Advanced Ceramics Injection Molding Services
Advanced ceramics, often called technical or engineering ceramics, are ceramic materials that exhibit exceptional properties beyond traditional ceramics. These ceramics are designed and engineered to meet specific performance requirements for various aerospace, electronics, automotive, medical, and CIM parts and other applications.
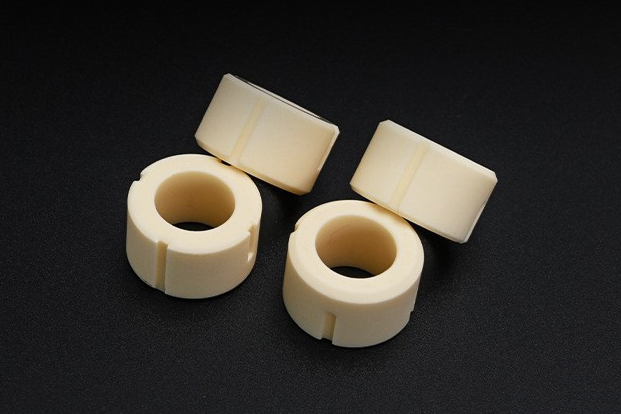
Advanced ceramics injection molding services combine the complexity of the plastic injection molding process and the excellent properties of advanced ceramics parts. Some examples of advanced ceramics include Alimina (Al2O3), Zirconia (ZrO2), Alumina-Zirconia, Silicon Carbide (SiC), Silicon Nitride (Si3N4), and more. These materials are used in diverse fields where their high-temperature stability, wear resistance, electrical insulation, and biocompatibility offer crucial advantages for cutting-edge technologies and innovative solutions.
What Are The Advanced Ceramics
Advanced or technical or engineering ceramics refer to a class of ceramic materials engineered to possess exceptional properties beyond traditional ceramics. These materials are tailored to meet specific performance demands in various industries owing to their superior mechanical, thermal, electrical, and chemical characteristics.
Unlike standard ceramics, advanced ceramics CIM parts are designed to excel in extreme conditions and specialized applications, making advanced ceramics CIM service invaluable for cutting-edge technologies and innovative solutions.
Properties of Each Advanced Ceramics:
1. Alumina (Al2O3)
Mechanical Strength: Alumina exhibits high compressive and flexural strength, making it suitable for structural components.
Thermal Conductivity: It has excellent thermal conductivity, ensuring effective heat dissipation.
Electrical Insulation: Alumina's electrical insulation properties are critical for electrical components and insulators.
Wear Resistance: Its hardness contributes to wear-resistant surfaces.
2. Zirconia (ZrO2)
Mechanical Toughness: Zirconia's transformation toughening enhances fracture toughness, which is crucial for high-stress applications.
Thermal Stability: It maintains stability at elevated temperatures, which is essential for high-temperature environments.
Wear Resistance: Zirconia's hardness and wear resistance makes it suitable for cutting tools and wear parts.
Biocompatibility: Certain zirconia forms are biocompatible, making them valuable for medical implants.
3. Silicon Carbide (SiC)
Hardness: SiC is one of the most rigid materials, offering excellent wear resistance.
Thermal Conductivity: Its high thermal conductivity aids heat dissipation, making it suitable for high-temperature applications.
Chemical Resistance: SiC's resistance to chemical corrosion makes it ideal for harsh environments.
Electrical Conductivity: It exhibits semiconducting properties, making it useful in electronics.
4. Silicon Nitride (Si3N4)
Thermal Shock Resistance: Silicon nitride's low thermal expansion coefficient enables it to withstand rapid temperature changes.
Mechanical Strength: It has high tensile and flexural strength, crucial for structural applications.
Wear Resistance: Silicon nitride's hardness and toughness contribute to its wear-resistant nature.
Biocompatibility: Some forms of silicon nitride are biocompatible, making it suitable for medical implants.
Applications of Advanced Ceramics CIM Parts
Advanced Ceramics Injection Molding Services find wide-ranging applications across industries thanks to their exceptional properties and versatile design capabilities. Here's a glimpse into the diverse applications where these services play a pivotal role:
1. Aerospace and Defense:
Advanced ceramics injection molding produces lightweight yet solid components for aerospace and defense applications. These components include turbine blades, nozzles, and radar equipment. Advanced ceramics' high-temperature stability and durability make them ideal for these demanding environments.
2. Electronics and Semiconductors:
In the electronics industry, advanced ceramics produce insulating components, substrates, and semiconductor packages. The excellent electrical insulation and thermal conductivity properties of ceramics enhance the performance and longevity of electronic devices.
3. Automotive:
Advanced ceramics injection molding creates components for automotive engines, such as sensors, spark plugs, and exhaust system parts. The wear resistance and thermal stability of ceramics ensure reliability in high-temperature engine environments.
4. Healthcare and Medical Devices:
Ceramics are vital in medical applications due to their biocompatibility and resistance to corrosion. Injection molding produces components like dental implants, joint replacements, and surgical tools, contributing to improved patient outcomes.
5. Industrial Machinery and Equipment:
Ceramics are used for manufacturing wear-resistant components in industrial machinery and equipment. Examples include ceramic bearings, cutting tools, and valves that withstand harsh conditions and reduce maintenance needs.
6. Energy Generation and Storage:
Ceramics find applications in energy generation through components like gas turbine blades and heat exchangers. They also play a role in energy storage, with ceramic components used in batteries and fuel cells.
7. Consumer Electronics:
Components such as insulators, connectors, and sensors in consumer electronics benefit from ceramics' precision and electrical properties. These materials contribute to the reliability and functionality of devices.
8. Chemical Processing:
In corrosive chemical environments, ceramics create resistant components like valves, pipes, and liners. Their chemical stability prevents material degradation and extends equipment lifespan.
9. Optoelectronics and Photonics:
Ceramics enable the production of optoelectronic components like laser gain media, lenses, and optical fibers. Their transparency to specific wavelengths and resistance to thermal effects are crucial for photonics applications.
10. Renewable Energy:
Ceramics are used in solar cells, wind turbines, and fuel cells to create components that withstand extreme temperatures and harsh environments, enhancing the efficiency and durability of renewable energy systems.
11. Telecommunications:
Components like ceramic antennas and substrates are used in telecommunications equipment due to their electrical properties and ability to transmit signals without interference.
Why Choose Neway For CIM Service
About Neway: Neway has provided exceptional ceramic injection molding services for 30 years. Their CIM capabilities deliver high-performance ceramic components with tight tolerances and complex geometries. Neway's decades of experience and stellar reputation make them the right choice for your next CIM project.
Customer Evaluation: After using Neway's ceramic injection molding services, I can't recommend them enough. The quality of their CIM parts is unparalleled, and their 30 years of experience shows through in their technical expertise and customer service. If you're looking for a proven CIM partner, choose Neway.
Real Case: When Volkswagen needed ceramic turbine blades molded, they turned to Neway's ceramic injection molding. Neway engineered a ZrO2 material formulation and CIM process that produced ceramic blades with the strength and heat resistance Acme's jet engines demanded. The project was a resounding success, proving Neway's expertise in ceramic injection molding.
评论
发表评论