Understanding Common Defects in CNC Machining
CNC machining is a cornerstone in modern manufacturing, offering unparalleled precision and repeatability. CNC Machining prototyping has revolutionized how parts are made, contributing significantly to advancements in various industries, from aerospace to automotive. However, like any manufacturing process, CNC machining has. Understanding and addressing common defects is crucial for maintaining high quality and efficiency.
This blog will delve into the typical defects encountered in CNC machining. By recognizing these issues, manufacturers can take proactive steps to mitigate them, ensuring the production of high-quality parts. Whether you're a seasoned engineer or new to CNC machining, this exploration will enhance your knowledge and help you better navigate the complexities of this advanced manufacturing process. Let's begin by understanding CNC machining and why identifying common defects is vital for success.
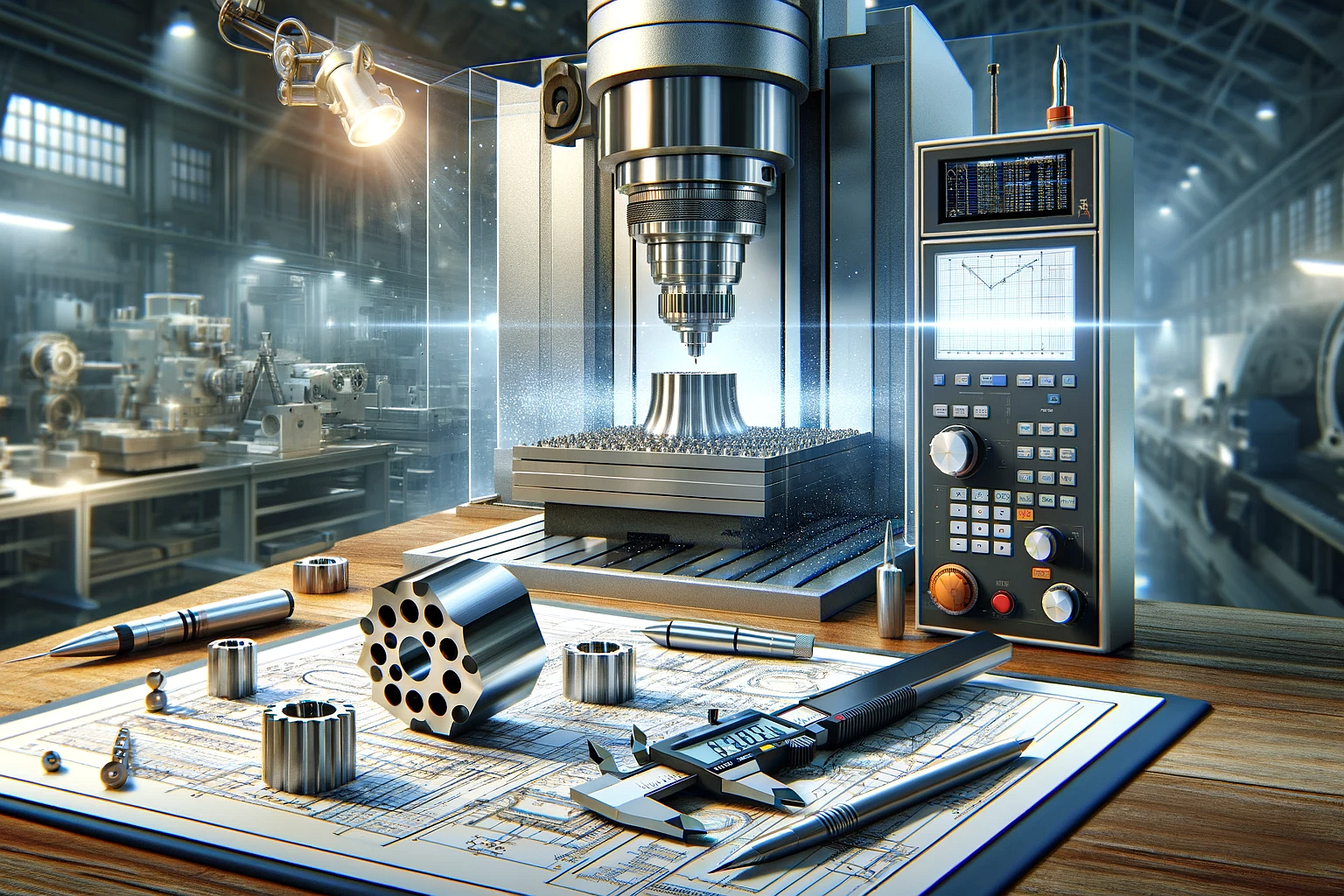
Overview of CNC Machining
CNC, short for Computer Numerical Control, machining is a manufacturing process that relies on computerized control systems to manipulate tools and machinery to produce parts and components precisely. It has become an integral part of modern manufacturing due to its ability to deliver high accuracy, consistency, and efficiency levels.
Applications of CNC Machining
CNC machining finds applications across various industries, making it a versatile and indispensable technology. Some common sectors where CNC machining is extensively used include:
Aerospace: CNC machining is vital for crafting intricate aerospace components that demand precision to ensure the safety and reliability of aircraft and spacecraft.
Automotive: In the automotive industry, CNC machining is employed to manufacture engine parts, transmission components, and custom car modifications.
Medical: The production of medical implants and devices relies on CNC machining to meet stringent quality and dimensional requirements.
Electronics: Precision is paramount in the electronics industry, and CNC machining plays a crucial role in producing circuit boards, connectors, and intricate electronic components.
Industrial Equipment: Manufacturing machinery and industrial equipment benefit from CNC machining's ability to create complex and durable parts.
Critical Components of a CNC Machine
To understand CNC machining fully, it's essential to grasp the critical components of a CNC machine:
Computer Control Unit (CCU): The brain of the CNC machine, the CCU interprets computer-generated code and translates it into precise movements and actions.
Machine Tools include cutting tools, spindles, and worktables where the material is shaped or cut.
Axes of Motion: CNC machines can have multiple axes of motion (typically three to five), allowing for intricate and multidimensional operations.
Advantages of CNC Machining
CNC machining offers several advantages, making it a preferred choice for precision manufacturing:
High Precision: CNC machines can achieve tolerances as tight as a few microns, ensuring parts meet exact specifications.
Repeatability: Once a program is set, CNC machines can produce identical parts consistently, reducing errors and waste.
Complex Geometry: CNC machining can create intricate shapes and contours that would be challenging or impossible with manual methods.
Efficiency: With automation, CNC machining can run 24/7, maximizing productivity.
Cost-Effective: While initial setup costs can be high, CNC machining often proves cost-effective for large production runs due to reduced labor and material waste.
Common Defects in CNC Machining
CNC machining is a precise and efficient manufacturing process that plays a pivotal role in various industries. However, like any manufacturing method, it is not immune to defects that can affect the quality and functionality of the produced parts. In this section, we will delve into some of the common defects encountered in CNC machining, along with their causes and methods of prevention.
Surface Finish Irregularities
One of the most noticeable defects in CNC machining is surface finish irregularities. These imperfections manifest as uneven surfaces, visible marks, or rough textures on the part's exterior. Surface finish is crucial, especially in applications where aesthetics and friction are important factors.
Examples: Surface finish irregularities can be tool marks, scratches, or waviness on the part's surface. For instance, if the cutting tool experiences excessive wear or vibrations during machining, it can leave behind undesirable marks on the workpiece.
Impact on Part Functionality: Surface finish irregularities can compromise the performance and appearance of the final product. In applications where low friction is essential, such as in bearings or sealing components, rough surfaces can lead to increased wear and reduced efficiency.
The ultimate surface roughness of CNC: The best surface roughness achieved by CNC machining is Ra 0.2, which is close to the surface roughness of ordinary polishing. However, very slight knife lines can also be discerned with the naked eye, and these knife lines can be concealed through surface treatments such as anodizing, powder spraying, and sandblasting.
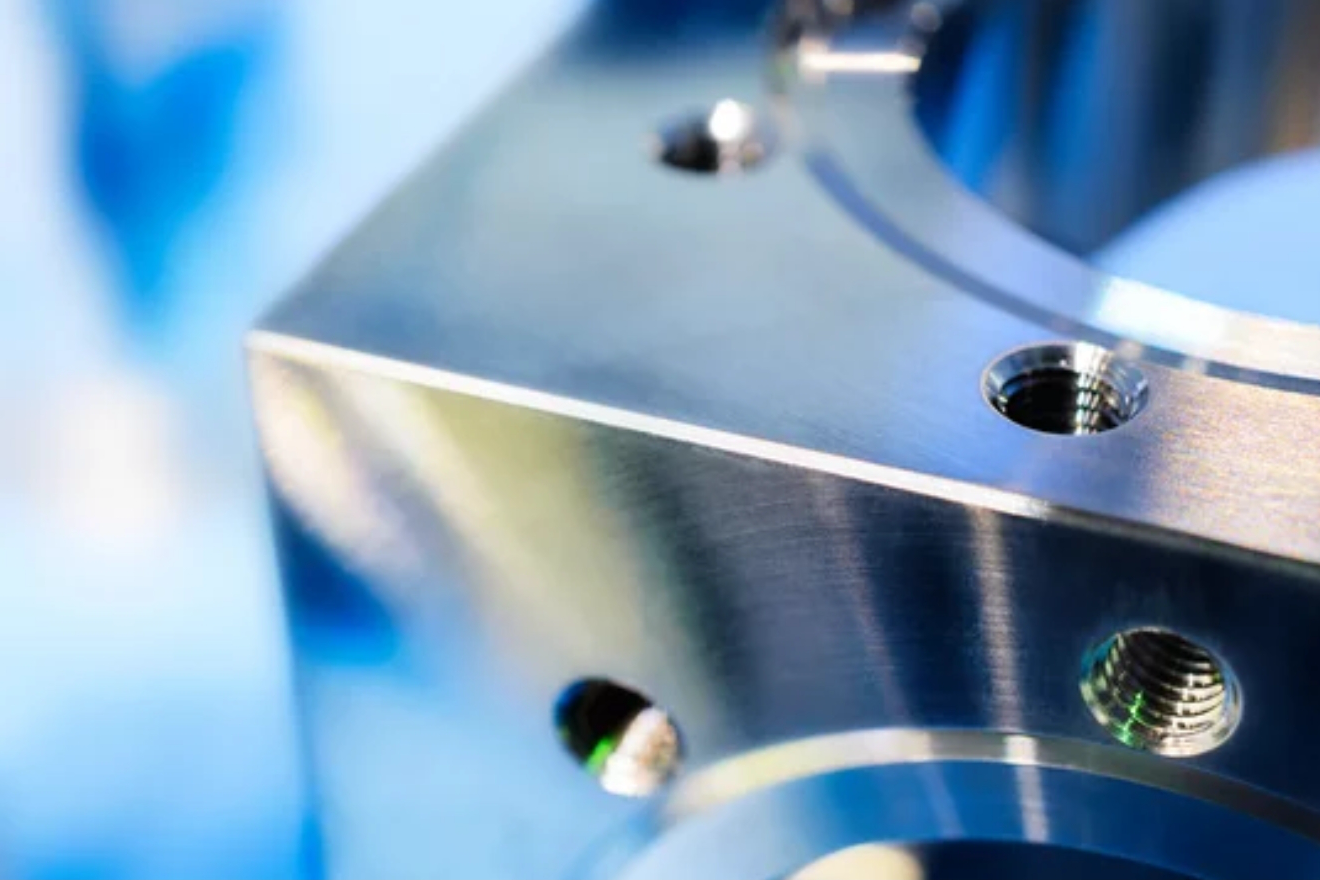
Dimensional Inaccuracies
Achieving precise dimensions is paramount in CNC machining, as parts must meet tight tolerances to function correctly. Dimensional inaccuracies occur when the final part deviates from the intended measurements.
Causes: Several factors can contribute to dimensional inaccuracies, including tool wear, improper toolpath programming, or inadequate machine calibration.
Effects on Part Tolerances: Specific numerical values dictate how closely a part must match its intended dimensions. For example, a part with a tolerance of ±0.005 inches means that its dimensions must fall within this range. Dimensional inaccuracies exceeding these tolerances can render a part unusable or require costly rework.
Tool Marks and Burrs
Tool marks and burrs are undesirable raised edges or protrusions on a machined part. They are typically the result of machining operations and can impact the part's functionality and aesthetics.
How They Occur: Tool marks and burrs often form during cutting or milling operations when the tool's edge interacts with the material. Excessive feed rates, improper tool geometry, or tool wear can exacerbate these issues.
Methods for Prevention and Removal: To prevent tool marks and burrs, it's essential to select the appropriate tool geometry and maintain tools in good condition. Post-processing methods like deburring, abrasive finishing, or chamfering can help remove existing burrs and improve the part's overall quality.
Material-Related Defects
Inconsistencies in Material Properties
Understanding Material Properties:
Every material used in CNC machining has distinct characteristics, like hardness, strength, and thermal conductivity. These properties directly influence the machining process and the quality of the final product. For example, softer materials like aluminum may machine easily but are prone to deformation, while harder materials like stainless steel can wear down tools faster.
Choosing the Right Material:
Selecting the appropriate material is crucial for minimizing defects. For instance, a part requiring high strength might be best made from titanium, whereas a part needing good thermal conductivity could be better suited with copper. It's important to match the material properties to the part's intended use.
Impact of Material Variability:
Materials can have slight composition or grain structure variations even within the same batch. These inconsistencies can lead to uneven machining results, like varying surface finishes or dimensional inaccuracies. Manufacturers should source materials from reliable suppliers to ensure consistency.
Thermal Expansion and Contraction
Temperature's Role in CNC Machining:
Materials expand when heated and contract when cooled. During CNC machining, the heat generated by the cutting process can cause materials to expand, affecting their dimensions. For example, a metal part might expand by 0.0025 mm per meter for every degree Celsius increase in temperature.
Controlling Thermal Effects:
To mitigate these effects, manufacturers use controlled environments with consistent temperatures. Also, tools with higher thermal stability can be used to reduce the heat generated during machining. For precise operations, allowing the part to cool down and stabilize before final measurements and adjustments is essential.
Material Selection for Thermal Stability:
Some materials are more susceptible to thermal expansion than others. For instance, plastics and certain metals like aluminum have higher thermal expansion coefficients than cast iron or steel materials. Selecting a material with lower thermal expansion can reduce the risk of defects due to temperature variations.
Best Practices for Handling Material-Related Defects
Material Testing: Conduct thorough testing of materials to understand their properties and behavior under machining conditions.
Supplier Quality Assurance: Partner with suppliers who provide consistent quality materials.
Environmental Control: Maintain a controlled machining environment to minimize temperature fluctuations.
Material Selection: Choose materials that align with the part's functional requirements and the limitations of the CNC process.
By understanding and addressing these material-related defects, manufacturers can significantly improve the precision and quality of CNC machined parts. This section highlights common issues and provides practical solutions, aiding in the continual improvement of CNC machining practices.
Machine and Process-Based Defects
Calibration Errors
The Need for Precision:
Calibration is critical in CNC machining. Even a minor deviation can lead to significant errors in the final product. For example, if a CNC machine is off by just 0.001 inches in its calibration, it can result in a dimensional inaccuracy that renders a part unusable for precision applications.
Regular Calibration Checks:
To avoid such issues, it's essential to perform regular calibration checks. This involves verifying the accuracy of the machine's movements and alignments using precise measuring instruments. Regular calibration ensures the machine operates within the required tolerances, often from 0.0005 inches to 0.001 inches for high-precision tasks.
Incorrect Tool Selection
Impact on Output Quality:
Choosing the wrong tool for a job can adversely affect the machined part's surface quality and dimensional accuracy. For instance, a tool that's too large may not be able to achieve the required fine details, while a tool that's too small may take longer and wear out quicker, leading to inconsistencies.
Tool Selection Best Practices:
It's vital to select tools based on the material being machined, the type of operation (like drilling, milling, or turning), and the specific details of the design. For example, a high-speed steel tool might suit softer materials, but carbide tools might be necessary for more rigid materials.
Programming Errors
Common Causes:
CNC machines rely on precise programming to operate. Errors in the programming can lead to defects such as incorrect dimensions, unwanted tool paths, or even machine crashes. These errors can stem from incorrect data input, misunderstanding of the design requirements, or software glitches.
Minimizing Programming Mistakes:
It's important to have a thorough review process to minimize these errors. This includes double-checking the programmed dimensions against the design specifications, simulating the tool paths before machining, and having experienced operators and programmers collaborate to identify potential issues.
Strategies for Addressing Machine and Process-Based Defects
Routine Machine Maintenance: Regularly inspect and maintain machinery to ensure optimal performance.
Staff Training: Ensure operators and programmers are well-trained and updated on CNC technologies and practices.
Use of Advanced Software: Implement advanced CAD/CAM software for accurate programming and simulation of machining processes.
Quality Control Protocols: Establish strict quality control protocols, including pre-machining checks and post-machining inspections.
Preventive Measures CNC Machining Defects
Regular Maintenance and Machine Upkeep
Machinery Longevity:
Maintaining CNC machines in peak condition is essential for consistent and defect-free production. Neglected machines are more likely to develop issues that can lead to defects. Regular maintenance ensures the longevity of these costly investments.
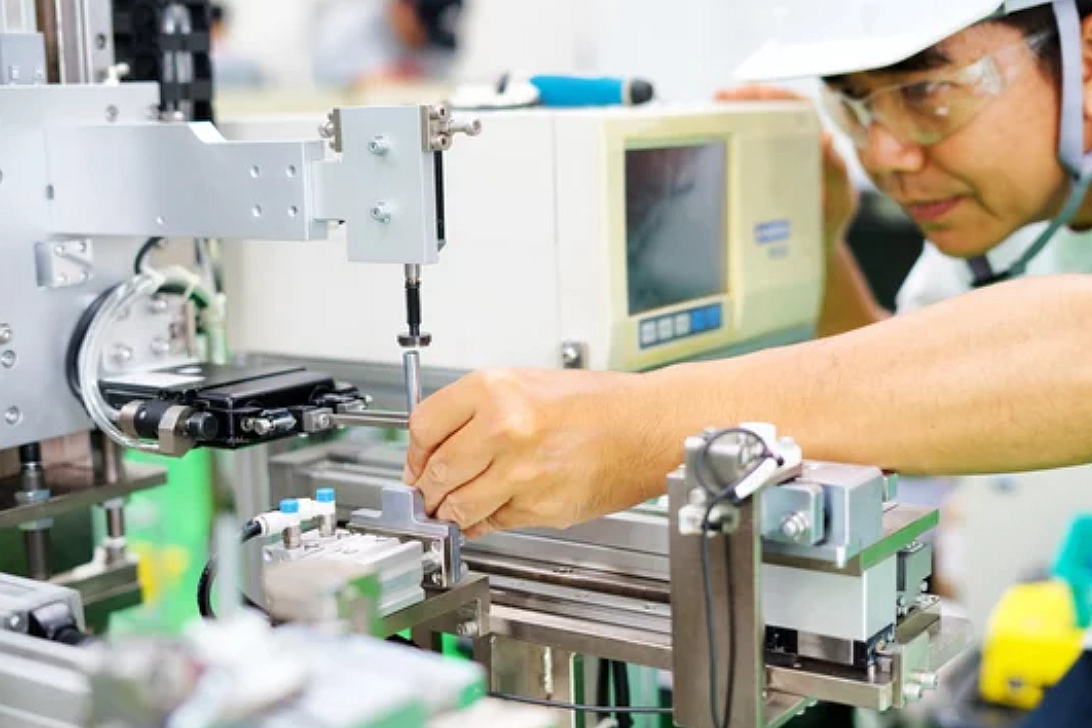
Maintenance Schedule:
Establish a comprehensive maintenance schedule with routine checks on critical components like spindles, bearings, and coolant systems. Specific intervals for maintenance depend on factors such as machine usage and environmental conditions but typically range from weekly to monthly.
Choosing the Right Tools and Materials
Tool Selection:
Selecting the right cutting tools and tool holders is crucial. Tools should match the machined material, the desired surface finish, and dimensional accuracy. Additionally, factors like tool wear and replacement frequency should be considered. Utilize tools made from high-quality materials for longer lifespan and precision.
Material Compatibility:
Carefully evaluate material choices based on the project's requirements. Consider the material's machinability, thermal properties, and compatibility with the machining process. Choosing the correct material minimizes the risk of defects caused by material-related issues.
Quality Control Measures
Preventive Quality Checks:
Implement a robust quality control system with regular inspections at various machining stages. Pre-machining checks ensure that materials and tools meet specifications, while in-process inspections catch issues early, reducing the likelihood of costly defects.
Precise Measuring Instruments:
Invest in precise measuring instruments like micrometers, calipers, and coordinate measuring machines (CMMs). These instruments enable accurate dimensional verification and ensure that parts meet tight tolerances, often in the range of micrometers (μm).
Statistical Process Control (SPC):
Implement SPC techniques to monitor and control the machining process. SPC involves collecting and analyzing data during production to identify trends and variations. By proactively addressing deviations from the norm, manufacturers can prevent defects from occurring.
Best Practices for Preventing Defects in CNC Machining
Scheduled Maintenance: Adhere to a routine maintenance schedule for CNC machines.
Tool and Material Expertise: Ensure your team is knowledgeable about tool and material selection.
Quality Control Integration: Integrate quality control checks at various stages of production.
Data-Driven Decisions: Use data analysis and SPC to identify and rectify process deviations.
Conclusion
In precision manufacturing, CNC machining is a cornerstone for producing high-quality parts and components. However, achieving precision and quality has its challenges. This blog has explored the intricacies of CNC machining, focusing on the critical aspect of understanding and addressing common defects.
By taking a closer look at CNC machining, we've uncovered the following key insights:
Precision in Practice: CNC machining offers unparalleled precision and repeatability but requires a deep understanding of its intricacies to unlock its full potential.
Common Defects: Surface finish irregularities, dimensional inaccuracies, tool marks, and material-related defects can plague CNC machining processes, affecting part functionality and quality.
Root Causes: Defects often stem from tool wear, programming errors, material variations, and thermal effects.
Preventive Measures: Regular maintenance, proper tool and material selection, and stringent quality control protocols are essential to prevent defects.
Real-World Solutions: Case studies have demonstrated that identifying root causes, implementing targeted solutions, and continuous process improvement can lead to defect reduction and enhanced quality.
As we conclude, it's crucial to emphasize that CNC machining is not just a process but a craft that demands expertise, precision, and a commitment to excellence. By embracing preventive measures, implementing best practices, and learning from real-world examples, manufacturers can continue to refine their CNC machining practices, delivering superior quality components for various industries.
The journey to precision in CNC machining is ongoing, and we hope that this blog has provided valuable insights and guidance to manufacturers striving for perfection in their craft. As technology advances and knowledge expands, the possibilities for achieving higher levels of precision and quality in CNC machining are limitless. Keep exploring, learning, and innovating to meet the ever-evolving demands of precision manufacturing.
评论
发表评论