Understanding Fused Deposition Modeling (FDM)
In the dynamic world of manufacturing and prototyping, technologies that offer speed, efficiency, and flexibility are king. Fused Deposition Modeling (FDM) is a cornerstone in additive manufacturing. This innovative 3D printing technique has revolutionized how engineers, designers, and manufacturers approach the creation of parts, from simple models to complex, functional components.
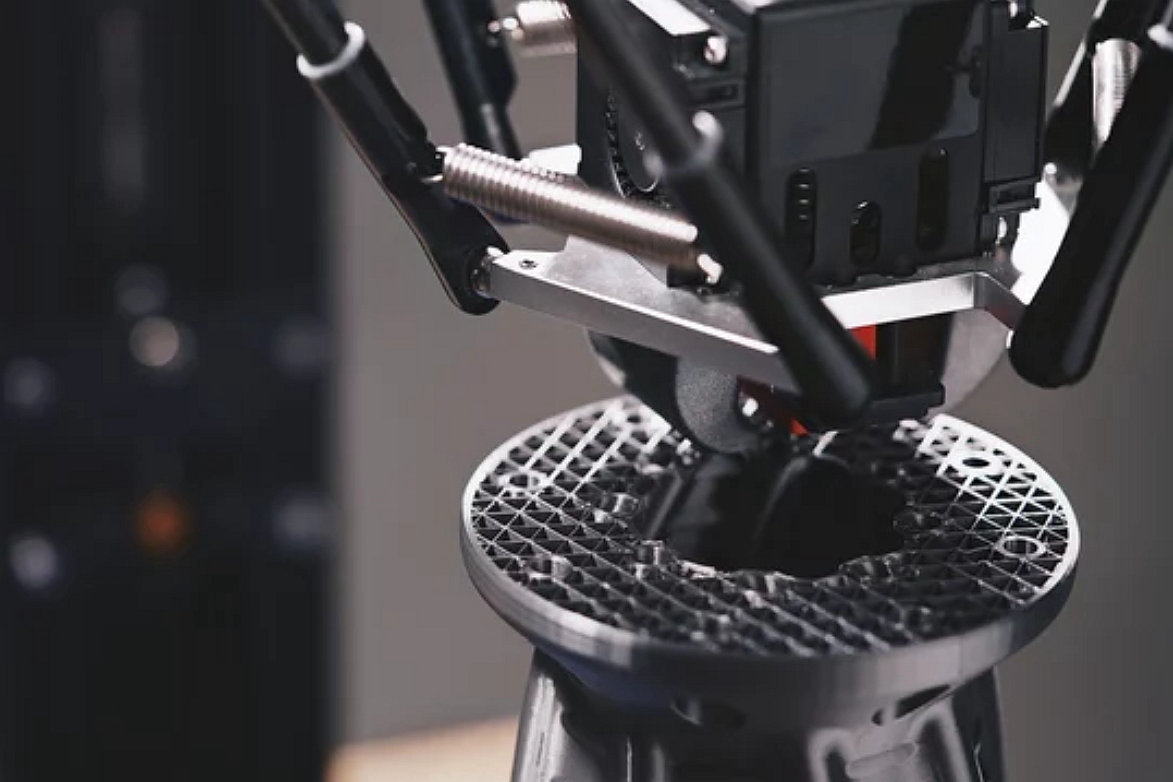
FDM works by extruding thermoplastic filaments through a heated nozzle, laying down material layer by layer to build objects from the bottom up. This process allows for rapid prototyping and supports the on-demand production of custom parts, making it an indispensable tool in various industries, including aerospace, automotive, medical devices, and consumer goods.
The versatility and accessibility of FDM have made it a popular choice for businesses and hobbyists alike, democratizing manufacturing in ways that were once thought impossible. As a pivotal technology within Neway's suite of manufacturing services, FDM plays a crucial role in enabling us to provide one-stop solutions for custom parts manufacturing, from initial concept to final product.
This blog will dive deep into Fused Deposition Modeling, exploring its workings, applications, benefits, and limitations. We'll also touch on how Neway leverages FDM technology to meet the evolving needs of our clients, showcasing our commitment to innovation and quality in every project we undertake. Whether you're a seasoned engineer or new to the world of 3D printing, join us as we uncover the intricacies and opportunities FDM offers.
The Basics of Fused Deposition Modeling
Fused Deposition Modeling (FDM) is a transformative additive manufacturing process that has reshaped the design, prototyping, and production landscape. FDM is elegantly simple yet profoundly powerful, offering a direct path from digital designs to tangible, functional parts. Here's what you need to know about the fundamentals of FDM:
Definition of FDM
FDM is a 3D printing technique that creates objects layer by layer. It uses thermoplastic polymers fed through a heated nozzle that melts and extrudes the material onto a build platform. As the material cools and solidifies, it fuses with the layer beneath, gradually building up the desired shape. This process is controlled by computer-aided design (CAD) software, ensuring precision and repeatability.
Historical Background and Development
Developed in the late 1980s, FDM technology was pioneered with the goal of rapid prototyping. Since its inception, FDM has undergone significant advancements, evolving from a niche prototyping tool to a mainstream manufacturing process. Today, FDM printers range from compact desktop models for hobbyists and small businesses to large-scale industrial machines capable of producing robust parts for critical applications.
Primary Components of an FDM Printer
Extrusion Head: The heart of the FDM printer, where the filament is heated and extruded. Precise temperature control is vital for achieving optimal print quality and material properties.
Filament: The raw material used in FDM printing. Common materials include Polycarbonate (PC), ABS (Acrylonitrile Butadiene Styrene), PETG (Polyethylene Terephthalate Glycol), and TPU (Thermoplastic Polyurethane), each offering unique properties that cater to different applications.
Build Platform: The surface upon which the object is printed. Some platforms are heated to prevent warping and improve adhesion between the layers.
At Neway, we understand that mastering these basics is the first step towards harnessing the full potential of FDM. Our expertise lies in operating machines and optimizing every aspect of the FDM process — from selecting the suitable material to fine-tuning print parameters. It ensures that every part we produce meets the highest quality, functionality, and aesthetic standards.
FDM's versatility and efficiency make it a preferred choice for rapid prototyping and on-demand production across various industries. Its ability to quickly turn ideas into tangible prototypes or end-use parts is invaluable in today's fast-paced manufacturing environment. As FDM technology continues to evolve, its role in driving innovation and reducing time-to-market for new products is set to grow even further.
How FDM 3D Printing Works
Understanding the mechanics of Fused Deposition Modeling (FDM) offers insight into its capabilities and versatility in producing custom parts and prototypes. The process, governed by meticulous control and advanced materials, unfolds through several key steps:
1. Design Preparation:
Every FDM project begins with a digital blueprint. Designers use computer-aided design (CAD) software to create detailed 3D models of the desired part. These models are then processed by slicing software, which converts the 3D design into a series of thin, horizontal layers. This data slice is essential for guiding the FDM printer through the build process.
2. Material Selection:
Choosing a suitable material is critical for the success of an FDM print. Materials such as PLA, ABS, and PETG are selected based on the part's intended use, required durability, and thermal properties. Neway's expertise in material science ensures that each project uses the most appropriate filament to meet the application's specific requirements.
3. Printing Process:
Heating: The selected filament is loaded into the FDM printer and heated to a precise temperature in the extrusion head. This temperature is carefully controlled to ensure the material flows smoothly and bonds effectively.
Layer-by-Layer Construction: The heated nozzle moves over the build platform, depositing the molten filament according to the slice data. After completing one layer, the build platform lowers slightly, and the next layer is applied directly on top of the previous one. This process repeats, with each layer fusing to the one below, until the part is fully formed.
Cooling and Solidification: As the material is deposited, it cools and solidifies rapidly, creating a strong bond between layers. Cooling must be managed carefully to prevent warping or deformities in the final part.
4. Post-Processing:
Once printing is complete, the part may undergo various post-processing steps to improve its appearance and properties. These can include support material removal, surface smoothing, and additional treatments to enhance strength or durability.
The layer-by-layer construction method central to FDM allows for complex geometries and intricate designs that, if possible, would be difficult to achieve with traditional manufacturing techniques. However, achieving the best results requires a nuanced understanding of material behavior, printer calibration, and design optimization.
At Neway, our proficiency in FDM extends beyond the technical operation of printers. We excel in optimizing the entire process, from initial design to final post-processing, to produce parts that meet our clients' exact specifications. Our engineers work closely with each project to ensure that every print maximizes the advantages of FDM, offering a blend of speed, efficiency, and quality that is unmatched.
FDM Applications and Industries
The versatility of Fused Deposition Modeling (FDM) technology has made it a pivotal tool in numerous fields, pushing the boundaries of design, prototyping, and manufacturing. Here, we explore the sectors that have embraced FDM, showcasing its wide-ranging impact and its unique benefits to each.
Aerospace
In the aerospace industry, FDM is valued for its ability to produce lightweight yet vital components. From cabin interiors to ductwork, FDM parts can withstand the rigors of flight while contributing to overall weight reduction, a critical factor in fuel efficiency and performance. Neway has collaborated on projects to develop specialized drone components and lightweight fixtures, demonstrating FDM's capability to meet stringent aerospace standards.
Automotive
The automotive sector utilizes FDM for both prototyping and end-use parts. The technology's rapid turnaround times accelerate the development cycle of new vehicles, allowing for faster testing and iteration. FDM's ability to produce durable, heat-resistant components makes it suitable for creating complex parts like ventilation systems and custom fittings for limited-edition models.
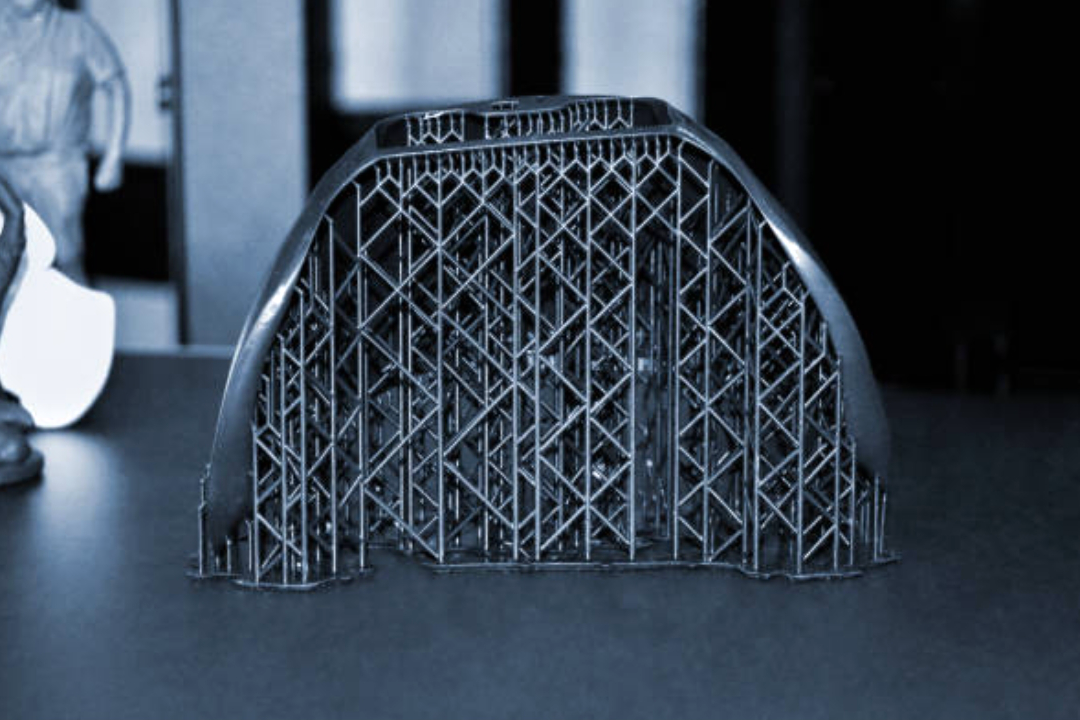
Medical Devices
In medical device manufacturing, FDM's precision and versatility support the creation of custom tools, prosthetics, and patient-specific models. These applications benefit from the ability to use biocompatible materials, ensuring safety and compatibility. Neway has produced surgical guides and prototypes for medical implants, underscoring the technology's role in advancing patient care.
Consumer Products
For consumer goods, FDM offers an unmatched ability to quickly bring new products to market. From ergonomic tools to wearable technology, FDM's flexibility in design and material choice enables brands to innovate freely, testing prototypes and final products quickly and cost-effectively. Neway's contributions to this sector highlight the role of technology in creating products that meet evolving consumer expectations.
Custom Manufacturing and Rapid Prototyping
The most significant impact of FDM is in custom parts manufacturing and rapid prototyping. The technology allows companies like Neway to offer tailored solutions to clients across industries, from initial concept models to functional prototypes and small-batch production runs. This capacity to iterate quickly and efficiently is invaluable in today's fast-paced market, where adaptability can define success.
The applications of FDM are as diverse as the industries it serves, with each sector leveraging the technology's strengths to solve unique challenges. Neway's deep understanding of FDM's capabilities and our commitment to quality and innovation positions us to help our clients explore new possibilities and achieve their goals.
As we continue to push the boundaries of what FDM can do, its role in shaping the future of manufacturing and product development is undeniable. Neway demonstrates FDM's potential with each project and reinforces our reputation as a leader in additive manufacturing solutions.
Advantages and Limitations of FDM
A blend of notable advantages and inherent limitations underpins FDM's transformative role in manufacturing. Understanding these can empower businesses to make informed decisions, ensuring that FDM is leveraged in ways that align with their needs.
Advantages of FDM
Cost-Effectiveness: FDM stands out for its economic efficiency. It significantly reduces the cost of prototyping and manufacturing by minimizing waste and eliminating the need for expensive tooling. For Neway's clients, this translates into lower development costs and the ability to iterate designs without prohibitive expenses.
Ease of Use: The straightforward operation of FDM machines, coupled with user-friendly software, makes this technology accessible to a wide range of users, from startups to established manufacturers. Neway capitalizes on this simplicity to quickly turn concepts into tangible prototypes, facilitating a dynamic development process.
Material Diversity: FDM's compatibility with various thermoplastics offers considerable prototype and part design flexibility. Materials range from standard plastics like PLA and ABS to advanced composites infused with metals or carbon fiber, enabling the creation of parts with specific properties such as enhanced strength, thermal resistance, or electrical conductivity.
Customization and Complexity: The layer-by-layer construction method of FDM allows for producing complex geometries that would be challenging or impossible to achieve through traditional manufacturing methods. This capability is pivotal for Neway, enabling the creation of customized parts tailored to the unique requirements of our clients.
Limitations of FDM
Surface Finish and Resolution: One of the primary limitations of FDM is the surface finish of printed parts. The layer-by-layer approach can result in visible layer lines, requiring post-processing for applications with a critical smooth surface. Additionally, the resolution of FDM may not match the precision achievable with technologies like SLA (Stereolithography) or SLS (Selective Laser Sintering), particularly for parts with intricate details.
Material Limitations: While FDM is compatible with a wide range of materials, the properties of these materials can be different from those of their traditionally manufactured counterparts. Factors such as temperature resistance, strength, and durability may vary, influencing the suitability of FDM parts for specific applications.
Structural Weaknesses: The nature of FDM means that parts can have anisotropic properties, with strength varying along different axes. This is due to the bonding between layers, which might be weaker than the material, potentially impacting the part's mechanical performance.
Despite these limitations, FDM's advantages often outweigh its drawbacks, especially in early-stage development, custom manufacturing, and applications where the benefits of rapid prototyping and on-demand production are paramount. At Neway, our expertise in FDM allows us to navigate these challenges effectively, optimizing designs and post-processing techniques to meet the high standards our clients expect.
Optimizing FDM for Quality and Efficiency
At Neway, our approach to FDM is not just about utilizing the technology; it's about perfecting it. By focusing on optimization strategies, we enhance the intrinsic value of FDM, producing parts that stand out for their precision, durability, and aesthetic appeal. Here's how we achieve this:
1. Optimizing Print Settings for Superior Quality
Layer Height and Print Speed: Fine-tuning the layer height and print speed can significantly impact the part's surface quality and structural integrity. Lower layer heights improve surface finish but increase print time. Balancing these factors is crucial in optimizing for both quality and efficiency.
Temperature Control: Precise control over the extrusion and bed temperature ensures consistent material properties throughout the print. It also minimizes warping and other defects affecting the part's final dimensions and appearance.
Infill Patterns and Density: Adjusting infill density and patterns based on the part's application balances strength and material usage. Strategic use of infill can reduce print time and material costs while maintaining part performance.
2. Selecting the Right Material
Different applications require different material properties. At Neway, we leverage our extensive knowledge of materials to select the best filament for each project, considering factors such as strength, flexibility, temperature resistance, and aesthetic qualities. It ensures the final part looks good and performs well under the intended use conditions.
3. Enhancing Productivity in FDM Processes
Batch Printing and Layout Optimization: By optimizing the layout of parts on the print bed, we can print multiple components simultaneously, maximizing the efficiency of each print run. This approach is particularly beneficial for small to medium-sized production runs, which can significantly reduce overall production time.
Automated Post-Processing: Where possible, we incorporate automated post-processing techniques to streamline the finishing of FDM parts. Techniques such as tumbling, sanding, and chemical smoothing can be semi-automated to reduce labor costs and improve consistency.
4. Future Developments in FDM Technology
Neway stays at the forefront of technological advancements in FDM, from exploring new materials with enhanced properties to integrating AI and machine learning for process optimization. These innovations promise to improve further the quality, efficiency, and range of applications for FDM manufacturing.
Optimizing FDM requires combining technical expertise, practical experience, and a commitment to continuous improvement. At Neway, we pride ourselves on pushing the boundaries of what's possible with FDM, crafting solutions that meet the exacting needs of our clients across industries.
FDM in the Context of Neway's Manufacturing Capabilities
At Neway, FDM is more than just a manufacturing process; it's a cornerstone of our innovative approach to custom parts production and rapid prototyping. Our deep understanding of FDM's nuances and commitment to quality and efficiency positions us as a leader in the additive manufacturing space. Here's how we leverage FDM to meet and exceed our client's expectations:
Customized Solutions: Neway specializes in tailoring FDM solutions to fit the unique requirements of our clients. From material selection to finishing techniques, we consider every aspect of the project to ensure optimal performance and aesthetics of the final part.
Case Studies of Success: Our portfolio includes a range of successful FDM projects across industries. For instance, we've facilitated rapid prototyping for automotive clients, reducing their development cycle by weeks. In the medical sector, we've produced custom surgical tools that combine precision with the necessary biocompatibility, showcasing FDM's versatility.
Innovation and Adaptability: We constantly explore new advancements in FDM technology — through materials with improved properties or process innovations like AI-driven optimization. It enhances our capabilities and ensures our clients benefit from the latest developments in additive manufacturing.
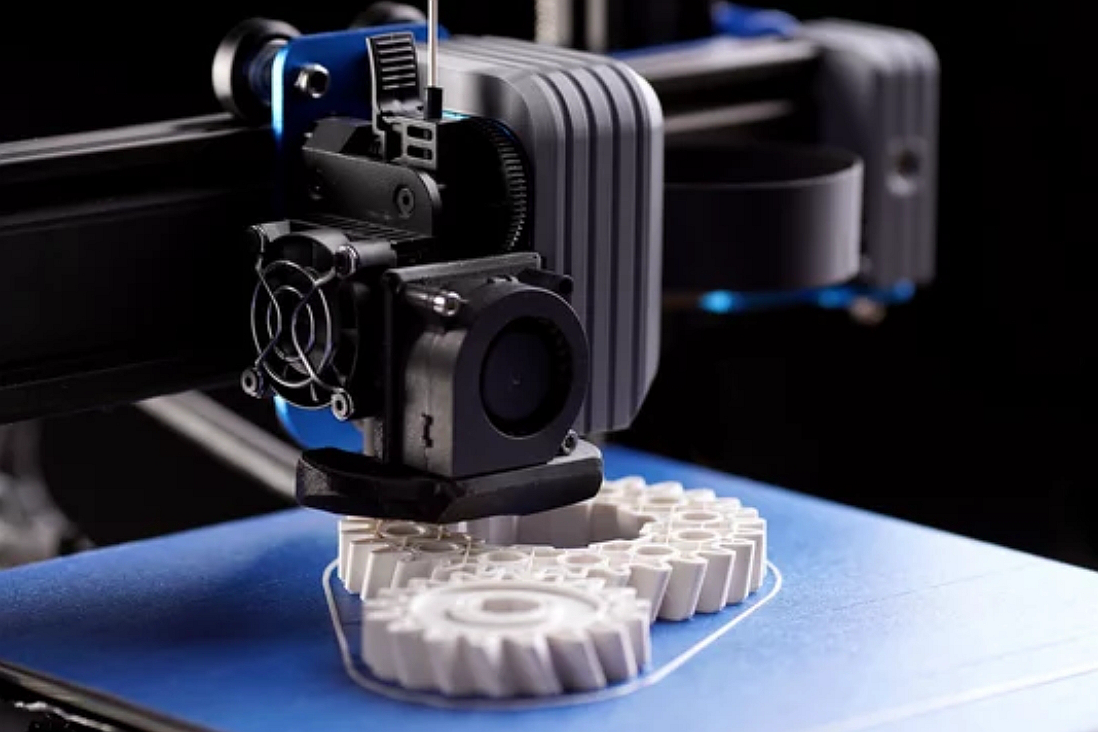
Conclusion
Fused Deposition Modeling (FDM) stands as a testament to the revolutionary impact of additive manufacturing on the modern industrial landscape. Its versatility, efficiency, and precision blend make it indispensable for rapid prototyping, custom part production, and beyond. As we've seen, the technology's applications span diverse industries, each leveraging FDM's strengths to innovate and solve unique challenges.
At Neway, our mastery of FDM technology and a holistic approach to manufacturing enables us to deliver solutions that truly make a difference. By staying at the forefront of technological advancements and optimizing our processes, we ensure that our clients always receive parts of the highest quality, tailored to their specific needs.
The future of FDM, filled with potential advancements in materials and processes, promises even greater possibilities for customization, efficiency, and sustainability in manufacturing. Neway remains committed to exploring these opportunities as we move forward, driven by our passion for excellence and innovation in manufacturing solutions.
What We Can Do In 3D Printing
Are you ready to explore the possibilities of FDM for your next project? Contact Neway today to learn how our expertise in additive manufacturing can bring your ideas to life with precision, efficiency, and unmatched quality. Let's shape the future of manufacturing together.
Visit our website or reach out directly to discuss your project needs and discover how Neway's FDM capabilities can provide your desired solutions.
评论
发表评论