Engineering thermoplastics are a cornerstone in advanced manufacturing, offering remarkable versatility and performance across various applications. From high-strength components in the automotive sector to precision medical devices, these materials have revolutionized industries with their superior mechanical properties, chemical resistance, and thermal stability. This comprehensive guide delves into the art and science of injection molding manufacturing using engineering thermoplastics, providing key insights that span from basic concepts to sophisticated techniques.
Injection molding of engineering thermoplastics is critical for producing consistent, high-quality parts efficiently and cost-effectively. Understanding the nuances of this process is essential not only for seasoned engineers but also for newcomers to the field who are looking to enhance their manufacturing capabilities. Through this guide, we aim to explore the various aspects of injection molding, including selecting appropriate materials, machinery setup, process optimization, and innovative manufacturing techniques that leverage the unique properties of engineering thermoplastics.
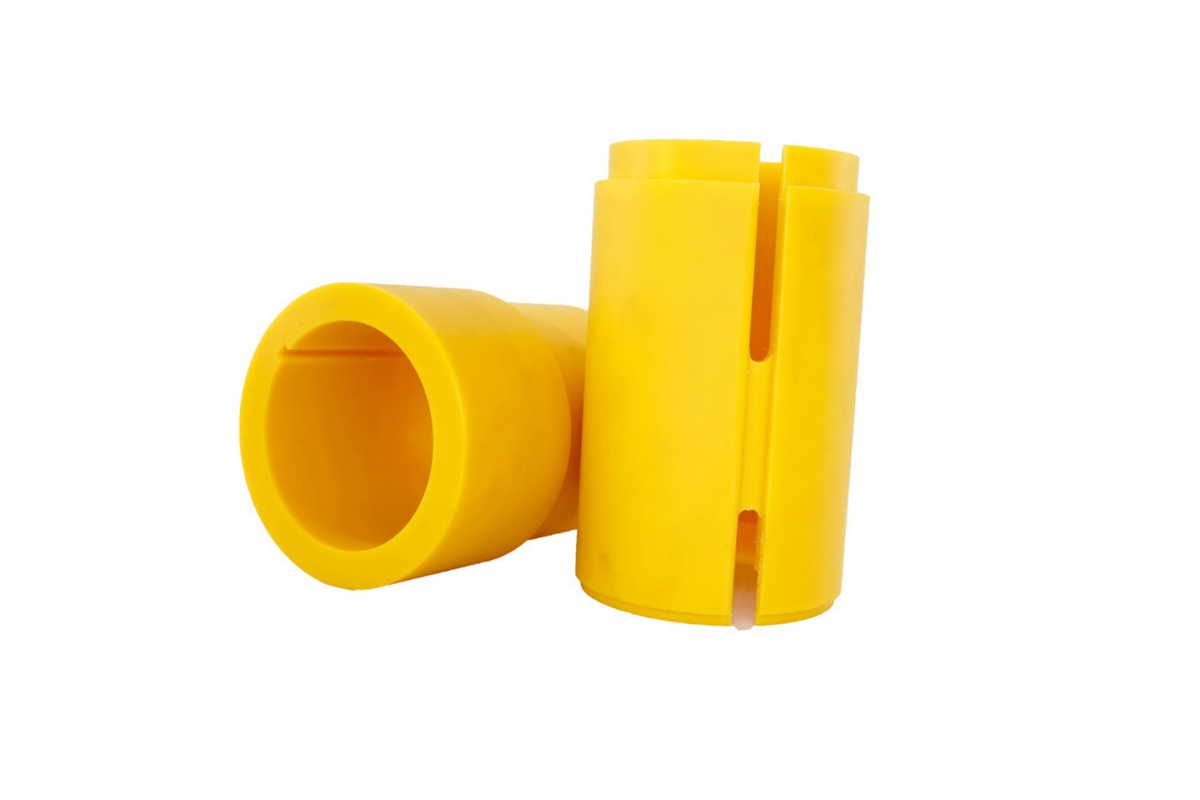
Basics of Injection Molding
Injection molding is a versatile and widely used manufacturing process for producing parts by injecting molten material into a mold. Particularly effective with engineering thermoplastics, this method is pivotal for creating components in the automotive and consumer electronics industries. This section introduces the fundamental aspects of injection molding, emphasizing its significance and utility in manufacturing with engineering thermoplastics.
Definition and Process Overview
Injection Molding Explained: At its core, injection molding involves heating plastic granules until they melt, then injecting the molten plastic into an exact mold at high pressure. Once the material fills the mold, it is cooled, solidified, and ejected as a finished part. This process is repeated cycle after cycle with remarkable consistency.
Steps in the Injection Molding Process:
Material Preparation: Plastic pellets are dried and fed into the injection molding machine.
Melting: The pellets are heated and melted in the machine's barrel.
Injection: The molten plastic is injected into the mold under controlled pressure.
Cooling and Solidification: The plastic cools and solidifies into the shape of the mold.
Ejection: The solidified part is ejected from the mold, and the process repeats.
Advantages of Injection Molding for Engineering Thermoplastics
Efficiency and Speed: Injection molding allows for the mass production of parts with short cycle times, making it highly efficient.
Repeatability: The high precision of the molds used in injection molding ensures that each part is virtually identical. It is critical for large-scale production, where consistency is vital.
Material and Design Flexibility: Engineering thermoplastics are favored for their ability to be molded into complex shapes and designs, which injection molding can readily accommodate. This flexibility extends to using different materials or blends, providing engineers with numerous options to meet specific application requirements.
Cost-Effectiveness: Although the initial cost of developing molds can be high, the per-unit cost of production is significantly reduced for large runs, making injection molding a cost-effective solution for manufacturing durable and complex parts.
Injection molding of engineering thermoplastics provides the benefits of durability and high performance. It offers the versatility needed to innovate and meet the evolving demands of various industries. Understanding these basics sets the stage for deeper exploration into more complex aspects of injection molding, including the selection of materials, machine types, and specialized molding techniques that can further enhance the quality and functionality of the final products.
Common Engineering Thermoplastics Used in Injection Molding
Engineering thermoplastics are valued for their exceptional strength, durability, and resistance to harsh environments, making them ideal for various applications. This section explores some of the most commonly used engineering thermoplastics in injection molding, detailing their properties, benefits, and typical applications. Understanding these materials is crucial for selecting the suitable thermoplastic for specific manufacturing needs.
Material Profiles
ABS (Acrylonitrile Butadiene Styrene)
Properties: ABS combines the strength and rigidity of acrylonitrile and styrene with the toughness of polybutadiene rubber. It is well-known for its good impact resistance, toughness, and surface hardness.
Benefits: ABS is easy to mold and provides a balanced combination of mechanical toughness, impact resistance, and aesthetic qualities.
Applications: Widely used in automotive components, consumer goods, and electronic housings due to its excellent surface finish and durability.
Properties: Nylon is known for its high strength, temperature resistance, and excellent wear properties. It also has good chemical resistance and performs well under mechanical stress.
Benefits: Offers significant flexibility in processing and design and is particularly effective for parts requiring high strength and stiffness.
Applications: Commonly used in automotive under-the-hood parts and mechanical gears, as a replacement for metal in many applications due to its light weight and strength.
Properties: Polycarbonate is distinguished by its strength, stiffness, and impact resistance. It also has a high degree of transparency.
Benefits: PC can be used in applications requiring high precision, dimensional stability, and transparency. It is also resistant to heat and impacts.
Applications: Often used in automotive lighting components, safety helmets, and bullet-proof glass alternatives.
Properties: PEEK offers exceptional thermal stability, chemical resistance, and wear resistance. It can withstand high temperatures and aggressive environments.
Benefits: High-performance material suitable for challenging industrial applications, offering longevity and reliability under extreme conditions.
Applications: Ideal for aerospace components, high-performance liquid chromatography columns, medical implants, and automotive parts where high temperature, chemical exposure, and mechanical performance are required.
Properties: Known for its low moisture absorption, excellent dimensional stability, and high heat resistance.
Benefits: It provides stable electrical properties and good mechanical characteristics, making it suitable for precision-demanding applications.
Applications: Used in electrical and electronic insulation, automotive parts, and medical devices where stability and performance are critical.
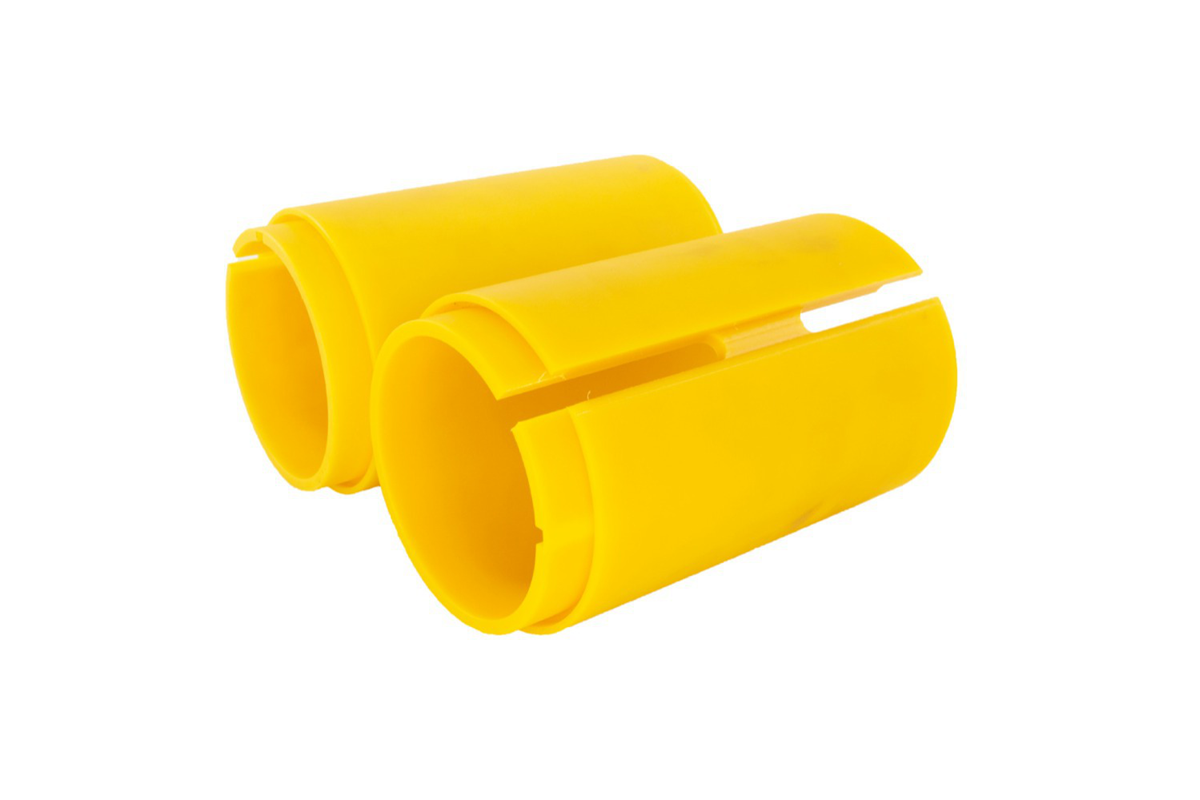
Selection Criteria
Thermal Resistance: Choose materials like PEEK and PPO for high heat resistance applications.
Mechanical Properties: Materials like Nylon and Polycarbonate offer high strength and durability for structural components.
Environmental Resistance: PEEK and PPO are excellent choices for applications exposed to harsh chemicals due to their superior chemical resistance.
Aesthetic Requirements: ABS and Polycarbonate are preferable for applications requiring an excellent aesthetic finish with options for transparency and color.
Machinery and Equipment
The success of injection molding with engineering thermoplastics hinges on the material selection and the machinery and equipment used in the process. This section details the different types of injection molding machines and the critical aspects of tooling and mold design that are essential for producing high-quality thermoplastic parts.
Types of Injection Molding Machines
Hydraulic Machines:
Description: Traditional hydraulic injection molding machines use hydraulic systems to power all machine movements, including clamping, injection, and ejection.
Advantages: These machines offer robust force and are highly effective for producing large parts. They are also generally less expensive compared to other types of machines.
Considerations: While powerful, hydraulic machines are less energy-efficient than electric machines and can be slower in cycle times.
Electric Machines:
Description: Electric injection molding machines use servo motors to power all movements, providing greater accuracy, repeatability, and energy efficiency.
Advantages: These machines offer precision control over all process parameters, which is crucial for engineering thermoplastics known for their stringent processing requirements. They also operate more quietly and with greater energy efficiency.
Considerations: Electric machines have a higher initial cost and are generally used for high-precision and control applications.
Hybrid Machines:
Description: Hybrid injection molding machines combine the best features of hydraulic and electric systems, using electricity for movements requiring precision and hydraulics for processes requiring deep force.
Advantages: Hybrids provide a good balance of power, speed, and energy efficiency, making them versatile for various applications.
Considerations: These machines can be complex in terms of maintenance due to the integration of hydraulic and electric systems.
Tooling and Mold Design
Material Selection for Molds:
Tool Steels: Often used for molds due to their high wear resistance and ability to withstand high pressures and temperatures. Tool steels are ideal for high-volume production runs.
Aluminum: Offers faster heat dissipation and shorter cycle times. Aluminum molds are cost-effective for prototypes and low-volume production.
Design Considerations:
Mold Layout: Ensuring optimal gating, runner systems, and venting is crucial to prevent defects and ensure the quality of molded parts.
Cooling Systems: Proper design of the cooling systems is vital to manage the temperatures effectively, especially for thermoplastics with high melting points. Efficient cooling helps reduce cycle times and improve part quality.
Ejection System: This system must be carefully designed to prevent damage to the finished parts. It is essential for engineering thermoplastics that may be more brittle or stress-sensitive.
Advanced Mold Technologies:
Conformal Cooling Channels: These are designed to follow the part's contour, allowing for more uniform cooling and faster cycle times.
Hot Runner Systems: Used to maintain a molten plastic flow directly into the cavities, reducing material waste and improving cycle times.
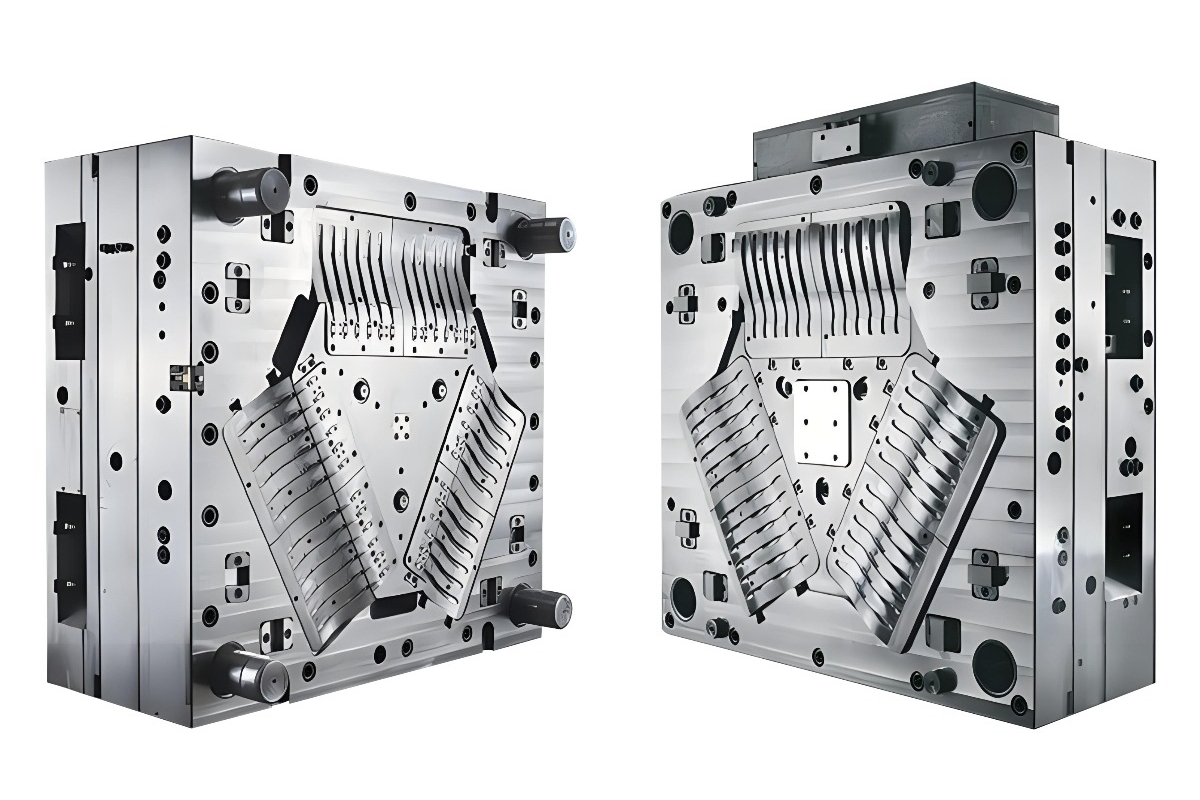
Maintenance and Upkeep
Regular maintenance is essential to ensure the longevity and efficiency of injection molding machines and molds. It includes routine checks, lubrication, cleaning, and immediate wear and tear repair.
Process Parameters and Optimization
Optimizing the process parameters in injection molding is critical for achieving high-quality parts, especially when working with engineering thermoplastics known for their stringent processing requirements. This section covers the key parameters that must be managed and offers strategies for optimizing each to ensure successful molding operations.
Temperature Settings
Melt Temperature: This is the temperature at which the plastic granules are melted before injection. Setting the correct melt temperature for each engineering thermoplastic ensures proper flow and prevents thermal degradation. For instance, a too high temperature can lead to material degradation. At the same time, a too low temperature might not allow the material to flow adequately into the mold.
Mold Temperature: The mold temperature significantly impacts the cooling rate and cycle time. A higher mold temperature improves the surface finish, reduces internal stresses, and increases cycle times. The optimal mold temperature depends on the specific thermoplastic material and the part design.
Pressure and Injection Speed
Injection Pressure: This is the pressure at which the molten plastic is injected into the mold. Adequate pressure must be maintained to ensure complete cavity filling without causing damage or excessive stress to the part. Different materials and part geometries require adjustments to the injection pressure to achieve the best results.
Injection Speed: The speed at which the molten plastic is injected into the mold affects the quality of the part, particularly around how the material fills the mold cavities. Too fast an injection speed can create turbulence and lead to air entrapment or other defects. However, too slow speed might result in premature cooling and incomplete filling.
Cooling Time and Cycle Time
Cooling Time: Proper cooling is essential to solidify the part without warping or creating internal stresses. The cooling time must be optimized based on the thickness of the part and the thermal properties of the thermoplastic used.
Cycle Time: Overall cycle time includes injection, cooling, and mold opening/ejection times. Optimizing cycle time balances achieves sufficient cooling and maximizes production efficiency.
Troubleshooting Common Issues
Warping: This can be minimized by ensuring uniform wall thickness during the design phase and optimizing cooling patterns in the mold.
Sink Marks: Occur due to insufficient cooling time or inadequate pressure in the thicker sections of a part. Adjusting holding pressure and cooling time can help alleviate this issue.
Short Shots: Caused by inadequate mold filling, which can be corrected by increasing the melt temperature or injection pressure.
Advanced Optimization Techniques
Scientific Molding: This approach involves rigorous data collection and analysis to understand and optimize all aspects of the injection molding process. Key variables are monitored in real-time to ensure consistent quality.
Design of Experiments (DOE): Used to systematically test changes in process parameters and determine their impact on part quality. This method helps identify optimal settings for all variables.
Advanced Techniques in Thermoplastic Injection Molding
As the demand for complex and high-performance plastic parts increases, manufacturers are turning to advanced injection molding techniques to meet these challenges. These sophisticated methods enhance the functionality and aesthetics of products and offer greater efficiency and precision in the manufacturing process. This section explores some advanced techniques in thermoplastic injection molding that are being used to push the boundaries of what can be achieved with engineering plastics.
Overmolding and Insert Molding
Overmolding: This technique involves molding a layer of plastic over a previously molded part. It is used to add soft-touch surfaces on rigid substrates or to create multi-material components that combine different properties, such as rigidity and flexibility. Overmolding can enhance the part’s aesthetic appeal and functionality without requiring assembly, providing improved structural integrity and design flexibility.
Insert Molding: Insert molding involves placing an insert (often made of metal or a different type of plastic) into the mold cavity and injecting thermoplastic around it. The result is a single piece with multiple materials integrated seamlessly. This technique suits parts requiring reinforced structural strength, integrated fasteners, or electrical conductivity.
Micro-Molding
Description: Micro-molding is a specialized injection molding that focuses on manufacturing tiny and precise thermoplastic components. This technique requires specialized equipment and expertise to handle the high precision and technical challenges of producing miniature parts.
Applications: Micro-molding is widely used in medical devices, microelectronics, and micro-optics, where tiny plastic parts with tight tolerances are required. It allows for producing micro-sized features on parts with complex geometries and excellent surface finish.
Gas-Assisted Injection Molding
Process Overview: In gas-assisted injection molding, a portion of the molten thermoplastic is injected into the mold, followed by high-pressure gas (usually nitrogen). The gas pushes the plastic into the mold extremities, forming a hollow channel within the part.
Benefits: This technique reduces material usage and part weight, improves dimensional stability, and eliminates sink marks and warping. It is particularly beneficial for large or thick components that need to be lightweight yet strong.
Water-Assisted Injection Molding
Similarities to Gas-Assisted: Like gas-assisted molding, water-assisted injection molding involves injecting water into the mold cavity following the injection of the molten plastic. Water, however, offers better cooling capabilities and faster process times.
Advantages: This method provides enhanced cooling efficiency and faster cycle times. It is ideal for creating hollow or tubular parts, which results in improved surface quality and part strength.
Bi-Injection and Multi-Component Molding
Technique: Bi-injection or multi-component molding involves injecting two different materials into the same mold during a single molding cycle. It can be done using a single machine with two injection units or a rotary mold that shifts between two injection positions.
Functionality: This method allows for producing complex parts with multiple colors or materials without requiring assembly. It is used for products that require different physical properties in different sections of the part, such as hard and soft areas.
Enhancing Properties with Additives and Fillers
In engineering, thermoplastic injection molding, additives, and fillers play a pivotal role in modifying and enhancing the properties of plastics to meet specific application requirements. These enhancements can significantly improve performance, aesthetic qualities, and processing characteristics, allowing manufacturers to tailor materials to fit the demands of various industries more precisely. This section outlines the additives and fillers commonly used in thermoplastics and their benefits in injection molding.
Types of Additives:
Flame Retardants:
Purpose: To reduce thermoplastic flammability and increase ignition and burning resistance.
Applications: Crucial for electrical and electronic housings, automotive components, and any application where fire safety is a priority.
UV Stabilizers:
Purpose: To protect plastics from degradation due to exposure to ultraviolet light, which can cause discoloration and loss of mechanical properties.
Applications: Essential for outdoor products such as automotive exteriors, garden equipment, and outdoor furniture.
Impact Modifiers:
Purpose: To improve the toughness of plastic parts without significantly reducing their stiffness or introducing other undesirable properties.
Applications: Used in products that require high impact resistance, such as protective gear, vehicle bumpers, and robust enclosures.
Role of Fillers:
Glass Fibers:
Benefits: Increase tensile strength, dimensional stability, and heat resistance. Glass fibers reduce shrinkage and warping during molding.
Applications: Widely used in automotive parts, industrial applications, and consumer electronics where additional strength is needed.
Carbon Fibers:
Benefits: Provide greater strength and stiffness than glass fibers and a significant weight reduction. Carbon fibers also enhance the electrical conductivity of plastics.
Applications: Ideal for aerospace and automotive sectors, sporting goods, and any application where weight reduction and high performance are critical.
Mineral Fillers (such as talc or calcium carbonate):
Benefits: Improve dimensional stability and rigidity and reduce the cost of materials.
Applications: Used in household appliances, automotive parts, and construction materials where increased stiffness and reduced part cost are desirable.
Optimizing Additive and Filler Use:
Compatibility: Ensure that the selected additives and fillers are compatible with the base resin and do not adversely affect the material’s inherent properties.
Dispersion: Achieve uniform dispersion within the polymer matrix to maximize the effectiveness of additives and fillers. Poor dispersion can lead to defects and diminished performance.
Concentration: Balance the concentration of additives and fillers to optimize the desired properties without compromising the plastic’s processability or physical properties. Excessive amounts can lead to issues such as brittleness or processing difficulties.
Advanced Compounding Techniques:
Masterbatching: Pre-mixing additives or fillers with polymers in concentrated form (masterbatch) before introducing them into the main polymer batch. This technique ensures better control over dispersion and concentration.
Nanocomposites: Incorporating nanoscale fillers to achieve property enhancements at lower filler loadings than conventional fillers, often leading to improvements in mechanical properties, barrier properties, and flame retardancy.
评论
发表评论