In the swiftly evolving domain of manufacturing and prototyping, 3D printing stands as a beacon of innovation, ushering in an era of speed, precision, and versatility previously unimaginable. Among the technologies that have propelled this revolution, Stereolithography (SLA) and Fused Deposition Modeling (FDM) emerge as foundational pillars, each with distinct mechanisms, applications, and advantages. These technologies have democratized manufacturing, making it accessible to designers, engineers, and businesses of all scales. Still, they have also spurred a renaissance in how products are conceptualized, developed, and brought to market.
SLA, known for its precision and detail, harnesses the power of light to transform liquid resins into solid objects, one meticulous layer at a time. This technology has carved a niche in applications requiring intricate detail and smooth finishes, from dental appliances to intricate jewelry designs. On the other hand, FDM, celebrated for its robustness and efficiency, builds objects by extruding thermoplastic filaments, layer by layer, into durable and functional items. Its versatility spans various applications, from prototype development to creating end-use products in various industries.
An Overview of Stereolithography (SLA) 3D Printing
At the heart of the 3D printing revolution, Stereolithography (SLA) stands as a testament to the power of precision and innovation. Developed in the 1980s, SLA has become one of the most sophisticated additive manufacturing techniques, revered for its ability to create parts with incredible detail and smooth surface finishes. Here's an in-depth look at SLA 3D printing, elucidating its core principles, the mechanics of its operation, and the materials that breathe life into digital designs.
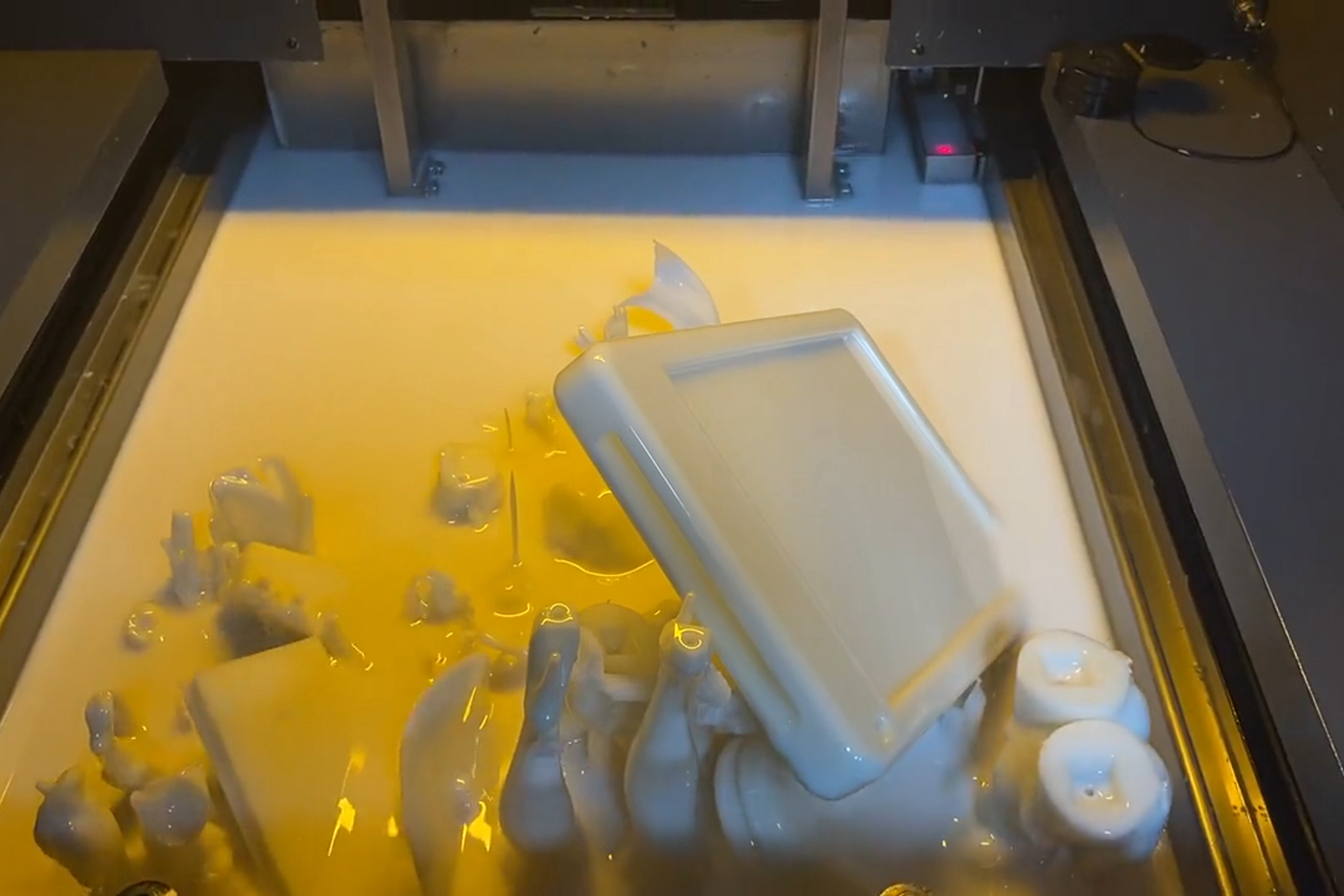
Core Principles of SLA 3D Printing
SLA operates on the principle of photopolymerization, a process where light causes chains of molecules within a photopolymer resin to link together, forming rigid structures. This technology utilizes an ultraviolet (UV) laser directed by computer-controlled mirrors to trace and solidify each layer of an object within a tank of liquid resin. As each layer cures, the build platform moves, allowing the next layer to be traced, gradually creating a three-dimensional object from the bottom up.
Critical Components of an SLA Printer
Light Source: The UV laser is the core component of SLA printers, and it is responsible for curing the resin with pinpoint accuracy.
Resin Tank: This tank holds the photopolymer resin. It's transparent at the bottom, allowing the laser to enter and cure the resin layer by layer.
Build Platform: The platform where the object is built, moving upward as the printing process progresses, pulling the solidified object out of the resin pool.
How SLA Works
Preparation: It begins with slicing a 3D model into hundreds or thousands of horizontal layers using specialized software.
Printing: The UV laser selectively cures the liquid resin, solidifying the areas corresponding to the digital model's first layer. After a layer is cured, the build platform lifts, separating the cured layer from the bottom of the tank and allowing the uncured resin to flow beneath the part. The process repeats layer by layer until the object is complete.
Post-Processing: After Printing, the object requires cleaning in a solvent to remove any uncured resin. Further curing under UV light may be necessary to achieve the final material properties.
Materials Used in SLA Printing
SLA printers use various resins, each formulated for specific properties and applications. These materials can mimic the appearance and functionality of plastics, ceramics, or glass, offering varied characteristics such as transparency, flexibility, or high-temperature resistance. Resin technology innovations continue to expand SLA printing capabilities, enabling applications ranging from detailed prototypes to custom medical devices.
Exploring Fused Deposition Modeling (FDM)
Fused Deposition Modeling (FDM), another titan in 3D printing, offers a distinctly different approach from SLA, championing robustness, material diversity, and ease of use. Developed in the late 1980s, FDM has become synonymous with additive manufacturing, especially for those seeking quick, efficient, and versatile production methods. Here, we delve into the fundamentals of FDM, providing insights into its operational mechanics and the plethora of materials that make it a go-to choice for professionals and hobbyists alike.
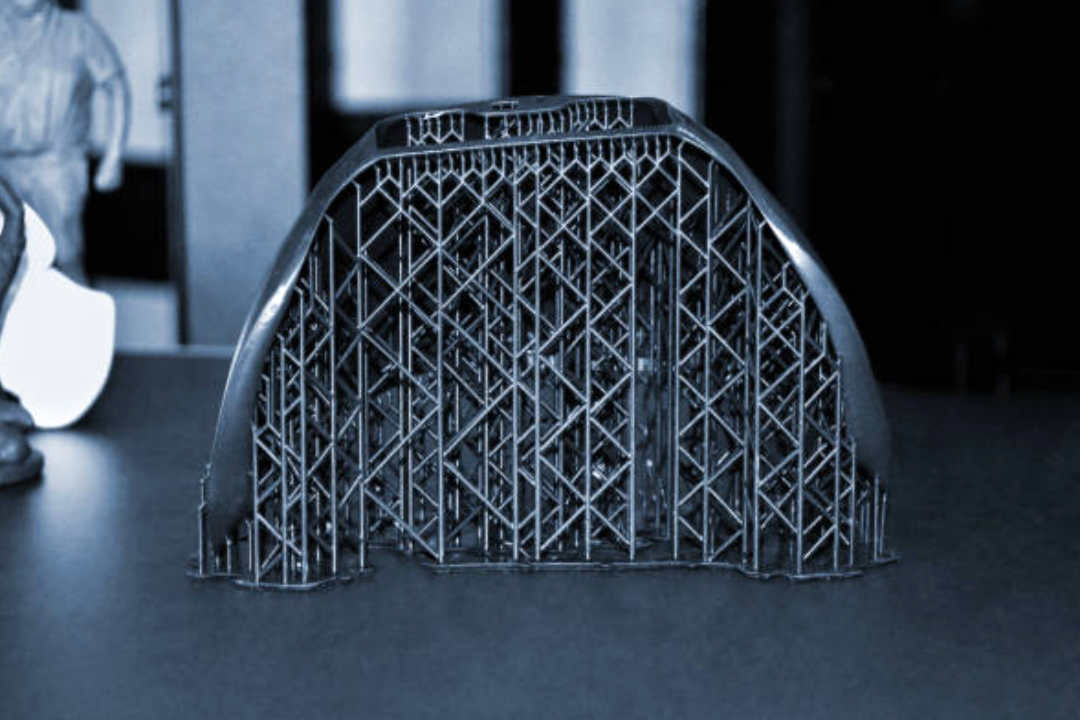
Fundamental Mechanics of FDM
FDM works by extruding thermoplastic filaments through a heated nozzle, meticulously depositing the material layer by layer onto a build platform. The material is melted just before being laid down, fusing with the previous layer as it cools and solidifies. This process is repeated, building up the object precisely, layer by layer.
Overview of the FDM Process
Preparation: The journey begins with the digital model slicing into thin, horizontal layers, preparing a pathway for the printer to follow.
Printing: The printer heats the thermoplastic filament to a state just beyond its glass transition temperature, enabling it to be extruded. The nozzle moves over the build plate, drawing the object's cross-section for each layer. After a layer is complete, the build plate lowers (or the nozzle rises), and the next layer is deposited directly on top of the previous one.
Cooling and Solidification: As the extruded material cools down, it solidifies, bonding with the layer beneath. This cooling process is crucial for the integrity and dimensional accuracy of the printed object.
Types of Filaments Used in FDM
PLA (Polylactic Acid): Known for its ease of use and environmentally friendly nature, PLA is great for prototyping, educational projects, and non-functional items.
ABS (Acrylonitrile Butadiene Styrene): Valued for its strength and durability, ABS is used in functional parts, automotive components, and household goods.
PETG (Polyethylene Terephthalate Glycol): Combining ease of printability with strength and chemical resistance, PETG is ideal for both functional parts and prototypes.
Polycarbonate (PC): a high-performance thermoplastic known for its remarkable clarity, impact resistance, and heat tolerance, making it suitable for various industrial and consumer applications.
TPU (Thermoplastic Polyurethane): a versatile thermoplastic material known for its excellent elasticity, abrasion resistance, and durability. It can be molded into various shapes, making it ideal for flexible and impact-resistant components in diverse industries.
Comparing SLA and FDM: The Technical Perspective
Diving into the technical intricacies of Stereolithography (SLA) and Fused Deposition Modeling (FDM) reveals a landscape where each technology shines in its own right while serving distinct niches within the additive manufacturing ecosystem. This comparison aims to illuminate the fundamental differences between SLA and FDM, guiding users in making informed decisions based on their specific project requirements.
Precision and Resolution
SLA stands out for its exceptional precision and resolution, attributable to the laser's ability to cure resin with pinpoint accuracy. This capability enables SLA to produce parts with smooth finishes and intricate details, making it ideal for applications requiring high aesthetic quality or fine features.
While offering commendable precision, FDM typically showcases visible layer lines and may require post-processing to achieve smooth finishes. Its resolution is generally lower than SLA, making it less suitable for objects with intricate details but well-suited for functional prototypes and parts.
Speed and Efficiency
SLA printing times can vary significantly based on the object's size, the intricacy of details, and the resin's curing speed. While not the fastest technology for all applications, SLA is highly efficient for producing small to medium-sized parts with complex geometries.
FDM is often praised for its speed in creating more significant and less detailed objects. The direct nature of the extrusion process allows for relatively quick production times, especially for objects with more considerable layer heights, which can be adjusted to strike a balance between speed and detail.
Material Diversity
SLA resins have evolved dramatically from flexible to rigid, transparent to opaque, and standard to high temperature. This diversity supports various applications, from detailed models and prototypes to functional parts requiring specific mechanical properties.
FDM excels in material versatility, utilizing a broad spectrum of thermoplastic filaments that range from basic PLA and ABS to advanced composites reinforced with carbon fiber or metal. This wide selection makes FDM adaptable to numerous applications requiring durability, flexibility, or specialized characteristics like electrical conductivity or thermal resistance.
Environmental and Operational Considerations
SLA printers operate with liquid resins that require careful handling and disposal, and post-processing involves cleaning and curing—the requirement for a clean, controlled environment and handling chemicals places specific operational demands on SLA printing.
Using thermoplastic filaments, FDM printers generally have fewer environmental concerns and more straightforward post-processing requirements. The ease of handling and storing filament materials and the straightforward removal of support structures make FDM more user-friendly and adaptable to various settings, from classrooms to industrial workshops.
Practical Applications of SLA and FDM
The practical applications of Stereolithography (SLA) and Fused Deposition Modeling (FDM) highlight the versatility and strengths of each technology, making them indispensable tools in various fields. From intricate models and prototypes to functional parts and tools, SLA and FDM cater to diverse needs, driving innovation across industries.
Industrial and Commercial Applications Where SLA Excels
Dental and Medical Devices: SLA's precision is particularly beneficial in the medical field, producing detailed dental models, custom hearing aids, and surgical guides. The availability of biocompatible resins makes SLA a preferred choice for patient-specific medical applications.
Jewelry: The high resolution of SLA printing allows jewelers to create intricate designs and patterns, offering a modern approach to crafting unique pieces and molds for traditional casting processes.
Prototyping for Consumer Electronics: SLA is used to develop prototypes with fine details and smooth finishes, ideal for the aesthetically driven consumer electronics industry. It enables designers to create complex geometries for new products with precision.
Versatility of FDM in Manufacturing
Functional Prototypes and End-use Parts: FDM's strength and durability make it suitable for creating functional prototypes that undergo rigorous testing, as well as for producing end-use parts in the automotive, aerospace, and consumer goods sectors.
Custom Tools and Fixtures: Using solid and durable materials allows FDM to produce custom tools, jigs, and fixtures that can withstand operational stresses, reducing production costs and improving efficiency on the manufacturing floor.
Educational Models and Architectural Mockups: FDM's material versatility and ease of use make it a popular choice for educational purposes, enabling students to bring their projects to life. It's also used in architecture to create scale models and detailed mockups of buildings.
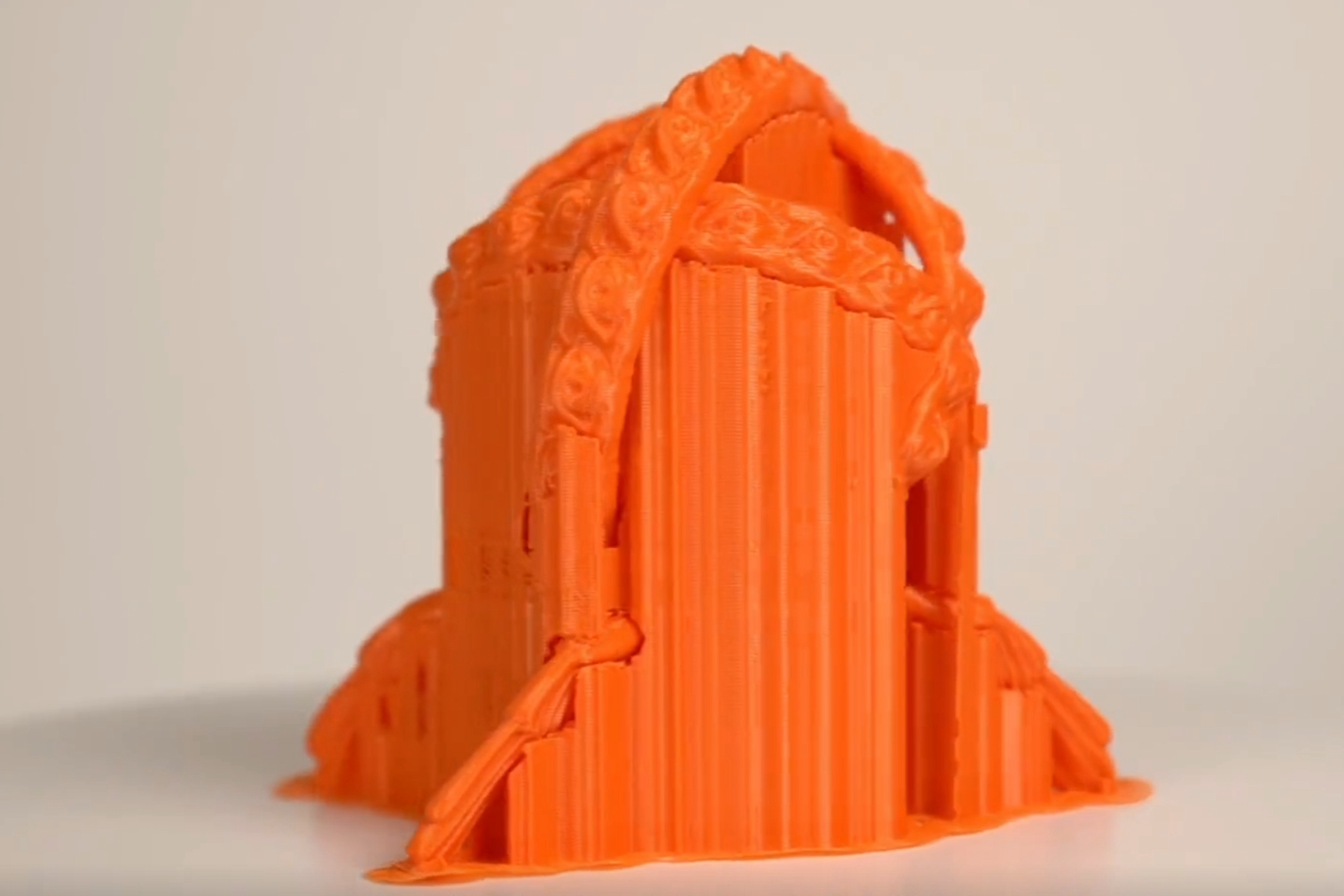
Choosing Between SLA and FDM Based on Sector Needs
Aerospace: Both SLA and FDM find applications in aerospace for different purposes. SLA is often used for detailed components requiring high precision, while FDM is preferred for durable, functional parts needed in prototyping and manufacturing.
Automotive: FDM's ability to produce durable parts quickly and cost-effectively makes it a go-to choice for automotive prototyping and production. SLA, however, is used for complex, detailed components like light covers and interior fixtures.
Healthcare: SLA's precision and compatibility with biocompatible materials make it ideal for custom healthcare applications, from prosthetics to surgical tools. FDM can also be used for prototyping and producing non-patient-specific tools and devices.
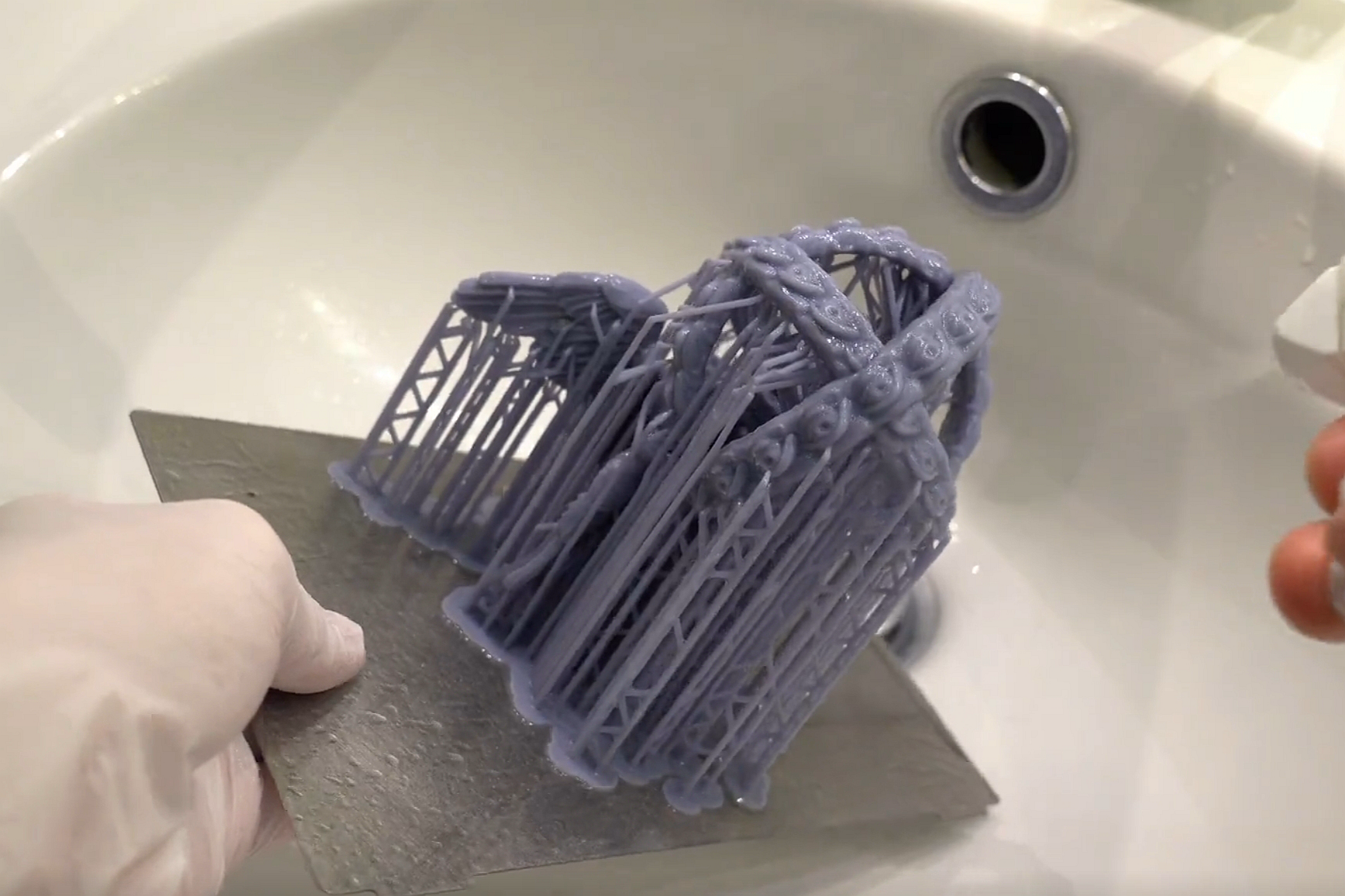
Advantages and Limitations: SLA vs. FDM
Delving into the advantages and limitations of Stereolithography (SLA) and Fused Deposition Modeling (FDM) provides critical insights that help users align their project requirements with the capabilities of these technologies. Each technology brings unique strengths while facing certain constraints, influencing its application in real-world scenarios.
Advantages of SLA
High Resolution and Detail: SLA's laser-based technology allows for extremely high precision, making it ideal for parts requiring intricate details and smooth surface finishes.
Wide Range of Materials: With developments in resin technology, SLA offers a broad spectrum of materials, including flexible, transparent, and high-strength options, catering to diverse application needs.
Excellent Surface Finish: Parts produced with SLA have a smooth finish, often requiring minimal post-processing, which is beneficial for aesthetic prototypes and parts with complex geometries.
Limitations of SLA
Material Brittleness: Despite the variety of resins available, SLA parts can be more brittle than those made with FDM, limiting their use in functional applications requiring high-impact resistance or long-term durability.
Smaller Build Volume: SLA printers typically have smaller build volumes than FDM machines, making them less suited for large parts or batch production.
Post-Processing Requirements: SLA parts often require cleaning and further curing, adding steps to the production process, and necessitating handling potentially hazardous materials.
Advantages of FDM
Material Durability: FDM uses thermoplastic materials that are inherently more robust and suitable for functional prototypes and end-use parts requiring strength and durability.
Ease of Use and Accessibility: FDM technology is generally more straightforward and user-friendly, making it accessible for hobbyists, schools, and professionals.
Cost-Effectiveness: The materials and operation of FDM printers are typically less expensive than those of SLA, offering a cost-effective solution for rapid prototyping and manufacturing.
Limitations of FDM
Lower Resolution and Detail: The nature of FDM means it cannot match the fine detail and smooth surfaces achievable with SLA, which may be a drawback for applications requiring high aesthetic quality.
Visible Layer Lines: FDM parts often exhibit layer lines and may require post-processing to achieve a smooth finish, which can be time-consuming.
Material Warping: Certain materials used in FDM, like ABS, are prone to warping or deformation if not adequately cooled, which can affect the accuracy and quality of the printed parts.
Making a choice: SLA vs. FDM
Choosing between Stereolithography (SLA) and Fused Deposition Modeling (FDM) is a pivotal decision in the 3D printing process, significantly impacting your project's outcome. This choice should be informed by understanding each technology's strengths and limitations and your specific needs. We provide guidelines to help navigate this decision, ensuring the selected technology aligns with the project's requirements, budget, and timeline.
Guidelines for Selection
Detail and Aesthetics: If your project demands excellent detail and a smooth finish—such as intricate jewelry, detailed prototypes, or custom figurines—SLA is the superior choice. Its precision and ability to produce parts with complex geometries and smooth surfaces make it ideal for applications where aesthetics are paramount.
Functional Strength and Durability: For projects requiring parts with functional strength, durability, or thermal resistance—such as mechanical parts, functional prototypes, and manufacturing tools—FDM is the better fit. The thermoplastic materials' robustness in FDM can withstand more rigorous testing and use.
Budget Considerations: If cost is a significant factor, FDM generally offers a more economical solution regarding initial investment and ongoing material costs. SLA materials and machines can be more expensive, although they provide value in applications where the unique advantages of SLA are a requirement.
Production Volume and Size: FDM's typically larger build volume and faster print speed may be more advantageous for more significant parts or batch production. SLA's smaller build volume and slower speed can limit large parts or high-volume projects, although it excels in producing smaller, highly detailed parts.
Case Studies and Examples
Aerospace Component Prototyping: An aerospace company needs prototypes for airflow testing. FDM was chosen for its ability to produce large, durable parts quickly that can withstand the physical stresses of wind tunnel testing.
Custom Dental Devices: A dental lab requires models for patient-specific devices. SLA is selected for its precision and the availability of biocompatible resins, ensuring accurate and safe products.
Consumer Electronics Casing: A startup designs a new smartphone case requiring detailed logos and a smooth finish. SLA is preferred for its fine detail and superior surface quality, enhancing its aesthetic appeal.
What We Can Do In 3D Printing?
The future of additive manufacturing continues to evolve, with SLA and FDM technologies at the forefront of innovation. Advances in resin chemistry and filament materials are expanding the capabilities of SLA and FDM printers, making 3D printing more accessible, versatile, and powerful than ever before. As new materials and improvements emerge, the boundaries of what can be achieved with each technology will undoubtedly expand, further solidifying the role of 3D printing in transforming ideas into tangible realities.
Selective Laser Melting (SLM) Service: Rapid prototyping and production of nickel, cobalt, and stainless steel superalloys.
Fused Deposition Modeling (FDM) Service: Prototypes and Functional Parts, Jigs and Fixtures, Low-Cost Models.
Stereolithography (SLA) Service: High-Detail Models, Dental and Medical Applications, Jewelry, and Art.
Selective Laser Sintering (SLS) Service: Complex Geometries, End-Use Parts, Snap-Fit Parts.
Multi Jet Fusion (MJF) Service: Functional Prototypes and End-Use Parts, Complex Assemblies, High-Volume Production.
Direct Metal Laser Sintering (DMLS) Service: Aerospace and Automotive Components, Medical Implants and Tools, Heat Exchangers and Custom Tooling.
评论
发表评论