CNC Machining Overview
CNC machining, also known as computer numerical control machining, is a manufacturing process that utilizes automated machines to remove material from a workpiece, creating precise and intricate parts. This process offers numerous advantages, including high accuracy, repeatability, and versatility. CNC machining eliminates the need for manual operation, reducing human error and increasing efficiency.
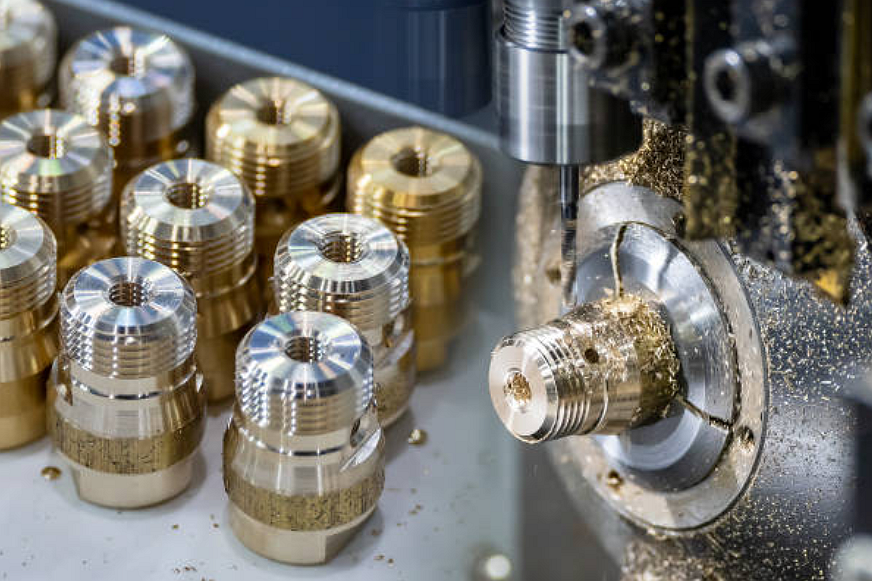
One popular type of CNC machining is lathe machining, which involves rotating the workpiece while a cutting tool removes material to create the desired shape. CNC lathe machining offers exceptional precision and allows for producing cylindrical or rotational parts with complex features.
Another commonly used technique is CNC machine milling, where a rotating cutting tool removes material from a stationary workpiece. This method is ideal for creating parts with intricate shapes, including slots, holes, and pockets. CNC machining combines the benefits of lathe machining and milling, offering a comprehensive solution for diverse manufacturing needs.
While CNC machining has numerous advantages, it also has some limitations. The initial setup and programming can be time-consuming, particularly for complex parts. Additionally, the cost of CNC machines and maintenance can be high, making it more suitable for large-scale production or specialized applications.
CNC Machining History
The history of CNC machining dates back to the mid-20th century when the need for automated manufacturing processes arose. The first numerically controlled machine tools were developed in the 1940s and 1950s, primarily for military and aerospace applications. These early systems utilized punched cards or magnetic tapes to control the machine's movements.
Over the years, advancements in computer technology led to the development of more sophisticated CNC systems. The introduction of computer-aided design (CAD) and computer-aided manufacturing (CAM) software further revolutionized CNC machining by enabling more precise and complex part designs.
CNC Machining Definition and Classification
What is CNC Machining?
CNC machining is a manufacturing process that utilizes computer-controlled machines to remove material from a workpiece and create precise parts. It involves the use of programmed instructions to control the movements of cutting tools, allowing for accurate and repeatable operations.
CNC machining encompasses various techniques, including lathe machining and machine milling, which offer different capabilities and applications. These techniques utilize different CNC machines, such as CNC lathes and milling machines, to achieve specific machining operations.
CNC Machining Classification
CNC machining can be classified into different categories based on the scope of application and complexity of the parts produced. The most common classifications include:
- CNC Lathe Machining: This technique rotates the workpiece while a cutting tool removes material, resulting in cylindrical or rotational parts. CNC lathe machining is suitable for producing parts like shafts, bushings, and threaded components.
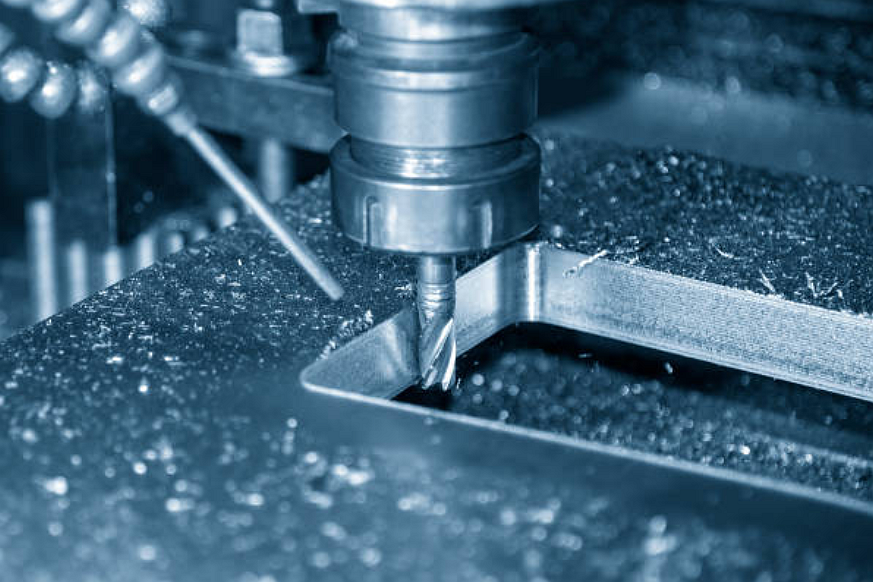
- CNC Milling Machining: A rotating cutting tool removes material from a stationary workpiece to create various shapes and features. CNC milling machining is ideal for producing parts with complex geometries, such as brackets, housings, and molds. Such as 3-axis CNC machining, 5-axis CNC machining.
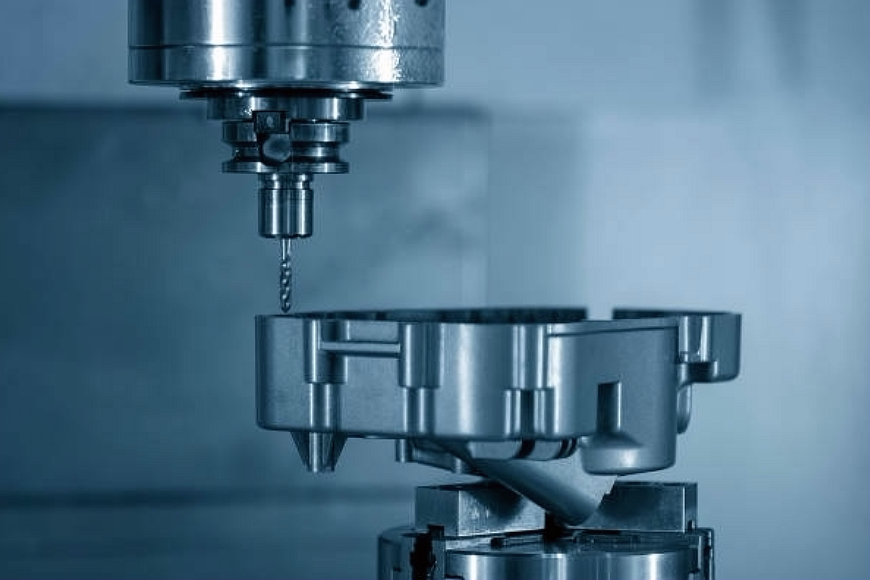
- CNC Turning: This technique focuses specifically on turning operations, where the workpiece rotates while the cutting tool shapes the outer diameter of the part. CNC turning is commonly used for creating cylindrical or conical parts, such as shafts, pulleys, and flanges.
- CNC Mill-Turn: This classification combines a single machine's lathe machining and milling operations. It allows for producing complex parts with rotational and prismatic features, reducing the need for multiple setups.
Each classification offers distinct advantages and is chosen based on the specific requirements of the part and the desired manufacturing process.
CNC Machining Operation Steps
CNC Machining Operation Step-by-Step
CNC machining involves several key steps to transform a digital design into a physical part. The step-by-step process typically includes:
1. Designing the part: Using computer-aided design (CAD) software, create a 3D model of the desired part. Specify dimensions, features, and tolerances.
The initial design determines the part's form, features, and functionality. Careful consideration of design specifications and manufacturability helps optimize the subsequent machining process.
2. Creating the CNC program: Convert the 3D model into a machine-readable format using computer-aided manufacturing (CAM) software. The program contains tool movements, feed rates, and cutting parameters instructions.
The CNC program serves as instructions that guide the machine's movements and cutting operations. It translates the design into a language the machine understands, enabling precise and consistent machining.
3. Material selection and preparation: Choose the appropriate material for the part based on its mechanical properties and intended application. Ensure the material is properly secured and aligned in the CNC machine.
Choosing the appropriate material is essential for achieving the desired part properties and performance. Proper material preparation, such as securing and aligning, ensures stable machining conditions and accurate results.
4. Machine setup: Install the cutting tools, tool holders, and work-holding fixtures in the CNC machine. Calibrate the machine and perform any necessary tool offsets.
The setup phase involves installing the necessary tools and fixtures and calibrating the machine. Accurate machine setup ensures proper tool alignment, minimizes errors, and ensures dimensional accuracy.
Transferring the CNC program to the machine allows for the execution of the machining instructions. Verifying the program before execution helps identify any potential errors or issues.
5. Loading the program: Transfer the CNC program to the machine's control unit. Verify the program and make any necessary adjustments or corrections.
Transferring the CNC program to the machine allows for the execution of the machining instructions. Verifying the program before execution helps identify any potential errors or issues.
6. Workpiece alignment: Align the workpiece with the machine's coordinate system to ensure accurate machining. This involves setting the origin point and establishing the X, Y, and Z axes.
Aligning the workpiece with the machine's coordinate system establishes the reference point for machining operations. Precise alignment is crucial for maintaining dimensional accuracy throughout the process.
7. Machining operations: Initiate the CNC program to begin machining. The machine follows the programmed instructions, executing cutting, drilling, and milling operations to shape the part.
The CNC machine executes the programmed instructions to remove material and shape the part. Each machining operation, cutting, drilling, or milling, contributes to creating the desired part geometry.
8. In-process monitoring: Continuously monitor the machining process to ensure the part is accurately and efficiently produced. Make adjustments as needed.
Continuous machining process monitoring allows for real-time adjustments and corrections, ensuring consistent quality and preventing errors or deviations.
9. Finishing operations: Once the primary machining is complete, perform secondary operations such as deburring, chamfering, or surface finishing to achieve the desired part specifications.
Secondary operations like deburring or surface finishing help refine the part's appearance and functionality. These operations remove sharp edges, improve surface quality, and prepare the part for its intended use.
10. Inspection and quality control: Inspect the finished part using precision measurement tools to verify its dimensional accuracy and quality. Make any necessary adjustments or corrections.
Inspecting the finished part verifies its dimensional accuracy and quality. Precision measurement tools, such as calipers or coordinate measuring machines (CMMs), ensure compliance with design specifications.
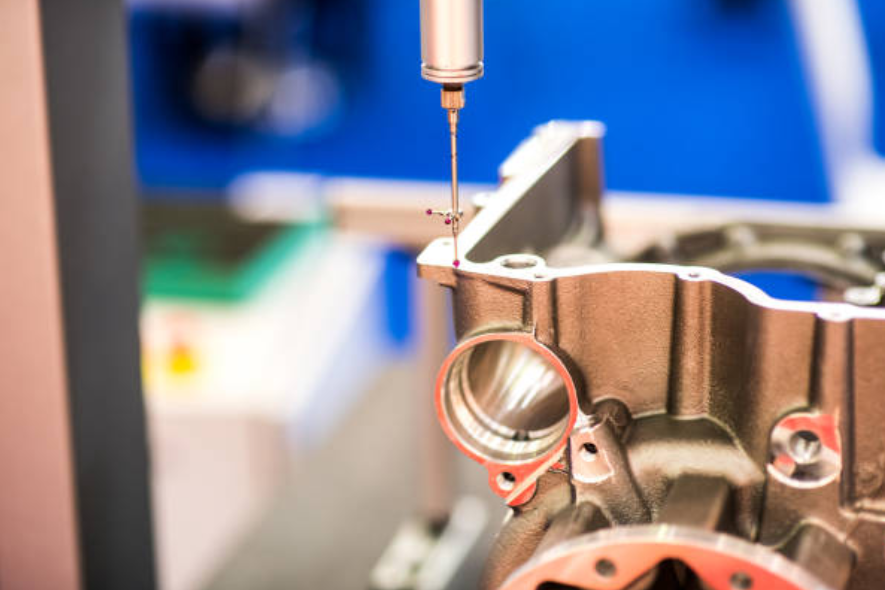
11. Part removal and cleaning: Remove the finished part from the CNC machine. Clean the part to remove any cutting fluids, chips, or debris.
Safely removing the finished part from the machine and thoroughly cleaning it ensures it is ready for use or additional post-processing steps.
Common CNC Machining Materials
Material Classification
CNC machining materials can be classified based on their mechanical, physical, and chemical properties. Understanding the different material classifications helps select the most suitable material for specific applications. The following are the standard material classifications used in CNC machining:
Metals
Metals are widely used in CNC machining for their excellent strength, durability, and thermal conductivity. Common metal materials include aluminum alloys, stainless steel, brass, copper, and titanium. Each metal has distinct properties that make it suitable for various applications.
Plastics
Plastics offer versatility, low density, and excellent electrical insulation properties. CNC machining can effectively shape plastic materials such as ABS, polycarbonate, acrylic, nylon, and polypropylene. Plastics are widely used in the automotive, electronics, and consumer goods industries.
Composites
Composites are materials composed of two or more constituent materials with distinct properties. The combination of materials enhances the overall performance and allows for customized material properties. Carbon fiber composites, fiberglass composites, and reinforced plastics are common examples used in CNC machining.
Ceramics
Ceramics exhibit high-temperature resistance, chemical inertness, and electrical insulation properties. Advanced ceramics like alumina, zirconia, and silicon nitride are used in CNC machining for applications requiring exceptional hardness, wear resistance, or thermal stability.
Other materials
Other materials, such as wood, foam, and certain types of rubber, can also be machined using CNC techniques. These materials have applications in furniture manufacturing, prototyping, and signage.
Material Selection Factors
How select a material for CNC machining, several factors should be considered:
1. Mechanical properties: Evaluate the material's strength, hardness, elasticity, and toughness to ensure it meets the part's functional requirements. Consider factors such as load-bearing capacity, wear resistance, and impact resistance.
2. Machinability: Assess the material's ease of machining, including cutting forces, chip formation, and tool wear. Materials with good machinability result in efficient machining processes and extended tool life.
3. Thermal properties: Consider the material's thermal conductivity and coefficient of expansion. These properties affect heat dissipation, thermal stability, and dimensional stability during machining.
4. Chemical resistance: Determine the material's resistance to corrosion, chemical degradation, or exposure to specific environments. This is crucial for applications in industries like aerospace, automotive, or chemical processing.
5. Cost considerations: Evaluate the material's cost per unit and availability. Some materials may be more cost-effective for specific applications, while others may offer unique properties that justify higher costs.
6. Regulatory requirements: In certain industries, compliance with regulations and standards is essential. Ensure that the selected material meets any specific regulatory or certification requirements.
By considering these factors, designers and manufacturers can select the most appropriate material for CNC machining, ensuring optimal part performance and functionality.
Advantages and Applications of CNC Machining
Advantages of CNC Machining
CNC machining offers numerous advantages over conventional machining methods:
1. High accuracy and precision: CNC machines can consistently achieve extremely tight tolerances and produce highly accurate parts. The use of computer-controlled movements eliminates the errors associated with manual operation.
2. Increased production efficiency: CNC machining allows for the automation of machining processes, resulting in faster production rates and reduced cycle times. Multiple axes of movement enable simultaneous machining operations, increasing productivity.
3. Versatility and flexibility: CNC machines can perform various machining operations, including turning, milling, drilling, and threading. They can accommodate complex part geometries and easily switch between different setups.
4. Repetitive and consistent results: CNC machines can reproduce identical parts consistently, eliminating variations caused by human error. This is especially beneficial for mass production or applications requiring high uniformity.
5. Design freedom and complexity: CNC machining produces intricate and complex part designs that may be challenging or impossible with traditional methods. CAD/CAM integration allows for the direct translation of digital designs into physical parts.
6. Cost-effective for large production runs: Once the CNC program is developed and optimized, CNC machining becomes cost-effective for large-scale production. The high level of automation reduces labor costs and improves overall production efficiency.
Applications of CNC Machining
CNC machining finds extensive applications across various industries, including:
1. Aerospace and defense: CNC machining manufactures critical components for aircraft, satellites, missiles, and defense equipment. It produces parts with high precision, dimensional accuracy, and strict adherence to aerospace standards.
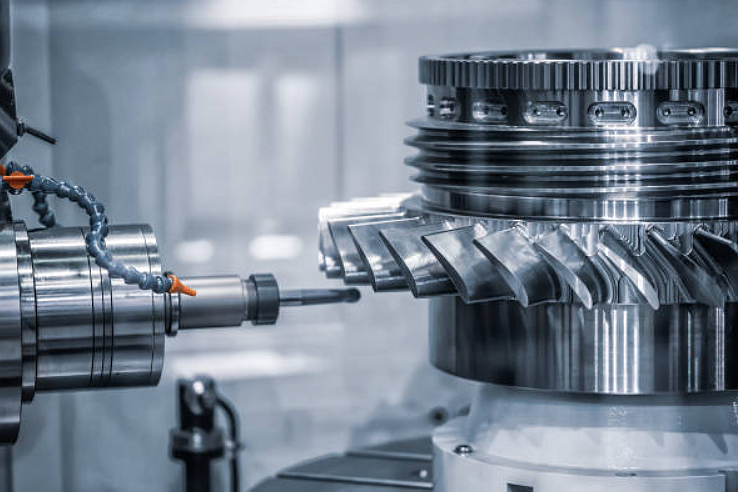
2. Automotive: CNC machining is used
to produce engine components, transmission parts, chassis components, and interior or exterior trim parts. It enables the production of complex shapes, tight tolerances, and consistent quality.
3. Medical and healthcare: CNC machining produces surgical instruments, orthopedic implants, prosthetics, dental components, and medical device parts. It offers the precision and quality required for medical applications.
4. Electronics: CNC machining produces printed circuit boards (PCBs), electrical connectors, enclosures, and heat sinks. It enables the creation of intricate designs and precise features required for electronic components.
5. Energy and power generation: CNC machining involves manufacturing parts for turbines, generators, pumps, and valves used in power generation plants. It ensures the accuracy and performance of components operating in demanding environments.
6. Industrial equipment: CNC machining produces machinery, heavy equipment parts, and tooling components. It enables the creation of custom parts with tight tolerances and complex geometries.
7. Consumer goods: CNC machining manufactures various consumer products, including appliances, furniture, sporting goods, and luxury items. It offers the ability to create aesthetically pleasing designs and functional components.
Defects and Prevention
Common Defects of CNC Machining
Common defects in CNC Machining include dimensional inaccuracies, surface imperfections, burrs, tool marks, and material deformation. These issues can arise due to improper tooling, inadequate machine calibration, incorrect machining parameters, or material inconsistencies.
Prevention Methods of CNC Machining Defects
Prevention of CNC Machining defects involves implementing measures like proper tool selection and maintenance, accurate machine calibration, optimized machining parameters, effective quality control, and thorough inspection techniques. Attention to detail and continuous process improvement help minimize defects and ensure high-quality part production.
Post-processing and Surface Treatment Properties
Common Post-processing
Post-processing methods in CNC Machining include deburring, polishing, sanding, painting, anodizing, plating, and more. These techniques enhance part aesthetics, improve surface finishes, and provide additional functionalities like corrosion resistance or electrical conductivity.
Common Surface Treatment of CNC Machined Parts
Surface treatment processes for CNC Machining parts include anodizing, electroplating, powder coating, passivation, and various coating methods. These treatments enhance part durability, aesthetics, and functionality, catering to specific application requirements.
Process Comparison
CNC Machining stands out among similar processes like 3D printing, injection molding, and traditional machining methods. While each process has its strengths and limitations, CNC Machining offers the advantage of high precision, versatility in material selection, and the ability to produce complex parts efficiently.
CNC Machining Case Study
Neway is a renowned CNC Machining company with a strong track record in delivering high-quality parts for various industries. Our expertise, state-of-the-art facilities, and commitment to customer satisfaction make us a reliable partner for CNC Machining projects. Check out our case studies to see our successful collaborations and outstanding results.
What is the Cost of CNC Machining
Cost Composition
The cost of CNC Machining comprises several factors: material costs, tooling expenses, machine setup, labor, post-processing, quality control, and overhead expenses. Each component contributes to the overall cost of producing a part.
12.2 Ways to Save Costs
To reduce CNC Machining production costs, consider factors like material optimization, efficient tooling utilization, streamlined processes, waste reduction, and economies of scale. Collaborating with an experienced CNC Machining partner like Neway can also help optimize costs through expertise and efficient project management.
Trends and Developments
CNC Machining continues to evolve with technological advancements. Trends like automation, integration of artificial intelligence, enhanced machine connectivity, and advanced tooling techniques are shaping the future of CNC Machining. Continuous speed, accuracy, and efficiency improvements will drive the industry forward.
Why Choose Us
Neway: Your Trusted CNC Machining Partner
With Neway, you gain access to exceptional CNC Machining services. We deliver high-quality parts with precision and efficiency, meeting the stringent requirements of various industries. Choose us for our cutting-edge facilities, skilled engineering team, and commitment to customer satisfaction.
Take advantage of our special offer! New customers can enjoy a 20% discount on their first order. Experience the excellence of Neway CNC Machining today.
Conclusion
CNC Machining is a highly efficient and precise manufacturing process that offers numerous benefits in terms of quality, repeatability, and complex part production. By understanding the operation steps, materials, mold design considerations, and post-processing options, you can optimize your CNC Machining projects for success. When choosing a CNC Machining service provider, consider partnering with Neway for their expertise, advanced capabilities, and commitment to delivering high-quality machined parts. Take advantage of our special offer of 20% off your first order! Contact Neway today to discuss your CNC Machining requirements and use our reliable services.
评论
发表评论