In manufacturing and product development, the advent of 3D printing technologies has marked a significant milestone, offering unprecedented flexibility, efficiency, and innovation in creating prototypes and end-use parts. Among these transformative technologies, Direct Metal Laser Sintering (DMLS) has emerged as a frontrunner, especially in rapid prototyping services. DMLS, a subset of metal 3D printing, harnesses the power of lasers to sinter powdered metal, layer by layer, into dense, complex, and highly durable objects directly from digital models.
Developed as an extension of the broader family of laser sintering technologies, DMLS has revolutionized how industries approach the prototyping of metal parts. It eliminates the need for traditional tooling, significantly reduces development time, and opens up new possibilities for design innovation by creating previously unattainable geometries with conventional manufacturing methods.
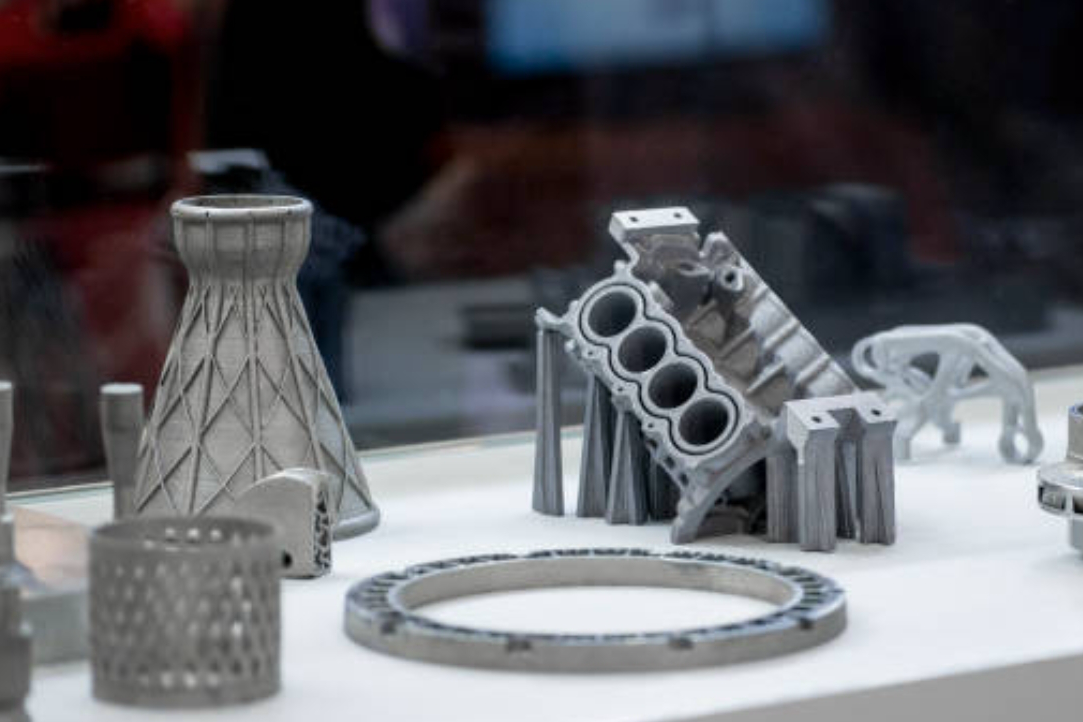
Understanding DMLS Technology
Direct Metal Laser Sintering (DMLS) represents a pinnacle of additive manufacturing technology, particularly for metals, allowing for creating parts that combine complexity with strength in ways traditional methods cannot match. Here, we explore the foundational aspects of DMLS, from its inception to the intricacies of its operation, laying the groundwork for appreciating its role in modern manufacturing.
Definition and Development
Direct Metal Laser Sintering (DMLS) is an additive manufacturing process that uses a laser to sinter powdered metal, bonding the material to create a solid structure, layer by layer. Unlike traditional subtractive manufacturing processes, DMLS builds parts by adding material rather than removing it, offering a more efficient and waste-reducing production method.
The technology was developed in the late 20th century, with the first systems introduced in the early 1990s. It was initially designed to address the limitations of existing manufacturing techniques, offering a solution for producing metal parts with complex geometries, internal features, and high levels of customization.
The DMLS Process: How It Works
The DMLS process involves several key steps:
Digital Model Preparation: CAD software creates a 3D digital model of the part to be produced. This Model is then sliced into thin horizontal layers, which serve as a guide for the DMLS machine.
Powder Dispersion: A thin layer of metal powder is evenly distributed across the build platform inside the DMLS machine.
Laser Sintering: A high-powered laser selectively sinters the metal powder, melting and fusing it to form a solid layer. The laser precisely follows the cross-sectional patterns defined by the sliced digital Model.
Layering and Repeating: After each layer is sintered, the build platform lowers, and a new layer of powder is spread. The process repeats, with each layer bonding to the one below, until the entire part is formed.
Cooling and Removal: The build chamber and the completed part can cool. The part is removed from the powder bed, and excess powder is brushed away or used in subsequent builds.
Critical Components of a DMLS Printer
Laser System: The core of a DMLS printer is the laser system responsible for melting and fusing the metal powder. Its precision and power are crucial for achieving the desired part quality and material properties.
Powder Bed: This is where the metal powder is laid out and sintered. It supports the part during the build process and contains the material needed to form each layer of the part.
Recoating System: A mechanism that spreads new layers of metal powder over the build area. It ensures a consistent and even distribution of material for each layer.
Advantages of DMLS in Rapid Prototyping
Direct Metal Laser Sintering (DMLS) technology stands at the forefront of revolutionizing the rapid prototyping landscape, particularly for metal parts. Its capabilities extend far beyond those of traditional manufacturing techniques, offering unparalleled benefits crucial for today's fast-paced, innovation-driven industries. This section explores the critical advantages of DMLS in rapid prototyping, underscoring why it has become an essential tool for engineers and designers.
Speed: Reducing Time from Design to Prototype
One of the most significant advantages of DMLS is the dramatic reduction in the time required to move from a design concept to a physical prototype. Unlike traditional metalworking processes that can be time-consuming and labor-intensive, DMLS allows for the direct creation of parts from digital files, eliminating the need for tooling and significantly cutting down production times. This rapid turnaround is invaluable for companies looking to accelerate their product development cycles and gain a competitive edge in the market.
Precision and Complexity: Unlocking New Design Possibilities
DMLS excels in producing parts with complex geometries and intricate details that would be challenging or impossible to achieve through conventional methods. The precision of the laser sintering process enables the fabrication of components with tight tolerances and delicate features, opening up new possibilities for design innovation. This capability is particularly beneficial for applications requiring the integration of internal channels, lattice structures, or other complex elements within a single part without compromising strength or functionality.
Material Properties: Ensuring Functional Prototyping
A key benefit of DMLS is its ability to maintain the metal powders' inherent properties, resulting in prototypes that closely mimic the characteristics of traditionally manufactured parts. It means that prototypes produced via DMLS can undergo functional testing under conditions similar to those they will face in actual use, providing accurate and reliable performance data. The process also allows for the creation of parts from a wide range of metals, including stainless steel, titanium, and aluminum alloys, offering versatility in material selection to match specific application requirements.
Cost-Effectiveness: Streamlining Prototyping Expenses
While the initial setup and material costs for DMLS can be higher than some traditional and additive manufacturing methods, the technology proves cost-effective in the long run, especially for low to medium-volume production runs. By eliminating the need for tooling and reducing waste material, DMLS lowers overall prototyping expenses. Additionally, consolidating multiple parts into a single, complex assembly reduces assembly time and costs, further enhancing the cost-efficiency of the prototyping process.
Material Options and Selection in DMLS
Direct Metal Laser Sintering (DMLS) offers diverse material options, each bringing unique properties and advantages. This versatility is crucial for tailoring prototypes to specific application requirements, from aerospace components to custom medical implants. Understanding the range of materials available and the criteria for selecting the right one is essential for maximizing the benefits of DMLS in rapid prototyping.
Overview of Metal Powders Used in DMLS
Stainless Steel: Renowned for its strength, corrosion resistance, and durability, stainless steel is a go-to material for various applications, including functional prototypes and end-use parts in demanding environments.
Titanium Alloys: Offering a superb strength-to-weight ratio and excellent biocompatibility, titanium alloys are particularly favored in aerospace, automotive, and medical industries for lightweight, high-performance parts.
Aluminum Alloys: Known for their excellent thermal properties and lightweight nature, aluminum alloys are used in DMLS for applications requiring heat dissipation and reduced part weight without sacrificing strength.
Nickel-based Alloys: These materials are characterized by their high-temperature resistance and strength, making them suitable for components in jet engines, gas turbines, and other high-temperature applications.
Criteria for Selecting Materials for DMLS Projects
The selection of the appropriate material for a DMLS project depends on several key factors:
Mechanical Properties: Strength, flexibility, and fatigue resistance are crucial considerations, especially for parts that undergo mechanical stress or need a long service life.
Thermal Properties: Materials with high thermal stability and conductivity are essential for components exposed to high temperatures.
Biocompatibility: Projects involving medical devices or implants require biocompatible materials that are safe for use in the human body.
Corrosion Resistance: In environments where parts are exposed to corrosive substances, selecting a material with high corrosion resistance ensures the longevity and reliability of the part.
Importance of Material Purity and Powder Particle Size
The quality of DMLS parts is significantly influenced by the purity of the metal powder and the consistency of the powder particle size. High-purity materials minimize the risk of inclusions and defects in the final part, while a uniform particle size ensures smooth, even layers and optimal density in the sintered parts. Manufacturers and designers must pay close attention to these parameters when choosing materials for their DMLS projects to achieve the best possible outcomes.
Applications of DMLS in Various Industries
Direct Metal Laser Sintering (DMLS) technology has seen widespread adoption across numerous industries, capitalizing on its ability to rapidly produce metal prototypes and parts with complex geometries and excellent mechanical properties. The unique advantages of DMLS, such as reduced lead times and the elimination of traditional tooling, have opened up new possibilities for product development and innovation. This section explores the transformative impact of DMLS across various sectors, demonstrating its versatility and effectiveness.
Aerospace Industry
The demand for lightweight, high-strength components is paramount in the aerospace sector. DMLS meets these requirements by enabling the fabrication of parts with complex internal structures, such as lattice frameworks, that significantly reduce weight without compromising strength. Components such as turbine blades, fuel nozzles, and air ducts are routinely produced using DMLS, contributing to enhanced performance and fuel efficiency in aircraft and spacecraft.
Medical Field
The medical industry benefits significantly from the customization capabilities of DMLS. Custom implants, surgical tools, and orthopedic devices can be tailored to fit individual patient anatomy, improving surgical outcomes and patient recovery times. The biocompatibility of certain DMLS materials, like titanium alloys, further underscores the suitability of this technology for medical applications, including prosthetics and dental fixtures.
Automotive Sector
DMLS is instrumental in the automotive industry, particularly in the prototyping and producing components for high-performance vehicles. It allows for the rapid iteration of design concepts, enabling engineers to test and refine parts such as gearbox components, exhaust systems, and custom engine parts. The ability to produce lightweight, durable components improves vehicle efficiency and performance.
Tooling and Mold Making
DMLS technology has also revolutionized the tooling and mold-making processes by enabling the direct fabrication of molds and dies with conformal cooling channels. These channels follow the contours of the mold cavity, improving temperature management during injection molding and reducing cycle times. The result is increased productivity and higher-quality plastic parts with reduced residual stresses and warpage production.
Energy Sector
In the energy industry, DMLS plays a crucial role in producing components for renewable energy systems, such as wind turbines and high-performance parts for oil and gas exploration. The technology's ability to withstand harsh environmental conditions and produce parts that endure high temperatures and pressures makes it an invaluable tool for developing more efficient and reliable energy solutions.
Comparing DMLS with Other Metal 3D Printing Technologies
Direct Metal Laser Sintering (DMLS) has established itself as a formidable force in metal 3D printing, offering benefits catering to rapid prototyping and beyond. However, DMLS is one of many players in the field. To fully grasp the scope and potential of DMLS, it’s crucial to compare it with other prevalent metal 3D printing technologies, such as Metal Binder Jetting (MBJ) and Electron Beam Melting (EBM). This comparative analysis highlights each method's distinct advantages and considerations, aiding in selecting the most suitable technology based on specific project requirements.
DMLS vs. Metal Binder Jetting (MBJ)
Process and Material Use: While DMLS uses a high-power laser to fuse metal powder layer by layer, MBJ spreads a layer of metal powder and then selectively deposits a binding agent in the cross-section of the part. Post-printing, the part is sintered in a furnace to achieve its final strength.
Speed and Cost: MBJ is generally faster and more cost-effective for larger batches of parts due to its ability to print multiple components simultaneously. However, DMLS offers superior material density and mechanical properties, making it the preferred choice for functional prototypes and high-stress applications.
Surface Finish and Detail: DMLS parts typically have a better surface finish and finer details out of the machine than MBJ, which may require additional post-processing to achieve similar quality levels.
DMLS vs. Electron Beam Melting (EBM)
Energy Source: The critical difference between DMLS and EBM lies in their energy sources; DMLS uses a laser, while EBM uses an electron beam to melt the metal powder. This distinction influences the materials each can process and the resulting part characteristics.
Material Compatibility: EBM is particularly suited for materials with high reflectivity and thermal conductivity, such as titanium alloys, which are challenging for laser-based systems. DMLS, on the other hand, has a broader material palette, including various steels, aluminum, and nickel-based alloys.
Applications and Use Cases: EBM excels in producing parts with excellent material properties under high vacuum and temperatures, making it ideal for aerospace applications. DMLS offers more flexibility regarding part complexity and is widely used across industries for functional prototypes and end-use parts.
Considerations for Choosing DMLS Over Alternative Technologies
Selecting between DMLS and other metal 3D printing technologies depends on several factors, including:
Part Complexity and Precision: DMLS’s ability to produce parts with complex geometries and tight tolerances often makes it the preferred choice for intricate designs and functional prototyping.
Material Requirements: The choice of material significantly impacts the selection process. DMLS’s wide range of compatible metals ensures that it can meet diverse material property requirements.
Production Volume and Cost: For small to medium-sized batches requiring high precision and material properties, DMLS is often more cost-effective despite the higher initial material and machine costs.
Optimizing Design for DMLS
As Direct Metal Laser Sintering (DMLS) continues to redefine the possibilities within rapid prototyping and manufacturing, understanding how to optimize designs specifically for this process is crucial. DMLS offers unparalleled flexibility in manufacturing complex metal parts, but harnessing its full potential requires a nuanced approach to design. This section explores best practices for designing for DMLS, ensuring that prototypes and parts are not only manufacturable but also optimized for performance, cost, and functionality.
Embracing Design for Additive Manufacturing (DfAM)
Complexity for Free: One of the most celebrated aspects of DMLS is its ability to handle complex geometries at no additional cost. Designers are encouraged to think beyond traditional constraints, directly incorporating complex internal channels, lattice structures for lightweighting, and intricate features into their designs.
Self-Supporting Structures: While DMLS can produce highly complex shapes, designs that minimize the need for support structures are more cost-effective and result in a cleaner surface finish. Angles over 45 degrees from the build plate typically do not require supports, a guideline that can significantly influence design considerations.
Material Considerations in Design
Selecting the Right Material: DMLS can process various metal powders, each offering different properties. Design decisions should be informed by the intended application of the part, considering factors such as mechanical strength, thermal properties, and corrosion resistance.
Accounting for Thermal Distortion: The high temperatures involved in the DMLS process can lead to thermal distortion. Designers should anticipate and compensate for potential warping, especially for extended, thin features.
Optimizing Part Orientation and Building Strategy
Orientation for Optimal Results: The orientation of a part on the build plate affects everything from surface finish to mechanical properties. Orienting critical surfaces vertically can enhance their quality, while strategic placement can reduce support needs.
Nested Designs for Efficiency: When planning for DMLS production, nesting multiple parts within a single build volume can maximize efficiency and reduce costs. This approach requires careful planning to ensure optimal part quality and build success.
Post-Processing and Finish Considerations
Designing for Post-Processing: Despite the high-quality finish achievable with DMLS, some applications may require additional post-processing steps, such as machining, polishing, or heat treatments. Designing with these steps in mind can streamline the final finishing process.
Surface Finish Expectations: It's essential to design with realistic expectations for the as-built surface finish of DMLS parts. Certain applications necessitate specific post-processing to meet functional or aesthetic requirements.
Software Tools and Simulation
Utilizing Advanced Software: Modern CAD and simulation software offer tools specifically designed for additive manufacturing, allowing designers to predict and optimize part performance before printing. Utilizing these tools can reduce the need for physical prototyping and iterate designs more efficiently.
What We Can Do In 3D Printing Service
Direct Metal Laser Sintering (DMLS) has emerged as a transformative force in rapid prototyping and additive manufacturing, enabling designers and engineers to transcend traditional manufacturing constraints. As we have explored, DMLS offers unparalleled advantages, including the ability to produce complex geometries, utilize a wide range of materials, and significantly reduce time-to-market for new products. These capabilities position DMLS not only as a tool for prototyping but also as a viable solution for producing functional, high-performance parts across various industries.
The comparative analysis with other metal 3D printing technologies underscores DMLS's unique position, offering a balance of precision, material properties, and often unmatched efficiency. However, to fully harness the potential of DMLS, a deep understanding of design optimization strategies is essential. By embracing Design for Additive Manufacturing (DfAM) principles, engineers can create feasible parts for DMLS production and optimize for the intended application.
Selective Laser Melting (SLM) Service: Rapid prototyping and production of nickel, cobalt, and stainless steel superalloys.
Fused Deposition Modeling (FDM) Service: Prototypes and Functional Parts, Jigs and Fixtures, Low-Cost Models.
Stereolithography (SLA) Service: High-Detail Models, Dental and Medical Applications, Jewelry, and Art.
Selective Laser Sintering (SLS) Service: Complex Geometries, End-Use Parts, Snap-Fit Parts.
Multi Jet Fusion (MJF) Service: Functional Prototypes and End-Use Parts, Complex Assemblies, High-Volume Production.
Direct Metal Laser Sintering (DMLS) Service: Aerospace and Automotive Components, Medical Implants and Tools, Heat Exchangers and Custom Tooling.
评论
发表评论