What is Thin Wall In Mim?
A thin wall refers to having a shallow thickness or narrow cross-section compared to an object or structure's overall size or length. In manufacturing and engineering, "thin wall" refers to components or parts with skinny and delicate sections compared to their dimensions.
Thin wall components are typically characterized by walls, surfaces, or features significantly thinner than the rest of the part. These thin sections are crucial for various applications, especially in industries such as Consumer Electronics, Telecommunication, and Lighting Solutions. Thin wall parts offer benefits like reduced weight, improved heat dissipation, and space-saving designs.
MIM Process Thin Wall Capability
MIM can achieve thin wall capabilities with thicknesses as low as 0.5mm (20 mils) or even thinner in some cases. It is particularly crucial in industries such as Consumer Electronics, Telecommunication, and Lighting Solutions, where compact and lightweight components are often required.
Applications Of Thin Walled MIM Parts
Thin-walled Metal Injection Molding (MIM) parts find various applications across several industries, including Consumer Electronics, Telecommunication, Lighting Solutions, and more. These thin-walled components offer unique advantages such as lightweight design, intricate geometries, and high precision. Here are some specific applications:
Consumer Electronics
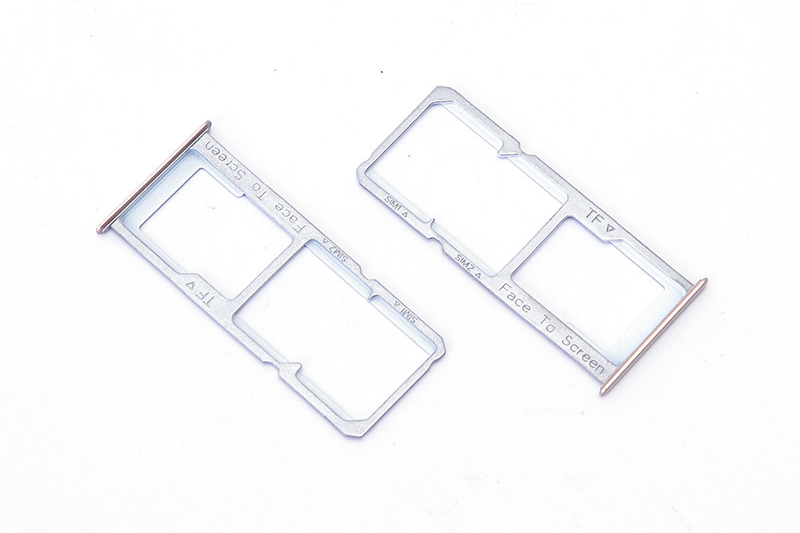
Smartphone Casings: Thin-walled MIM parts are commonly used to manufacture smartphone casings. These parts offer a sleek and lightweight design while accommodating various electronic components.
Laptop Housings: Laptops require thin and lightweight housings to maintain portability. MIM parts provide the necessary strength and thin profiles for these applications.
Wearable Technology: Thin walls in MIM parts are essential for wearables like smartwatches, ensuring comfort and aesthetics.
Telecommunication
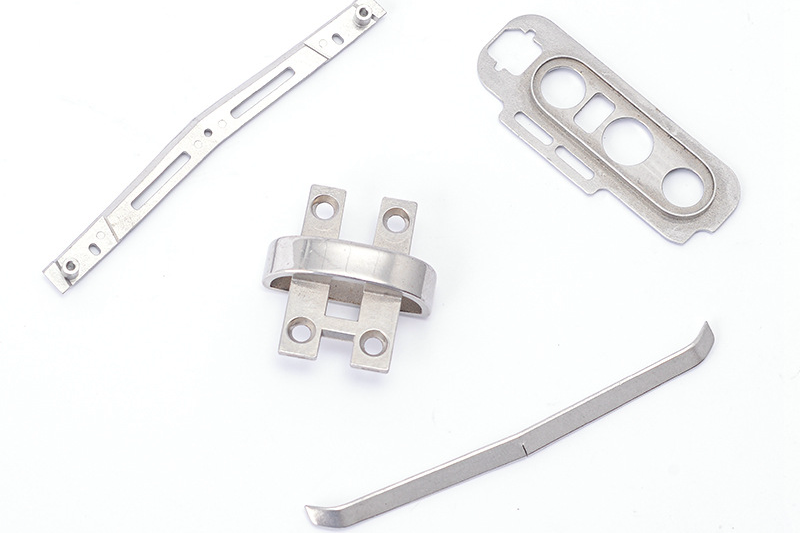
Connector Components: Telecommunication devices use connectors with precise, thin-walled parts for signal transmission. MIM parts ensure reliable connections.
Antenna Components: Antenna housings and components benefit from thin walls for efficient signal transmission and reduced weight.
Lighting Solutions
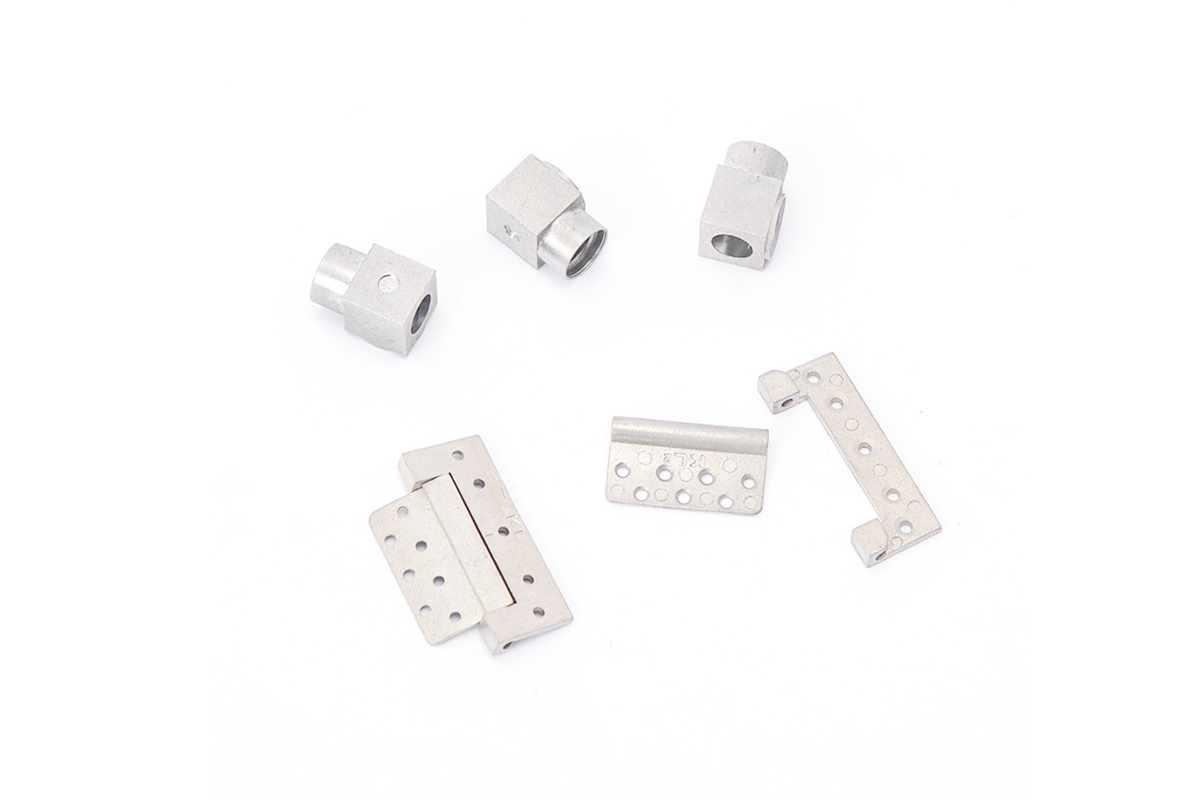
LED Heat Sinks: LED lighting often requires efficient heat dissipation. Thin-walled MIM heat sinks provide effective cooling solutions while maintaining lightweight designs.
Light Fixture Housings: Thin-walled MIM parts are used for lighting fixtures' housing and mounting components, contributing to aesthetic and functional designs.
Medical Devices
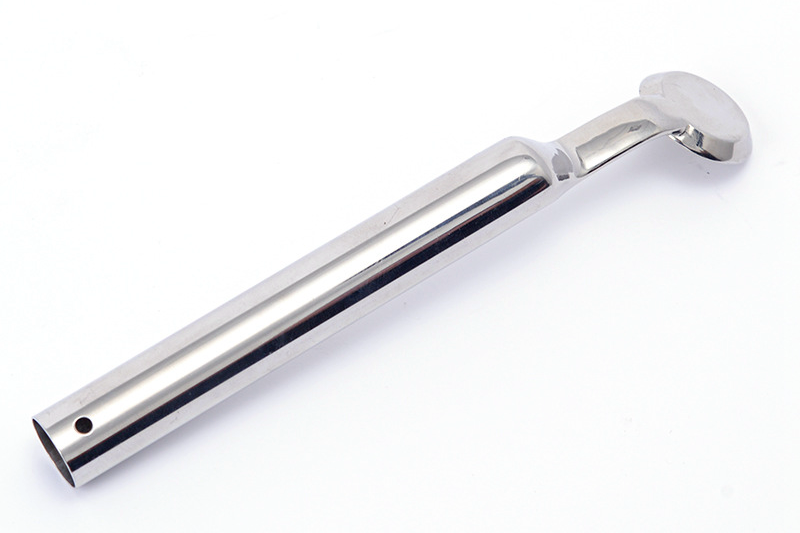
Implantable Devices: Some medical implants, such as pacemaker cases, benefit from thin-walled MIM parts to minimize intrusion and optimize biocompatibility.
Surgical Instruments: Thin-walled components produce delicate surgical instruments, ensuring precision and ease of use.
Aerospace
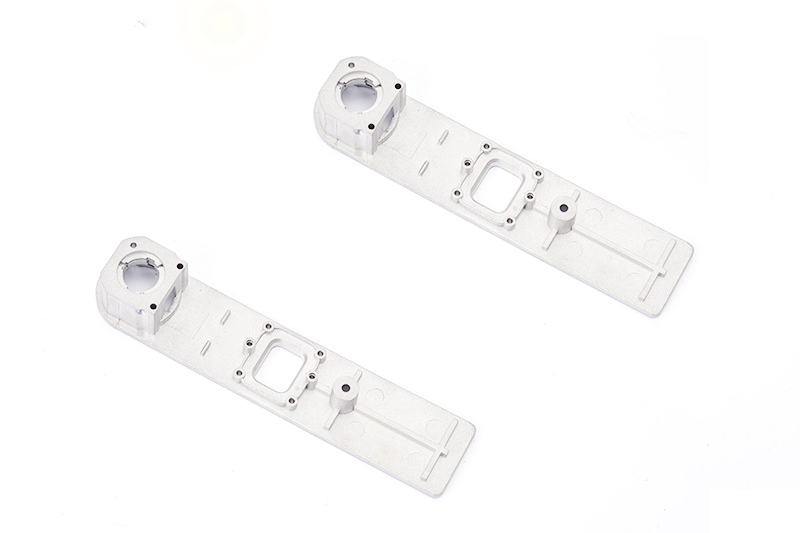
Satellite Components: Thin-walled MIM parts are employed in satellite construction for lightweight yet durable components, contributing to lower launch costs.
Interior Components: Aircraft interiors, including seating and cabin components, benefit from thin-walled MIM parts to reduce weight and enhance passenger comfort.
Automotive

Engine and Transmission Parts: Thin-walled MIM parts are utilized in critical engine and transmission components to reduce weight and improve fuel efficiency.
Sensor Housings: Automotive sensors require precise and lightweight housings, which thin-walled MIM parts can provide.
Neway In House Thin-Walled Parts Manufacturing
Typically, the thin-wall capability of the metal injection molding (MIM) or powder compression molding (PCM) process is 0.5mm. But Neway can produce MIM blanks up to 0.35mm according to the product's specific needs. The final parts, after post-processing, such as CNC machining or fine polishing, can achieve a wall thickness of 0.3mm without MIM defects.
Try Neway For Free
Neway provides free Consultative Design and rapid prototyping services for valid projects for free.
1. CNC Machining Prototyping Service
Correctly fill in your information and send it to our engineer to get free service.
评论
发表评论