Introduction to Multi-Axis Milling
In precision engineering and advanced manufacturing, the evolution of CNC (Computer Numerical Control) milling is a pivotal development. Originally, CNC technology revolutionized production with three-axis milling machines capable of moving a cutting tool in three directions: X, Y, and Z. However, as industries demanded more complex and intricately designed parts, the limitations of three-axis machines became apparent. This necessity drove the innovation towards multi-axis milling—a more advanced version of CNC technology.
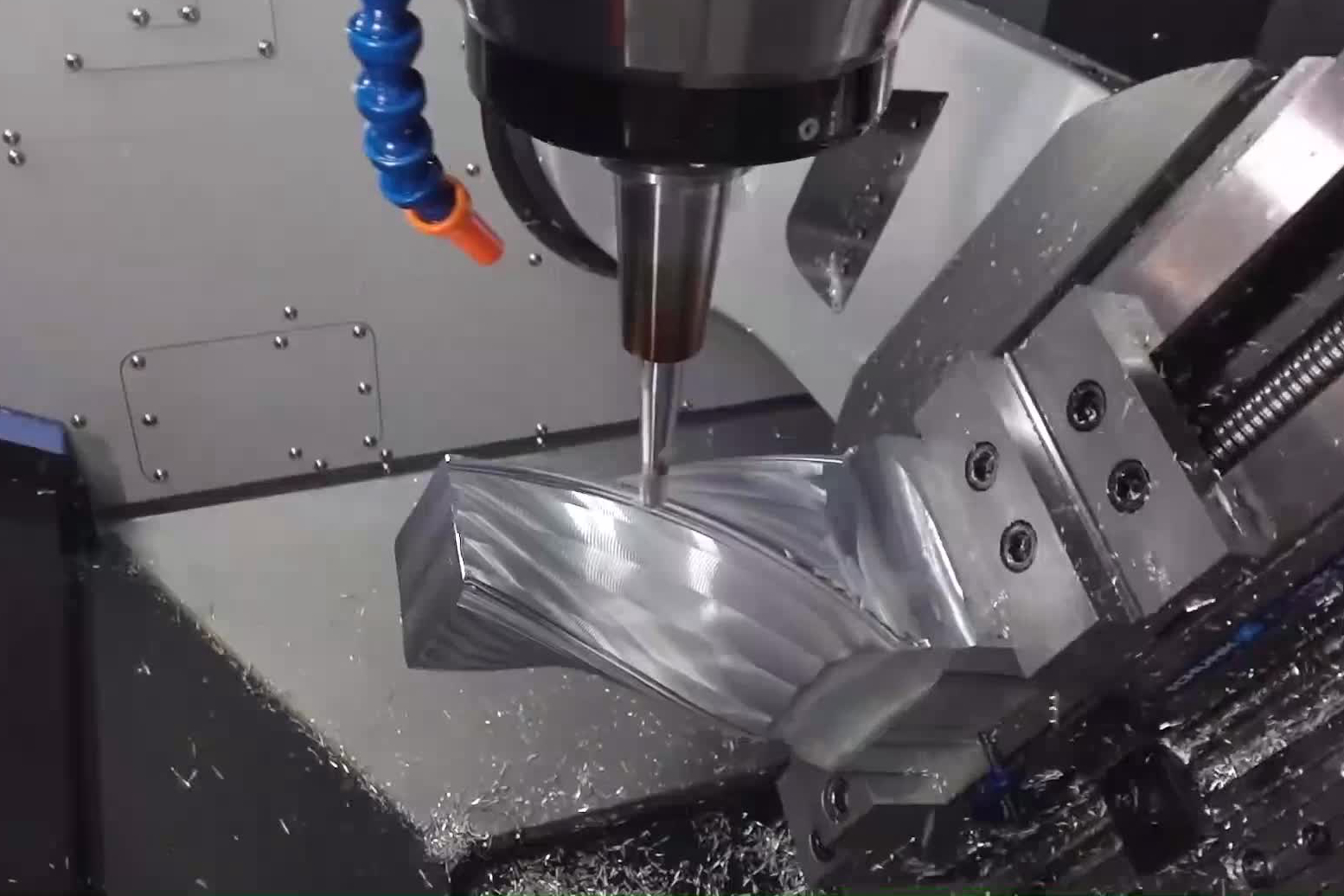
What is Multi-Axis Milling?
Multi-axis milling refers to CNC milling machines that operate beyond the traditional three axes, incorporating additional rotary axes to enhance the flexibility and capability of the machining process. This technology allows for machining incredibly complex geometries that are otherwise impossible to achieve with standard CNC milling. The ability to rotate the workpiece and the tool simultaneously reduces the need for multiple setups. It improves the precision of the final product.
Significance of Multi-Axis Milling
The advent of multi-axis milling machines marks a significant leap in manufacturing capabilities, enabling industries such as aerospace, automotive, and medical devices to fabricate parts with unprecedented precision and complexity. These machines can produce components with intricate details and complex surfaces without compromising speed or efficiency, making multi-axis milling a cornerstone of modern manufacturing.
Understanding Multi-Axis Milling
Multi-axis milling refers to using CNC machines incorporating additional axes beyond the standard X, Y, and Z axes in traditional milling. This technology enables the simultaneous movement and rotation of the tool and the workpiece, allowing for more complex machining operations with high precision. Including extra axes transforms the milling process, expanding its capabilities and enabling the creation of intricate and sophisticated designs that are impossible with 3-axis machines.
Comparison with Traditional (3-axis) Milling
To understand the capabilities of multi-axis milling, it is helpful to compare it with traditional 3-axis milling:
3-axis milling: Involves movements and cuts along three linear axes—X, Y, and Z. This setup is sufficient for many standard milling tasks but is limited in handling complex geometries and undercuts.
Multi-axis milling: Adds one or more rotary axes, significantly enhancing the machine's ability to access multiple sides of a part without human intervention. This results in reduced setup times, improved surface finishes, and the ability to create more complex shapes.
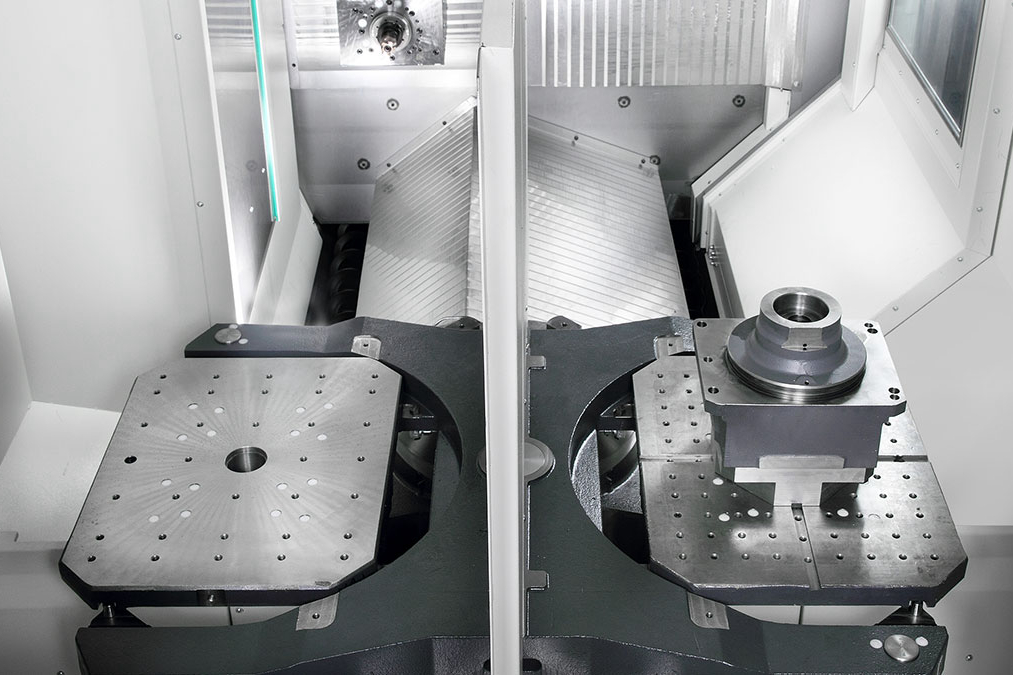
Core Aspects of Multi-Axis Milling
Complexity in Design: Multi-axis machines can execute intricate cuts and detailed features on parts from virtually any angle, providing designers and engineers greater freedom in product design.
Precision and Flexibility: The additional axes in multi-axis milling offer unmatched precision, making it easier to achieve tight tolerances and produce parts that fit exact specifications.
Efficiency: With the ability to perform complex machining tasks in a single setup, multi-axis milling reduces the overall machining time and increases throughput in production environments.
Classifications of Multi-Axis Milling Machines
Multi-axis milling machines vary primarily in the number of axes they can manipulate during machining. This variety allows for various capabilities, from simple geometries to highly complex shapes requiring precise control over the machine's movements. Here's a detailed look at the main classifications of multi-axis milling machines:
1. 4-Axis Milling Machines
Description: A 4-axis milling machine introduces a rotary axis, often called the A-axis, which rotates around the X-axis. This additional axis expands the machining capabilities beyond the simple vertical and horizontal cuts typical of 3-axis machines.
Capabilities: With 4-axis milling, the machine can create holes and cuts in a workpiece from angles and directions that a 3-axis machine cannot achieve without repositioning. This capability is handy for creating complex geometries like those in automotive and aerospace parts.
2. 5-Axis Milling Machines
Description: The 5-axis machines incorporate two additional rotary axes, typically A and B or A and C, depending on their rotation relative to the X, Y, and Z axes. These machines can simultaneously manipulate the tool or workpiece along five axes.
Capabilities: 5-axis milling is ideal for complex, precision-demanding tasks in aerospace, medical, and die/mold manufacturing industries. This machine type can efficiently produce intricate parts with complicated geometries and excellent surface finish, reducing the need for multiple setups and tool changes.
3. Additional Configurations
6-Axis Milling Machines: Although less common, 6-axis milling machines offer even greater versatility and precision. These machines add another degree of freedom, making them capable of executing the most intricate and detailed designs. They are handy for parts with complex contours that require precise tool alignment from nearly any angle.
Capabilities: The extra axis in a 6-axis machine allows for unparalleled flexibility in machining. It can effectively reduce the time and effort needed to set up and execute jobs that would otherwise be highly complex and time-consuming.
Explanation of Each Type's Unique Capabilities and Suitable Applications
4-Axis Machines: Suitable for applications requiring complex, detailed cuts that include engravings and reliefs and applications where multiple sides of a part need to be machined in a single setup.
5-Axis Machines: Essential for industries where precision is critical, such as in the aerospace sector for machining airfoils, turbine blades, and prototyping new designs.
6-Axis Machines: Best for advanced research and development applications and for manufacturing parts with extremely complicated geometries that require a superior level of detail and finish.
The Multi-Axis Milling Process
The multi-axis milling process involves several intricate steps that together ensure the successful production of complex parts with high precision. Here's a detailed exploration of each step in the multi-axis milling process:
1. CAD Model Creation
The process begins with creating a precise 3D model using Computer-Aided Design (CAD) software. This model serves as the blueprint for the part and includes all critical dimensions, tolerances, and geometries. The detail in the CAD model is crucial as it directly influences the quality and accuracy of the final product.
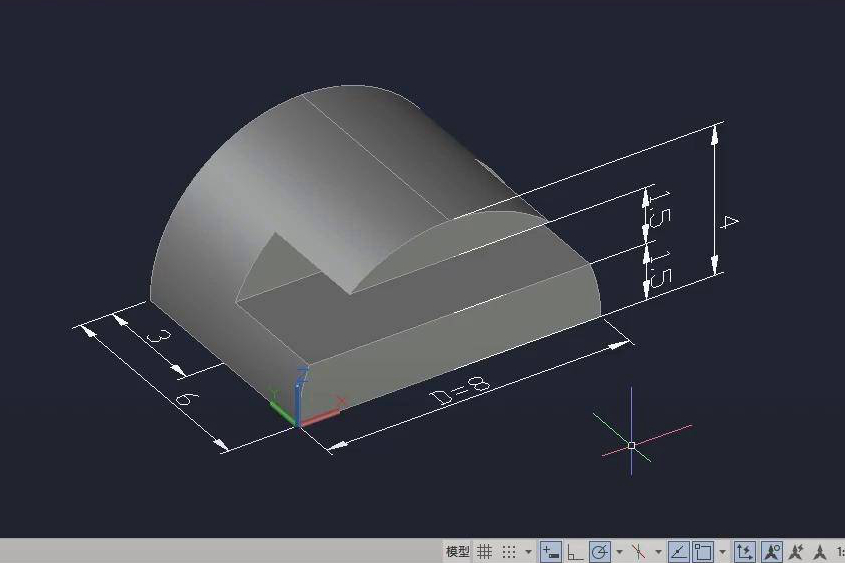
2. CAM Software Programming and Simulation
After the CAD model is complete, the file is imported into Computer-Aided Manufacturing (CAM) software, which converts the 3D model into a machine-readable format. The CAM software is used to plan and simulate the tool paths, ensuring that the movement of the milling tools is optimized for efficiency and accuracy. The simulation stage is vital for identifying issues such as tool collisions or inefficient movements that could affect the machining process.
3. Setup and Tooling Considerations Specific to Multi-Axis Machines
Setting up a multi-axis milling machine involves configuring the machine's various axes to align perfectly with the planned machining paths. This setup also includes selecting and installing the appropriate tools and fixtures. Special attention is given to the tool length and diameter in multi-axis milling, as these factors significantly influence the ability to access complex geometries without interference. The setup's rigidity and stability are paramount to maintaining precision across multiple axes.
4. The Actual Machining Process
The milling process begins with setting up the machine and testing the program through simulations. The raw material is securely fastened to the machine table or held in a fixture, and the milling tools are activated. As the machine executes the programmed tool paths, the cutting tools move along designated axes, simultaneously rotating and tilting to access the workpiece from various angles. This capability allows for creating intricate designs and complex features that are difficult or impossible to achieve with fewer axes.
Real-time monitoring and adjustments are often necessary throughout the machining process to compensate for deviations from the expected tool paths or material inconsistencies. This adaptive approach helps ensure the part's final dimensions are within the specified tolerances.
5. Precision and Tolerances Achievable with Multi-Axis Machines
Multi-axis milling machines can achieve extremely tight tolerances, often within a few microns. The precise control over the tool's position and orientation allows for better surface finishes and more accurate features, which are crucial in industries with critical dimensional accuracy.
Through its advanced technological capabilities, the multi-axis milling process offers a significant advantage in efficiently and accurately manufacturing complex parts. This process enhances the functionality and aesthetic of the parts produced. It reduces waste and overall production time, making it a preferred choice for high-precision manufacturing applications.
Advantages of Multi-Axis Milling
Multi-axis milling provides several advantages over traditional methods, mainly when producing complex and precision-engineered components. Here are the key benefits that make multi-axis milling a valuable asset in modern manufacturing:
1. Increased Precision and Complexity in Part Design
Multi-axis milling machines allow simultaneous movement along multiple axes, offering exceptional control over the tool's path and angle. This enhanced control enables the production of highly complex parts with intricate geometries and detailed features that would be challenging or impossible with traditional 3-axis machines. The ability to achieve complex shapes in a single setup ensures precision and maintains the integrity of the design.
2. Reduction in Setup Times and Overall Production Efficiency
Traditional milling often requires multiple setups to achieve different angles and positions for complex parts. Multi-axis milling significantly reduces the number of setups needed by allowing the tool to access multiple sides of the part in a single setup. This reduction in setup time leads to faster production cycles. It increases overall manufacturing throughput, enhancing production efficiency and reducing costs.
3. Enhanced Surface Finish Capabilities
The precise control over tool orientation and path in multi-axis milling also translates to superior surface finishes. With the ability to optimally angle the tool relative to the workpiece, multi-axis machines can achieve smoother surfaces and finer details, often eliminating the need for post-machining finishing processes, such as grinding or polishing.
4. Reduced Need for Secondary Operations
Multi-axis milling's capability to execute complex cuts and achieve precise internal features reduces the dependency on secondary machining operations. This integration of functions not only streamlines the manufacturing process but also minimizes handling and setup errors, further enhancing the quality and consistency of the final product.
5. Ability to Handle Extremely Complex Parts
The additional axes in multi-axis milling provide unmatched versatility in machining. It enables more effective handling of parts with complex contours, undercuts, and deep cavities. As a result, industries that require high levels of detail and precision, such as aerospace, medical, and automotive, rely heavily on multi-axis milling for their critical components.
6. Improved Material Utilization
Multi-axis machines are designed to maximize the material removal rate while minimizing waste. This efficient use of material reduces costs and aligns with sustainable manufacturing practices by decreasing scrap.
These advantages demonstrate why multi-axis milling is considered a cornerstone of advanced manufacturing. By enabling the production of complex parts more efficiently and with higher quality, multi-axis milling helps industries meet demanding production schedules and stringent quality standards. This technology continues to evolve, pushing the boundaries of what can be achieved in precision machining.
Applications of Multi-Axis Milling
Multi-axis milling is a versatile and powerful machining process that finds applications across various industries. Its ability to produce complex shapes with high precision makes it indispensable in sectors where intricate designs and tight tolerances are the norm. Here’s an overview of some of the primary applications of multi-axis milling:
1. Aerospace
In the aerospace industry, precision and reliability are paramount. Multi-axis milling manufactures critical components such as turbine blades, engine mounts, and landing gear parts. These components often feature complex geometries that are only feasible with the capabilities of multi-axis machines, ensuring that they meet the industry's stringent safety and performance standards.
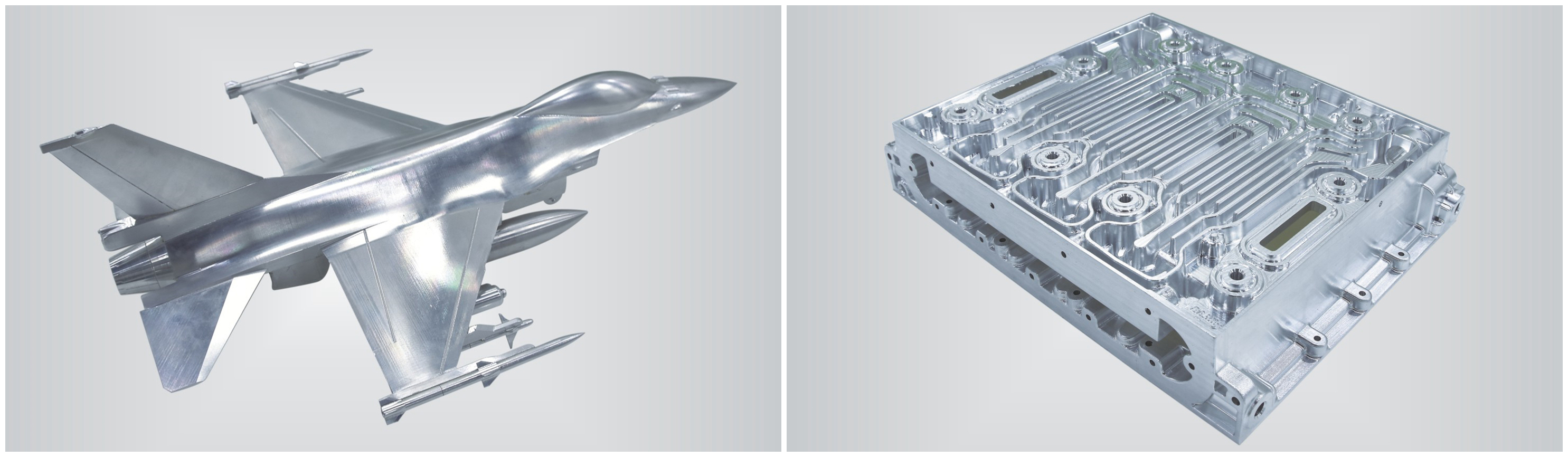
2. Automotive
Multi-axis milling is crucial in the automotive sector, especially in producing high-performance engine components, transmission housings, and suspension systems. These parts require precise machining to ensure they perform reliably under extreme conditions. The flexibility of multi-axis milling also allows custom modifications and prototypes to be produced much more efficiently than traditional methods.
3. Medical
The medical field benefits significantly from the advanced capabilities of multi-axis milling. This process is used for creating complex surgical instruments and implants, such as joint replacements and bone screws. Working with various biocompatible materials and achieving the necessary precision and smooth finishes is crucial for medical devices, which directly impact patient outcomes.
4. Electronics
Multi-axis milling is also integral to the electronics industry, where it is used to create components of enclosures, heat sinks, and other critical parts of electronic devices. These components often require exact features and smooth surfaces to ensure the proper functionality and longevity of the electronic products.
5. Mold Making
The mold-making process benefits from multi-axis milling through its ability to machine complex molds with fine details and excellent surface finishes. These molds are used in various applications, including plastic injection molding, die casting, and glass molding, requiring high accuracy to ensure the quality of the final products.
6. Tool and Die Making
Multi-axis milling is essential for tool and die making, providing the precision necessary for creating dies, jigs, and fixtures used throughout the manufacturing industry. These tools often have complex shapes and must meet exact specifications to function correctly in their respective applications.
7. High-Tech Research and Development
In research and development, multi-axis milling enables the fabrication of components with experimental designs and new materials. This capability is vital for developing new products and technologies, allowing researchers and developers to prototype and test their ideas efficiently.
The diverse applications of multi-axis milling underscore its importance in modern manufacturing. By enabling the production of complex, high-quality parts, multi-axis milling enhances the capabilities of the industries it serves and drives innovation, pushing the boundaries of what can be manufactured. As technology advances, the applications of multi-axis milling are likely to expand, further entrenching its role as a critical player in the manufacturing sector.
Future Trends and Technological Advancements in Multi-Axis Milling
As industries evolve and demand more sophisticated and precise manufacturing techniques, multi-axis milling is also advancing. Here’s a look at some of the key future trends and technological advancements that are shaping the future of multi-axis milling:
Our Services
Are you looking to improve manufacturing processes or develop complex components with unmatched precision? Consider exploring the power of multi-axis milling. Contact us at Neway to learn more about our advanced multi-axis milling solutions and how they can be integrated into your production to drive efficiency, reduce costs, and enhance product quality. Reach out today to schedule a consultation with one of our experts, or visit our website for more information on our capabilities and services. Let us help you take your manufacturing operations to the next level with state-of-the-art multi-axis milling technology.
评论
发表评论