What Is Powder Compression Molding (PCM) Service?
Powder Compression Molding (PCM) Service is a sophisticated manufacturing process offered by Neway, involving the compression of powdered materials such as metals, plastics, ceramics, and composites within precisely engineered molds. This compression, performed under high pressure and often followed by sintering or curing, creates intricate, customized components with exceptional precision.
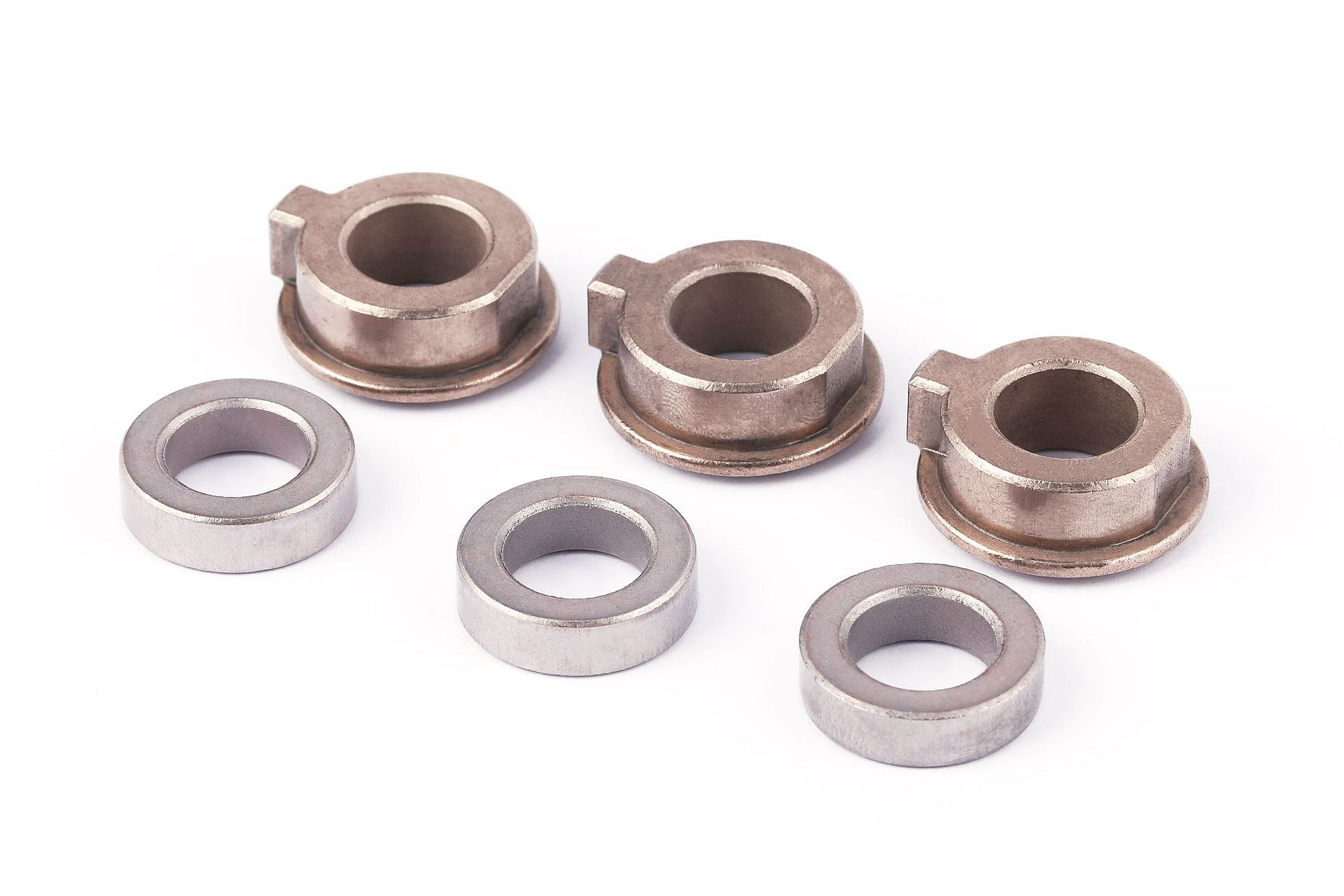
PCM service is mainly used to mass-produce small-medium-sized complex metal parts. The complexity of the PCM parts is lower than MIM parts. Ordinary powder compression-molded materials like Ceramic Powder, Cobalt Alloys, alloy Steel, Magnetic alloys, Stainless Steel, Titanium Alloy, Tool Steel, and Tungsten Alloy.
Powder Compression Molding (PCM) Operation Steps
1. Material Selection:
The material selection of PCM begins with carefully selecting powdered material, considering mechanical properties, thermal characteristics, and the intended application.
Neway's material engineers work closely with clients to select the most suitable material, ranging from metals (like aluminum, titanium, or steel) to ceramics or composite blends.
2. Powder Preparation:
The chosen powdered material undergoes rigorous preparation to ensure consistency.
Particle size, shape, and distribution are controlled to achieve the desired properties and uniformity. This step is crucial for successful PCM.
3. Mold Design:
Neway's engineers design precision molds tailored to the specific geometry and requirements of the desired component.
Considerations include parting lines, draft angles, and tolerances to ensure the final product's accuracy and quality. Powder compression molding (PCM) molds can not support the high complexity parts with undercuts.
4. Powder Loading:
The prepared powder is loaded into the mold cavity with meticulous attention to detail.
Automated systems may be used to ensure even distribution and optimal packing density, which is vital for the compression process.
5. Compression:
At the heart of PCM, this step involves subjecting the loaded mold to high-pressure conditions, often utilizing hydraulic presses.
The immense pressure compacts the powder, reducing its volume and causing the particles to adhere together, forming a solid component.
6. Sintering or Curing:
Depending on the material, the compacted powder may undergo either sintering (for metals and ceramics) or curing (for plastics).
Sintering involves heating the material below its melting point, allowing particles to fuse.
Curing typically employs heat and pressure to solidify plastic materials.
7. Cooling and Ejection:
After the sintering or curing, the component can cool within the mold to ensure structural stability.
Once cooled, the finished part is carefully ejected from the mold cavity. The mold design facilitates easy removal.
8. Post-Processing (If Necessary):
Depending on client requirements, additional post-processing steps may be performed.
It can include CNC machining to achieve tolerance, polishing to achieve a smooth or mirror surface, PVD (physical vapor deposition) to enhance the surface, or creating colors or heat treatment to achieve specific properties and dimensions.
9. Quality Control:
Neway maintains a stringent focus on quality control throughout the entire PCM operation.
Precise measurements and inspections are conducted to ensure that the final components meet the exacting standards set by Neway and its clients.
Features And Applications of PCM Parts
High Precision
PCM parts are renowned for their exceptional precision up to 0.002 inch (0.05mm). Combined with meticulously designed molds, the compression process ensures that components meet stringent dimensional tolerances and intricate geometrical requirements.
The high-precision powder compression molded parts can used in low or medium-precision applications without dimensional post-processing.
Material Versatility
PCM process is adaptable to various materials, including common metals (stainless steel, titanium, etc.), plastics, ceramics, and composite blends.
Powder compression molding service can also process hard and high melt point metals, such as tungsten alloys, tool steels, Etc. This versatility allows for tailoring material properties to specific application needs.
Cost-Efficiency
PCM minimizes material wastage due to its near-net-shape manufacturing approach. Reduced material consumption translates to cost savings, making it an economically viable option.
Customization
PCM parts can be customized to meet precise requirements. Mechanical properties, surface finishes, and dimensional accuracy can be finely tuned to suit specific applications.
Consistency
The controlled process parameters of PCM lead to consistent part quality. This reliability is crucial in applications where uniformity is paramount.
Complex Geometries
PCM excels in producing components with complex and intricate shapes, including undercuts and fine details. It offers design freedom that may be challenging with other manufacturing methods.
Material Density
The high-pressure compression in PCM results in high material density, enhancing the mechanical properties of the finished parts, such as strength and durability.
Process Comparison
Metal Injection Molding (MIM) vs. Powder Compression Molding (PCM)
The metal injection molding (MIM) process, known for its exceptional precision and complexity in handling metals and alloys, is a go-to choice for small to medium-sized, intricately designed metal components. Its strength is producing parts with complex geometries, including fine details, undercuts, and thin-walled structures. With precision tolerances typically within ±0.005 inches (±0.127 mm) or better, MIM is preferred for high-accuracy applications. However, MIM's cost-effectiveness shines in high-volume production due to economies of scale, while the initial tooling and material costs can be relatively high. MIM parts often require minimal post-processing, thanks to the inherent precision of the process.
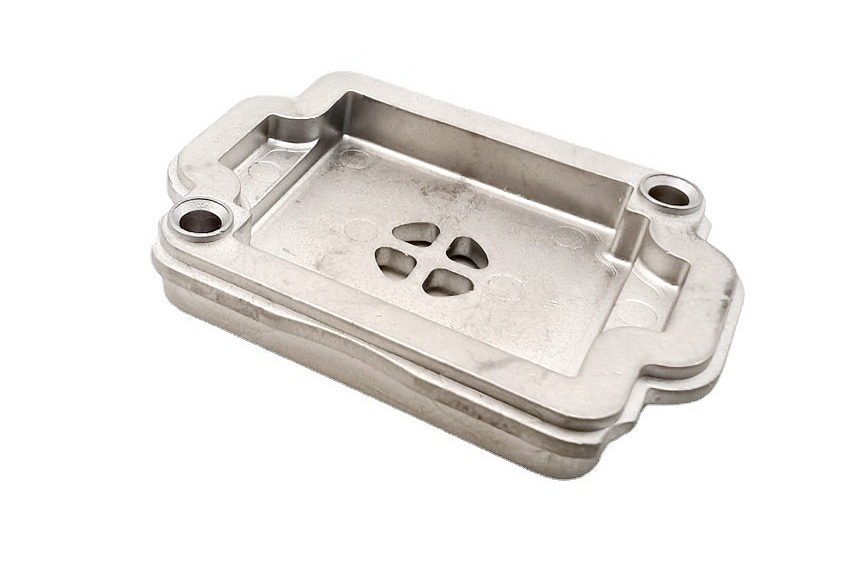
The powder compression molding (PCM) process is celebrated for its versatility in handling a broader range of materials, including metals, plastics, ceramics, and composites. This flexibility allows it to cater to diverse industries and applications. While PCM can achieve high precision and tight tolerances similar to MIM, it offers cost-effective solutions for smaller production runs. With generally lower initial tooling costs, PCM is accessible to various projects. However, depending on material properties and application requirements, some PCM parts may require post-processing, such as machining or surface finishing.
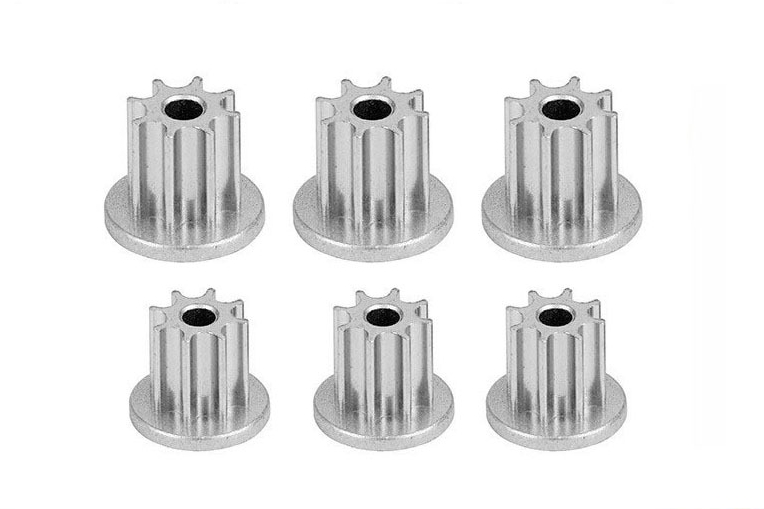
The choice between Metal Injection Molding (MIM) vs. Powder Compression Molding (PCM) depends on several factors, including material requirements, part complexity, production volume, and budget considerations. MIM is a top contender for high-volume, intricately designed metal parts with high initial cost. At the same time, PCM offers material versatility, flexibility in production quantities, and cost advantages for smaller to medium runs with lower initial costs. Both processes play critical roles in modern manufacturing, ensuring that a wide array of components meets the demands of various industries and applications.
Investment Casting vs. Powder Compression Molding (PCM)
The investment casting process, known as lost wax casting, is one of the precision casting processes and is renowned for producing intricate and highly detailed metal components with exceptional surface finishes. It is a versatile process that caters primarily to metals, especially alloys, such as stainless steel, aluminum, and titanium. Investment casting is ideal for applications where design intricacy and aesthetic appeal are paramount, such as aerospace, jewelry, and art casting. However, it can be less cost-effective for high-volume production due to the time-consuming nature of the process and material costs, making it better suited for smaller batch sizes or specialized parts.
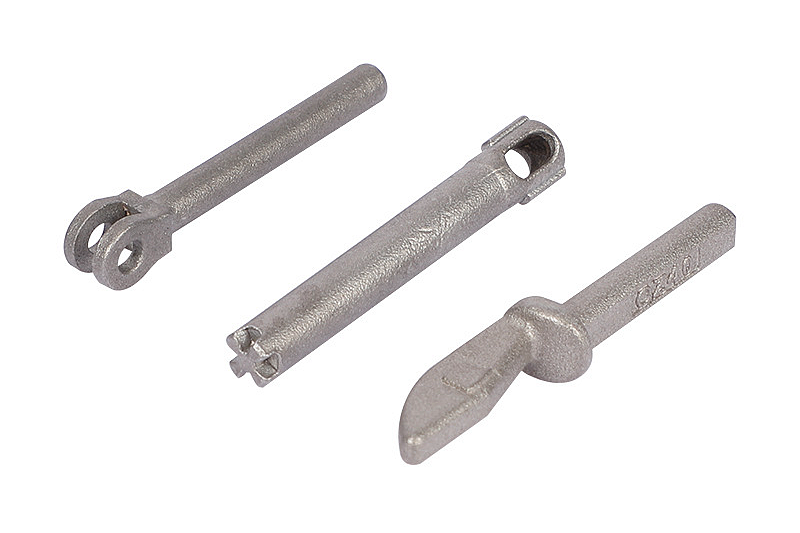
The powder compression molding (PCM) process is versatile, encompassing various materials, including metals, plastics, ceramics, and composites. It excels in producing components with precision and can handle complex geometries. PCM offers advantages in material versatility, cost-effectiveness, and flexibility in production quantities. It is particularly well-suited for applications where dimensional accuracy and versatility across different material types are crucial, such as automotive, electronics, and industrial machinery. Additionally, PCM often involves lower initial tooling costs compared to investment casting.
The choice between investment casting vs. PCM hinges on specific project requirements. Investment casting is favored for its ability to create intricate metal parts with superb surface finishes, making it suitable for specialized applications. In contrast, PCM offers versatility across materials, cost advantages for smaller production runs, and precision in a broader range of applications, making it a versatile choice for various industries and component types.
Applicability of Powder Compression Molding (PCM) process
The Powder Compression Molding (PCM) process is highly applicable across various industries and applications due to its versatility and ability to work with various materials.
Automotive Industry: PCM manufactures engine parts, transmission components, and chassis parts. Its precision and material versatility make it valuable for enhancing vehicle performance and reducing weight.
Aerospace and Defense: In these critical sectors, PCM produces components like aircraft parts, missile casings, and radar components. Its precision and ability to handle a variety of materials are crucial for aerospace and defense applications.
Electronics: PCM is used in the electronics industry to create components like heat sinks, connectors, and enclosures. Its material versatility allows for tailored solutions in electronic component manufacturing.
Medical Devices: In the medical field, PCM manufactures intricate and customized components for devices such as implants, surgical instruments, and diagnostic equipment.
Industrial Machinery: PCM contributes to constructing machinery components with high precision and durability. It includes gears, bearings, and specialized industrial tools.
Renewable Energy: PCM parts play a role in renewable energy applications, such as wind turbines and solar panel components. Its high material density and customization capabilities enhance performance and longevity.
Consumer Products: PCM parts are employed in various consumer goods, from high-end watches to kitchen appliances. Their precision and aesthetic appeal make them suitable for enhancing product quality and design.
Oil and Gas: In the oil and gas sector, PCM parts are used in critical equipment such as valves, pumps, and drilling components. Their durability and resistance to harsh environments are advantageous.
Telecommunications: PCM parts contribute to the telecommunications industry by providing components for network infrastructure, including antennas, waveguides, and connectors.
Custom and Prototype Parts: PCM is valuable for producing custom and prototype parts across industries. Its flexibility allows for quick iteration and customization.
In summary, Powder Compression Molding (PCM) is a versatile manufacturing process with broad applicability across various industries and applications. Its versatility, precision, and ability to handle complex geometries make it a valuable choice for producing a wide range of components, from critical aerospace parts to intricate medical devices and consumer products. Its suitability for low and high-production quantities adds to its appeal in diverse manufacturing scenarios.
What We Can Offer In PCM?
Neway is a custom parts manufacturer with 30 years of experience. As a powder compression molding (PCM) supplier, we offer one-stop service from design to production:
1. Consultive Design Service: You are welcome to consult our material and design engineers from the beginning of the project. We provide free services, including material selection advice, process advice, structural design advice
2. Mechanical Design And Data Copying: We conduct mechanical design based on the product requirements as you provide or copy parts' data based on your samples and create highly feasible production drawings for production.
3. Rapid Prototyping: Neway can conduct prototype testing through CNC machining, 3D printing, and rapid molding.
4. On-demand Manufacturing: Neway supports on-demand customization without MOQ to minimize the initial cost of product development.
5. Simple Assembly And Testing: Hardware assembly capabilities include basic soldering, fastening, snap-fit, and Interlocking. Prototype testing like dimensional and tolerance testing, fit and form testing, durability, and wear testing.
评论
发表评论