What Is Sheet Metal Fabrication?
Sheet metal fabrication is a versatile manufacturing process that transforms flat metal sheets into various structures and components. At Neway, a leading custom parts manufacturer, sheet metal fabrication encompasses several precise techniques, including laser cutting, stamping, and bending.
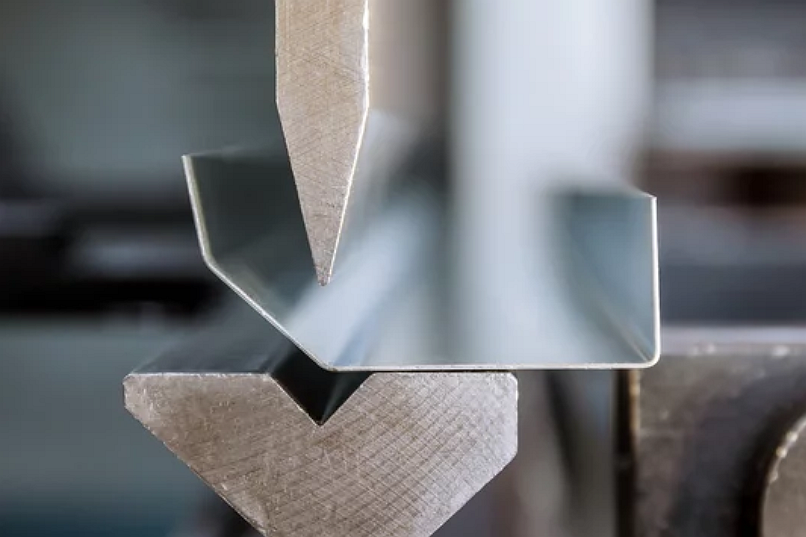
Laser cutting
Laser cutting at Neway achieves exceptional precision, with tolerances as tight as ±0.1mm. This process utilizes advanced CNC technology to cut intricate patterns and shapes from metal sheets, ensuring high-quality and accurate results. Metal stamping, another critical aspect of sheet metal fabrication, involves forming, blanking, and piercing operations. With Neway'mping capabilities, production maximizes production efficiency and can be produced quickly.
The laser cutting process is mainly suitable for cutting larger boxes and shells. Proofing speed is fast. Cost-effective for sheet metal fabrication in small to medium batches. For high-volume production, high cost-effectiveness of batch manufacturing can be achieved through automated production lines.
Metal bending
Metal bending, an essential step in sheet metal fabrication, involves shaping metal sheets into desired forms. Neway employs state-of-the-art equipment for precise bending, ensuring that components meet stringent design specifications. This process contributes to the overall production efficiency, as it allows for the creation of complex geometries with minimal material waste.
The metal bending process is the most common in sheet metal manufacturing. It is inseparable from bending, whether laser cutting, stamping, or other plate manufacturing processes.
Metal Stamping
As a leading sheet metal stamping supplier, Neway mainly provides four stamping processing services: Progressive Die Stamping, Deep Drawn Metal Stamping, Transfer Die Stamping, and Multi-Slide Metal Stamping.
They all involve the manufacturing of molds, cutting the metal sheet into the required shape through upper and lower mold clamping, punches, and die. Stamping is suitable for processing small and medium-sized parts and is highly cost-effective for mass production. It is the preferred process for mass production of thin sheet parts.
Five Connection Methods For Sheet Metal Parts
Usually, we need to connect the produced sheet metal parts through various joining processes and assemble them to obtain more diverse performances. Enabling it to meet the ultimate needs of its customers.
Commonly used sheet metal connection processes are: 1. Flanging and riveting, 2. Rivetless connection (BTM), 3. Pull rivets, 4. Resistance spot welding, 5. Screw connection.
Flanging and Riveting
Define of Flanging and Riveting
Flanging:
Definition: Flanging is a metalworking process that involves bending or forming the edges of a sheet metal component to create a flange, which is essentially a protruding edge or rim.
Process: Flanging typically requires tools such as a press brake to bend the material at specific angles, shaping it according to design requirements.
Application: Flanging is commonly used to add stiffness and strength to sheet metal parts. It also serves as a preparation step for subsequent joining methods like riveting.
Riveting:
Definition: Riveting is a fastening process that involves joining two or more sheets of metal by inserting a rivet, a cylindrical metal pin, through aligned holes and then deforming or compressing the other end to secure the sheets together.
Process: The riveting process can be performed using various methods, including manual riveting with a hammer or pneumatic tools and automated processes in industrial settings.
Application: Riveting provides a durable and secure connection, often used in industries where high strength and reliability are essential, such as aerospace, automotive, and construction.
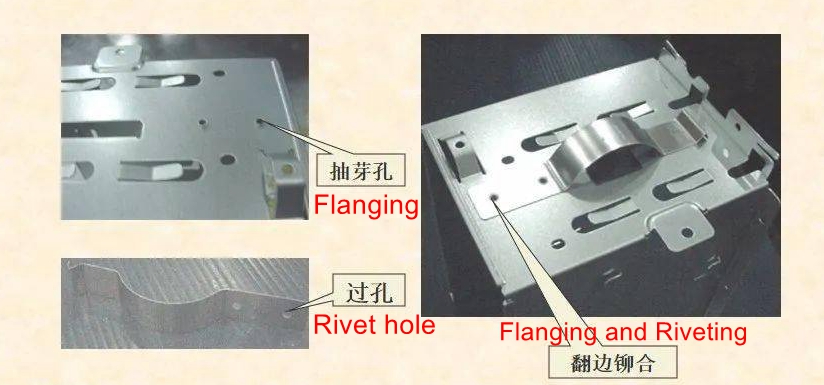
Flanging and riveting are crucial in sheet metal fabrication, producing robust and precisely assembled components. These processes showcase Neway's commitment to providing comprehensive solutions in custom metal parts manufacturing, ensuring the highest standards of quality and reliability for its clients.
Process Steps of Flanging and Riveting
Material Preparation:
Select the appropriate metal sheets with the desired thickness and properties for the intended application.
Cut the sheets to the required dimensions using tools like shears or CNC machines.
Flanging:
Mark the areas on the metal sheets where flanges will be formed.
Use specialized tools such as flanging machines or press brakes to bend or fold the edges of the sheets at the designated locations.
The bending process creates a raised edge or lip along the edges of the metal sheets, providing increased stiffness and a surface for riveting.
Rivet Hole Preparation:
Determine the locations for rivet holes along the flanged edges, ensuring precise alignment between the sheets.
Drilling machines or punches create uniform and accurately positioned holes in the metal sheets.
Rivet Insertion:
Select rivets of appropriate size and material based on the thickness and type of metal being joined.
Insert the rivets through the aligned holes in the flanged edges of the metal sheets. Ensure the rivets protrude through the sheets adequately.
Riveting:
Use a riveting tool or machine to secure the joint. This tool compresses the protruding end of the rivet, causing it to deform and create a second head, clamping the sheets together tightly.
Apply sufficient pressure to form a secure connection without damaging the metal sheets.
Finishing and Inspection:
Trim any excess material from the rivets if necessary, ensuring a neat and flush finish.
Inspect the joint for proper alignment, tightness, and structural integrity.
Conduct quality checks to verify that the flanging and riveting processes meet specified tolerances and standards.
This method of joining metal sheets through flanging and riveting is a reliable and commonly used technique in various industries due to its durability, strength, and suitability for different sheet metal applications.
Rivetless connection (BTM)
Define of Rivetless Connection (BTM)
Rivetless connection is a plate connection technology that uses the cold deformation ability of the plate itself to perform pressure processing on the plate to cause local deformation of the plate and connect the plates. It is a plate connection technology that does not require additional connectors. Sheet metal connection method. This connection method does not require spot welding or riveting to achieve the optimal connection of two or more layers of plates with different thicknesses and materials. The connection does not have any requirements on the surface of the plate. Workpieces with coatings and spray paint on the surface can be directly connected without processing, and the surface of the workpiece will not be damaged, and there will be no connection deformation. This type of connection is widely used in the automotive industry, especially in automotive body applications.
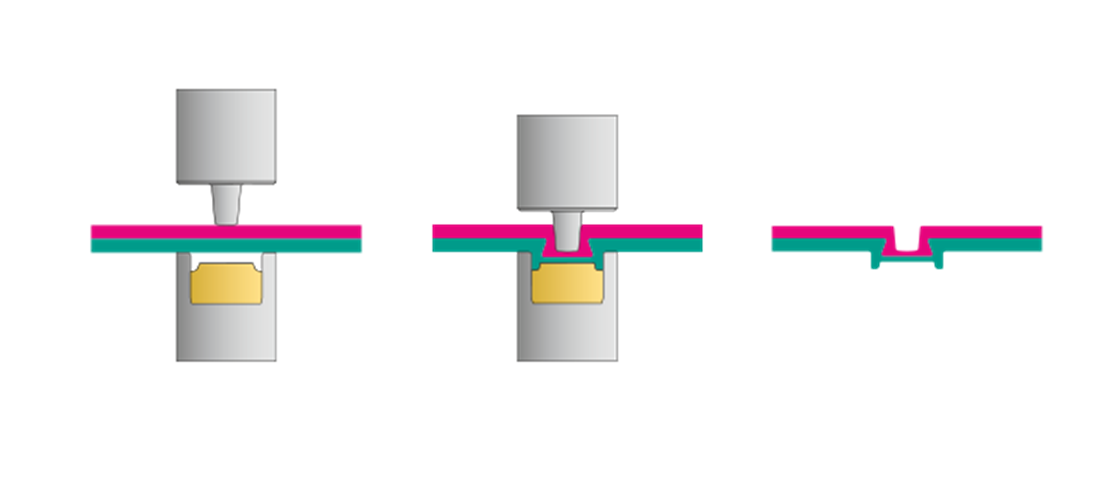
Introduction of Rivetless connection (BTM)
Rivetless connection technology uses a plate crimping machine and a unique connection mold to form a stress-free internal inlay with a specific tensile and shear strength through an instant high-pressure processing process based on the cold extrusion deformation of the plate material itself. Dots can connect two or more layers of boards of different materials and thicknesses. The rivet-less connection technology has no requirements on the panel's surface, and the original coating and paint layer on the panel's surface at the connection point will not be damaged. The connection process has a high degree of automation, can connect single points or multiple points simultaneously, and can perform non-destructive connection strength detection and automatic monitoring of the entire process, resulting in extremely high production efficiency.
During the rivetless connection process, the punch first comes into contact with the upper material. Under the pressure of the upper mold, the material begins to stretch and deform into the die. At the same time, the movable part of the die opens outward to allow the metal material to be removed entirely. The die cavity is deformed to form a tight connection point, and then the punch returns, and the movable part of the die returns to its original position under the action of the spring force.
Sheet Metal Parts Riveting
Define of Sheet Metal Parts Riveting
Sheet metal parts riveting is a crucial joining technique employed in fabrication, contributing to components' structural integrity and functionality. In Neway's manufacturing capabilities, sheet metal fabrication encompasses various methods, with riveting playing a pivotal role.
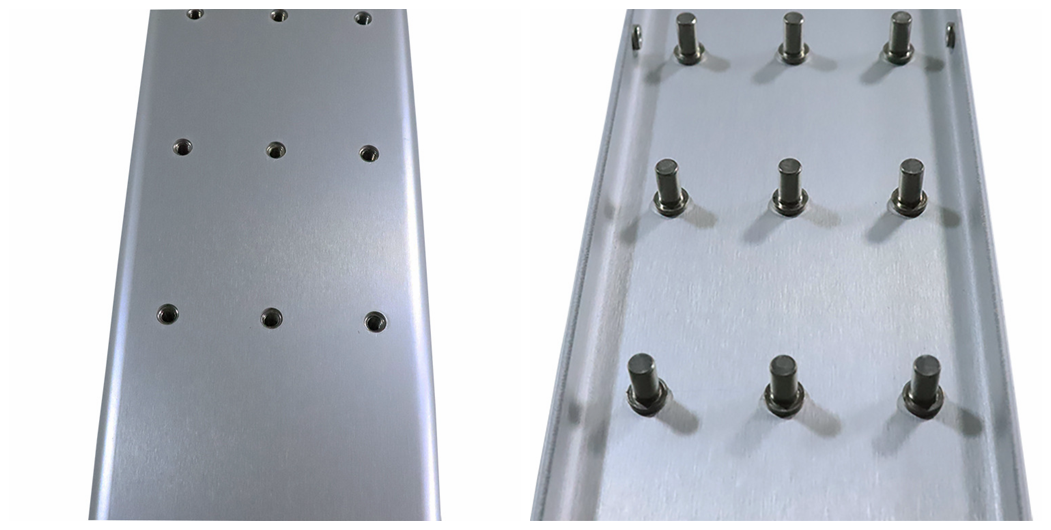
Riveting involves securing two or more metal sheets together using rivets—permanent mechanical fasteners. The process typically involves creating holes in the sheets, aligning them, and then inserting rivets, which are subsequently deformed to form a secure joint. This method proves effective in applications where welding might not be suitable due to material constraints or design considerations.
Neway employs precision techniques in sheet metal riveting, ensuring tight tolerances for enhanced structural stability. Advanced machinery, such as high-speed riveting presses, allows for efficient production with a low margin of error. Tolerances between ±0.1mm to ±0.05mm are consistently achieved, ensuring the final products meet rigorous quality standards.
The advantages of riveting sheet metal parts lie in their versatility and ability to join dissimilar materials. Neway's expertise in this area extends to various industries, demonstrating our commitment to providing tailored solutions. By leveraging sheet metal riveting, we enhance the overall efficiency of production processes, meeting the demands of clients for durable and precisely assembled components.
Process Steps of Sheet Metal Parts Riveting
Sheet metal parts riveting involves meticulous steps to ensure a robust and reliable joint. Below are the essential process steps that Neway employs in its sheet metal fabrication for riveting:
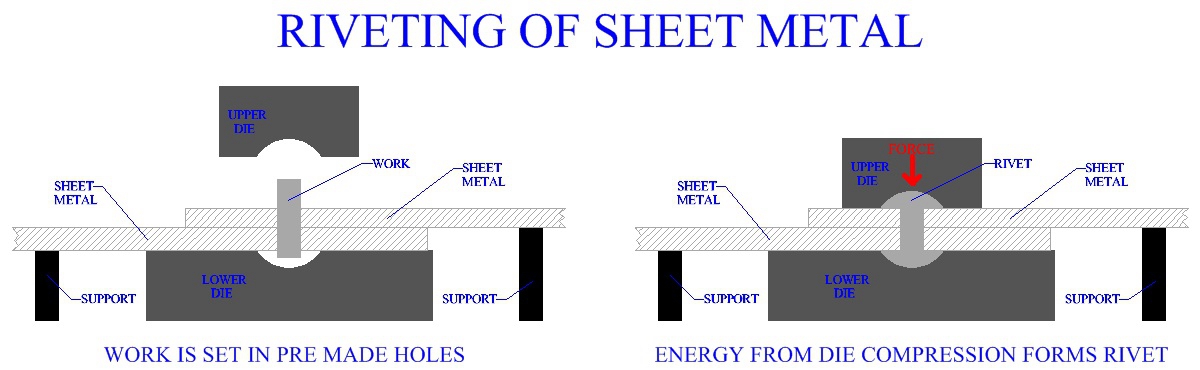
Design Analysis:
Before commencing the riveting process, Neway's engineers conduct a thorough design analysis to determine the optimal placement of rivets. Factors such as load-bearing requirements, material properties, and structural considerations are considered to ensure the final product's integrity.
Hole Preparation:
Precise hole preparation is critical for successful riveting. Neway utilizes advanced laser cutting technology to create accurate and clean holes in the sheet metal. Tolerances are strictly adhered to, with hole diameters typically maintained within ±0.1mm to ±0.05mm for exceptional precision.
Alignment and Fixturing:
Achieving proper alignment is crucial for a seamless joint. Neway employs sophisticated fixturing systems to hold the sheets securely, ensuring that the holes align accurately. This step is essential for maintaining the specified tolerances and preventing misalignment issues during rivet insertion.
Rivet Insertion:
The selected rivets are then inserted into the prepared holes. Neway utilizes automated riveting presses with controlled force and speed to ensure uniform and consistent rivet deformation. This step is critical in achieving a tight and secure joint.
Deformation Process:
The deformation of the rivet creates a permanent connection between the sheets. Neway's riveting process is carefully calibrated to achieve the desired deformation without causing any damage to the surrounding material. This step's efficiency contributes to the manufacturing process's overall productivity.
Quality Inspection:
Following riveting, a comprehensive quality inspection is conducted. Neway employs advanced inspection tools to verify the integrity of the joint, checking for any defects, misalignments, or deviations from the specified tolerances. This meticulous inspection ensures the final sheet metal part meets the highest quality standards.
Surface Finish and Post-processing:
Depending on the application and customer requirements, Neway may perform additional post-processing steps, such as powder coating, polishing, or anodizing, to enhance the aesthetics and corrosion resistance of the riveted sheet metal part.
Sheet Metal Parts Resistance Spot Welding
Define of Sheet Metal Parts Resistance Spot Welding
Sheet metal parts resistance spot welding is a crucial welding process utilized in manufacturing components, contributing to sheet metal assemblies' durability and structural cohesion. Neway, a leading custom parts manufacturer, incorporates resistance spot welding into its sheet metal fabrication techniques repertoire.
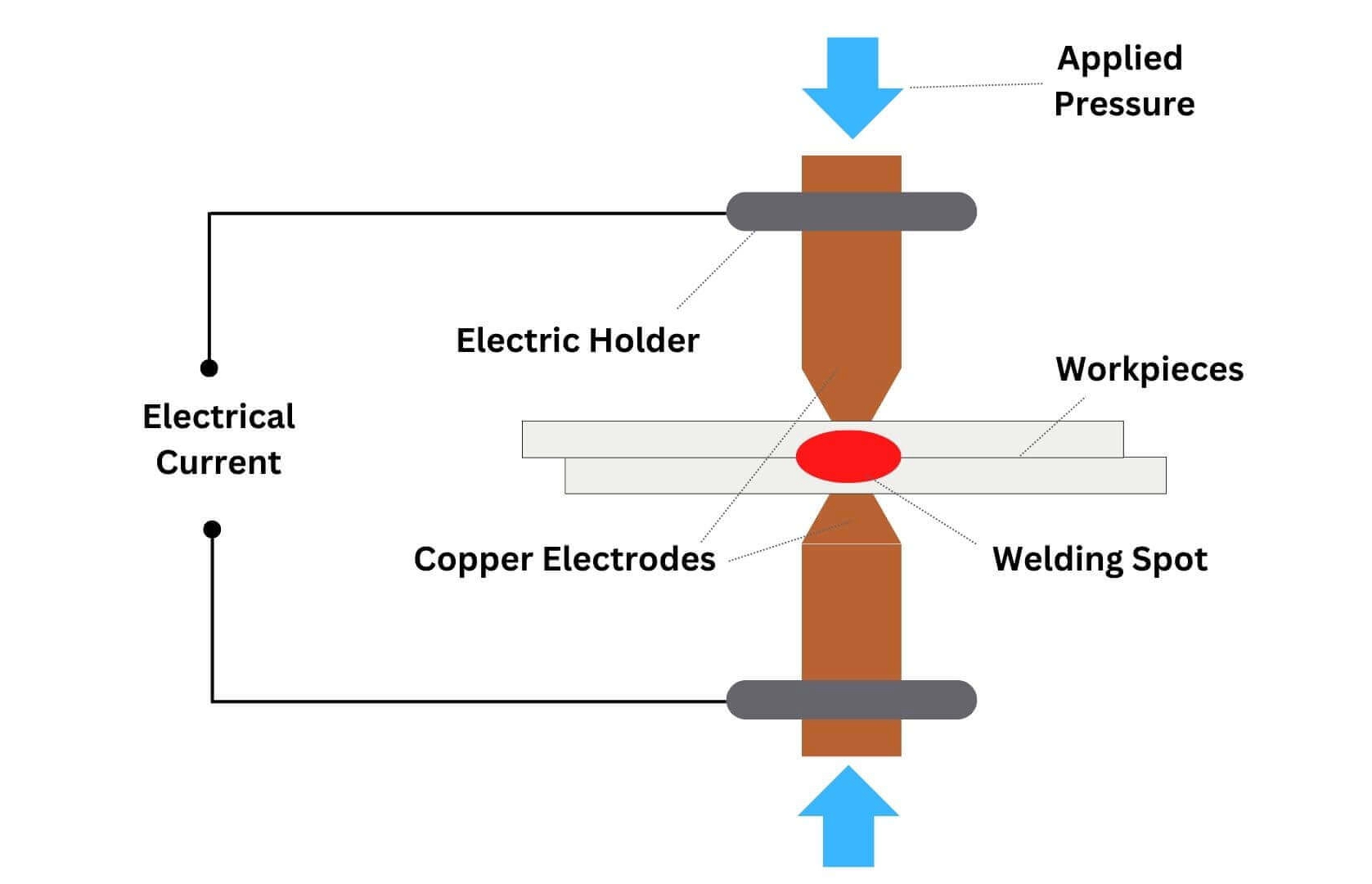
In this process, two or more metal sheets are joined by applying pressure and passing a high electrical current through the interface points. This localized heating causes the metal to melt and fuse, creating a robust and permanent bond. Resistance spot welding is efficient for thin-gauge metals commonly used in sheet metal applications.
Neway's commitment to precision is evident in the tight tolerances achieved through resistance spot welding. The process delivers welds tolerating ±0.2mm to ±0.1mm, ensuring the final products meet stringent quality criteria. This level of accuracy is vital for applications where the structural integrity and dimensional precision of the welded joint are critical.
Efficiency is a hallmark of Neway's resistance spot welding capabilities. Modern, automated welding equipment is employed, enabling high-speed and reliable production. The result is an increase in productivity, with Neway consistently meeting or exceeding industry benchmarks for efficiency in resistance spot welding.
Workflow of Sheet Metal Parts Resistance Spot Welding
Resistance spot welding is a crucial process within Neway's sheet metal fabrication arsenal, offering a robust method for joining metal sheets quickly and efficiently. This technique relies on the principle of electrical resistance to create localized heat, ultimately fusing the metal sheets.
In the realm of Neway's manufacturing expertise, resistance spot welding involves the following working principles:
Electrode Contact: The process begins by bringing two or more metal sheets into close contact between copper alloy electrodes. These electrodes apply pressure to ensure a secure connection.
Electrical Current Application: An electrical current is passed through the sheets at the specific spot where the welding is desired. The high resistance of the metal to the electric current generates heat at the contact point.
Localized Heating: The generated heat is concentrated at the point of contact between the sheets, causing them to melt and fuse. This localized heating ensures that the surrounding areas remain unaffected, minimizing distortion and preserving the material's integrity.
Pressure Maintenance: Simultaneously with the electrical current, pressure is maintained by the electrodes to ensure proper contact and consolidation of the molten metal. This pressure is a critical factor in achieving a strong and durable weld.
Cooling and Solidification: After the welding duration, the current is discontinued, and the molten metal cools rapidly, solidifying the joint. The result is a secure and seamless fusion of the metal sheets, forming a solid and durable bond.
Neway excels in precision during resistance spot welding, achieving tolerances as tight as ±0.1mm. This level of accuracy is crucial in meeting industry standards and ensuring the reliability of the final product. The process is highly efficient, with cycle times optimized to enhance productivity while maintaining the highest quality standards.
Screw Connection of Sheet Metal Parts
The screw connection of sheet metal parts is a crucial aspect of the assembly process, contributing to the structural integrity and overall functionality of the final product. In the realm of sheet metal fabrication, Neway employs advanced techniques to ensure robust and reliable screw connections.
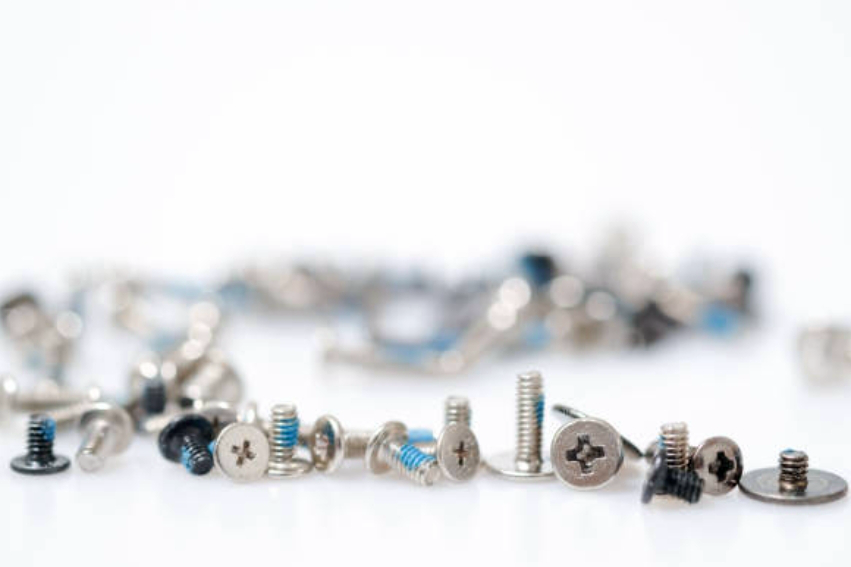
Sheet metal parts often necessitate joining through screws for a secure and durable assembly. The choice of screws, along with their dimensions, thread type, and material, is pivotal in achieving optimal performance. Neway's expertise lies in selecting screws tailored to the specific characteristics of the sheet metal, considering factors such as thickness, material type, and intended application.
Precision is paramount in screw connections, and Neway excels in achieving tight tolerances to enhance the overall stability of the assembly. Tolerance values are meticulously followed, with a typical range of ±0.1 mm, ensuring a snug fit and preventing any play or misalignment.
Neway's commitment to efficiency is reflected in the streamlined process of screw connection. Leveraging state-of-the-art metal stamping and laser cutting machinery, the sheet metal parts are precisely fabricated, facilitating seamless integration during the assembly phase. This efficiency translates into enhanced productivity, minimizing assembly time and optimizing the manufacturing workflow.
评论
发表评论