Hot Isostatic Pressing (HIP) Services in Manufacturing
In advanced manufacturing, Hot Isostatic Pressing (HIP) stands out as a transformative technology that significantly enhances the properties and performance of manufactured parts. HIP employs high pressure and high temperature in a controlled environment to improve material characteristics, offering a pivotal advantage in producing high-quality, high-performance components across various industries.
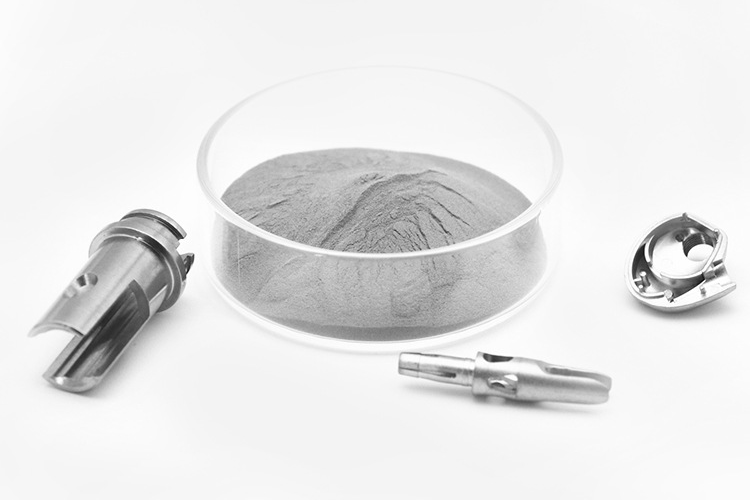
This process begins with densifying the component inside a high-pressure vessel. The vessel is then filled with an inert gas, usually argon, heated and pressurized to levels where the material's microstructure is optimized. This combination of heat and isotropic (equal in all directions) pressure effectively eliminates porosity. It increases the density of the material, resulting in parts with superior mechanical properties, durability, and longevity.
HIP is versatile and applicable to various materials, including metals, ceramics, and composites. It makes it an invaluable service in industries demanding the utmost in part performance and reliability, such as aerospace, defense, medical implants, energy, and automotive sectors. The process can refine and enhance newly manufactured parts and repair existing components, providing a critical tool in the push towards higher efficiency, reduced waste, and developing components that meet stringent specifications and tolerances.
Understanding Hot Isostatic Pressing
Definition and Explanation of HIP Technology
Hot Isostatic Pressing (HIP) is a manufacturing process that combines high temperature and high isotropic pressure to densify and improve the properties of materials. This process can eliminate porosity and increase the density of materials, leading to enhanced mechanical properties. The HIP is performed in a specially designed chamber, known as a HIP unit, where components are subjected to pressures up to 30,000 psi (approximately 207 MPa) and temperatures up to 2000°C (about 3632°F), depending on the material requirements.
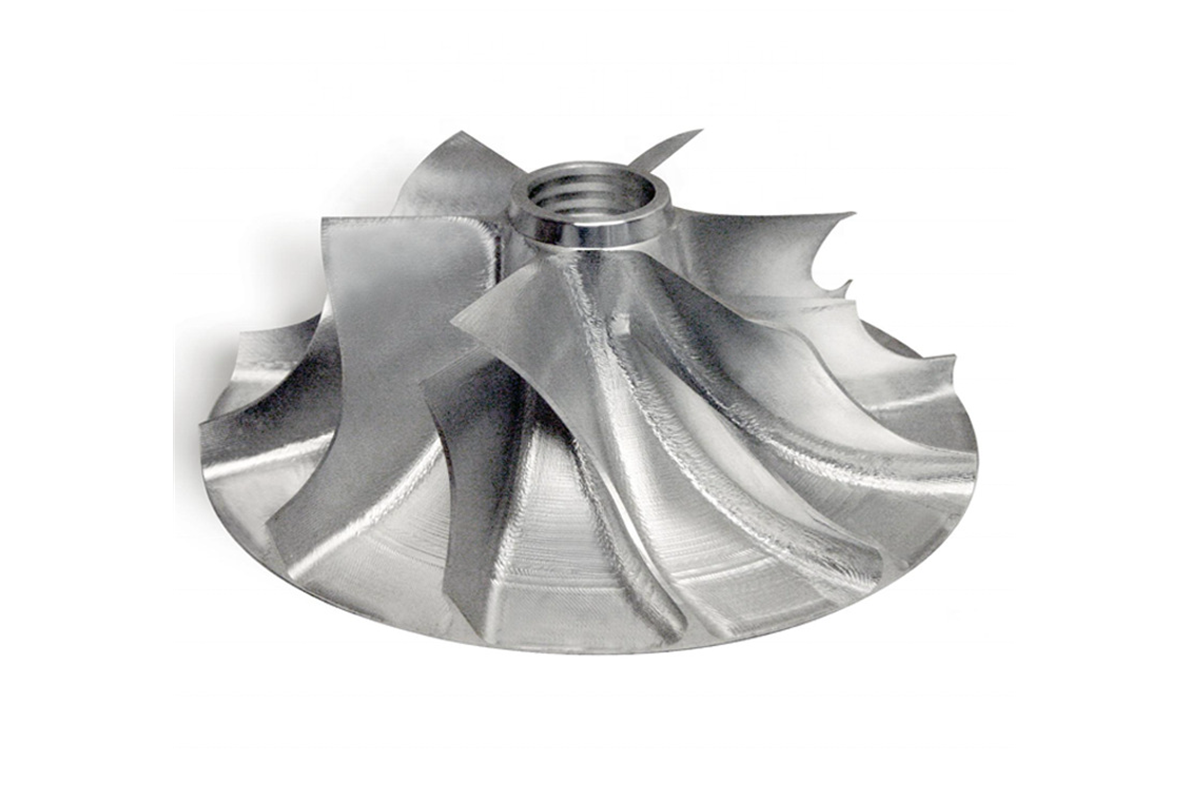
Step-by-Step Walkthrough of the HIP Process
Preparation: The components or powders to be HIPed are encapsulated in a container, usually made of steel or other materials that can withstand the HIP conditions. This container is then evacuated to remove air and sealed.
Heating and Pressurizing: The sealed container is placed inside the HIP unit. The chamber is then pressurized with an inert gas, typically argon, and heated to the required temperature. The pressure and heat are applied isotropically, meaning uniformly from all directions, ensuring even densification.
Cooling: After maintaining the high-pressure and high-temperature conditions for a predetermined period (sufficient to achieve the desired material properties), the unit is allowed to cool, still under pressure, to ensure controlled microstructural development.
Post-Processing: Once cooled, the pressure is released, and the component is removed from the chamber. The encapsulation material is removed, and the part may undergo further post-processing steps, such as machining or surface treatment, to achieve the final specifications.
Key Benefits of Using HIP in Manufacturing
Improved Material Properties: HIP dramatically enhances the density and mechanical properties of materials, including strength, fatigue resistance, and flexibility.
Elimination of Porosity: One of the primary advantages of HIP is its ability to eliminate internal voids and porosity without changing the component's dimensions, which is crucial for high-performance applications.
Increased Component Reliability: Parts processed through HIP exhibit improved reliability and longer service lives, reducing the risk of failure in critical applications.
Versatility: HIP can be applied to various materials, including metals, ceramics, and composites, making it a versatile process for various manufacturing needs.
Cost Efficiency: By improving components' material properties and reliability, HIP can reduce the need for expensive alloys and decrease overall manufacturing costs by minimizing waste and scrap.
Hot Isostatic Pressing offers unique advantages that can significantly improve the quality and performance of manufactured components through its combination of high pressure and high temperature. Its ability to enhance material properties and eliminate defects positions HIP as a critical technology in the manufacturing landscape, supporting the production of components that meet the highest durability and reliability standards.
HIP Across Industries
Hot Isostatic Pressing (HIP) has become a cornerstone technology in various industries thanks to its ability to enhance parts' mechanical properties and reliability. Let's explore how HIP benefits critical sectors such as aerospace, defense, medical, energy, and automotive.
Aerospace and Defense: Enhancing Critical Components
In the aerospace and defense industries, component failure is not an option. HIP is critical in improving the durability and fatigue life of parts exposed to extreme conditions. HIP eliminates porosity and ensures uniform density for turbine blades, engine components, and structural parts, resulting in components that can withstand high stresses and temperatures, enhancing aircraft and defense system safety and performance.
Medical: Advancing Biomedical Implants
The medical industry benefits from HIP by producing more muscular, reliable implants such as hip and knee replacements. HIP improves the compatibility and longevity of these implants by ensuring they are free from defects that could lead to failure. By achieving a higher density and improved mechanical properties, HIP-treated implants better withstand the physiological loads they will be subjected to over their lifetime, reducing the risk of implant failure and subsequent revision surgeries.
Energy: Strengthening Components for Harsh Environments
In the energy sector, especially in oil and gas extraction, components must endure harsh environments under extreme pressures and temperatures. HIP significantly strengthens parts like drill bits, valves, and pipeline components, making them more resistant to corrosion and wear. This process extends the service life of these components and enhances operational safety and efficiency in energy production operations.
Automotive: Refining High-Performance Engine Components
The automotive industry, particularly in the high-performance and racing segments, demands components that exhibit superior strength, durability, and lightweight properties. HIP optimizes the properties of engine components such as pistons, rods, and turbocharger parts, ensuring they can handle the extreme pressures and temperatures associated with high-speed performance. It leads to engines that are more reliable, efficient, and capable of delivering enhanced performance.
Superiority of HIP in Manufacturing
Hot Isostatic Pressing (HIP) revolutionizes manufacturing processes by enhancing material properties, offering cost-effectiveness, and demonstrating unparalleled versatility. This section delves into the advantages of HIP, setting it apart as a superior manufacturing method.
Enhanced Material Properties
HIP significantly increases the density of materials, eliminating internal voids and porosity that could lead to part failure. This process results in materials with superior mechanical characteristics, including increased tensile strength, improved fatigue resistance, and higher flexibility. For industries where part performance under stress, temperature, or corrosive environments is critical, HIP ensures that components meet the stringent requirements for reliability and longevity.
Cost-effectiveness
One of the compelling advantages of HIP is its ability to reduce manufacturing costs while enhancing product quality. By improving the material's density and properties, HIP minimizes the need for expensive post-processing steps such as machining and finishing, directly impacting the bottom line. Moreover, HIP's process efficiency and waste reduction make it a cost-effective solution for high-volume production, as it maximizes material utilization and minimizes scrap.
Versatility
HIP's application spans various materials, including metals, ceramics, and composites, making it a versatile choice for various manufacturing needs. This process is more comprehensive than the complexity of the part geometry, enabling the production of components with intricate designs that would be challenging or impossible to create using traditional manufacturing methods. Additionally, HIP's ability to improve the properties of newly manufactured and repaired components further underscores its versatility and broad applicability in modern manufacturing landscapes.
HIP Versus Other Manufacturing Techniques
Hot Isostatic Pressing (HIP) not only stands as a formidable process on its own but also when compared to other advanced manufacturing techniques such as Metal Injection Molding (MIM) and Selective Laser Melting (SLM). This section explores how HIP stacks up against these methods regarding the manufacturing process, product quality, material selection, delivery time, and cost.
HIP vs. MIM (Metal Injection Molding)
Manufacturing Process: While MIM involves mixing metal powders with a binder, injecting them into a mold, and then sintering, HIP applies high pressure and temperature to already compacted or cast parts to eliminate porosity and improve properties. MIM is best for complex, small, to medium-sized parts, whereas HIP is suited for densifying and improving the mechanical properties of a broader range of sizes and complexities.
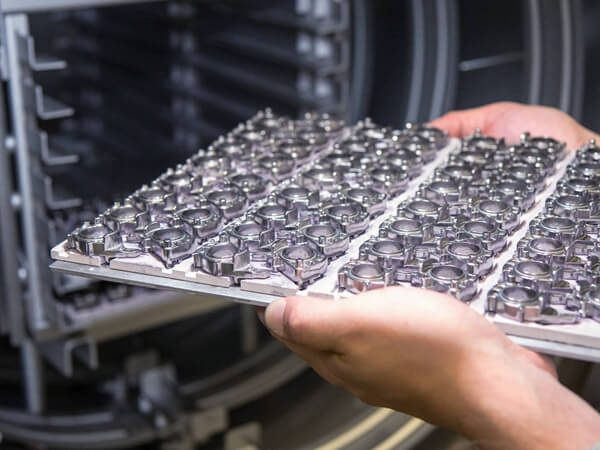
Product Quality: HIP produces parts with superior density and mechanical properties by eliminating internal porosities, a challenge sometimes faced by MIM parts, especially in larger or more complex geometries.
Material Selection: MIM offers a wide range of metal materials but is typically limited by the flow properties of the metal-binder mix. HIP can be applied to virtually any material that can be compacted or cast, including metals, ceramics, and composites.
Delivery Time and Cost: MIM can be more cost-effective for producing complex parts in large quantities due to the efficiencies of the injection molding process. However, HIP, although potentially higher in initial cost, can significantly reduce the need for post-processing and improve the performance of critical components, justifying its cost for high-value applications.
HIP vs. SLM (Selective Laser Melting)
Manufacturing Process: SLM builds parts layer by layer by selectively melting powder material using a laser, which is ideal for complex geometries and customization. HIP can further process SLM parts to enhance density and mechanical properties, complementing these processes.
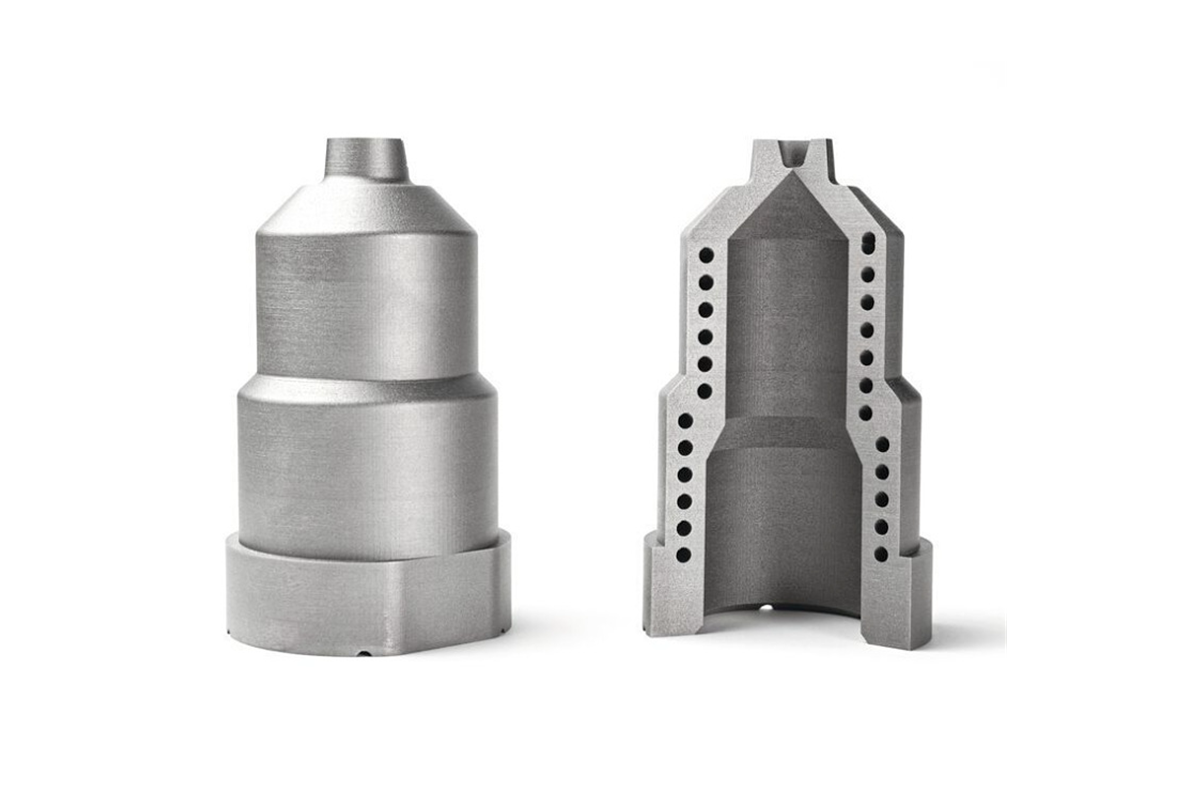
Product Quality: SLM parts can exhibit porosity and anisotropy in mechanical properties due to layer-based construction. HIP post-processing SLM parts can eliminate these issues, enhancing performance and reliability.
Material Selection: SLM is limited by the need for materials to be laser-compatible and by the challenges of managing thermal stresses during printing. HIP does not have these limitations and can treat various materials.
Delivery Time and Cost: SLM can rapidly produce parts with complex geometries but often requires significant post-processing. The combined process time and cost can increase when SLM parts are finished with HIP. Still, the result has exceptional quality and performance, making it a valuable option for critical applications.
Main Applications of HIP as Post-Processing
HIP is an essential post-processing step for enhancing SLM 3D printed and vacuum investment cast superalloy parts. By applying HIP to these parts, manufacturers can achieve improved density, uniform mechanical properties, and extended component lifespans, which are crucial in industries requiring the highest material performance and reliability levels.
HIP as a Crucial Post-Processing Method
Hot Isostatic Pressing (HIP) is a powerful post-processing technique that is precious for parts produced via Selective Laser Melting (SLM) and other additive manufacturing processes and for enhancing vacuum investment cast superalloy components. This section delves into the main applications of HIP as a post-processing method, underscoring its ability to refine and improve the properties of parts for critical applications.
Enhancing SLM 3D Printed Parts
Selective Laser Melting (SLM) is renowned for its ability to produce complex geometries and custom parts directly from digital models. However, the layer-by-layer construction inherent to SLM and other additive processes can introduce porosity, resulting in anisotropic mechanical properties. HIP post-processing addresses these issues by:
Eliminating Porosity: Applying high pressure and temperature uniformly across the part, HIP closes internal voids, significantly reducing porosity and improving the overall density of the component.
Homogenizing Material Properties: The isotropic pressure during HIP ensures uniform material properties throughout the part, enhancing mechanical characteristics such as tensile strength, fatigue resistance, and flexibility.
Improving Surface Finish: While not a substitute for mechanical finishing processes, HIP can improve the surface condition of SLM parts, contributing to better performance and aesthetics.
Refining Vacuum Investment Cast Superalloy Parts
Superalloys, often used in aerospace, energy, and other high-performance industries, are known for their excellent mechanical strength and resistance to thermal creep deformation, corrosion, and oxidation. Vacuum investment casting is a preferred method for creating complex shapes from superalloys. However, cast parts can suffer from micro-porosities that compromise their mechanical integrity. HIP post-processing of these parts offers several benefits:
Enhanced Structural Integrity: By eliminating micro-porosities, HIP increases the structural integrity of superalloy parts, which is crucial for applications subjected to extreme operational stresses.
Increased Fatigue Life: Reducing internal defects through HIP significantly extends the fatigue life of components, an essential factor for parts in aerospace engines and power generation turbines.
Uniform Mechanical Properties: Similar to its effect on SLM parts, HIP ensures that vacuum investment cast parts have consistent material properties. This is vital for their predictable performance in demanding environments.
Superalloy Manufacturing
We can use MIM, SLM, vacuum casting, HIP, and other technologies to manufacture high-temperature metal parts such as nickel, cobalt, and tungsten. At the same time, HIP technology can also be selected as a post-processing process to improve the density of the blank and eliminate pores and internal defects.
Metal Injection Molding (MIM) Service
Superalloy SLM 3D Printing Service
Vacuum Investment Casting Service
Hot Isostatic Pressing (HIP) Services
评论
发表评论