The automotive industry, a global manufacturing cornerstone, relies heavily on metal parts to construct vehicles. These parts, from engine components to structural frames, are integral to automobiles' functionality, safety, and performance. Manufacturing these large auto parts utilizes specialized processes, notably stamping and deep-drawn techniques, to shape metal sheets into precise, complex forms.
Stamping and deep drawing are critical in producing large, durable auto parts with high precision. Stamping involves pressing flat metal sheets into a desired shape using a die and a press machine. This process is ideal for quickly and efficiently creating large quantities of parts with uniform specifications. On the other hand, deep drawing extends this principle to produce parts with a depth greater than their diameter, enabling the creation of complex, hollow shapes that stamping alone cannot achieve. Both processes are fundamental in manufacturing robust components like car bodies, fuel tanks, and engine parts, which must meet stringent quality standards.
Understanding Stamping and Deep Drawn Processes
Stamping and deep drawing are critical processes for shaping metal in automotive manufacturing. Though both techniques are designed to transform flat metal sheets into three-dimensional parts, they employ distinct methods and serve different purposes within auto parts manufacturing. Understanding these processes, their applications, and their advantages is crucial for appreciating the technological artistry behind automotive production.
Definition and Comparison
Stamping is a cold-forming process that involves placing a flat sheet of metal, often steel or aluminum, in a press where a tool and die surface form the metal into a new shape. The process encompasses a variety of specific techniques, including punching, embossing, bending, and coining, making it highly versatile for creating detailed and complex parts. Stamping is particularly suited for high-volume production runs where consistency and speed are paramount.
Deep Drawing, on the other hand, is a specialized form of stamping that draws the metal sheet into a die by a mechanical action, creating a part whose depth can exceed its diameter. This process is ideal for manufacturing components with significant depth, such as automotive body panels, fuel tanks, and specific engine parts. Deep Drawing requires precise control over material properties and process parameters to avoid common defects like wrinkling, tearing, or earring.
Key Differences in Applications
While both processes manufacture auto parts, their applications within the automotive industry vary based on the part requirements. Stamping is often the go-to process for flat or moderately complex parts that require high strength and durability, such as brackets, chassis components, and structural reinforcements. Its ability to rapidly produce many parts makes it essential for meeting the automotive industry's demands.
Deep Drawing is chosen for parts that require a hollow, seamless construction with a high depth-to-diameter ratio. Components like fuel tanks, housing for specific mechanical systems, and complex panels benefit from Deep Drawing's ability to create durable, lightweight parts without compromising structural integrity.
Advantages of Each Process
Tolerance and Precision: Both stamping and deep Drawing offer exceptional precision, with tolerances as tight as ±0.01 mm for stamping and slightly higher for deep Drawing, depending on the material and part complexity. This precision is critical in automotive manufacturing, where even minor deviations can lead to assembly issues or performance deficits.
Material Usage and Cost-Effectiveness: Stamping and deep Drawing are lauded for their efficient use of material, minimizing waste through careful design and process control. This efficiency reduces material costs and contributes to the sustainability of manufacturing operations. The ability to produce large volumes of parts quickly and with minimal material waste makes both processes highly cost-effective, especially for high-volume production runs typical in the automotive industry.
Versatility and Application Range: The versatility of stamping and deep drawing processes allows for a wide range of applications, from simple flat components to complex, three-dimensional shapes. This adaptability ensures that automotive manufacturers can employ these techniques across various parts, enhancing the vehicle's overall design and functionality.
The Stamping Process for Large Auto Parts
The stamping process is integral to manufacturing large auto parts, providing the automotive industry with a reliable method for producing components at high volumes. This section delves into the specifics of the stamping process, including design considerations, material selection, tooling, and a case study that highlights the efficiency and precision achievable through stamping.
Design and Material Selection
The initial step in the stamping process involves meticulous design and material selection, ensuring the final component meets the required specifications for strength, durability, and performance. Engineers use advanced CAD (Computer-Aided Design) software to model the part and simulate the stamping process, which helps identify potential issues before production begins.
Material selection is paramount, with choices often including steel, aluminum, and alloys tailored for specific properties like tensile strength, flexibility, and corrosion resistance. The chosen material must suit the part's functional requirements and manufacturability, considering how different metals behave under the stresses of stamping.
Tooling
Tooling in stamping involves the creation of dies and punches designed to cut, shape, and form the metal sheet into the desired part. The complexity of these tools can vary significantly, from simple flat shapes to complex geometries requiring multi-stage tooling processes. Precision in tool design is critical, as it directly affects the part's quality, production speed, and tool longevity.
The development of tooling is a high upfront cost but is justified by the efficiency and repeatability it brings to mass production. Regular maintenance and adjustments to the tooling are necessary to ensure consistent quality over thousands, or even millions, of parts.
Case Study: High-Efficiency Production of an Automotive Chassis Component
A notable example of the stamping process's efficiency and precision is producing an automotive chassis component, a critical part requiring high strength and tight tolerances. The manufacturing process was designed to produce 150 parts per hour, with each part meeting a tolerance of ±0.01 mm.
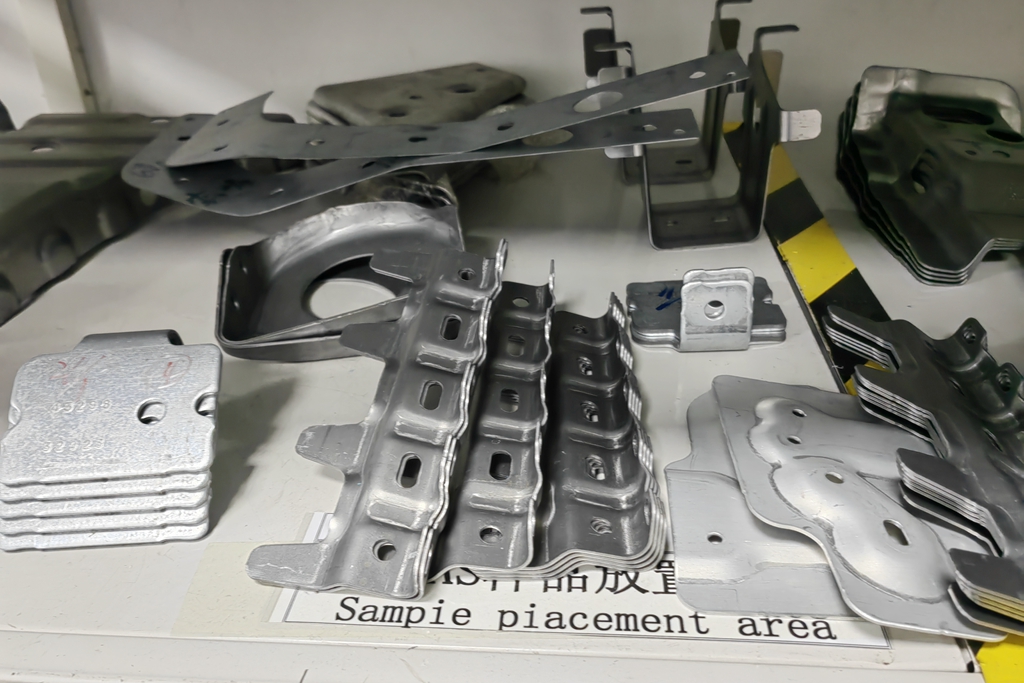
This efficiency level was achieved through advanced tool design, optimized material selection, and precise control of the stamping parameters. The tooling was engineered to minimize wear and tear, incorporating self-lubricating components and shock-absorbing mechanisms to extend its lifespan and reduce downtime.
The material selected for this component was a high-strength steel alloy, chosen for its excellent formability and durability under the stresses of vehicle operation. The stamping process was closely monitored using sensors and real-time data analysis to ensure each part remained within the specified tolerances. This resulted in a highly efficient production line with minimal waste.
The Art of Deep Drawing for Complex Auto Parts
Deep drawing is a specialized and intricate process in the fabrication of auto parts, particularly suited for producing complex, hollow shapes that require a depth greater than their diameter. This section explores the nuanced aspects of deep drawing, focusing on material stretchability, tool design, lubrication techniques, and a case study that underscores the process's productivity and quality control measures.
Understanding Material Stretchability and Tool Design
The success of deep drawing largely hinges on the material's ability to stretch without failing and the precision of tool design. Materials selected for deep drawing must possess high ductility and a balanced strength-to-elongation ratio, allowing them to be formed into deep, complex shapes without tearing or wrinkling. Commonly used materials include various grades of steel, aluminum, and stainless steel, each chosen based on the part's final application and required properties.
Tool design in deep drawing is sophisticated, requiring dies and punches that shape the metal and control its flow and distribution during the drawing process. Tools are often designed with features such as draw beads or pads to manage material flow and prevent defects like wrinkling or tearing. The clearance between the punch and die, along with the speed of the drawing process, is meticulously calibrated to ensure uniform material thickness and minimize stress concentrations.
Lubrication Techniques
Lubrication plays a pivotal role in the deep drawing process, reducing friction between the workpiece and the tools, which minimizes wear on the tools and prevents defects in the finished part. The choice of lubricant varies based on the material being drawn, the complexity of the part, and the drawing conditions. Synthetic lubricants, oils, and greases are commonly used with formulations tailored to specific applications and materials to optimize performance and part quality.
Case Study: Production of a Complex, Deep-Drawn Auto Part
A notable application of deep drawing in the automotive industry is the production of a fuel tank, a part that exemplifies the process's capability to produce complex, functional components. The project highlighted a productivity rate of 100 units daily, with each part subjected to rigorous quality control measures to ensure uniformity and integrity.
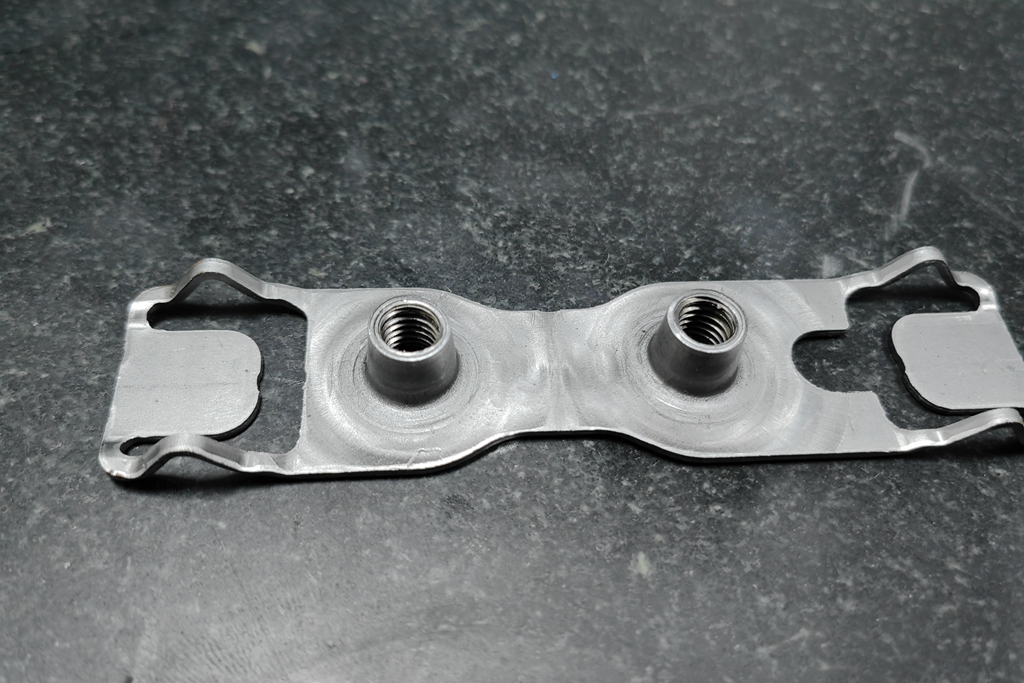
This level of productivity and quality was achieved through a combination of advanced material science, precise tooling, and optimized process parameters. The material chosen for the fuel tank was a high-grade aluminum alloy, selected for its excellent ductility and strength-to-weight ratio. The tooling was custom-designed to accommodate the part's complex shape, incorporating features to control material flow and prevent defects.
Quality control was integral to the process, involving dimensional inspections, material thickness measurements, and leak tests to ensure each fuel tank met strict safety and performance standards. The use of real-time monitoring systems and automated inspection techniques allowed for immediate identification and correction of any issues, maintaining high standards of quality and efficiency.
Stamping and Deep Drawn Challenges and Solutions
Manufacturing large auto parts through stamping and deep drawing processes involves a complex interplay of material properties, tool design, and precise control of manufacturing parameters. While efficient and capable of producing high-quality parts, these processes have challenges. This section outlines some common challenges encountered in stamping and deep drawing, along with the innovative solutions that industry professionals have developed to overcome them.
Stamping Challenges and Solutions
1. Material Wrinkling
Challenge: Material wrinkling can occur in stamping when uneven pressure is applied, especially in more significant parts with complex shapes.
Solution: Advanced simulation software is used to predict material behavior before production, allowing for the adjustment of press parameters. Employing blank holders with adjustable pressure can also help evenly distribute force, minimizing wrinkling.
2. Springback
Challenge: Springback is the material's tendency to revert partially to its original shape after being stamped, affecting dimensional accuracy.
Solution: Tooling adjustments based on predictive modeling can compensate for spring back. Using materials with lower elastic modulus or altering the material's microstructure through heat treatment may also mitigate this issue.
3. Tool Wear
Challenge: The repetitive nature of stamping, especially for large parts, accelerates tool wear, impacting product quality and increasing maintenance costs.
Solution: Wear-resistant tool materials, such as carbide or advanced coatings, extend tool life. Regular maintenance and inspection schedules ensure timely identification and replacement of worn components.
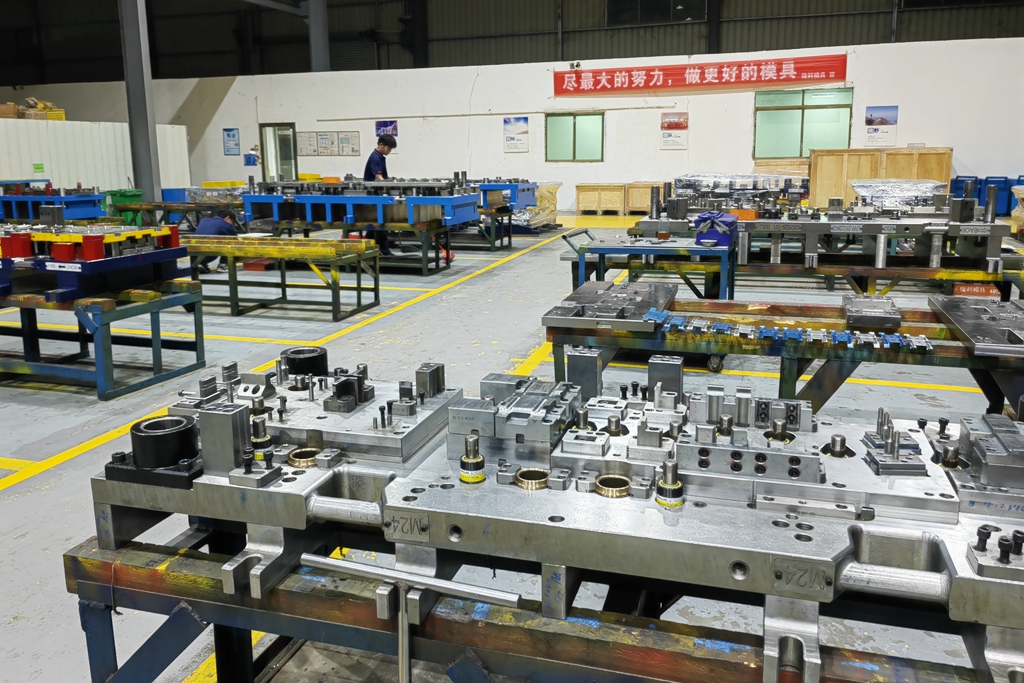
Profound Drawing Challenges and Solutions
1. Cracking and Tearing
Challenge: Excessive tensile stress during the deep drawing process can cause the material to crack or tear, especially at the component's base or walls.
Solution: Optimizing blank size and shape through trial and error or simulation reduces stress concentrations. Using materials with higher flexibility and adjusting the draw ratio are effective strategies.
2. Uneven Thickness Distribution
Challenge: Maintaining uniform material thickness in deep-drawn parts is challenging, especially for significant components with complex geometries.
Solution: Adjusting process parameters such as punch and die clearance and applying variable blank holder forces can help achieve a more uniform thickness. Material selection plays a crucial role, with some alloys offering better formability characteristics.
3. Wrinkling in Flange Areas
Challenge: Insufficient control over material flow can lead to wrinkling in the flange areas during deep drawing.
Solution: Fine-tuning the blank holder pressure ensures it's sufficient to prevent slippage but not so high as to hinder material flow. Employing numerical simulation to predict and counteract potential wrinkling zones before production is also effective.
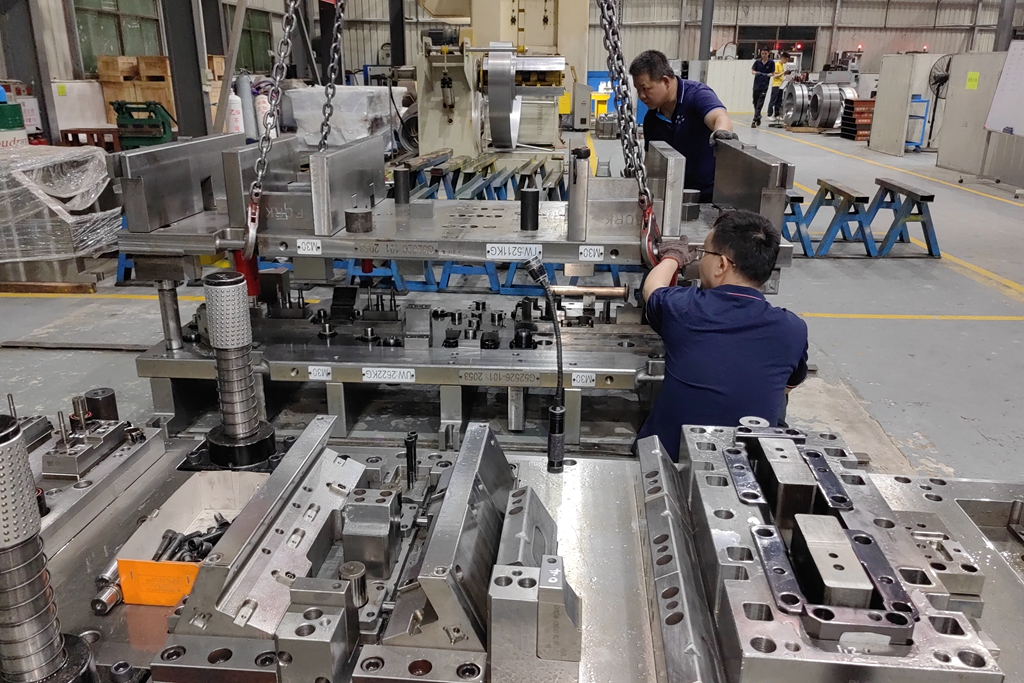
General Strategies for Enhancing Productivity and Quality
Across both stamping and deep drawing, several overarching strategies help manufacturers address these challenges:
Advanced Material Technologies: Investing in new materials with improved formability and strength can solve many issues inherent in these processes.
Automation and Robotics: Automation of material handling and part transfer processes reduces human error and increases production speed.
Quality Control Technologies: Implementing real-time monitoring systems and adopting Industry 4.0 technologies for predictive maintenance and process optimization ensures consistent product quality and reduces downtime.
By tackling these challenges with innovative solutions, manufacturers can maintain high levels of efficiency and quality in producing large auto parts. These efforts improve the reliability and performance of the parts and contribute to advancing manufacturing technologies in the automotive industry.
评论
发表评论