The plasma cutting process is a sheet metal fabrication process. It has become one of the most popular and widely used thermal cutting processes in industrial fabrication and manufacturing. Its ability to cut through all conductive metals with precision and speed makes it a versatile choice for many applications. However, like any process, plasma cutting has advantages and limitations.
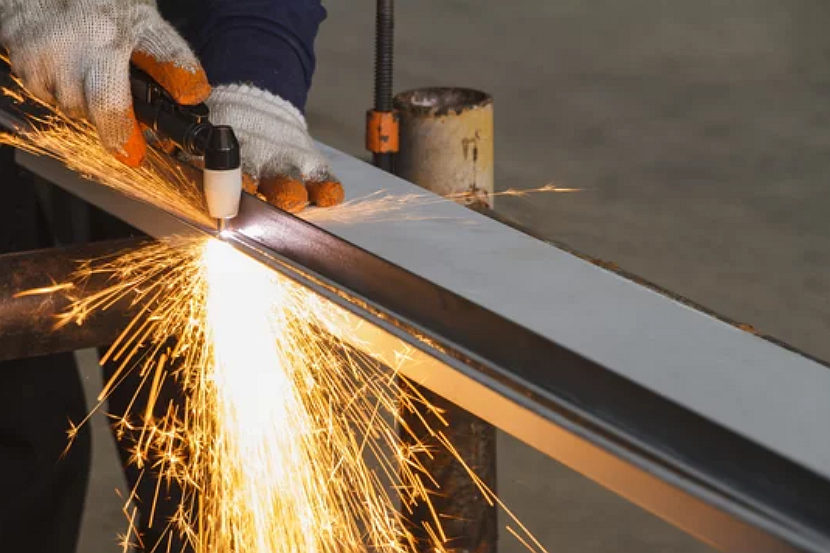
Pros of Plasma Cutting
Cutting Speed
One of the most significant advantages of the plasma cutting process is its very high cutting speed capability. Plasma systems can make straight cuts at over 100 inches per minute on thin gauge metal less than 1/4" thickness. This is around 2-3 times faster than processes like oxyfuel or laser cutting. The high speed is achieved because the plasma jet melts a very narrow kerf width of only 1/16" to 1/8".
Plasma still maintains faster cutting speeds on thicker steel plates than other methods. Cut speeds will reach 30-40 pm on 1" mild steel with high amperage plasma cutters. This productivity makes plasma ideal for high-volume fabrication shops and cutting of thicker material.
Cutting Quality
Plasma cutting produces immaculate and precise cut edges with a smooth surface that requires minimal secondary finishing. The smaller heat-affected zone and oxidation from the plasma arc produce a square, dense kerf with minimal dross adhesion. It is an advantage over other thermal cutting methods.
The constricted plasma arc column forced through the torch nozzle makes excellent cut quality possible. It focuses the heat into an intense jet that melts the metal cleanly. Precision cut parts and shapes can be achieved with minimal post-processing cleanup.
Cut Thickness Capabilities
Plasma cutting service provides thicker metal cutting capability unmatched by other methods besides oxyfuel. High amperage plasma cutters in the 80-200 amp range can reliably cut mild steel from 1/4" up to 2" thick in a single pass. With multiple passes and edge beveling, thicknesses over 6" can be achieved.
The concentrated plasma arc allows the heat to penetrate thicker material and make reliable complete cut severance. Operators do not have to worry about metal thickness limitations affecting laser or waterjet cutting processes.
Low-Cost Process
The overall operating costs of plasma cutting are relatively affordable compared to other cutting methods. The main consumable is compressed air or nitrogen gas, along with periodic replacement of torch parts like electrodes and nozzles. However, expenses are still far lower than laser gas consumption or abrasive costs with waterjet.
The equipment costs for plasma systems are also on the lower end of the spectrum for industrial cutting machinery. Even high-output automated plasma tables are reasonably priced compared to lasers or waterjets with similar cutting power. The technology's cost-effectiveness makes it accessible to most fabrication shops.
Cutting Versatility
Plasma cutters can sever all electrically conductive metals, from mild and stainless steel to aluminum, brass, and copper alloys. Painted or rusted metals and those with some surface contaminants can also be cut effectively. This versatility supports a wide variety of fabrication and repair applications.
The plasma arc concentrates into a tight column, allowing for cutting small and intricate patterns or doing jobs involving hole piercing or metal engraving. Precision parts with detailed contours and tolerance-critical specifications are achievable.
Limited Heat-Affected Zone
The plasma jet focuses heat into a narrow zone on the material surface. It means only a tiny heat-affected zone on either side of the cut line. The concentrated plasma column minimizes the warping and metal degradation you would get with processes like oxyfuel or abrasive cutting.
Parts have less thermal damage and distortion, reducing the secondary machining or grinding needed later. Welding near the cut zone is easier since the material properties remain unchanged outside the kerf line—overall, less wasted material and labor.
Portability & Construction
Compared with alternatives like lasers or waterjet cutters, plasma systems are lightweight and compact. Handheld torches allow the operator to bring the cutter to the workpiece rather than vice versa. Fieldwork is flexible, confined spaces or outdoor cutting applications.
The consumable torch parts and overall rugged design of plasma cutters also make them well-suited for construction sites and heavy fabrication cutting work. They can withstand conditions with more dirt, vibration, weather effects, and rough handling compared to other precision cutting tools.
Cons of Plasma Cutting
Limitations on Highly Reflective Metals
The plasma arc depends on electrical conductivity to cut material. However, metals like aluminum, brass, and copper have a highly reflective surface, making maintaining good contact between the plasma arc and the workpiece challenging. The arc tends to "bounce" rather than penetrate the material. It can result in an inconsistent cut.
Special plasma-cutting procedures have been developed for these metals but typically involve lower cut speeds. Results still may need to match the ease of cutting mild steel. Laser cutting is preferred for the best performance on aluminum and copper alloys.
Cutting Thinness Limitations
While plasma can cut thick material, it does have limitations when cutting fragile metals below 1/8" thickness. The high plasma gas pressure and arc force blow away these thin materials. Precision cutting also becomes difficult on thin gauge material.
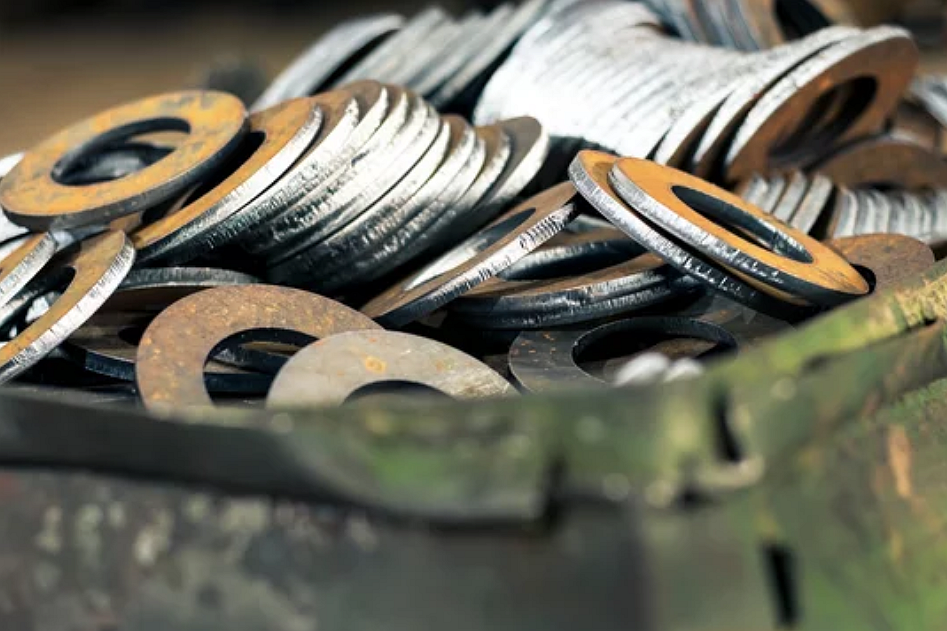
Alternative processes like laser or waterjet cutting are better for thin sheet metals. Plasma cutting should be limited to 1/8" thickness and above for best results.
Surface Coating Removal
Before plasma cutting can start, paint, powder coating, epoxy, and other material surface finishes have to be removed from the area to be cut. These coatings insulate the metal from good electrical contact with the plasma arc. A 6-8" strip must be cleaned to bare metal along the cut path.
Surface coatings also introduce contamination into the kerf that reduces cut quality. The secondary cleanup adds time and cost compared with cutting bare metal.
Cut Tolerance Capabilities
While plasma cuts are exact for many applications, the process cannot match the tolerance capabilities of laser or waterjet cutting. Those processes offer narrower kerfs and more consistent cut geometry. Plasma usually holds tolerances of +/- 0.005" to 0.020" depending on material thickness.
For extreme precision parts that require cutting tolerances within +/- 0.005" and minimal heat-affected zone, plasma is not the ideal choice. The slight but noticeable kerf taper and heat effects limit how tight tolerances can realistically be held.
Slower Cut Speed on Thick Material
As mentioned earlier, plasma cutting achieves very high speeds on thin gauge metals. But when cutting plate steel over 1" thickness, the cut speed drops considerably, down to 10-30 inches per minute depending on cut thickness and amperage.
While these thick metal cut speeds are still faster than alternatives, it does mean lower plasma productivity for heavy fabrication jobs involving plate steel. It can be a limitation for shops that work with substantial thicknesses.
Cut Taper
All thermal cutting processes introduce some degree of kerf taper, where the entry cut width is slightly narrower than the exit width. It is caused by drag from the walls of the material closing in on the cut as it penetrates deeper. Plasma cutting results in a taper of 1-3 degrees typically.
While not a significant drawback for many applications, the cut taper does introduce some dimensional variance from top to bottom. Precision cuts may require compensation of programmed dimensions. The kerf taper is more pronounced on thicker materials.
Fixturing Requirements
The workpiece must be firmly clamped or fixtured to maximize plasma cutting's high speeds and quality. Any vibration or workpiece movement during cutting will introduce dimensional errors and rounded cut lines. Removing the backing plate also becomes difficult.
Proper fixturing requires additional setup time and costs. Water table systems that submerge and support the metal are ideal but involve a significant investment. Fixturing is less critical for other cutting methods like handheld oxyfuel.
Cut Path Deviations
Like the taper effect, plasma cutting can introduce slight arc wander and path deviations as the cut penetrates deeper into the material. It can cause the exit cut location to be off-target by more than the kerf width. Precision cutting depends on maintaining exact cut path geometry.
Any instabilities in the plasma arc or workpiece vibrations will be exaggerated through the entire thickness. While automated CNC controls compensate for much of this deviation, it can still affect cut precision.
Nozzle & Electrode Replacement
The torch nozzle and interior electrode are regular consumable parts that wear during use. Nozzle orifices will deteriorate from the hot plasma jet passing through them over time. Electrodes slowly erode from the arcing to generate the plasma.
These parts must be replaced after a certain number of arcs start and cut minutes. Nozzles may need replacing as often as once a day on heavy-use machines. It contributes significantly to total plasma operating costs.
Noise Production
The plasma cutting arc creates a high noise level averaging around 85-95 decibels near the cut zone. It exceeds the OSHA standard 85 dB limit for extended exposure. Proper ear and hearing protection is mandatory for the plasma system operator and anyone nearby.
The need for hearing protection equipment and potential worker safety hazards from the noise levels must be considered. Noise can also be a distraction in shops where multiple operations occur.
Fume & Dust Production
The plasma cutting arc interacting with metal vaporizes base material and heats air, creating an oxide layer. It produces significant volumes of dust and fumes that must be captured and filtered by exhaust ventilation systems. The dust contains toxic metals like chromium, nickel, and manganese, posing health risks.
Installing industrial fume extraction, designing proper enclosure hoods, and purchasing filtration systems are expensive. Poor fume capture allows the dust to spread in the work environment. Proper ventilation planning is essential with plasma use.
High Amperage Power Demands
Plasma cutting requires power sources delivering very high amperages, from around 30 amps on handheld torches and up to 300 amps on CNC cutting tables. This sustained power draw requires a capable incoming electrical supply, upgraded shop wiring, special high amp plugs, and surge protection.
Providing the necessary electrical infrastructure is a cost factor for facilities installing plasma systems. Fortunately, the power supplies convert incoming AC to DC internally, so no 3-phase input is needed. But amperage capacity on lines must be ensured.
Plasma cutting offers excellent cut quality and high speeds unmatched by other metal cutting methods. It is a cost-effective and versatile fabrication process. However, limitations with highly reflective metals, precision tolerances, noise, and fumes must be weighed when considering a plasma investment. For many shops, the productivity benefits outweigh the drawbacks of plasma cutters.
评论
发表评论