Stainless Steel Precision Casting
Stainless steel is a versatile material with several key features that make it a standout choice in precision casting, including investment casting, sand casting, and gravity casting. Its exceptional corrosion resistance ensures durability, making it ideal for applications in demanding environments. Stainless steel also boasts high strength, enhancing the structural integrity of cast components.
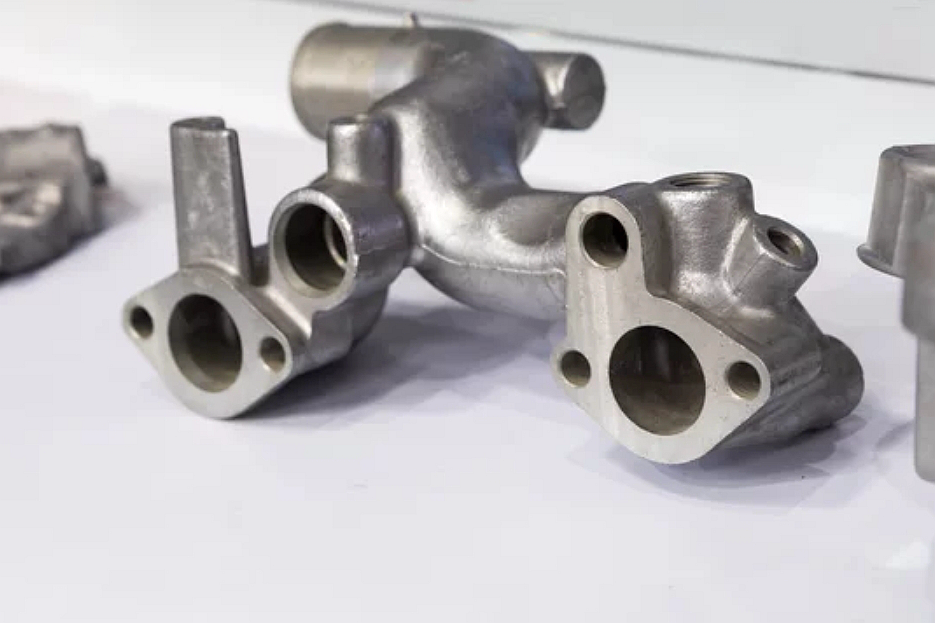
Stainless Steel's diverse range of alloys provides tailored solutions, ensuring it suits various applications. In consumer electronics, it's employed for durable and aesthetically pleasing components, while in the aerospace industry, it contributes to lightweight yet robust structures. These exceptional attributes of stainless steel underscore its indispensable role in precision casting across multiple industries.
Stainless Grade Neway Uses:
SS 304
SS 316
SS 17-4 PH
SS 410
SS 2205
SS 17-7 PH
SS 440C
Alloy 718
Properties of Cast Stainless Steel
Download PDF: Cast Stainless Steel Datasheet |
---|
Chemical Comparison of Cast Stainless Steel
Alloy Type | C (Carbon) | Si (Silicon) | Mn (Manganese) | P (Phosphorus) | S (Sulfur) | Cr (Chromium) | Ni (Nickel) | Mo (Molybdenum) | Cu (Copper) | Nb (Niobium) | N (Nitrogen) | Other Elements |
---|---|---|---|---|---|---|---|---|---|---|---|---|
SS 304 | 0.08 | 0.75 | 2.00 | 0.045 | 0.030 | 18.00 | 8.00 | - | - | - | 0.10 | - |
SS 316 | 0.08 | 0.75 | 2.00 | 0.045 | 0.030 | 16.00 | 10.00 | 2.00 | - | - | 0.10 | - |
SS 17-4 PH | 0.07 | 1.00 | 1.00 | 0.040 | 0.030 | 15.50 | 3.00 | 0.25 | 3.75 | - | 0.15 | - |
SS 410 | 0.15 | 1.00 | 1.00 | 0.040 | 0.030 | 11.50 | - | - | - | - | - | - |
SS 2205 | 0.03 | 1.00 | 2.00 | 0.030 | 0.020 | 22.00 | 5.50 | 3.00 | - | 0.14 | 0.20 | - |
SS 17-7 PH | 0.09 | 1.00 | 1.00 | 0.040 | 0.030 | 16.00 | 7.00 | - | - | - | - | Al: 0.75, Si: 1.00 |
SS 440C | 0.95 | 1.00 | 1.00 | 0.040 | 0.030 | 17.00 | - | - | - | - | - | - |
Alloy 718 | 0.08 | 0.35 | 0.35 | 0.015 | 0.015 | 19.00 | 52.50 | 3.05 | 0.90 | 5.13 | 0.04 | Ti: 0.65, Al: 0.21 |
Function of Chemical Components
Carbon (C):
Carbon content primarily influences the hardness and strength of stainless steel. Higher carbon levels increase hardness, making steel suitable for cutting tools and applications requiring wear resistance. In contrast, low carbon levels improve ductility and weldability but may reduce hardness and strength. Careful control of carbon content is essential to achieve the desired balance of these properties.
Silicon (Si):
Silicon enhances the steel's resistance to oxidation at high temperatures. It acts as a deoxidizer during steel production, preventing the formation of undesirable oxides. Silicon also improves the steel's electrical resistivity, making it valuable in electrical applications.
Manganese (Mn):
Manganese serves multiple functions, including deoxidation, which helps eliminate impurities. It also aids in controlling the formation of sulfides, which can be detrimental to steel quality. Manganese contributes to strength, flexibility, and workability, making it crucial in various fabrication processes.
Phosphorus (P) and Sulfur (S):
Phosphorus and sulfur are typically minimized in stainless steel because they can lead to brittleness and reduced corrosion resistance. These impurities can promote the formation of brittle phases within the steel, affecting its mechanical properties.
Chromium (Cr):
Chromium is the cornerstone of stainless steel's corrosion resistance. It forms a passive oxide layer on the steel's surface, known as chromium oxide. This layer acts as a barrier, preventing further oxidation and corrosion. Higher chromium content equates to improved corrosion resistance, which is vital in applications exposed to aggressive environments.
Nickel (Ni):
Nickel enhances both corrosion resistance and flexibility. It is precious in stainless steel alloys that resist aggressive chemicals, such as those used in the chemical and petrochemical industries. Nickel also contributes to a higher level of toughness, making stainless steel more durable.
Molybdenum (Mo):
Molybdenum significantly improves stainless steel's resistance to pitting and crevice corrosion, especially in chloride-rich environments like seawater. It also contributes to the steel's high-temperature strength, making it suitable for applications in elevated-temperature conditions.
Copper (Cu):
Copper can be added in small quantities to enhance resistance to specific types of corrosion, such as sulfuric acid attack. It makes copper-containing stainless steels useful in applications where exposure to aggressive acids is a concern.
Niobium (Nb):
Niobium stabilizes the steel's structure, particularly in applications where high-temperature exposure can lead to sensitization. Sensitization can reduce the corrosion resistance of stainless steel. Niobium helps prevent this issue.
Nitrogen (N):
Nitrogen can be intentionally added to enhance strength and corrosion resistance in austenitic stainless steel. It can promote the formation of nitrogen-rich precipitates, which strengthen the steel's structure.
Stainless Steel Physical and Mechanical Properties
Alloy Type | Tensile Strength (MPa) | Yield Strength (MPa) | Hardness (Brinell) | Shear Strength (MPa) | Impact Strength (J) | Fatigue Strength (MPa) | Thermal Conductivity (W/m·K) | Density (g/cm³) | Melting Range (°C) |
---|---|---|---|---|---|---|---|---|---|
SS 304 | 515 | 205 | 201 | 275 | 100 | 150 | 16.2 | 7.93 | 1,400-1,450 |
SS 316 | 580 | 290 | 217 | 297 | 100 | 150 | 16.2 | 7.98 | 1,370-1,400 |
SS 17-4 PH | 1034 | 760 | 363 | 688 | 20 | 380 | 14.9 | 7.78 | 1,045-1,100 |
SS 410 | 655 | 310 | 201 | 450 | 25 | 260 | 24.9 | 7.74 | 1,400-1,480 |
SS 2205 | 620 | 450 | 293 | 420 | 105 | 260 | 14.2 | 7.80 | 1,399-1,465 |
SS 17-7 PH | 1000 | 780 | 363 | 689 | 20 | 380 | 15.2 | 7.85 | 1,060-1,100 |
SS 440C | 758 | 448 | 57 HRC | 550 | 10 | 275 | 24.2 | 7.80 | 1,100-1,370 |
Alloy 718 | 965 | 550 | 363 HB | 550 | 140 | 415 | 6.6 | 8.24 | 1,250-1,350 |
Key Features and Applications of Stainless Steel Castings
Stainless Steel 304 (AISI 304, SAE 304, UNS S30400)
Stainless Steel 304 (AISI 304, SAE 304, UNS S30400) is a highly regarded material in precision casting due to its remarkable features. SS 304 is ideal for precision casting applications because it has excellent corrosion resistance, formability, and versatility. Its exceptional corrosion resistance ensures that components remain unscathed in challenging environments, making it particularly suitable for investment casting, gravity casting, and sand casting processes. Additionally, SS 304's non-magnetic property is advantageous in precision casting, as it prevents interference with magnetic fields, contributing to enhanced precision.
In the realm of precision casting, SS 304 finds its applications in various industries. Its superior corrosion resistance and clean aesthetic make it an excellent choice for critical components in consumer electronics, telecommunication equipment, and lighting solutions. Additionally, SS 304's ease of cleaning and resistance to corrosion make it an attractive option for precision casting in the mentioned industries, where performance and aesthetics are paramount. However, it's important to note that SS 304 is less commonly used in marine applications due to specific corrosion challenges in that environment.
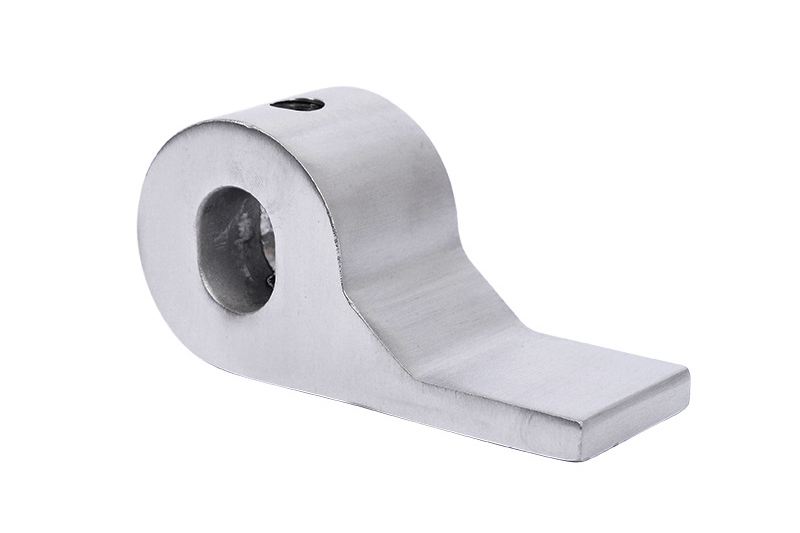
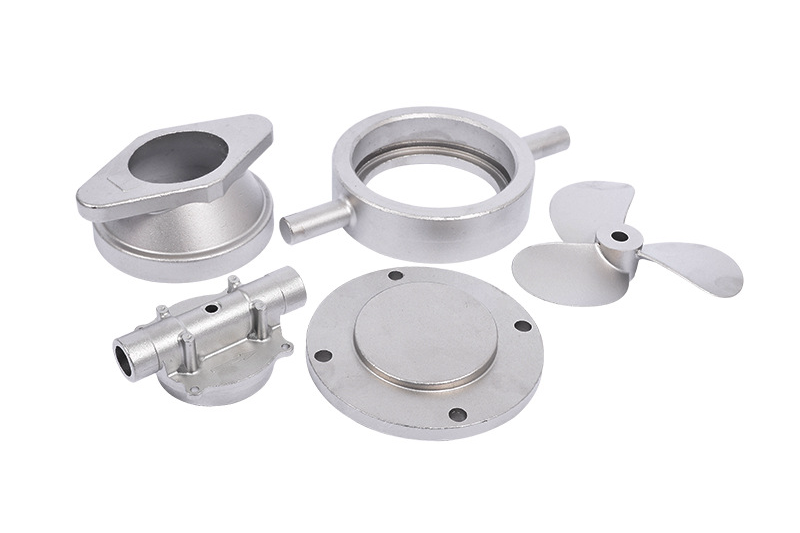
Stainless Steel 316 (AISI 316, SAE 316, UNS S31600)
Stainless Steel 316 (AISI 316, SAE 316, UNS S31600) is a paramount choice for precision casting due to its exceptional attributes. It offers even higher corrosion resistance than SS 304, especially in chloride-rich environments, making it a top contender for precision casting in investment, gravity, and sand casting applications. The resistance to pitting and crevice corrosion further enhances its appeal for precision casting in challenging conditions, ensuring the longevity and reliability of cast components.
In precision casting, SS 316 finds its applications in various critical sectors. Its unparalleled corrosion resistance makes it indispensable in marine equipment, where exposure to saltwater is constant. Furthermore, SS 316 is extensively utilized in precision casting for chemical processing equipment, where resistance to harsh chemicals is imperative. Its remarkable weldability makes it an attractive choice for complex precision casting requirements, such as medical implants and pharmaceutical machinery, ensuring the production of high-quality components in these precision-critical applications.
Stainless Steel 17-4 PH (AISI 630, SAE 630, UNS S17400)
Stainless Steel 17-4 PH, also known as AISI 630 or SAE 630, is a remarkable alloy renowned for its exceptional attributes in precision casting, including investment casting, gravity casting, and sand casting. The key features of this alloy are its remarkable blend of high strength, hardness, and corrosion resistance. It is a versatile material that can be further enhanced through heat treatment, yielding even greater strength, making it an excellent choice for precision casting applications. Additionally, its durability sets it apart, ensuring longevity in the most demanding environments.
In precision casting, SS 17-4 PH finds its niche in various applications. Its high strength and durability make it an ideal candidate for aerospace components, where the stringent demands for structural integrity and resistance to harsh conditions are paramount. Furthermore, this alloy is indispensable in medical devices, where the precision and reliability of components are critical. Though slightly lower than some counterparts, its corrosion resistance still proves sufficient for mechanical parts that demand a balance of strength and corrosion resistance, further underscoring its versatility in precision casting across industries.
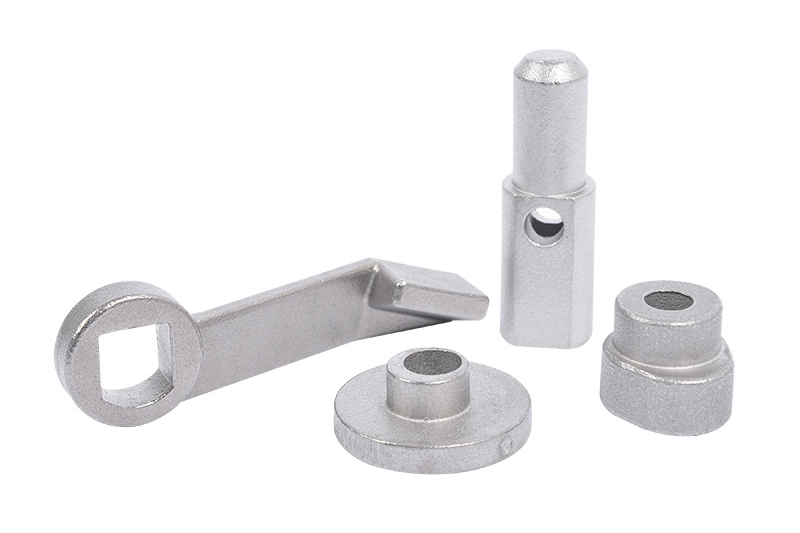
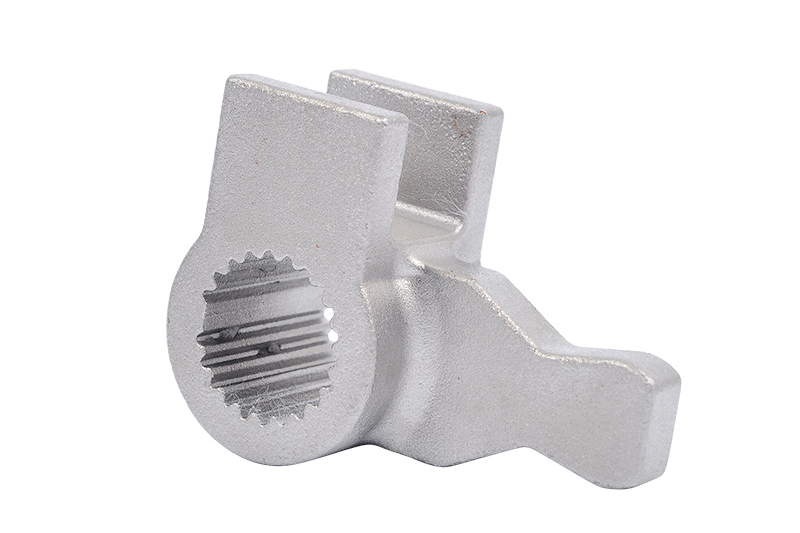
Stainless Steel 410 (AISI 410)
Stainless Steel 410, also known as AISI 410, possesses several key features that make it a valuable material in precision casting, including investment casting, gravity casting, and sand casting. First and foremost, SS 410 offers commendable corrosion resistance, ensuring cast components maintain their structural integrity even in challenging environments. Moreover, its ability to undergo heat treatment allows for enhanced hardness and wear resistance, a crucial advantage in precision casting where durability is paramount. Notably, Stainless Steel 410 is inherently magnetic and boasts high tensile strength, further accentuating its suitability for precision casting applications.
In the realm of precision casting, SS 410 finds diverse applications. Its combination of corrosion resistance and robustness makes it an ideal choice for investment casting, where intricate and detailed parts are created with precision. In gravity casting, SS 410 excels in crafting components that require strength and durability, often seen in industries like Power Tools and Locking Systems. SS 410's properties in sand casting make it a preferred material for manufacturing components such as valves and pumps, where hardness and resistance to abrasion are essential for reliable and long-lasting performance.
Stainless Steel 2205 (Duplex Stainless Steel, 2205 - UNS S32205)
Stainless Steel 2205, also known as Duplex Stainless Steel or UNS S32205, possesses vital features that make it an excellent choice for precision casting processes such as investment, gravity, and sand. This remarkable alloy offers a unique combination of high corrosion resistance and superior strength, making it particularly well-suited for precision casting applications. Its resistance to stress corrosion cracking is a notable advantage, ensuring the integrity of cast components in demanding environments.
In precision casting, SS 2205 finds its applications in a variety of industries. Investment casting provides a robust material for creating intricate and highly detailed components, ensuring dimensional accuracy and surface finish. In gravity casting, its exceptional strength and corrosion resistance are leveraged for manufacturing parts like pumps, valves, and fittings that must withstand harsh conditions. In sand casting, SS 2205's versatility shines in producing components for applications in chemical processing, the oil and gas industry, and offshore structures where the requirements of dual strength and corrosion resistance are paramount.
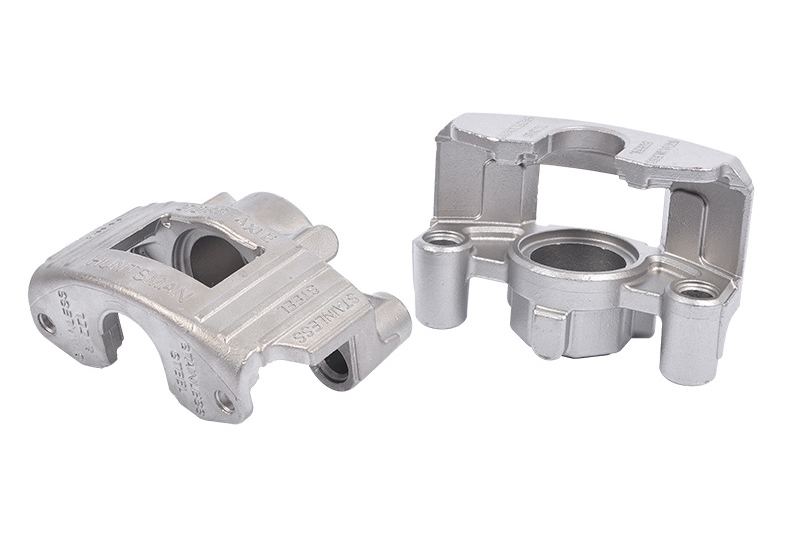
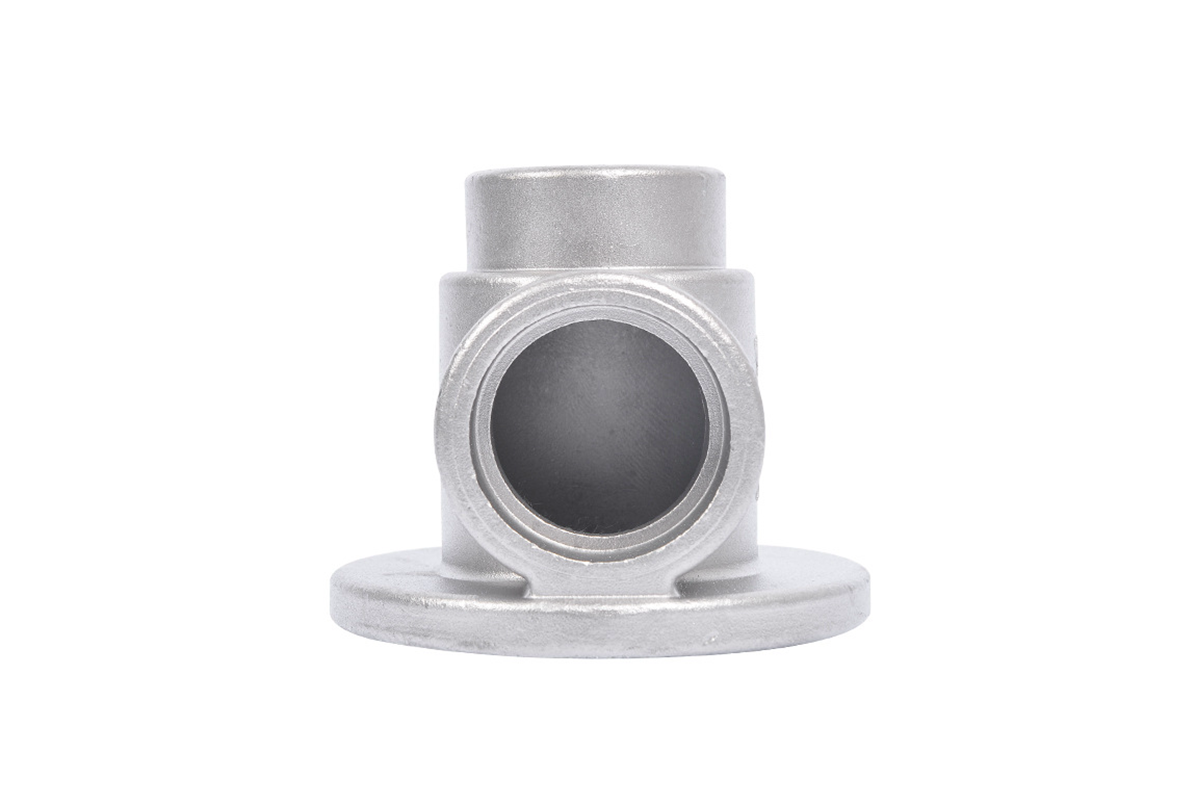
Stainless Steel 17-7 PH (AISI 631)
Stainless Steel 17-7 PH (AISI 631) holds several vital features that make it an exceptional choice for precision casting, including investment casting, gravity casting, and sand casting. This alloy boasts remarkable corrosion resistance, surpassing even SS316 and SS304, a pivotal advantage when considering the longevity of precision-cast components in demanding environments. Furthermore, its ability to undergo precipitation hardening enhances its strength and durability, a crucial attribute for precision-cast parts subjected to high stress. Notably, it is magnetic, adding versatility to its applicability in various casting methods.
In precision casting, such as investment, gravity, and sand casting, Stainless Steel 17-7 PH finds its niche in applications where strength and corrosion resistance are paramount. It becomes an ideal choice for components used in marine environments, where the challenge of combating corrosion is ever-present. Its strength makes it invaluable in precision-cast parts that withstand substantial loads or stress. This alloy's magnetic properties also provide an advantage in specific applications within these casting methods, where magnetic properties may be required.
Stainless Steel 440C (AISI 440C, SAE 51440C, UNS S44004)
Stainless Steel 440C (AISI 440C, SAE 51440C, UNS S44004) is a tool steel that makes it a valuable choice in precision casting processes such as investment, gravity, and sand. This high-carbon martensitic stainless steel stands out for its exceptional hardness, making it ideal for applications demanding superior wear resistance. Its moderate corrosion resistance further enhances its suitability for precision casting in various industries.
In precision casting, particularly investment casting, SS 440C excels in applications requiring intricate and high-precision components. The alloy's wear resistance is also invaluable in gravity casting, where components are subjected to substantial friction and stress. SS 440C's ability to withstand wear and retain its hardness in sand casting makes it a robust choice, contributing to producing durable and reliable parts. These qualities position Stainless Steel 440C as a versatile and dependable material in precision casting across industries like Consumer Electronics, Telecommunication, Lighting Solutions, Power Tools, and Locking systems.
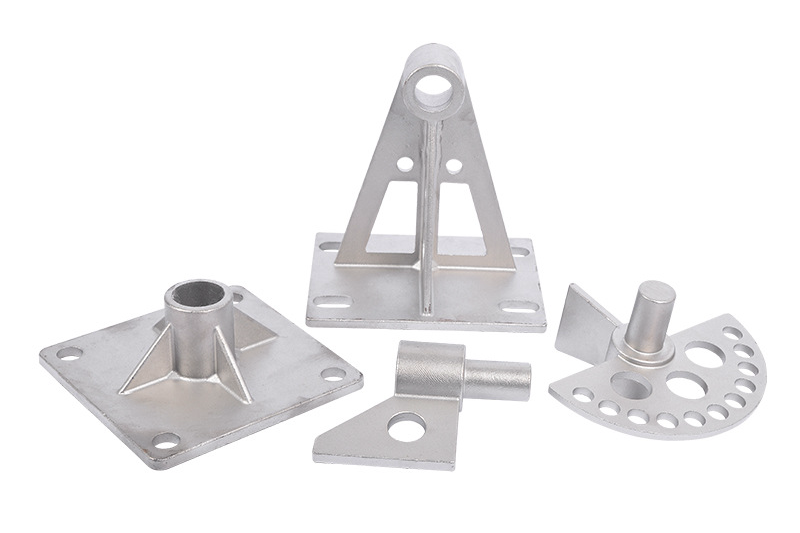
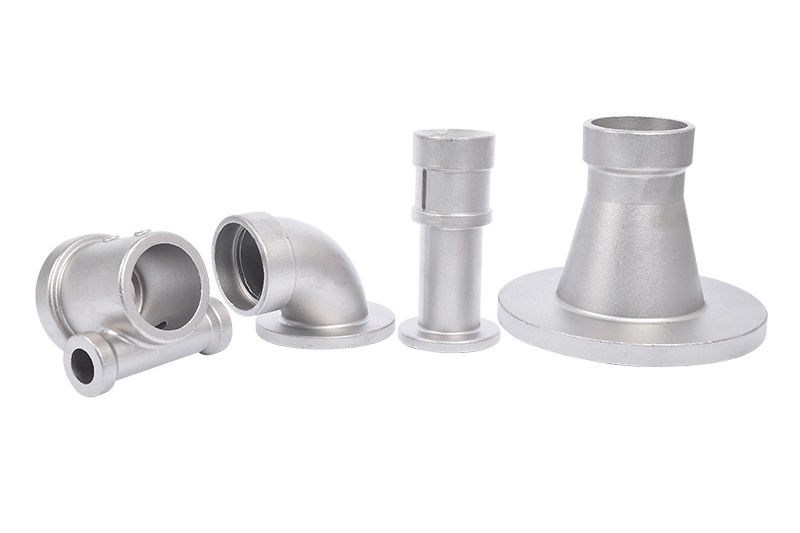
Alloy 718 (UNS N07718)
Alloy 718 (UNS N07718) is mold steel with high hardness and strength, suitable for manufacturing large injection molds. Usually, the higher the carbon content of 718, the higher the hardness, but too high a carbon content will reduce the toughness; titanium can prevent the precipitation of nitrides and carbides in 718, thus improving the oxidation resistance of 718. The more brutal 718 has smaller, denser, and more uniform grains, and the number and size of grain boundaries and precipitates will also affect the hardness of 718.
In precision investment casting, Alloy 718's high-temperature capabilities are harnessed for crafting intricate components for the aerospace and aircraft industries. In gravity casting, it excels in applications requiring resistance to extreme conditions, such as components in gas turbines. Moreover, Alloy 718's corrosion resistance comes to the forefront in sand casting, making it a dependable choice for high-temperature applications within the oil and gas industry. Its versatility and superior characteristics make Alloy 718 a standout performer in precision casting, serving various demanding industrial needs.
What We Offer In Custom Precision Casting
Neway excels in precision casting, offering die casting, investment casting, gravity casting, and sand casting services. Our expertise ensures impeccable parts with precision values exceeding industry standards. Explore our diverse applications in Consumer Electronics, Telecommunication, Lighting Solutions, Power Tools, and Locking systems. Unleash innovation with Neway's casting solutions.
2. Investment Casting Services
Try us with 20% off your first order:
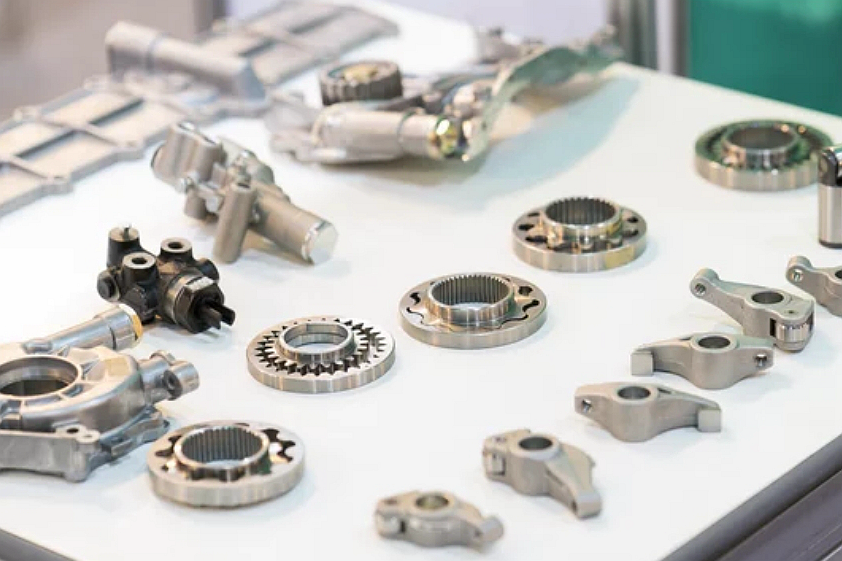
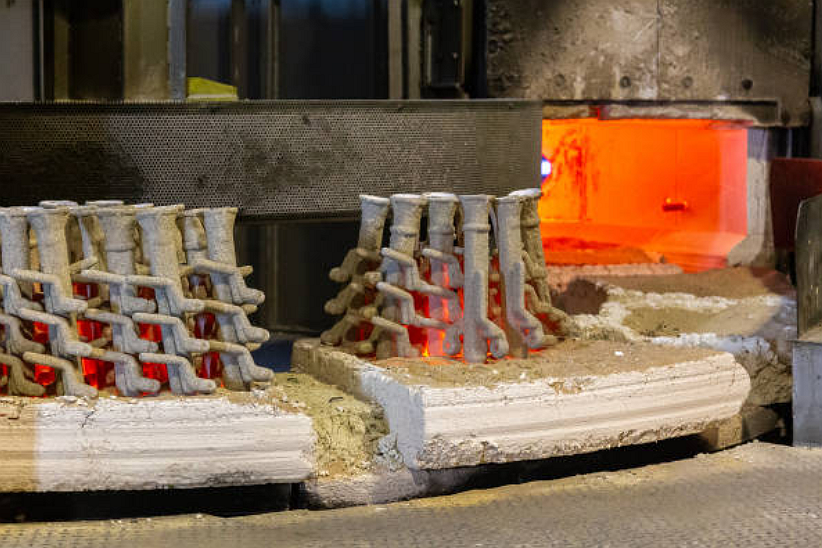
Industries We Cover In Precision Casting
Neway mainly provides Die Casting Services, Investment Casting Services, Gravity Casting Services, and Sand Casting Services. Has experience in serving projects for well-known brand companies and has been used in multiple industries:
Brand Case Study
Neway is a leading precision casting (Die Casting Services, Investment Casting Services, Gravity Casting Services) manufacturer, supplying many branded companies in cases:
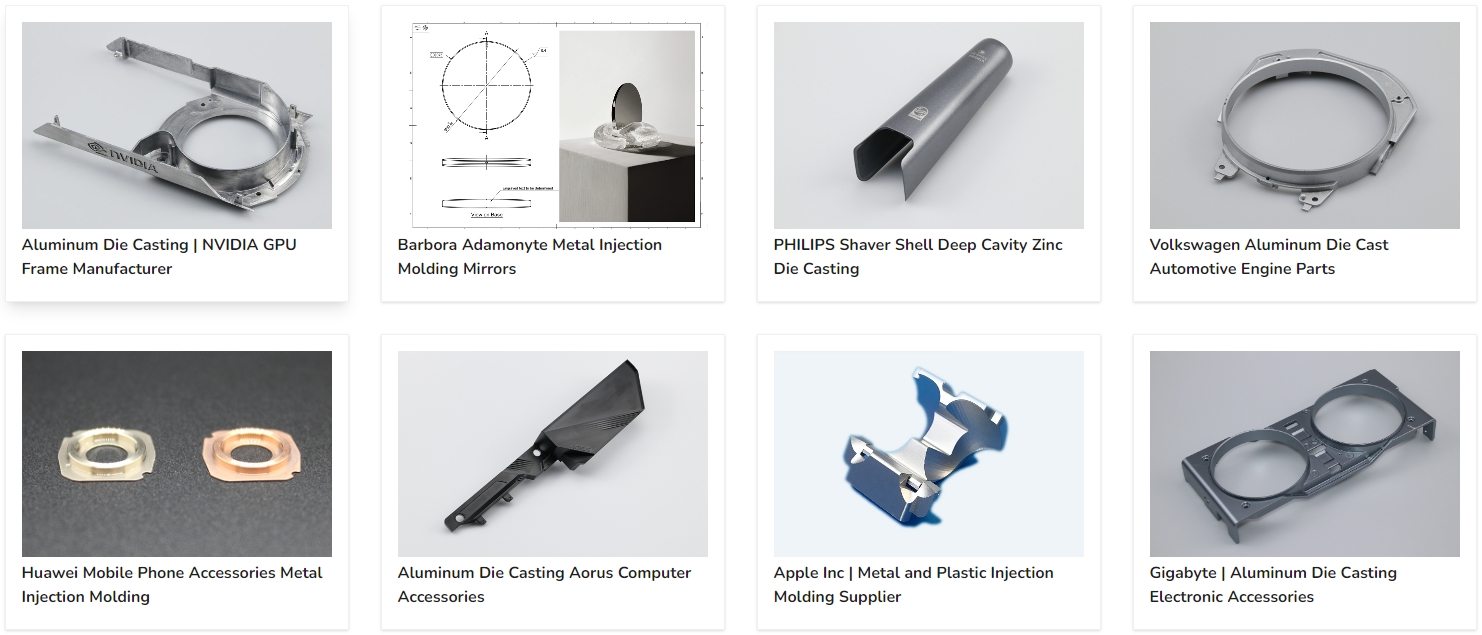
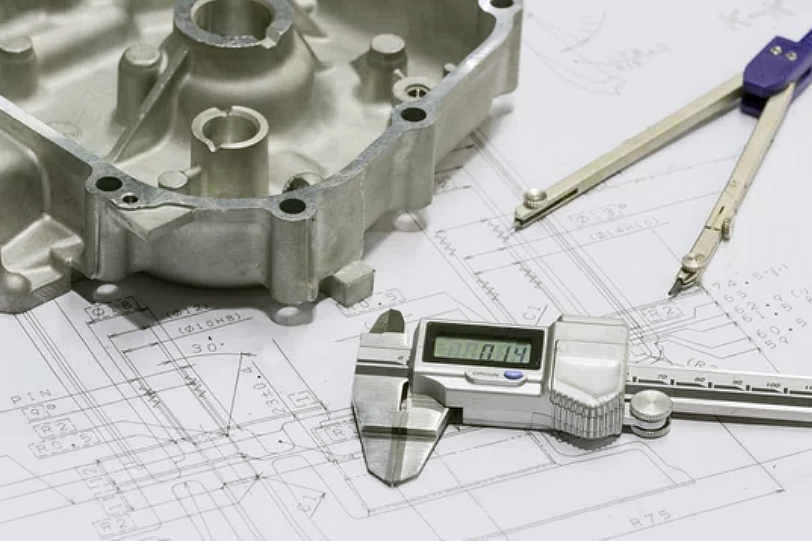
Consultative Design Services
Consultative Design Services
Neway offers free Consultative Design Services for precision casting (die casting, investment casting, gravity casting, and sand casting) services. It includes all processes from your design stage to finished castings.
1. Material selection Consult
2. Surface selection Consult
3. Structural design service
4. Mold design service
Contact us now if you are interested.
What We Can Do In Precision Casting?
We offer a one-stop service in precision castings (die casting, investment casting, gravity casting, die casting) manufacturing from prototyping to mass production. This includes:
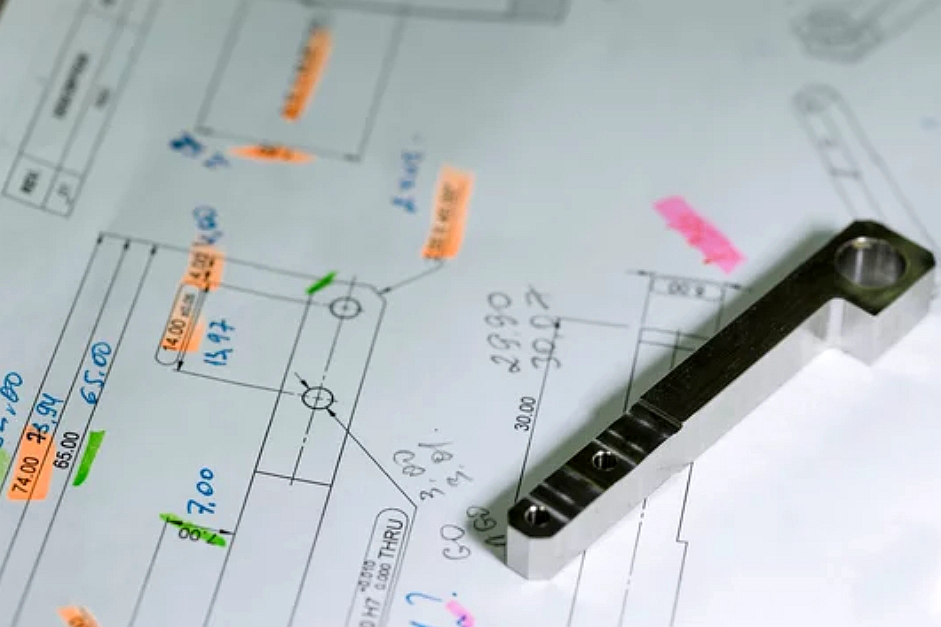
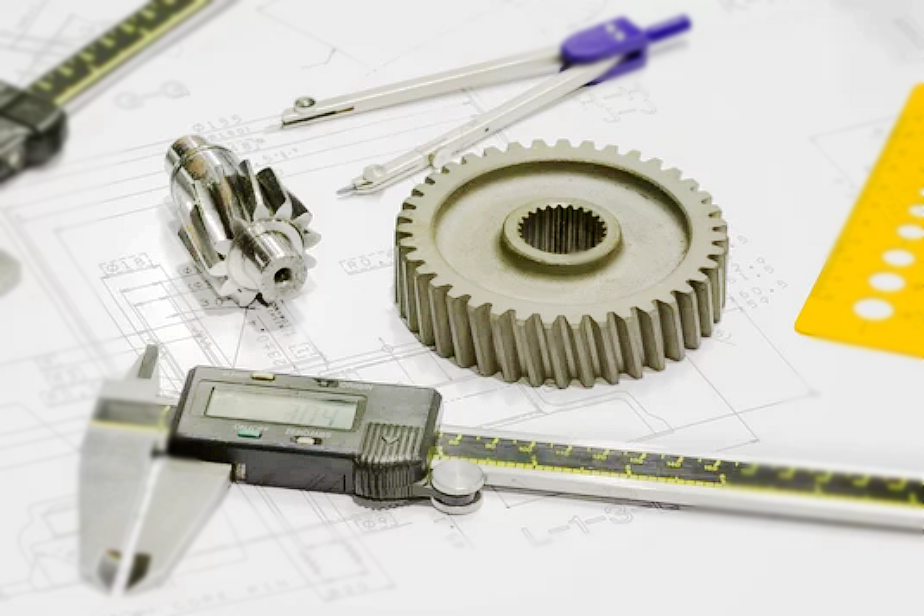
Try Neway Prototyping Service For Free
Neway provides free Consultative Design and rapid prototyping services for valid cast projects for free.
1. CNC Machining Prototyping Service
Correctly fill in your information and send it to our engineer to get free service.
Neway Custom Manufacturing Capability
Neway offers a one-stop solution for custom castings. Based on supplying precision cast (die cast, investment cast, gravity cast, sand cast) parts, we further provide post-processing and surface treatment (heat treatment, polishing, PVD) services.
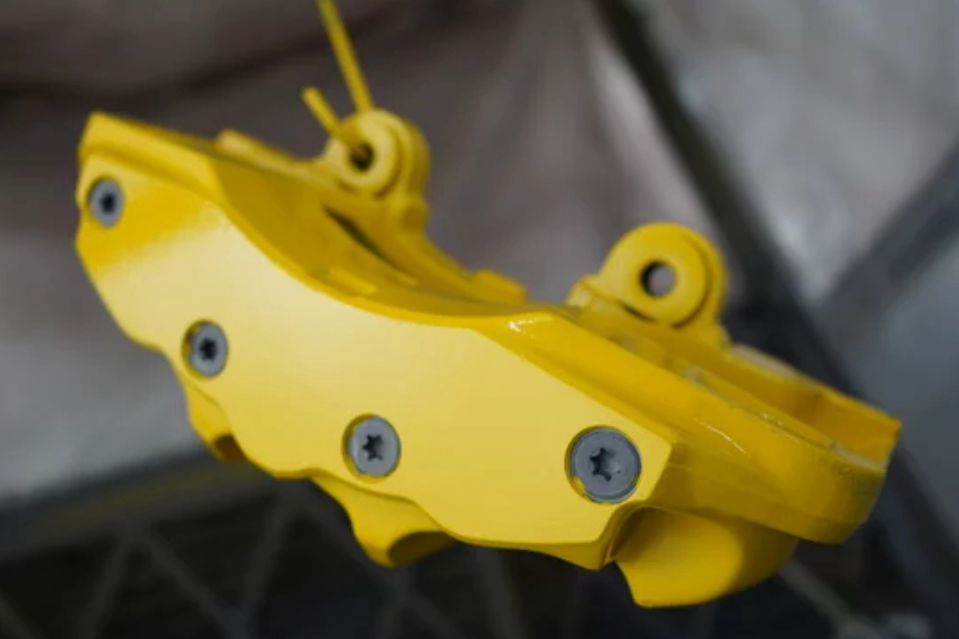
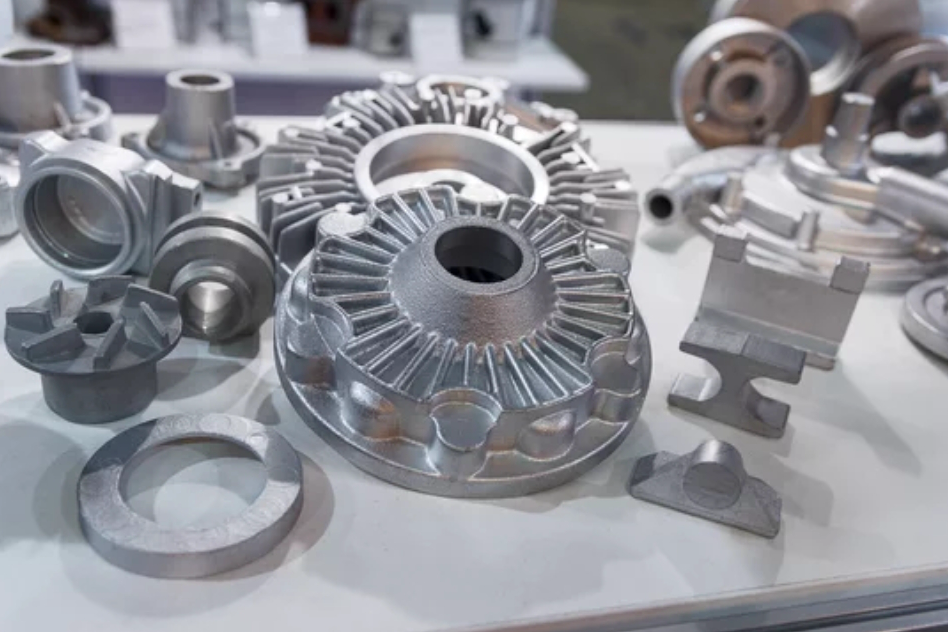
Precision Casting Cases Study
Neway is involved in many industries as an experienced precision castings (die castings, investment castings, gravity castings, and sand castings) manufacturer.
Here are related industries casting cases for your reference:
Precision Casting Materials Available
Precision Casting FAQs:
1. What Precision Casting Services Do You Offer?
2. What Are the Differences Between Die Casting and Investment Casting?
3. What Are the Tolerance Standards of Precision Casting?
4. Common Defects and Solutions in Aluminum Die Casting?
5. What is the Difference Between Sand and Investment Casting?
评论
发表评论