Carbon Steel Investment Casting
Carbon steel is a versatile material in investment casting, valued for its strength, affordability, and excellent machinability. Key features include a wide range of carbon content, from low to medium, offering a tailored approach to mechanical properties. Additionally, carbon steel is easy to cast, allowing for complex, intricate designs.
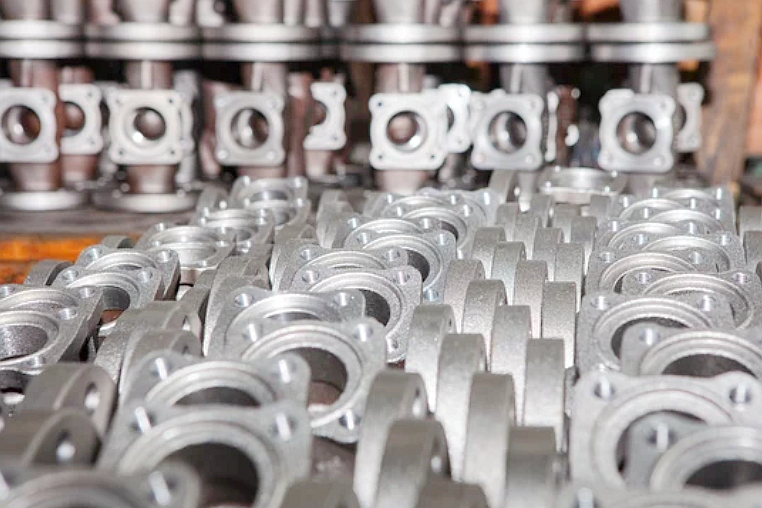
What Is Investment Casting Carbon Steel?
According to its carbon content, it can be divided into low, medium, and high carbon steel, etc. Carbon steels are mainly used in casting engineering parts, gears, bearings, and large load parts. Valve components, engine support, etc. Commonly used carbon steel casting materials such as:
AISI 1010 (Plain Carbon steel, Low Carbon Steel)
AISI 1020 (Low Carbon Steel)
AISI 1045 (Medium Carbon Steel)
AISI 4140 (chromoly steel, High Carbon Steel)
AISI 4340 (Alloy Structural Steel)
AISI 52100 (Bearing steel)
AISI 8620 (Low Carbon Alloy Steel)
Properties of Investment Cast Carbon Steels
Chemical Comparison of Investment Cast Carbon Steels
Grade | Carbon (C) | Manganese (Mn) | Phosphorus (P) | Sulfur (S) | Silicon (Si) |
---|---|---|---|---|---|
AISI 1010 | 0.08 - 0.13 | 0.30 - 0.60 | 0.040 (Max) | 0.050 (Max) | 0.10 (Max) |
AISI 1020 | 0.18 - 0.23 | 0.30 - 0.60 | 0.040 (Max) | 0.050 (Max) | 0.10 (Max) |
AISI 1045 | 0.43 - 0.50 | 0.60 - 0.90 | 0.040 (Max) | 0.050 (Max) | 0.15 - 0.35 |
AISI 4140 | 0.38 - 0.43 | 0.75 - 1.00 | 0.035 (Max) | 0.040 (Max) | 0.15 - 0.35 |
AISI 4340 | 0.38 - 0.43 | 0.60 - 0.80 | 0.025 (Max) | 0.025 (Max) | 0.20 - 0.35 |
AISI 52100 | 0.95 - 1.10 | 0.25 - 0.45 | 0.025 (Max) | 0.025 (Max) | 0.15 - 0.35 |
AISI 8620 | 0.18 - 0.23 | 0.70 - 0.90 | 0.035 (Max) | 0.040 (Max) | 0.15 - 0.35 |
Function of Chemical Components
Carbon (C):
Function: Carbon is the most significant element in carbon steel. Its concentration directly influences the steel's hardness, strength, and ability to be heat-treated.
Impact: A higher carbon content leads to greater hardness and strength but reduces ductility. Lower carbon content results in improved ductility but reduced strength.
Silicon (Si):
Function: Silicon is added to deoxidize the steel and enhance its casting properties. It also contributes to increased strength and wear resistance.
Impact: Silicon content impacts the fluidity of the molten steel and helps reduce the risk of casting defects.
Manganese (Mn):
Function: Manganese is added to increase hardenability, strengthen the steel, and improve its weldability.
Impact: Higher manganese content increases the depth to which the steel can be hardened, making it suitable for various applications.
Phosphorus (P):
Function: Phosphorus is typically kept low as it can lead to brittle castings. It may be intentionally reduced to enhance ductility.
Impact: Lower phosphorus levels are essential for maintaining the steel's toughness and preventing brittleness.
Investment Cast Carbon Steels Physical and Mechanical Properties
Steel Grade | Tensile Strength (MPa) | Yield Strength (MPa) | Hardness (Brinell) | Shear Strength (MPa) | Impact Strength (J) | Fatigue Strength (MPa) | Thermal Conductivity (W/m·K) | Density (g/cm³) | Melting Range (°C) |
---|---|---|---|---|---|---|---|---|---|
AISI 1010 | 330 - 365 | 205 - 245 | 105 - 135 | 205 - 230 | 49 (annealed) | 150 | 51.2 | 7.87 | 1460 - 1515 |
AISI 1020 | 420 - 470 | 250 - 320 | 119 - 235 | 250 - 300 | 39 (annealed) | 140 | 53.0 | 7.87 | 1495 - 1540 |
AISI 1045 | 565 - 710 | 310 - 480 | 163 - 229 | 350 - 480 | 14 (annealed) | 170 | 49.6 | 7.87 | 1480 - 1530 |
AISI 4140 | 850 - 1000 | 620 - 850 | 190 - 270 | 490 - 650 | 31 (normalized) | 415 | 44.5 | 7.85 | 1465 - 1520 |
AISI 4340 | 745 - 1000 | 470 - 850 | 201 - 248 | 450 - 650 | 31 (normalized) | 420 | 45.2 | 7.85 | 1425 - 1470 |
AISI 52100 | 325 - 580 | 240 - 515 | 150 - 680 | 370 - 515 | 2 (annealed) | 260 | 44.5 | 7.81 | 1500 - 1650 |
AISI 8620 | 470 - 850 | 290 - 550 | 156 - 255 | 380 - 520 | 8 (normalized) | 335 | 46.6 | 7.81 | 1470 - 1550 |
Key Features and Applications of Carbon Steels
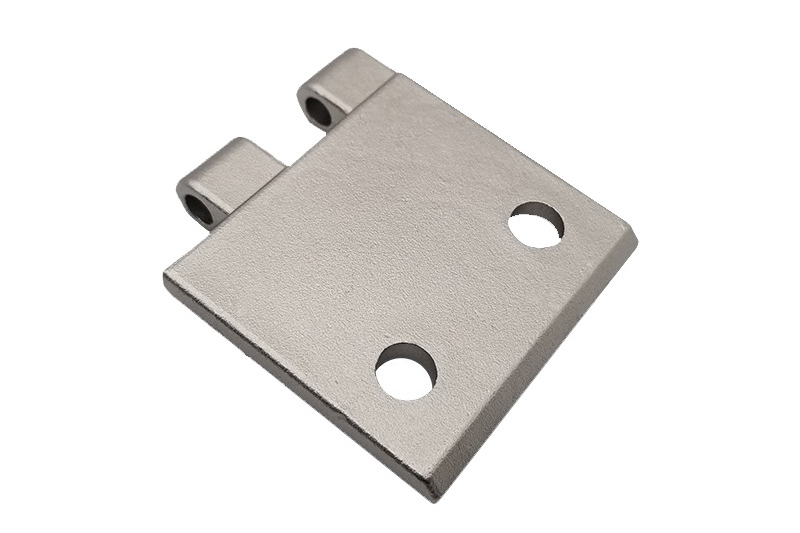
AISI 1010 (Plain Carbon steel, Low Carbon Steel) Investment Castings
AISI 1010, a type of plain carbon steel known for its low carbon content, offers distinct advantages when utilized in investment casting processes. Its key features lie in its exceptional formability and cost-effectiveness. This steel grade can be easily molded into intricate and precise shapes, making it an ideal choice for investment casting where intricate patterns and designs are crucial. The low carbon content minimizes the risk of cracking during solidification, ensuring a high-quality final product.
In investment casting applications within industries such as Consumer Electronics and telecommunications, AISI 1010 is often chosen for its ability to create intricate components with remarkable precision. This precision is particularly vital in manufacturing components for devices like smartphones and communication equipment, where the exacting tolerances of AISI 1010 enhance product performance and quality. Furthermore, its cost-effectiveness is a significant advantage, making it an attractive choice for investment casting projects in these industries.
AISI 1020 (Low Carbon Steel) Investment Castings
AISI 1020, a low-carbon steel, distinguishes itself with its suitability for a wide range of general engineering applications. Its key features include exceptional machinability and cost-effectiveness, making it a favored material in various industries. This steel's ease of machining is a critical asset, enabling efficient production of intricate and customized components, while its affordability makes it an economically sound choice for many engineering purposes.
In investment casting, AISI 1020 is frequently employed to craft components with precision and versatility. This material is precious in industries such as Power Tools and Locking Systems, where it creates intricate and durable parts. The ease of machining offered by AISI 1020 facilitates the production of high-precision gears, locks, and mechanical components. Furthermore, its cost-effectiveness aligns well with the economic considerations of these industries, making AISI 1020 a popular choice for investment casting applications.
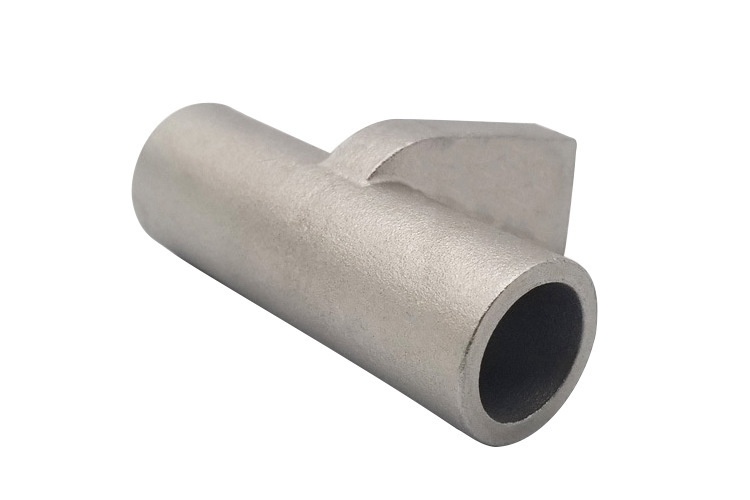
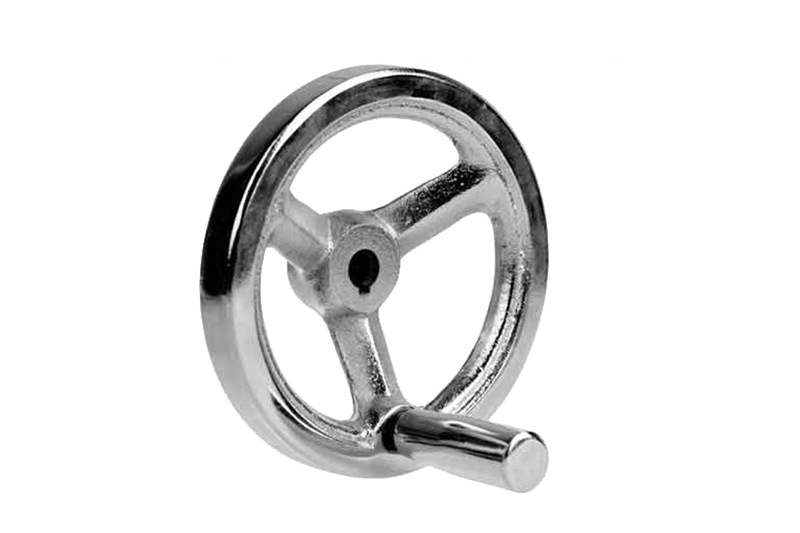
AISI 1045 (Medium Carbon Steel) Investment Casting
AISI 1045, medium carbon steel, is known for its remarkable balance between surface hardness and flexibility, making it highly suitable for various applications in the investment casting process. The inherent medium carbon content ensures that AISI 1045 can be cast precisely, maintaining intricate details while retaining mechanical strength.
AISI 1045 is widely employed in investment casting for crafting gears, shafts, and forged parts. Its remarkable balance of properties ensures that these components can withstand the rigorous demands of industries like automotive and aerospace, where precision and durability are paramount. The ability to achieve precise casting, with specific dimensional tolerances and surface finish requirements, sets AISI 1045 apart as an ideal choice for investment casting, making it a cornerstone material in the production processes of Neway, particularly in the aerospace and automotive sectors.
AISI 4140 (Chromoly steel or High Carbon Steel) Castings
AISI 4140, also known as Chromoly Steel or High Carbon Steel, possesses distinctive attributes that make it an excellent choice for investment casting in various industries, including the oil and gas sector. Its notable composition, enriched with chromium and molybdenum, imparts outstanding characteristics. This alloy is highly regarded for its exceptional strength, durability, and resistance to wear and impact, making it a prime candidate for investment casting applications.
In investment casting, AISI 4140 is pivotal in creating critical components such as connecting rods, collets, transfer pins, gears, valve stem assemblies, pump shafts, and tool holders. Its high strength and corrosion resistance, coupled with precision casting techniques, enable the production of intricate and high-precision parts for the oil and gas industry. The versatility of AISI 4140 in investment casting offers a reliable and cost-effective solution for manufacturing components with stringent requirements, ensuring optimal performance and longevity in challenging operational environments.
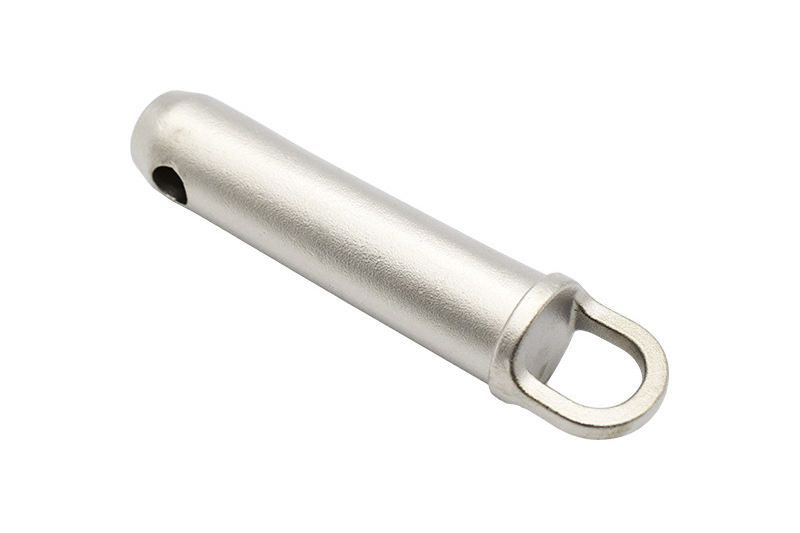
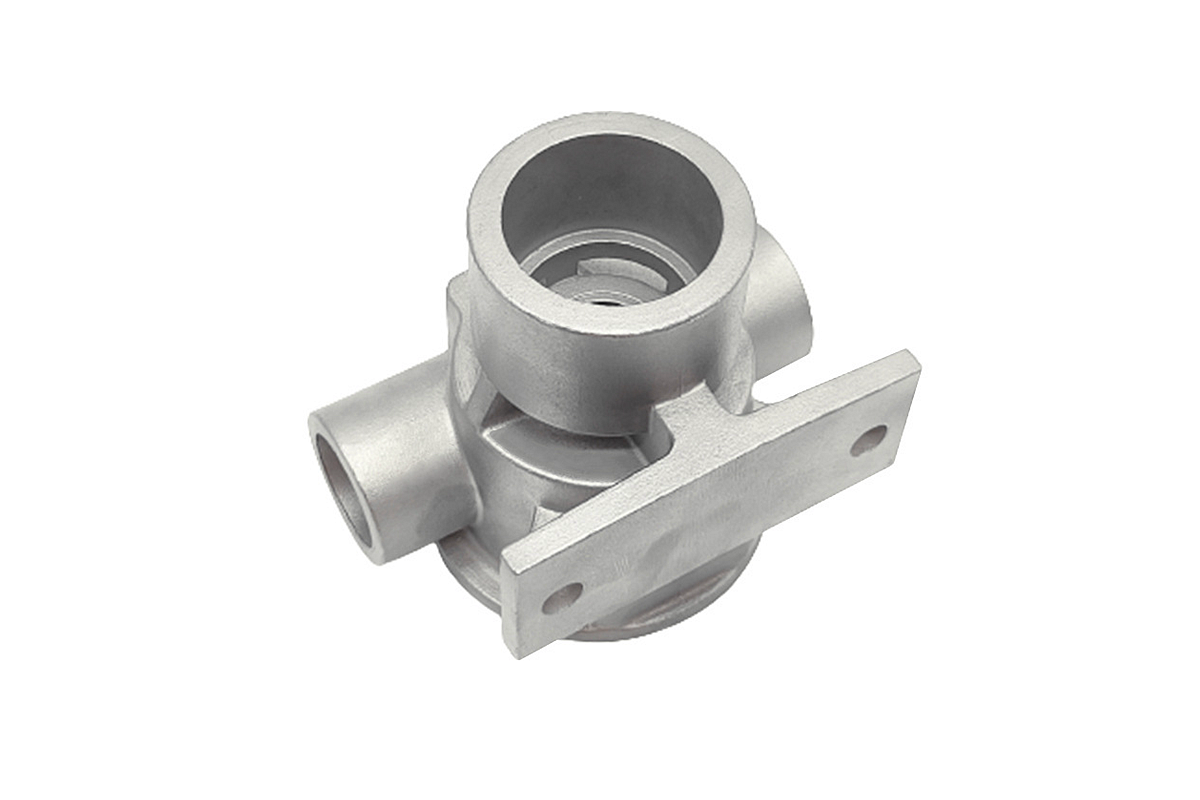
AISI 4340 (Alloy Structural Steel) Investment Cast Parts
AISI 4340, classified as Alloy Structural Steel, is renowned for its strength and toughness. This steel grade is particularly well-suited for demanding industries where structural integrity is paramount. Its composition makes it a preferred material for investment casting in applications such as aircraft parts, with a specific focus on landing gear components. The need for strength and toughness in these components is met by AISI 4340, ensuring safe and reliable operation in aviation.
Furthermore, AISI 4340's versatility extends to the automotive and heavy machinery sectors, where it serves as an essential material for investment casting structural parts. These applications benefit from their capacity to withstand heavy loads and severe stress conditions. In investment casting, AISI 4340 enables the creation of intricately designed components with precision and durability, underpinning the safety and performance standards in these critical industries.
AISI 52100 (Bearing steel) Investment Casting
AISI 52100, known as bearing steel, boasts remarkable characteristics that make it a prime choice for investment casting applications. This material is renowned for its exceptional precision and load-bearing capabilities. With outstanding wear resistance and high hardness, AISI 52100 is a top-notch choice for components that demand precision, high-speed operation, and resilience against fatigue.
In investment casting, AISI 52100 has applications in various industries, including Consumer Electronics, Telecommunication, and Power Tools. Its precision ensures that intricate components are faithfully reproduced. At the same time, its high load-bearing capacity and fatigue resistance make it ideal for mechanical parts within electronic devices, telecommunications equipment, and power tools. Whether in intricate gear components or precision bearings, AISI 52100 material excels in these industries due to its unmatched quality and performance, aligning perfectly with Neway's commitment to delivering excellence in investment casting.
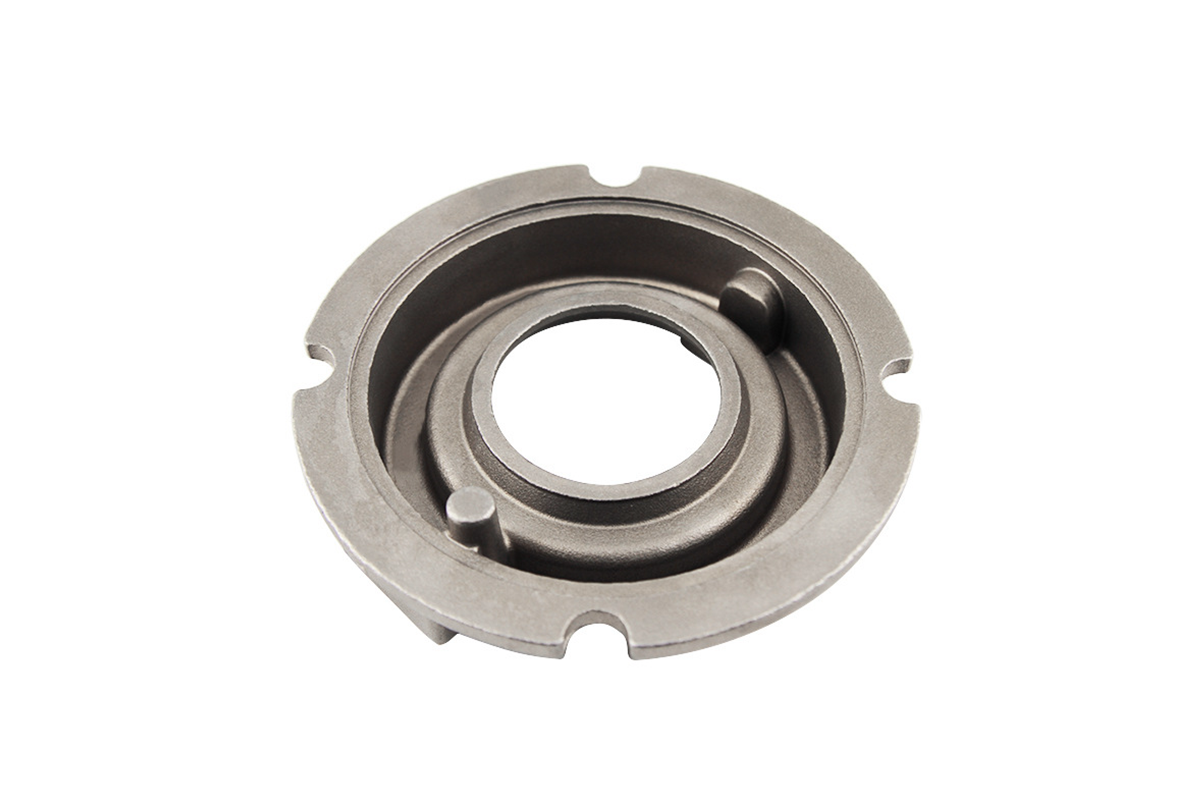
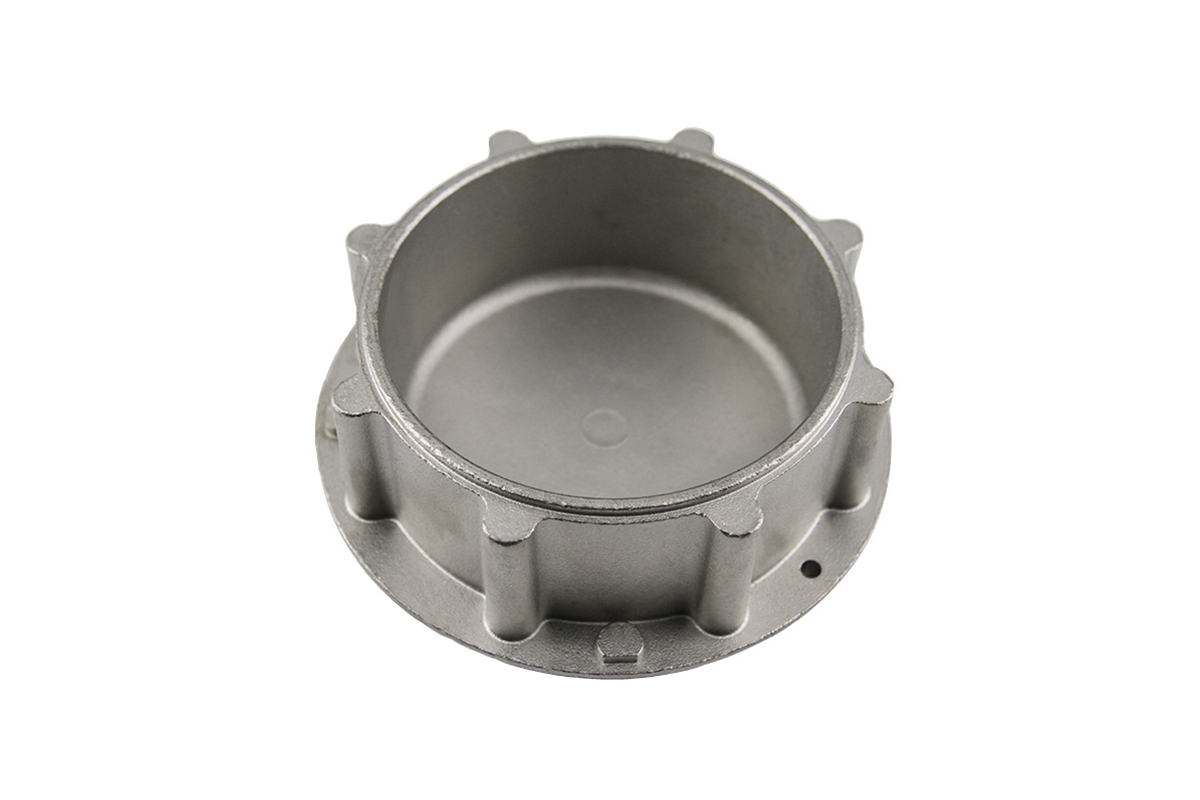
AISI 8620 (Low Carbon Alloy Steel) Investment Casting
AISI 8620, a low-carbon alloy steel, has a unique combination of toughness and wear resistance that sets it apart. This steel exhibits exceptional hardenability, allowing for precise control of its mechanical properties during the investment casting process. The low carbon content in AISI 8620 minimizes the risk of distortion and cracking during heat treatment, ensuring a high-quality final product.
In investment casting, AISI 8620 is prominent in crafting components that require durability and resilience. Its applications span various industries, including gears and camshaft components. For instance, AISI 8620's wear resistance ensures a longer operational life in producing gear components for power tools, while its toughness guarantees reliable performance under demanding conditions. The steel's ability to be intricately cast and retain its structural integrity makes it a prime choice in investment casting for numerous critical components across various industrial sectors.
Industries We Cover In Precision Casting
Neway mainly provides Die Casting Services, Investment Casting Services, Gravity Casting Services, and Sand Casting Services. Has experience in serving projects for well-known brand companies and has been used in multiple industries:

#Carbonsteelinvestmentcasting,#Investmentcastingmaterials,#AISI1010,#PlainCarbonsteel,#LowCarbonSteel,#AISI1020,#AISI1045,#MediumCarbonSteel,#AISI4140,#chromolysteel,#HighCarbonSteel,#AISI4340,#AISI52100,#Bearingsteel,#AISI8620
评论
发表评论