grades. Another test, the ASTM D7027/ISO 1518, uses a stylus to apply a controlled force to the coated surface to evaluate its resistance to scratching.
Real-World Examples from Industry ApplicationsIn the automotive industry, scratch-resistant coatings on aluminum die-cast parts, such as trim components and engine parts, help maintain a pristine appearance despite harsh conditions. Similarly, in consumer electronics, these coatings protect the casings of devices from daily wear and tear, ensuring they remain attractive and functional over time.
2.2 Corrosion Resistance
Corrosion resistance is another critical function of spray coatings, especially for aluminum die-cast parts in environments prone to moisture and chemical exposure.
Mechanisms of Corrosion ResistanceSpray coatings protect against corrosion through several mechanisms. The barrier effect physically isolates the aluminum surface from corrosive agents such as water and salts. Some coatings also provide sacrificial protection, where the coating material preferentially corrodes, sparing the underlying aluminum. Additionally, certain coatings contain corrosion inhibitors that chemically neutralize corrosive elements.
Testing StandardsThe effectiveness of corrosion-resistant coatings is typically evaluated using the ASTM B117 salt spray test. This accelerated corrosion test exposes coated samples to a salt fog environment, simulating long-term exposure to corrosive conditions. The coatings are assessed based on their ability to prevent rust and other corrosion over a specified period.
Case Studies Demonstrating Improved Lifespan in Harsh EnvironmentsIn the marine industry, aluminum die-cast parts coated with corrosion-resistant sprays are used in boat components and offshore equipment, where they endure constant exposure to saltwater and humidity. These coatings have proven to extend the lifespan of parts, reducing maintenance costs and improving reliability. In industrial machinery, such coatings protect parts from chemical exposure and environmental factors, ensuring consistent performance and longevity.
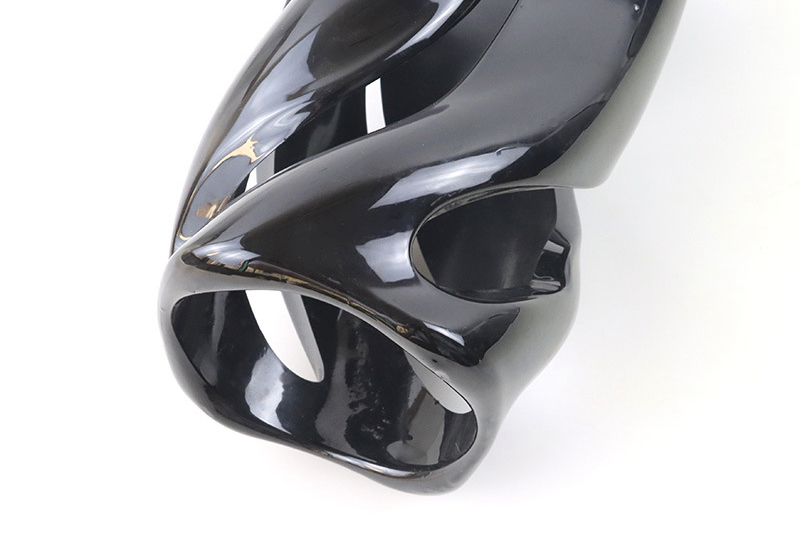
Precautions for Painting
3.1 Surface Preparation
Proper surface preparation is crucial for achieving a high-quality spray coating on aluminum die-cast parts. Withting may not adhere correctly without appropriate preparation, leading to defects and reduced performance.
Importance of Cleaning and DegreasingBefore applying any coating, it is essential to thoroughly clean and degrease the aluminum surface. Contaminants like oil, grease, dirt, and oxides can prevent the coating from adhering properly. Solvents, alkaline cleaners, or ultrasonic cleaning methods can ensure a clean surface.
Techniques for Better AdhesionTo further enhance adhesion, techniques like sandblasting or chemical etching are employed. Sandblasting roughens the surface, providing more surface area for the coating to bond. Chemical etching involves using acidic solutions to micro-etch the surface, improving the mechanical bond between the coating and the metal.
3.2 Application Techniques
Choosing the proper application technique is critical to achieving a uniform, defect-free coating.
Spraying MethodsSeveral spraying methods can be used, each with its advantages:
Electrostatic Spraying: Utilizes electrostatic charge to attract the coating particles to the aluminum part, ensuring even coverage and minimal waste.
Powder Coating: Dry powder is applied electrostatically and cured under heat to form a durable finish. It is known for its excellent adhesion and resistance properties.
Wet Spray Coating: Uses liquid paint applied via spray guns. It allows various finishes but requires careful control to avoid running and sagging.
Ensuring Uniform CoverageUniform coverage is essential to avoid weak spots that can lead to corrosion or other failures. Proper technique, equipment calibration, and skilled operators are necessary for a consistent coating.
3.3 Environmental Considerations
The environment in which spraying is conducted plays a significant role in the quality of the coating.
Controlling Humidity and TemperatureHumidity and temperature can affect the drying and curing process. High humidity can cause defects like blistering, while temperature fluctuations can affect the coating’s viscosity and application. Maintaining controlled conditions, typically within 20-25°C and 40-60% relative humidity, is essential.
Ensuring Proper Ventilation and Safety MeasuresProper ventilation is necessary to remove fumes and overspray, ensuring a safe working environment. Using appropriate personal protective equipment (PPE) like masks, gloves, and eye protection is also essential to safeguard workers from hazardous substances.
3.4 Curing Process
The curing process solidifies the coating, enhancing its adhesion and durability.
Importance of Correct Curing Times and TemperaturesEach coating type has specific curing requirements. Following the manufacturer’s guidelines for curing times and temperatures is critical to achieving the desired properties. Under-curing can result in a soft, ineffective coating, while over-curing can cause brittleness and loss of adhesion.
Consequences of Improper CuringImproper curing can lead to several issues, including reduced durability, poor adhesion, and aesthetic defects like color changes. Ensuring the correct curing process helps in achieving a robust and long-lasting finish.
3.5 Quality Control
Regular inspections and testing ensure the coating meets the required standards and specifications.
Regular Inspections and Testing Conducting inspections at various stages of the coating process help identify and rectify issues early. Testing methods such as adhesion tests, thickness measurements, and visual inspections ensure the coating meets the desired quality levels.
Adherence to Industry Standards and SpecificationsFollowing industry standards such as ISO, ASTM, and specific customer requirements ensures that the coating process meets the highest quality benchmarks. Consistent adherence to these standards helps in delivering reliable and high-performing products.
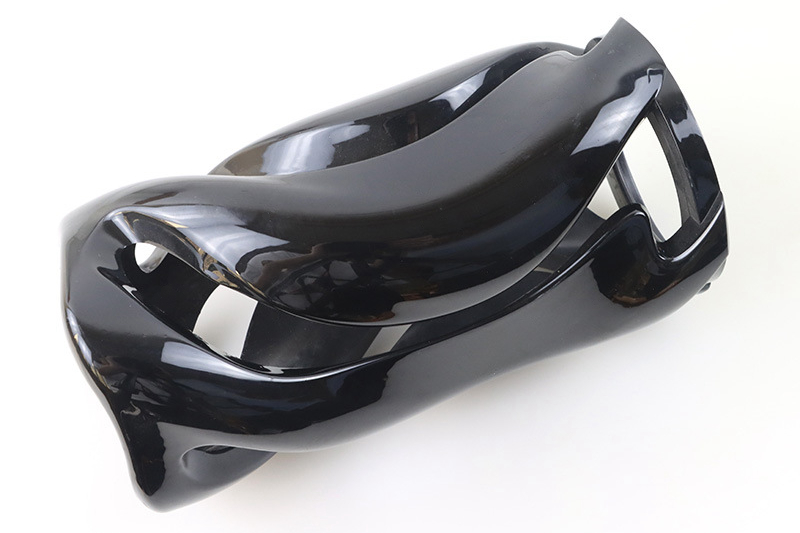
Conclusion
Spray-coating aluminum die-cast parts offer many benefits, from enhancing durability and protection to improving aesthetics and adding specialized functions. Understanding the functions, resistance capabilities, and precautions of spray coating is essential for manufacturers aiming to produce high-quality, long-lasting parts.
By applying a protective spray coating, manufacturers can shield aluminum parts from environmental factors such as humidity, UV radiation, and temperature fluctuations, significantly extending their lifespan. The coatings also offer scratch and corrosion resistance, critical for parts exposed to mechanical wear and harsh conditions.
Furthermore, the ability to customize the appearance of aluminum die-cast parts through various finishes and colors adds significant value, making the parts functional and visually appealing. Functional coatings can provide additional properties such as non-slip surfaces, anti-static features, and electrical insulation, broadening the range of applications for these parts.
To achieve optimal results, manufacturers must follow rigorous surface preparation protocols, select appropriate application techniques, maintain controlled environmental conditions, and ensure proper curing processes. Regular quality control inspections and adherence to industry standards are vital to maintaining the highest quality and performance levels.
评论
发表评论