In the dynamic and ever-evolving world of manufacturing and design, 3D printing technologies have emerged as a beacon of innovation, reshaping how products are conceptualized, designed, and brought to life. Among the myriad additive manufacturing techniques, Selective Laser Sintering (SLS) stands out for its versatility, ability to produce complex geometries, and the durability of its fabricated parts. Developed in the mid-1980s, SLS has steadily grown from a novel manufacturing process to a cornerstone technology in rapid prototyping and direct digital manufacturing.
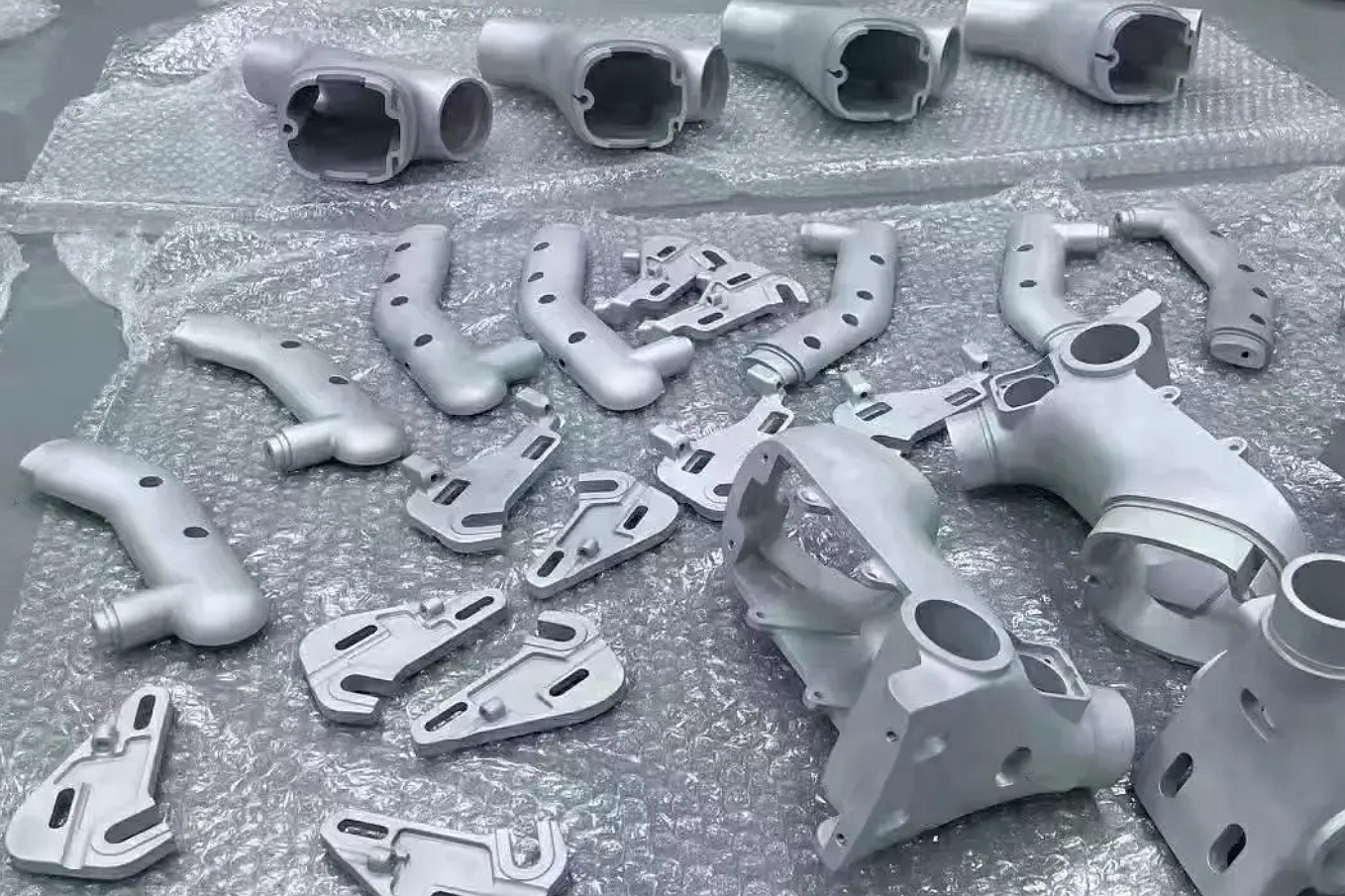
Selective Laser Sintering (SLS) employs a high-powered laser to fuse small particles of polymer powder, metal, or other materials into a solid, three-dimensional object. The process is distinguished by its unique ability to create parts that are robust, complex, and ready for functional use without the need for additional support structures. This capability streamlines the manufacturing process and opens up new avenues for design innovation previously constrained by traditional manufacturing methods' limitations.
The Basics of Selective Laser Sintering (SLS)
Selective Laser Sintering (SLS) is a powerful 3D printing technique that has carved a niche in the additive manufacturing world, offering unparalleled flexibility in design and production. As we delve into the basics of SLS, it's essential to understand what sets this technology apart and how it has evolved to become a vital tool in various industries.
Definition and Development
Selective Laser Sintering (SLS) is an additive manufacturing process that uses a laser to sinter powdered material, typically plastic, metal, ceramic, or glass, binding the material together to create a solid structure. Unlike other 3D printing techniques that require support structures, SLS builds parts by fusing material layer by layer from the bottom up, creating complex geometries with considerable freedom in design.
The concept of SLS was developed in the mid-1980s by Dr. Carl Deckard and Dr. Joe Beaman at the University of Texas at Austin. The technology was commercialized in the late 1980s, and since then, it has undergone significant advancements, expanding its material capabilities and finding new applications across a broad spectrum of industries.
The SLS Process Explained
The SLS process involves a few key components: a high-powered laser, a powder bed, and a build platform. Here's a simplified overview of how SLS works:
Preparing the Build Chamber: The build chamber is preheated to a temperature just below the melting point of the powder material. This preheating ensures that the laser can more efficiently sinter the powder particles.
Powder Deposition: A thin layer of powder is spread across the build platform. The thickness of this layer can vary but typically ranges from 0.1 to 0.15 mm.
Laser Sintering: The laser selectively targets and sinters the powder according to the cross-section of the 3D model, binding the particles together to form a solid layer.
Lowering the Build Platform: After a layer is sintered, the build platform lowers, and a new layer of powder is spread on top. The process repeats until the part is fully built.
Cooling and Cleaning: The entire build chamber is allowed to cool before the finished parts are removed. Excess powder is cleaned off and often recycled for future use.
Critical Components of an SLS Printer
Laser: The laser in an SLS printer is precisely controlled and focused on accurately sintering the powder material. Its intensity and speed are crucial factors in determining the quality of the finished product.
Powder Bed: This is where the powdered material is deposited and sintered layer by layer. The powder bed also supports the part during printing, eliminating the need for additional support structures.
Build Platform: The platform within the build chamber where the object is printed. It lowers incrementally after each layer is sintered to allow the addition of new powder layers.
How SLS Works - The Technical Process
Delving deeper into the technical workings of Selective Laser Sintering (SLS), we uncover the intricate process that transforms powdered materials into solid, functional parts. This section breaks down the SLS process into a step-by-step explanation, shedding light on the sophisticated interplay of heat, material, and laser precision that defines this additive manufacturing technique.
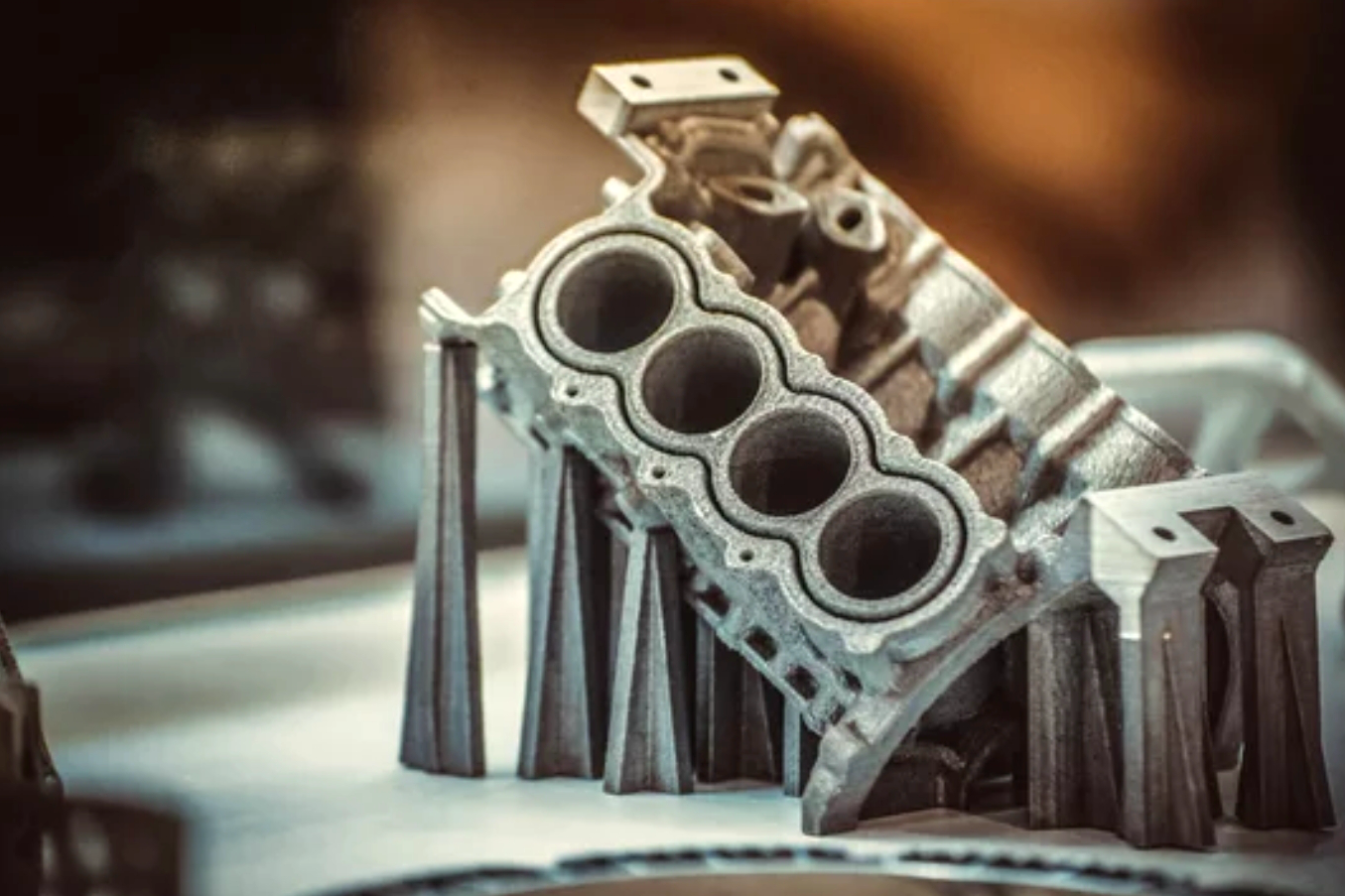
Step-by-Step Explanation of the SLS Process
Preparation and Digital Modeling
Before printing begins, a digital 3D model of the object to be manufactured is created using CAD (Computer-Aided Design) software. This model is then converted into a.STL or similar file format slices the model into thin, horizontal layers to be built sequentially.
Powder Dispersion
The SLS machine preheats to a temperature below the powder material's melting point. A recoating blade or roller spreads a thin layer of powder onto the build platform. Consistency in layer thickness is crucial for detail accuracy and part strength.
Laser Sintering
A high-power laser scans the first layer of the powder, selectively sintering (fusing) the powder according to the slice taken from the CAD model. The laser heats the powder just above its melting point, causing the particles to bond without fully melting, forming a solid layer.
Building the Object
After the first layer is sintered, the build platform lowers by the thickness of one layer. A new layer of powder is spread over the sintered surface, and the laser process repeats, bonding the new layer to the previous one. This cycle continues, building the object layer by layer from the bottom up.
Cooling and Post-Processing
Once the printing is complete, the build chamber is allowed to cool, which can take several hours, depending on the size and complexity of the part(s). The finished objects are then excavated from the powder bed. Excess powder is removed through brushing or air blowing and can often be reused for future prints. Additional post-processing steps, such as sandblasting, coloring, or infiltration with other materials, may be applied to achieve the desired finish and mechanical properties.
Role of Temperature Control and Inert Atmosphere
Temperature Control: Maintaining the correct temperature within the build chamber is critical for SLS. The preheated bed helps minimize thermal gradients, ensuring uniform sintering across the part. This control is vital for achieving optimal mechanical properties and dimensional accuracy in the final product.
Inert Atmosphere: Many SLS machines operate under an inert atmosphere, typically nitrogen or argon, to prevent any oxidation of the powder material during sintering. Metal SLS processes must ensure the finished parts' purity and integrity.
Materials Used in SLS Printing
Selective Laser Sintering (SLS) stands out in the 3D printing world for its wide range of material compatibilities, enabling the creation of parts that meet various functional and aesthetic requirements. This versatility makes SLS a preferred choice for many industries, from aerospace to fashion. Let's explore the types of materials commonly used in SLS printing, their advantages, and how they compare with materials used in other 3D printing technologies.
Overview of SLS Materials
Polymers: The most commonly used SLS materials are Nylon 11 and Nylon 12. These materials are prized for their excellent strength, flexibility, and durability balance. They can be used in various applications, including functional prototypes, end-use parts, and complex assemblies.
Metals: SLS technology extends to metal powders, such as aluminum, steel, and titanium. Metal SLS produces highly durable and heat-resistant parts for aerospace, automotive, and medical applications. This process is often called Direct Metal Laser Sintering (DMLS).
Composites and Filled Materials: Composite powders containing a base material mixed with glass, carbon fibers, or other additives are used to enhance specific properties like stiffness, thermal resistance, or electrical conductivity. These materials expand the functionality of SLS parts beyond what pure polymers or metals can offer.
Ceramics: While less common, ceramics are another group of materials compatible with SLS. They are used for applications requiring high-temperature resistance, biocompatibility, or specific electrical properties.
Advantages of Using Powdered Materials
Recyclability: One of the significant advantages of using powdered materials in SLS is the high degree of recyclability. Unused powder can be reused for subsequent prints, reducing waste and lowering material costs.
Support-Free Structures: SLS does not require support structures since unsintered powder supports the part during printing. This feature enables the creation of complex geometries and internal features without the post-processing hassle of removing supports.
Material Efficiency: The ability to sinter only the necessary material for each layer means SLS is exceptionally material-efficient. This efficiency is crucial for expensive materials like metals and composites.
Comparison with Other 3D Printing Technologies
Material Diversity: Compared to Fused Deposition Modeling (FDM) and Stereolithography (SLA), SLS offers a broader range of functional materials, particularly in high-performance polymers and metals.
Functional Parts: While FDM and SLA are excellent for prototyping and aesthetic models, SLS materials generally provide better mechanical properties, making them suitable for functional parts and end-use applications.
Finish and Detail: SLA can achieve finer details and smoother surface finishes than SLS; however, SLS parts are more robust and more suitable for applications where function takes precedence over form.
Advantages of SLS Over Other Additive Manufacturing Techniques
Selective Laser Sintering (SLS) has cemented as a pivotal technology in the additive manufacturing landscape, offering unique benefits that distinguish it from other 3D printing methods. Its ability to produce high-strength, durable parts with complex geometries without supporting structures makes SLS a game-changer for many industries. Here, we explore the critical advantages of SLS and how it stands out from other additive manufacturing techniques.
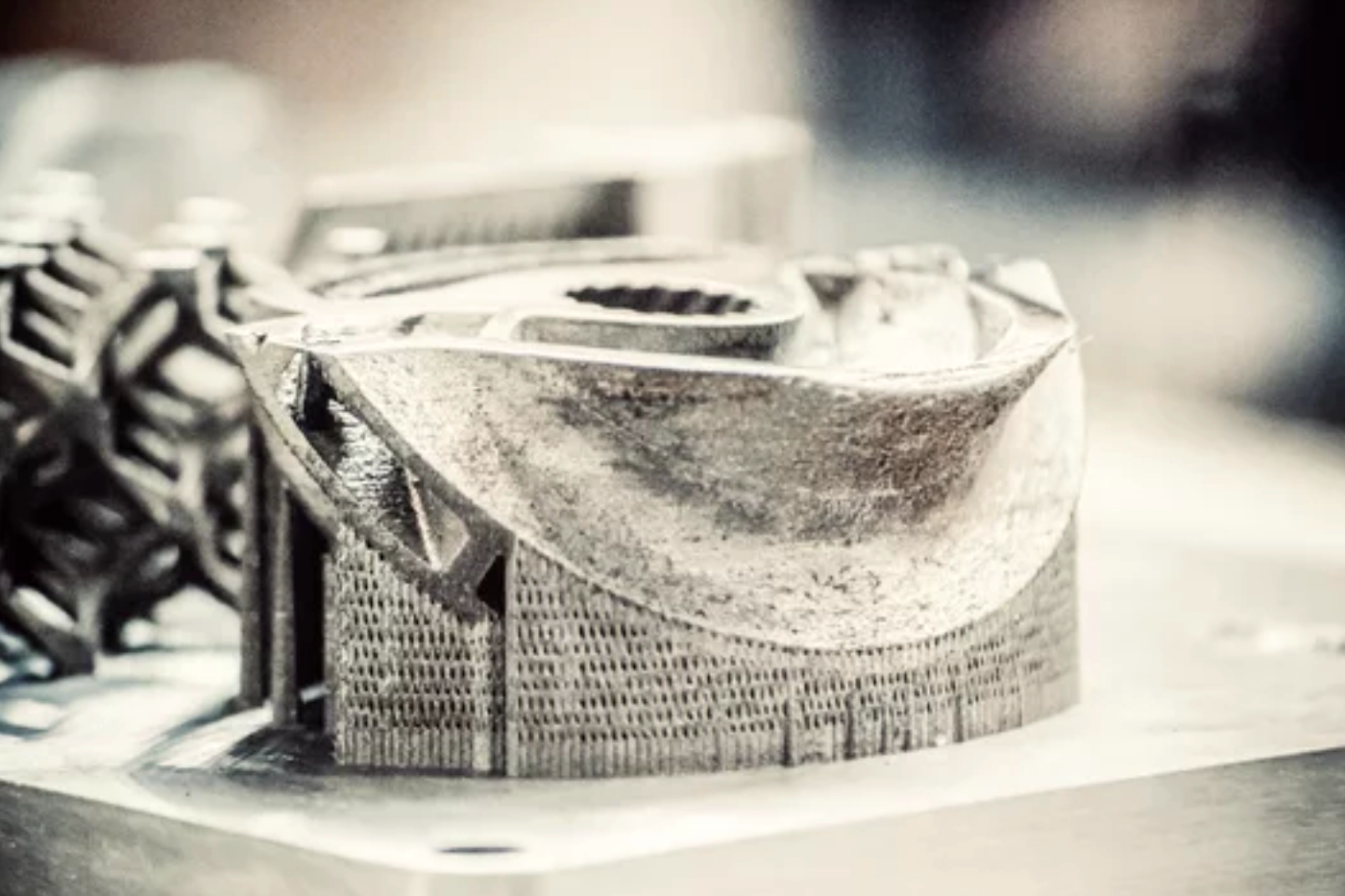
Versatility of Materials
SLS printing's compatibility with various materials, from high-performance polymers and metals to innovative composites, allows designers and engineers to choose materials that best suit their specific application requirements. This versatility ensures that SLS can create functional prototypes, end-use parts, and everything across various sectors.
Complex Geometries and Detailed Parts
One of the standout features of SLS is its ability to fabricate parts with intricate details and complex internal geometries—capabilities that are often limited or impossible with technologies like Fused Deposition Modeling (FDM) or Stereolithography (SLA). The powder bed in SLS supports the sintered material, allowing for the creation of designs with overhangs, undercuts, and internal channels without additional support structures.
High Strength and Durability
Parts produced through SLS are known for their strength and durability, making them suitable for functional testing and end-use applications. The sintering process results in nearly isotropic parts, meaning their strength and mechanical properties are consistent in all directions. This characteristic is essential for components subjected to dynamic loads or those requiring high-impact resistance.
Efficiency in Batch Production
SLS's ability to efficiently produce batches of parts by nesting them within the build volume optimizes the use of space and materials. This efficiency reduces production times and costs, making SLS an excellent choice for small to medium batch production. The capacity to run the printer unattended for extended periods further enhances production efficiency.
Minimized Waste and Recyclability
The powder-based nature of SLS allows for the recycling of unused material, significantly reducing waste and lowering material costs compared to other additive manufacturing processes. The ability to reuse powder multiple times without significantly compromising the quality of the final parts underscores the sustainability aspect of SLS printing.
Comparison with Other Additive Manufacturing Technologies
While SLA can achieve smoother surface finishes and finer details, SLS excels in producing parts with superior mechanical properties and complex geometries. Unlike FDM, SLS offers more excellent material options and the ability to print more intricate designs without support structures. However, FDM may be more accessible for entry-level applications due to its lower equipment cost.
Practical Applications of SLS Technology
Selective Laser Sintering (SLS) technology has transformed various industries by offering a flexible, efficient, and robust method for producing parts. Its unique advantages, such as creating complex geometries without support structures and using a wide range of materials, have opened up new possibilities for design and manufacturing. This section explores the diverse applications of SLS across different sectors, illustrating its impact and versatility.
Aerospace and Automotive
In the aerospace and automotive industries, SLS manufactures lightweight, durable components that can withstand the demanding environments of air and space travel and on-road performance. From intricate parts like ductwork and fuel system components to custom tooling and fixtures for assembly lines, SLS offers the precision and strength required. Its ability to produce solid and light parts improves fuel efficiency and performance in these sectors.
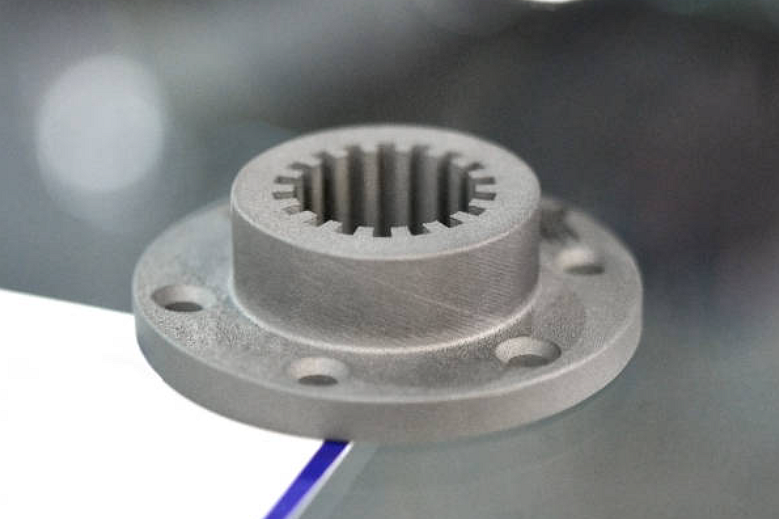
Medical and Dental
The medical and dental fields benefit significantly from SLS technology, especially in customizing patient-specific implants, prosthetics, and surgical tools. The compatibility of SLS with biocompatible materials allows for the creation of custom-fit devices that improve patient outcomes. Additionally, SLS produces intricate dental models and orthodontic devices, streamlining the workflow in dental practices and laboratories.
Consumer Products and Fashion
SLS has notably impacted the consumer goods sector, enabling the design and production of complex, durable products ranging from wearable technology to personalized fashion items. Designers leverage SLS to create bespoke jewelry, eyewear, and footwear that combine aesthetic appeal with personalized fit and comfort. The technology's flexibility also supports rapid prototyping and customization in consumer electronics, allowing for the swift development of ergonomic and functional designs.
Industrial and Engineering
For industrial applications and engineering projects, SLS is invaluable for creating functional prototypes, end-use parts, and complex tooling with high mechanical properties. Its ability to fabricate parts with internal features and channels enables the production of optimized components for fluid dynamics studies, heat dissipation elements, and lightweight structures for robotics. Moreover, the technology's efficiency in batch production makes it an excellent choice for manufacturing small to medium-sized runs of specialized industrial components.
Art and Architecture
Artists and architects utilize SLS to bring their visionary concepts to life, creating sculptures, models, and functional art pieces that are both intricate and robust. The technology's capacity for detailed, complex structures allows for exploring new forms and textures in architectural models, custom fittings, and decorative elements, pushing the boundaries of traditional design and construction methods.
Comparing SLS with Other 3D Printing Technologies
As the additive manufacturing landscape evolves, understanding the nuances between different technologies becomes crucial for selecting the most suitable method for a project. Selective Laser Sintering (SLS) is often compared to other prominent 3D printing techniques, such as Fused Deposition Modeling (FDM), Stereolithography (SLA), and Direct Metal Laser Sintering (DMLS). This comparative analysis highlights the distinctive features, material options, and application suitability of SLS in contrast to these technologies.
SLS vs. FDM
Material Options: FDM primarily uses thermoplastic filaments, which, while diverse, don't match the strength and functional versatility of the powdered materials used in SLS, including polymers, metals, and composites.
Surface Finish and Detail: SLS parts generally have a more consistent and finer surface finish than FDM due to the powder sintering process, which allows for more detailed and complex geometries without supporting structures.
Application Suitability: FDM is accessible and cost-effective for hobbyist projects and preliminary prototypes. In contrast, SLS is better suited for producing functional prototypes and end-use parts that require higher strength, precision, and complexity.
SLS vs. SLA
Material Durability: SLA parts are known for their high resolution and smooth surface finishes, making them ideal for models and prototypes requiring fine details. However, SLS materials generally offer superior durability and are better suited for functional parts and applications requiring mechanical strength.
Design Flexibility: SLA and SLS allow for complex geometries, but SLS has an advantage in producing functional parts with intricate internal features, thanks to the inherent support provided by the unsintered powder.
Post-Processing: SLA parts often require extensive post-processing, including washing and curing, whereas SLS parts need minimal post-processing, primarily de-powdering, making them quicker to finish and use.
SLS vs. DMLS
Material Range: DMLS is used explicitly for metal 3D printing and offers a range of metal powders. While versatile across polymers and metals, SLS is predominantly recognized for its capabilities in polymer-based applications.
Part Complexity: Both SLS and DMLS excel in producing parts with complex geometries. However, DMLS parts are denser and more suited to high-stress applications in the aerospace and automotive industries.
Production Cost and Speed: SLS is generally faster and more cost-effective for producing polymer parts than DMLS, which requires more energy and post-processing for metal parts.
Guidance on Choosing the Right Technology
Selecting between SLS and other 3D printing technologies depends on several factors, including:
Material Requirements: Consider whether your project needs the durability and versatility of SLS materials or if the aesthetic qualities of SLA resins or the specific properties of FDM filaments are more critical.
Part Complexity and Functionality: Evaluate the complexity of the design and its functional requirements. SLS is preferable for parts with intricate details and complex internal geometries that must withstand functional testing or end-use applications.
Budget and Production Volume: Assess the cost implications and production volume. FDM may be more cost-effective for low-volume, simple prototypes, while SLS is cost-efficient for medium-volume production of complex parts.
What We Can Do In SLS 3D Printing
Selective Laser Melting (SLM) Service: Rapid prototyping and production of nickel, cobalt, and stainless steel superalloys.
Fused Deposition Modeling (FDM) Service: Prototypes and Functional Parts, Jigs and Fixtures, Low-Cost Models.
Stereolithography (SLA) Service: High-Detail Models, Dental and Medical Applications, Jewelry, and Art.
Selective Laser Sintering (SLS) Service: Complex Geometries, End-Use Parts, Snap-Fit Parts.
Multi Jet Fusion (MJF) Service: Functional Prototypes and End-Use Parts, Complex Assemblies, High-Volume Production.
Direct Metal Laser Sintering (DMLS) Service: Aerospace and Automotive Components, Medical Implants and Tools, Heat Exchangers and Custom Tooling.
评论
发表评论