MIM-A2 Tool Steel Injection Molding
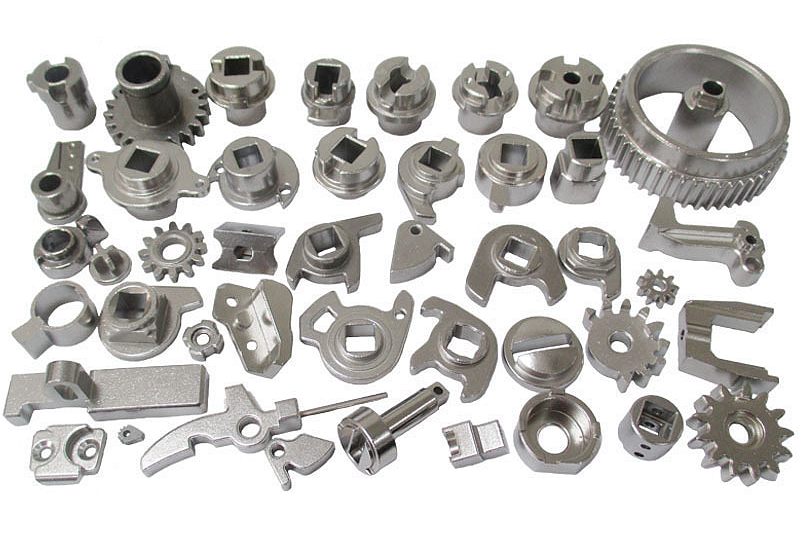
A2 Tool Steel Injection Molding Parts
A2 Tool Steel Injection Molding Parts have exceptional hardness, with a Rockwell C hardness of 60-62, ensuring durability and wear resistance, making them ideal for applications requiring precision and long-term reliability. This hardness also enables A2 Tool Steel Parts to maintain their shape and dimensions under extreme conditions, preventing deformation and ensuring consistent, high-precision manufacturing.
Secondly, A2 Tool Steel Parts exhibit excellent dimensional stability, even in high-temperature environments. This quality is crucial for maintaining tight tolerances in injection molding processes, resulting in consistently accurate and repeatable components. Additionally, A2 Tool Steel's good machinability facilitates the production of intricate molds and dies, further enhancing the precision and efficiency of injection molding operations.
Typical Properties Of MIM A2 Tool Steel
Download PDF: MIM A2 Tool Steel Materials Datasheet |
---|
Chemical Composition Of MIM A2 Tool Steel
Element | Carbon (C) | Chromium (Cr) | Manganese (Mn) | Silicon (Si) | Nickel (Ni) | Vanadium (V) | Molybdenum (Mo) |
---|---|---|---|---|---|---|---|
Composition (%) | 1.00 | 5.00 | 0.30 | 0.60 | 0.30 | 0.32 | 1.20 |
MIM-A2 Tool Steel Physics and Mechanical Properties
Property | Status | Tensile Strength (MPa) | Yield Strength (MPa) | Impact Strength (J) | Hardness (HRC) | Young's Modulus (GPa) | Poisson's Ratio | Elongation (%) | Density (g/cm³) |
---|---|---|---|---|---|---|---|---|---|
Typical Values | Heat Treated | 670 | 560 | 12.0 | 60 | 210 | 0.28 | 14 | 7.83 |
Applications of MIM-A2 Tool Steel Injection Molding Parts
A2 Tool Steel Injection Molding Aerospace Fasteners
A2 Tool Steel Injection Molding Aerospace fasteners ensure aircraft components' structural integrity and safety. These fasteners, often in the form of bolts, screws, and rivets, benefit from A2 Tool Steel's exceptional properties.
Firstly, A2 Tool Steel's high hardness and wear resistance make it an ideal choice for aerospace fasteners. In demanding flight conditions, where extreme temperatures, vibrations, and stress are commonplace, these fasteners maintain their integrity, preventing loosening or failure. Their resistance to wear ensures long-term reliability. Secondly, the dimensional stability of A2 Tool Steel ensures that these fasteners meet precise specifications, guaranteeing a secure fit and maintaining structural integrity. In aerospace applications, where precision is paramount, A2 Tool Steel Injection Molding Parts provide the strength and accuracy needed for safe and efficient flight.
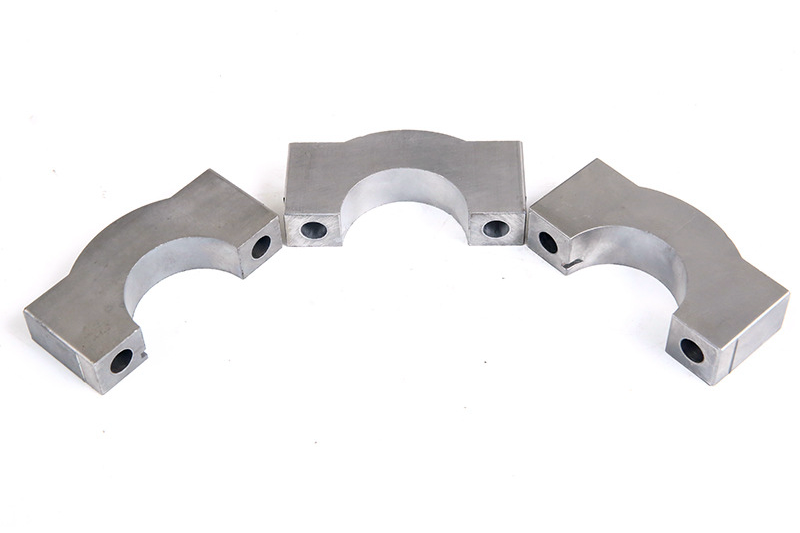
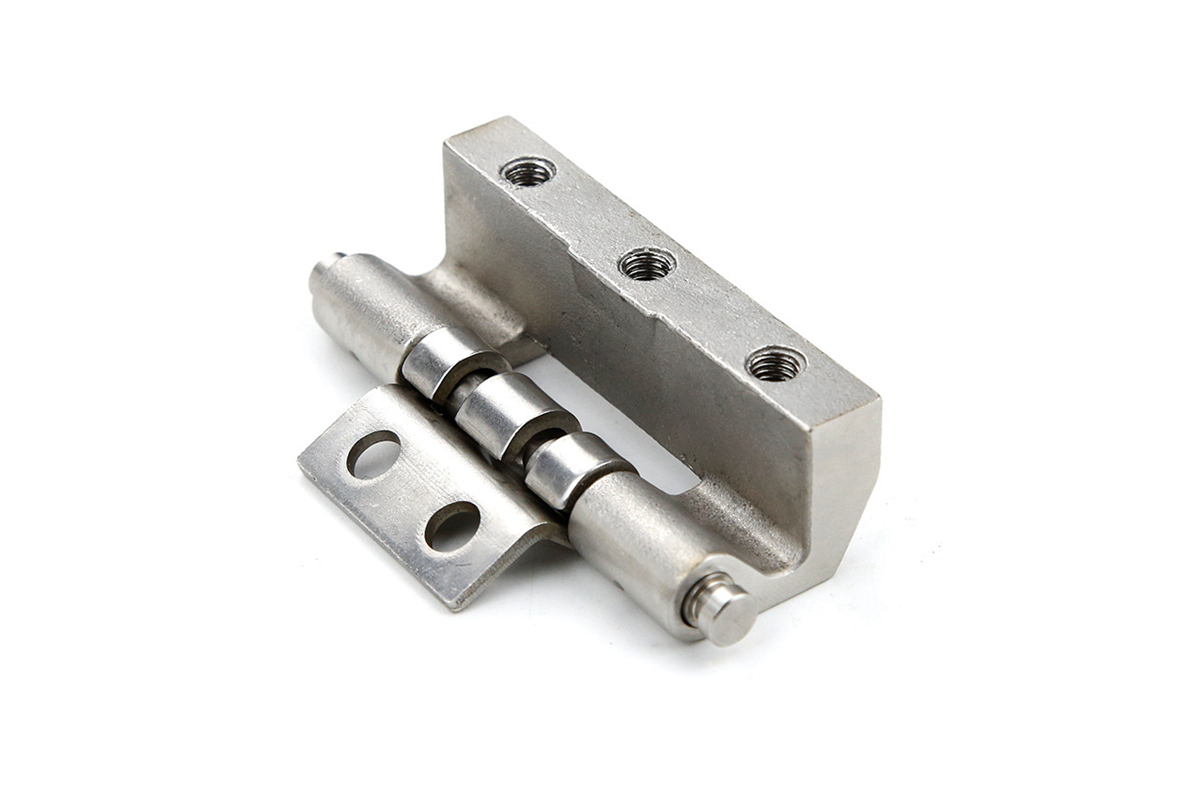
A2 Tool Steel Injection Molding Computer Hinges
Computer hinges made from A2 Tool Steel are renowned for their exceptional hardness and wear resistance. This robustness ensures that the hinges endure repeated opening and closing of laptop screens or other devices without wear and tear. The high precision achievable with A2 Tool Steel Injection Molding also contributes to the hinges' reliability, ensuring a smooth and precise movement, which is crucial in laptops and other electronic devices.
Furthermore, A2 Tool Steel Injection Molding allows for complex hinge designs with tight tolerances, ensuring a perfect fit within the device's structure. This precision contributes to modern laptops' sleek, compact design and enhances usability. In summary, A2 Tool Steel Injection Molding computer hinges offer a winning combination of durability, precision, and wear resistance, making them an ideal choice for the demanding requirements of the computing industry.
A2 Tool Steel Injection Molding Camera Mounts
Firstly, A2 Tool Steel's high hardness and wear resistance ensure the durability of camera mounts. These mounts are subjected to frequent adjustments and load-bearing tasks, and A2 Tool Steel's robustness ensures that they can withstand repeated use without deforming or deteriorating over time.
Secondly, A2 Tool Steel Injection Molding allows for intricate and precise designs. This level of precision is vital for achieving accurate camera angles and positions. Whether in professional studios or outdoor settings, confidently making micro-adjustments enhances the quality and consistency of captured images and videos. In summary, A2 Tool Steel Injection Molding Camera Mounts offer the advantages of durability and precision, providing photographers and videographers with the reliability and stability needed to achieve exceptional results in their creative endeavors.
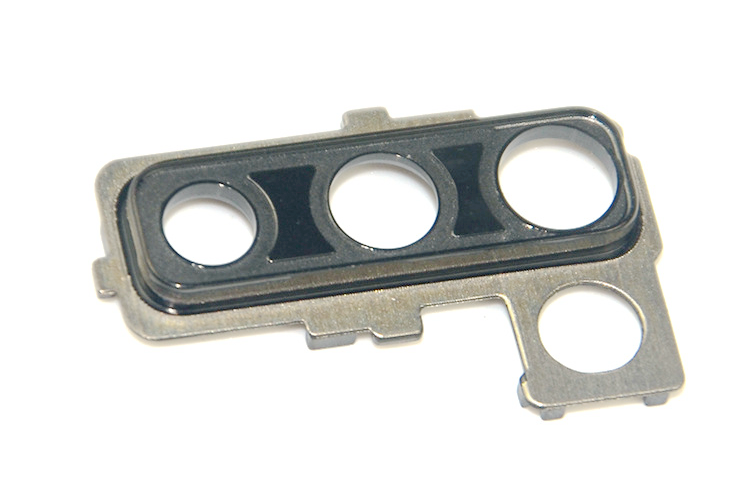
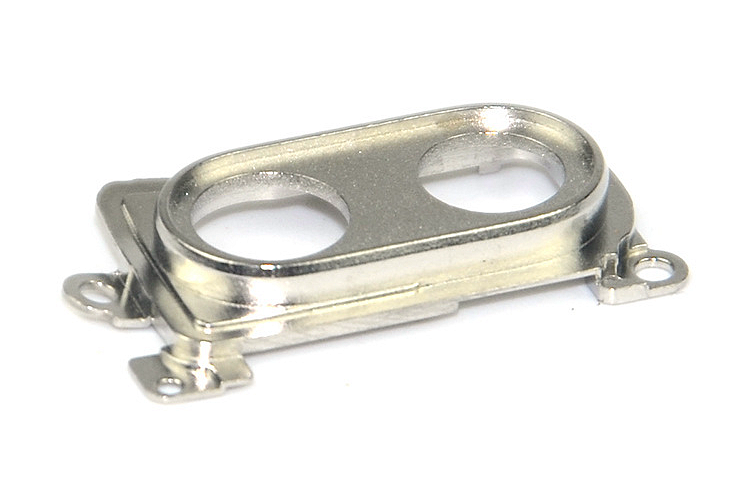
A2 Tool Steel Injection Molding Lens Mounts
Firstly, A2 Tool Steel's exceptional hardness and wear resistance ensure the longevity and reliability of lens mounts. These mounts are responsible for securely holding delicate and expensive camera lenses. A2 Tool Steel's durability guarantees that lens mounts can withstand the stress of repeated lens changes without wearing down or causing misalignment.
Secondly, A2 Tool Steel Injection Molding allows for intricate and precise manufacturing, ensuring that lens mounts maintain tight tolerances and accurate alignment. This precision is crucial for maintaining the optical integrity of lenses and ensuring that images remain sharp and distortion-free. In summary, A2 Tool Steel Injection Molding Lens Mounts offer the benefits of longevity, reliability, and precision, contributing to producing high-quality optical equipment for photographers and professionals in the imaging industry.
评论
发表评论