Welcome to the fascinating world of Metal Injection Molding (MIM), a process that combines the design flexibility of plastic injection molding with the strength and integrity of wrought metals. The importance of material selection in MIM cannot be overstated. The choice of material directly influences the final product's performance, durability, and application. This blog aims to provide a comprehensive overview of the various alloy options available in MIM, their properties, and their implications for part designers and purchasers.
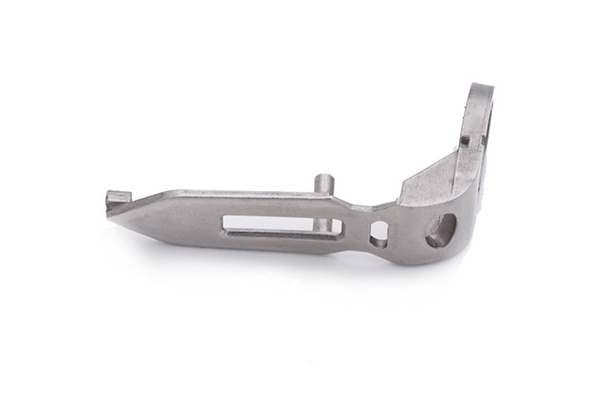
MIM Alloy Options
Material Types | Common Grade |
MIM 4605, MIM 4140, MIM 4340, MIM 2700, MIM 2200, MIM 52100, MIM 8620, MIM 9310 | |
MIM-Fe-50Ni, MIM-Fe-3Si, MIM-Fe-50Co, MIM-2200 (Fe-2%Ni), MIM-430L | |
MIM-304, MIM-316L, MIM-17-4 PH, MIM-420, MIM-440C, MIM-430 | |
Ti-6Al-4V (Grade 5), Ti-6Al-7Nb (Grade 26), Ti-5Al-2.5Fe (Grade 38), Ti-3Al-2.5V (Grade 9), Ti-15V-3Cr-3Al-3Sn, Ti-10V-2Fe-3Al (Grade 20), Ti-15Mo-5Zr-3Al (Grade 21) | |
A2, M2, M4, D2, S7, H13, T15 | |
MIM W-Ni-Fe, MIM W-Ni-Cu, MIM W-Cu, MIM W-Ni-Co, MIM W-Fe | |
MIM-CoCrMo (ASTM F75), MIM-CoCrW, MIM-CoNiCrMo, MIM-MP35N, MIM-Haynes 25, MIM-Stellite 6 |
Properties And Applications
Metal Injection Molding (MIM) has revolutionized how complex metal components are manufactured. This innovative process combines the design flexibility of plastic injection molding with the material properties of metal, resulting in intricate, high-performance parts. MIM metals, such as low alloy steels, magnetic alloys, stainless steel, titanium alloy, tool steel, and tungsten alloy, offer unique features and find diverse industry applications.
Low Alloy Steels
Key Features: Low alloy steels are known for their balanced strength, toughness, and cost-effectiveness. They are alloyed with small amounts of other elements to enhance their properties. These steels exhibit good machinability, wear resistance, and impact strength, making them suitable for various applications.
Applications: Low alloy steels find applications in automotive, aerospace, industrial machinery, and consumer goods. They are used to create gears, sprockets, shafts, and structural components that require high strength and durability. Low alloy steel MIM parts in the automotive sector contribute to engine, transmission, and suspension components. In industrial settings, they are utilized for machinery parts that undergo heavy loads and wear.
Magnetic Alloy
Key Features: Magnetic alloys possess excellent magnetic properties, including high permeability and saturation magnetization. They can conduct and concentrate magnetic flux effectively, making them vital for applications requiring magnetic functionality.
Applications: Magnetic alloy MIM parts are used in electronics, telecommunications, automotive, and medical industries. They are crucial in producing magnetic cores for inductors and transformers used in electronic devices. These parts ensure efficient energy transfer, electromagnetic shielding, and accurate signal transmission. Magnetic alloy MIM components also find applications in automotive sensors, actuators, and motor assemblies.
Stainless Steel
Key Features: Stainless steel is renowned for its corrosion resistance, mechanical strength, and aesthetic appeal. It comes in various grades, each with specific properties suited to different applications.
Applications: Stainless steel MIM parts are widely utilized in the medical, automotive, aerospace, and consumer goods sectors. In medical applications, stainless steel implants, surgical instruments, and orthopedic devices benefit from their biocompatibility and resistance to corrosion. In the aerospace industry, stainless steel components contribute to exhaust systems, engine parts, and structural components due to their ability to withstand harsh environments. In consumer goods, stainless steel MIM parts are used in watches, jewelry, and accessories.
Titanium Alloy
Key Features: Titanium alloys offer a remarkable strength-to-weight ratio, excellent corrosion resistance, and biocompatibility. These alloys are lightweight yet strong, making them suitable for high-performance and durability applications.
Applications: Titanium alloy MIM parts find applications in aerospace, medical, sports, and industrial sectors. In aerospace, titanium MIM components contribute to aircraft structures, engine components, and landing gear due to their lightweight nature and resistance to corrosion. Titanium implants, surgical instruments, and orthopedic devices leverage its biocompatibility and strength in medicine. Sports equipment, such as bicycle frames and golf club heads, benefit from titanium MIM parts' high strength and lightweight properties.
Tool Steel
Key Features: Tool steels are characterized by their high hardness, wear resistance, and ability to maintain sharp edges. They excel in applications that require cutting, shaping, and forming.
Applications: Tool steel MIM parts play a critical role in manufacturing, machining, automotive, and aerospace industries. They are used to create cutting tools, molds, and dies for shaping and forming operations. Tool steel MIM components also contribute to automotive components that require precision cutting and forming. They are integral to producing machine components that endure high stress and wear in manufacturing.
Tungsten Alloy
Key Features: Tungsten alloys are known for their high density and strength. They offer exceptional mass and radiation shielding properties.
Applications: Tungsten alloy MIM parts find applications in aerospace, medical, and sporting goods industries. In aerospace, they contribute to balance and stability in aircraft components. In medical technology, tungsten alloys are used for radiation shielding in imaging and treatment equipment. They also find use in sporting goods, such as darts and golf club weights, where precise weight distribution is essential for performance.
Cobalt Alloys
Key Features: Cobalt alloys, known for their exceptional corrosion resistance, high-temperature strength, and wear resistance, are vital in MIM applications. These alloys maintain their mechanical properties even at elevated temperatures, making them suitable for extreme environments. Adding chromium, tungsten, and molybdenum enhances their performance in challenging conditions. Cobalt alloys exhibit superior hardness, making them ideal for wear-resistant components.
Applications: Cobalt alloys find applications across industries that demand reliable performance in harsh environments. MIM cobalt alloy components contribute to aircraft engines, gas turbine parts, and exhaust systems in aerospace. These alloys excel in parts subjected to high temperatures, combustion, and corrosive gases. The medical field benefits from cobalt alloy MIM parts used in orthopedic implants and dental prosthetics due to their biocompatibility and resistance to bodily fluids. Additionally, cobalt alloy MIM parts are utilized in the energy sector for oil and gas exploration components, where their corrosion resistance is paramount.
What We Can Offer?
We offer free material selection and consultative design services from beginning to end. No MOQs, Rapid prototyping, and mass production are our strengths.
评论
发表评论