Neway's Role in Powder Metallurgy
As a trailblazer in Powder Metallurgy and Metal Sintering, Neway has carved a niche in producing Metal Injection Molding (MIM) parts. With a rich legacy and a relentless pursuit of innovation, Neway has consistently delivered precision-engineered sintered metal parts to various industries. At the same time, Neway has summed up the experience in 30 years of custom sintering metal parts manufacturing career and has made outstanding achievements in the fields of Self-Lubricating Sintered Bearings, tungsten alloy pressing and sintering forming, and the manufacture of porous metal parts.
Neway's Contribution to Powder Metallurgy
Neway's prowess in Powder Metallurgy is evident in its ability to produce intricate, high-precision parts in large volumes. The company's proficiency in choosing the suitable metal powder, molding it into the desired shape, and executing the sintering process to form a solid piece sets it apart in the industry. More importantly, Neway cooperates with many world-famous universities to develop metal powder formulas. Metal powders can be prepared according to the customer's unique needs, and mass production can be realized, such as manufacturing armor-piercing warheads, ultra-high temperature components, etc.
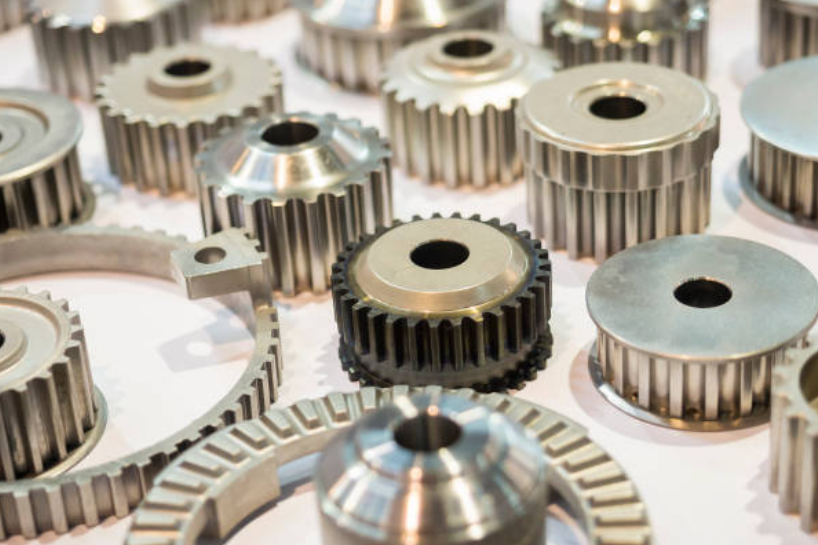
Understanding Powder Metallurgy Process and Metal Sintering
Selection of Metal Powder
The journey of powder metallurgy begins with selecting the appropriate metal powder. How to choose the right MIM materials for your custom parts? The choice of metal powder is instrumental in determining the properties of the final product, making it a crucial step in the MIM parts production process. Of course, you can also customize the metal sintered powder according to the product performance you need to achieve. But the premise is that you understand the types and properties of standard metal sintering powders.
Forming and Shaping
Once the suitable powder is chosen, it is compacted into the desired shape using a die press. The pressure applied and the duration of pressing are tailored to the powder type and the final product's specifications. Or by injection molding after mixing with a binder. There are two powder molding processes: powder pressing and injection molding. The specific molding method you choose depends on the metal powder you choose, the structure of the product, and the desired product performance.
Sintering
The compacted powder is then subjected to the sintering process. This involves heating the powder below its melting point, enabling the particles to bond and form a solid piece. We usually use pressureless sintering or hot pressing sintering methods to sinter the powdered parts. The duration and temperature of heating are adjusted based on the powder type and the final product's requirements. Regardless of the molding method, there are tiny gaps between the metal powders. This means that when the sintering temperature is close to the melting point of the metal powders, these tiny voids will disappear as the powder is combined. In layman's terms, the pressed or injection molded metal powder parts will shrink slightly in sintering. We call it the sintering shrinkage ratio. The smaller the shrinking ratio, the higher the accuracy of the final powder metallurgy part.
Decoding the Furnace Zones in the Sintering
Pre-heating
This is the initial phase of the sintering process. The compacted powder is gradually heated to prepare it for the sintering phase, effectively eliminating any residual lubricants in the powder.
Sintering (Hot Zone)
This is the crux of the sintering process. The temperature is meticulously controlled to reach just below the melting point of the primary metal in the powder. This bonds the metal particles, creating a solid, sintered metal part. According to the powder material or different production requirements, we will choose continuous sintering and batch sintering furnaces for sintering.
Cooling
Post-sintering, the parts are gradually cooled. This critical step allows the newly formed part to solidify and acquire its final properties.
Understanding the Metal Sintering Atmospheres
Nitrogen-Hydrogen Atmosphere: This is commonly used in sintering, particularly for stainless steel and other alloys. The nitrogen-hydrogen atmosphere aids in preventing oxidation and enhances the sintering process.
Hydrogen Atmosphere: A pure hydrogen atmosphere is employed for sintering certain metals. It acts as a reducing agent, removing oxides and promoting the sintering process.
Vacuum: Some sintering processes are carried out in a vacuum to prevent oxidation and other reactions that could affect the quality of the final sintered products.
Dissociated Ammonia: This is used as a protective atmosphere in some sintering processes. It prevents oxidation and assists in the removal of lubricants.
Endothermic Gas Atmosphere: This is a commonly used atmosphere in sintering. It provides a controlled environment that promotes the sintering process.
Applications and Innovation of MIM Parts
Sintered Gears
Neway excels in producing high-quality sintered gears known for their superior performance and durability. These gears find extensive use in various applications, including automotive and industrial machinery. There are many methods to manufacture gears, such as CNC Milling gears, Gear shaping machine machining, metal injection molding gears, etc. These methods have their advantages and disadvantages. How to choose the most suitable gear manufacturing method is what a professional purchaser should consider.
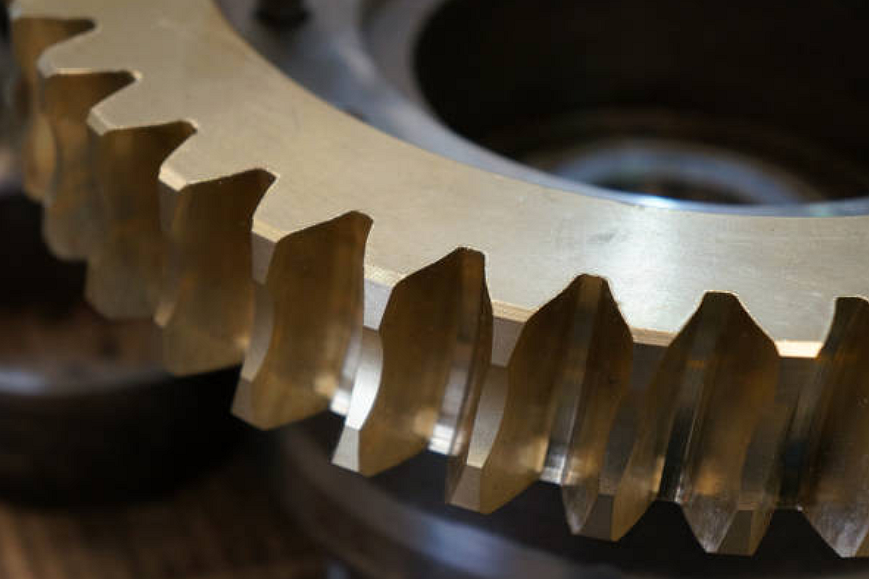
Sintered Bearings
Neway's sintered bearings are renowned for their high load capacity and exceptional wear resistance. They are utilized in various applications, including automotive, aerospace, and industrial machinery, such as metal injection molding oil-impregnated bearings and alumina Ceramic Bearings, which are unmatched by other gear manufacturing processes.
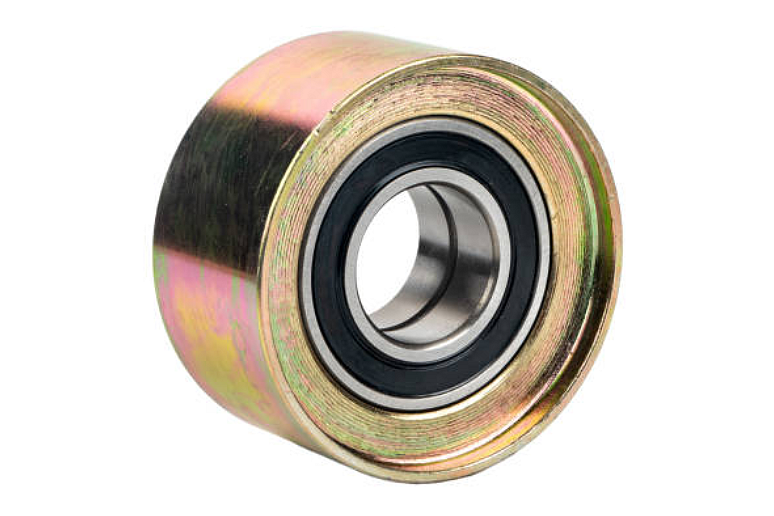
Soft Magnetic Sintered Components
Neway produces soft magnetic sintered components that are used in various applications. Soft magnetic sintered components refer to parts made from powder metallurgy processing of ferromagnetic metallic materials with low coercivity and high magnetic permeability, such as Iron-silicon alloys, Iron-nickel alloys, and Iron-cobalt alloys, Ferrites. Typical applications include transformer cores, ductors and chokes, Electromagnetic shields, Motors and actuators, Sensors, Radiofrequency (RF), Etc.
Filters and Porous Metallic Components
Neway also specializes in the production of filters and porous metallic components. These components have a wide range of applications, including filtration systems and fluid control systems.
Use of Tungsten in Powder Metallurgy
Neway has been pioneering the use of tungsten in powder metallurgy. Tungsten's unique properties make it ideal for various applications, including electrical contacts and cutting tools.
Copper and Graphite Alloys
Neway has been innovating in the production of copper and graphite alloys. These alloys have unique properties ideal for various applications, including electrical and thermal conductivity.
The Merits of Powder Metallurgy
Cost-Effective Manufacturing: Powder metallurgy is a cost-efficient method for producing complex metal parts. It minimizes the need for extensive machining and finishing, reducing the production cost.
Versatility in Metal and Alloy Choices: Powder metallurgy allows for the use of a wide range of metals and alloys, offering greater flexibility in material selection.
Reduced Scrap Loss: Powder metallurgy generates less waste than other manufacturing methods, reducing scrap loss.
Creation of MIM Parts Complexity: Powder metallurgy enables the creation of complex shapes that would be challenging to achieve with other manufacturing methods.
High-Dimensional Precision: Parts produced through powder metallurgy have high dimensional precision, ensuring they meet the exact specifications required.
Reliability and Repeatability: Powder metallurgy is a reliable and repeatable process, making it ideal for large-scale production.
Self-Lubrication: Some parts produced through powder metallurgy, such as bearings, have self-lubricating properties.
Creation of Unique Isotropic Materials: Powder metallurgy can create unique isotropic materials with the same properties in all directions.
Green Technology: Powder metallurgy is green as it produces less waste and uses less energy than other manufacturing methods.
Vibration Damping: Some parts produced through powder metallurgy have vibration-damping properties, making them ideal for applications where noise reduction is required.
Post-Processing Operations in MIM
Coining and Resizing
After sintering, some parts may require coining or resizing after sintering to achieve the desired dimensions or enhance their mechanical properties.
Steam Treatment
This secondary operation improves the sintered parts' surface hardness and wear resistance.
Heat Treatment
Heat treatment is used to enhance the mechanical properties of the sintered parts, such as their hardness, toughness, and strength.
Vacuum or Oil Impregnation
This process is used to improve the density and strength of the sintered parts.
Structural Infiltration
This process is where a secondary metal infiltrates the sintered part to improve its properties.
Resin or Plastic Impregnation
This process seals the sintered parts' pores or enhances their mechanical properties.
CNC Machining
Some sintered parts may require CNC machining to achieve the desired dimensions or to create specific features.
Grinding
Grinding enhances the sintered parts' surface finish or achieves the desired dimensions.
Surface Treatments
Various surface finishing processes, such as polishing, PVD plating, or coating, may enhance the sintered parts' appearance or performance.
Developments and Trends in Powder Metallurgy
The realm of sintering and powder metallurgy is in a constant state of evolution, with new developments and trends emerging regularly. Some key trends include using new materials, developing new sintering techniques, and increasing use of sintering in additive manufacturing or 3D printing. There is also a growing focus on sustainability, with efforts to make the sintering process more energy-efficient and environmentally friendly. As a leader in the field, Neway is committed to staying at the forefront of these developments, continually innovating and improving its processes to deliver the highest quality products to its customers.
评论
发表评论