MIM-Haynes 25 Sintered Parts Manufacturer
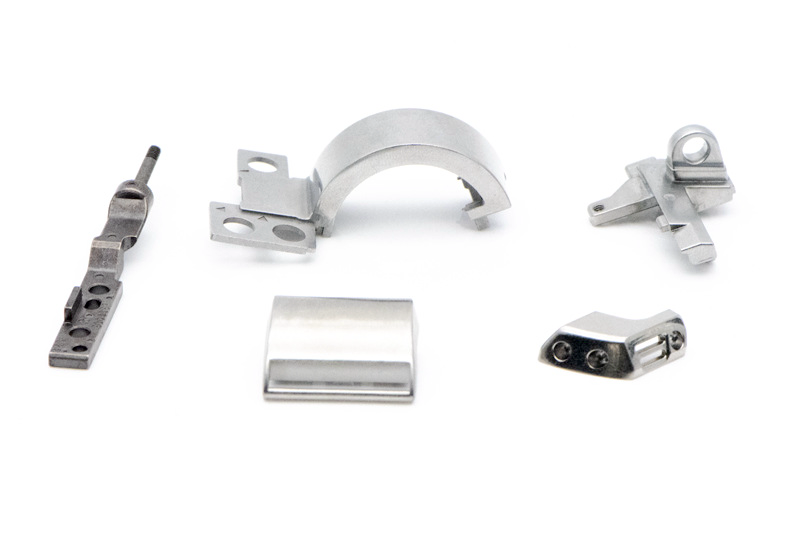
Sintered Haynes 25 MIM Parts For Telecommunication
Sintered Haynes 25 MIM parts are components made from Haynes 25, a high-temperature alloy renowned for its strength, corrosion resistance, and durability. These parts are manufactured using the Metal Injection Molding (MIM) process, which allows for precise and complex geometries.
Typical applications of sintered Haynes 25 MIM parts in telecommunication accessories include:
Connector Components
Antenna Mounts
Heat Dissipation Components
Waveguide Components
Satellite Systems
Typical Properties of MIM-Haynes 25 Cobalt Alloy
Download PDF: Cobalt Alloy MIM-Haynes 25 Datasheet |
---|
MIM-Haynes 25 Chemical Composition
Nickel (Ni) | Cobalt (Co) | Chromium (Cr) | Iron (Fe) | Molybdenum (Mo) | Tungsten (W) | Titanium (Ti) | Aluminum (Al) | Carbon (C) | Boron (B) |
---|---|---|---|---|---|---|---|---|---|
47.5% | 20.0% | 15.5% | 5.5% | 4.0% | 3.0% | 1.5% | 0.4% | 0.03% | 0.015% |
MIM-Haynes 25 Physics and Mechanical Properties
Status | Tensile Strength (MPa) | Yield Strength (MPa) | Impact Strength (J) | Hardness (HRC) | Young's Modulus (GPa) | Poisson's Ratio | Elongation (%) | Density (g/cm³) |
---|---|---|---|---|---|---|---|---|
As Sintered | 850 | 700 | 30 | 35 | 200 | 0.3 | 10 | 8.3 |
MIM-Haynes 25 Injection Molded Applications
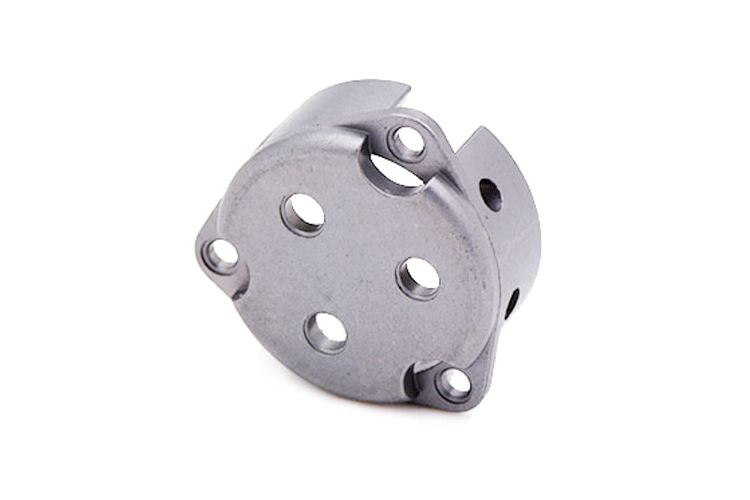
MIM-Haynes 25 injection-molded Connector Components
MIM-Haynes 25 injection-molded connector components offer a range of invaluable benefits that make them essential in various industries, particularly telecommunications and electronics. Firstly, these components boast exceptional corrosion resistance, a crucial attribute for connectors often exposed to moisture, humidity, and corrosive environments. Haynes 25's resistance to corrosion ensures that connectors maintain their electrical conductivity and structural integrity over time, reducing the risk of signal degradation and system failures.
Secondly, Haynes 25 connector components exhibit remarkable mechanical strength and durability. Their ability to withstand high mechanical stresses and extreme temperatures ensures their longevity and reliability in demanding applications. Whether in aerospace, automotive, or telecommunications, these components provide secure and stable connections, minimizing the risk of electrical disruptions.
MIM-Haynes 25 Injection molding Antenna Mounts
MIM-Haynes 25 injection-molded antenna mounts provide various benefits that make them vital components in telecommunications and other industries. Firstly, these mounts exhibit exceptional corrosion resistance, a crucial feature when considering their outdoor applications. Haynes 25's resistance to corrosion ensures that antenna mounts maintain their structural integrity, even when exposed to moisture, temperature variations, and harsh weather conditions.
Secondly, Haynes 25 antenna mounts offer robust mechanical strength and durability. They withstand the mechanical stresses and vibrations that antennas experience during operation. The high tensile strength of Haynes 25 ensures the stability of the entire antenna system, preventing structural failures and signal disruptions.
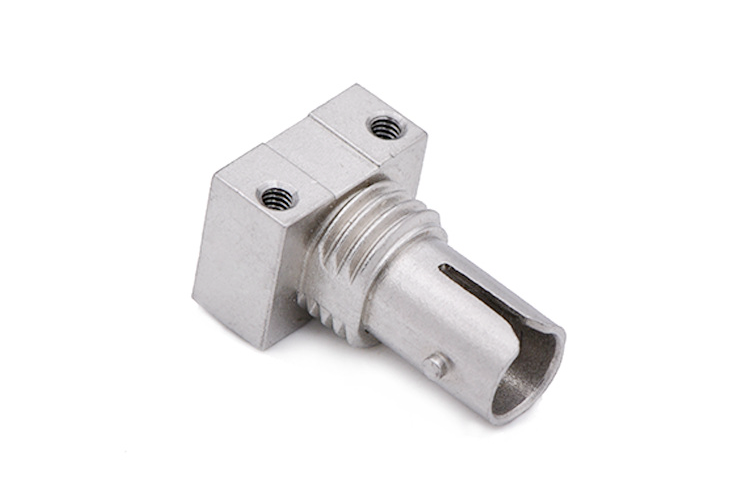
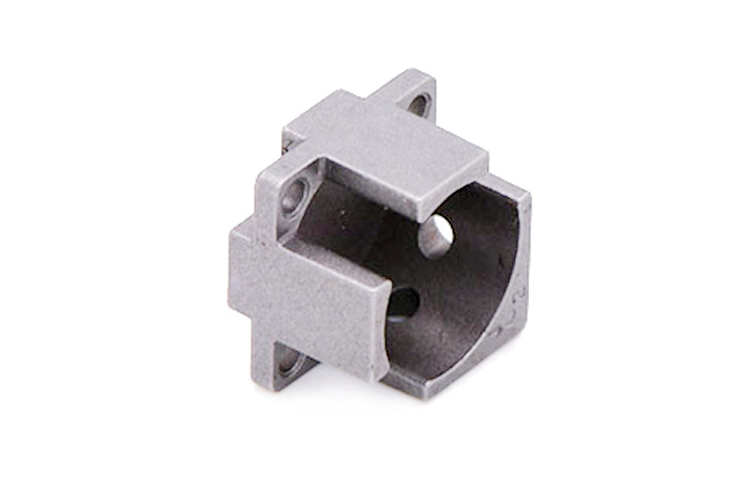
MIM-Haynes 25 MIM sintering Heat Dissipation Components
MIM-Haynes 25 MIM sintered heat dissipation components offer indispensable benefits for industries that rely on efficient thermal management. Firstly, these components excel in heat resistance, making them ideal for dissipating excess heat generated by electronic devices and industrial machinery. Haynes 25's ability to withstand high temperatures without compromising its structural integrity ensures reliable and continuous heat dissipation.
Secondly, Haynes 25 heat dissipation components possess remarkable corrosion resistance. Environmental factors and moisture are exposed daily in various applications, such as outdoor electronics and industrial machinery. The corrosion resistance of Haynes 25 ensures that heat dissipation components remain effective over time, reducing maintenance needs and enhancing the longevity of the systems they protect.
MIM-Haynes 25 Metal Injected Waveguide Components
MIM-Haynes 25 metal-injected waveguide components offer a range of pivotal benefits for high-performance telecommunications and signal transmission systems. Firstly, these components excel in corrosion resistance, a critical feature when considering their role in waveguide systems exposed to outdoor and harsh environments. Haynes 25's resistance to corrosion ensures that waveguide components maintain their structural integrity and signal transmission properties over time, reducing the risk of signal degradation and system failures.
Secondly, Haynes 25 waveguide components provide exceptional mechanical strength and durability. They withstand the mechanical stresses, temperature variations, and vibrations that waveguide systems may experience during operation. The high tensile strength of Haynes 25 ensures the stability of the entire waveguide system, preventing signal disruptions and ensuring continuous data transmission.
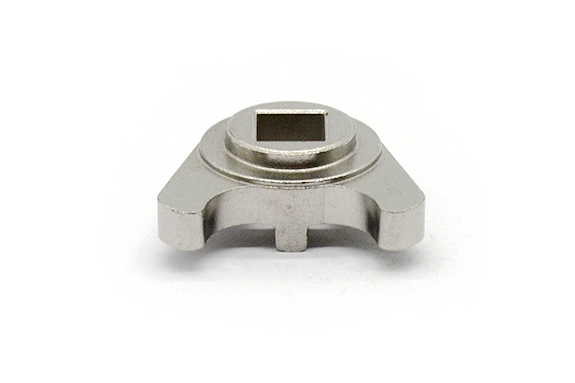
Consultative Design Services
Neway Custom Metal Injection Molding Service provides free Consultative Design Services throughout the process. It includes all processes from your design stage to mass-produced finished products.
1. Material selection Consult
2. Structural design service
3. Mold design service
Contact us now if you are interested.
评论
发表评论