Metal Injection Molding (MIM) process is a manufacturing process that marries the versatility of plastic injection molding with the strength and resilience of powder metallurgy. MIM offers a unique proposition for mass production, enabling the creation of complex, precision parts across various industries. This blog aims to comprehensively understand the MIM process, its pros and cons, and the critical considerations for mass production.
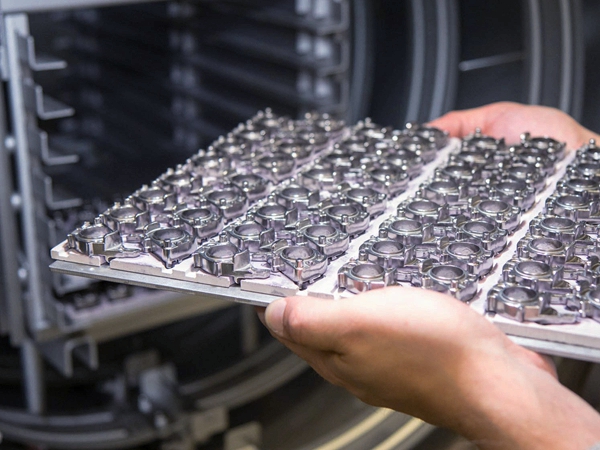
What is Metal Injection Molding
Metal Injection Molding (MIM) is a transformative manufacturing technology that has been shaping the industrial landscape for decades. But what exactly is MIM, and how has it evolved? Let's delve into MIM's definition, history, and role in various industries.
Definition and History
MIM is a process that combines the high-volume capability of injection molding with the benefits of metallic materials. It involves mixing metal powders with a binder to form a feedstock, which is then injected into a mold to create a green part. The binder is removed, and the part is sintered to achieve its final properties.
The roots of MIM can be traced back to the 1970s when the need for complex, high-volume metal parts began to grow. Over the years, advancements in material science and process control have significantly expanded the capabilities of MIM, making it a preferred choice for manufacturing precision metal parts.
The Role in Industries
MIM is crucial in various industries, including automotive, aerospace, medical, electronics, and consumer goods. Its ability to produce complex parts with high precision and excellent mechanical properties makes it ideal for applications where performance and reliability are paramount. MIM has many applications, from surgical instruments and automotive components to aerospace parts and electronic devices.
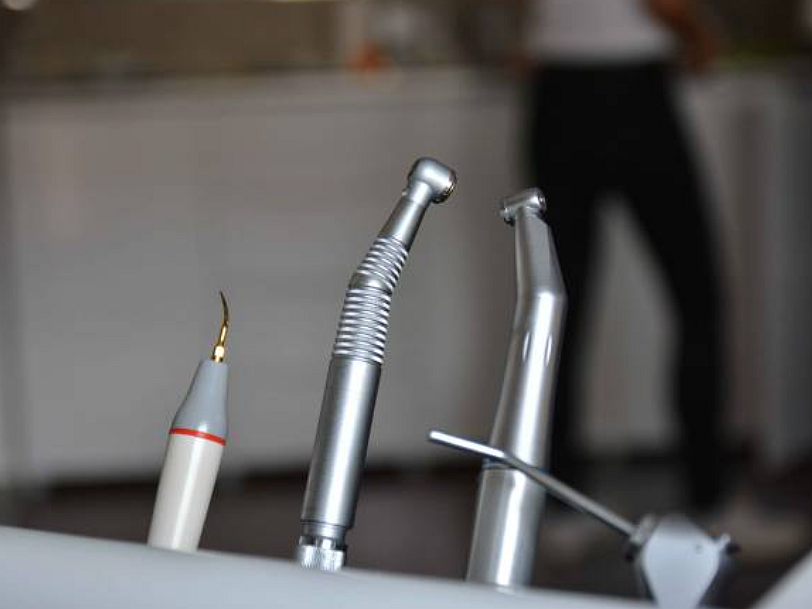
MIM Process Steps
The Metal Injection Molding (MIM) process is a multi-step procedure that transforms metal powders into solid, fully dense components. Each step in the process plays a crucial role in determining the quality and properties of the final product. Let's explore each of these steps in detail.
Feedstock Mixing
The MIM process begins with preparing the feedstock, a mixture of metal powders and a binder. The metal powders provide the material properties of the final part, while the binder facilitates the molding process. The feedstock must be thoroughly mixed to ensure a uniform distribution of the metal powders in the binder.
Injection Molding
The mixed feedstock is then heated and injected into a mold under high pressure, similar to the process used in plastic injection molding. The mold is designed to produce a green part with the final product's shape but is more significant to account for MIM shrinkage during sintering.
Debinding and Sintering
After the green part is removed from the mold, the binder is removed in debinding. It leaves behind a porous part, known as a brown part, composed mainly of metal powders. The brown part is then heated to a high temperature in a controlled atmosphere in a process called sintering. Sintering causes the metal particles to bond, forming a solid, fully dense part.
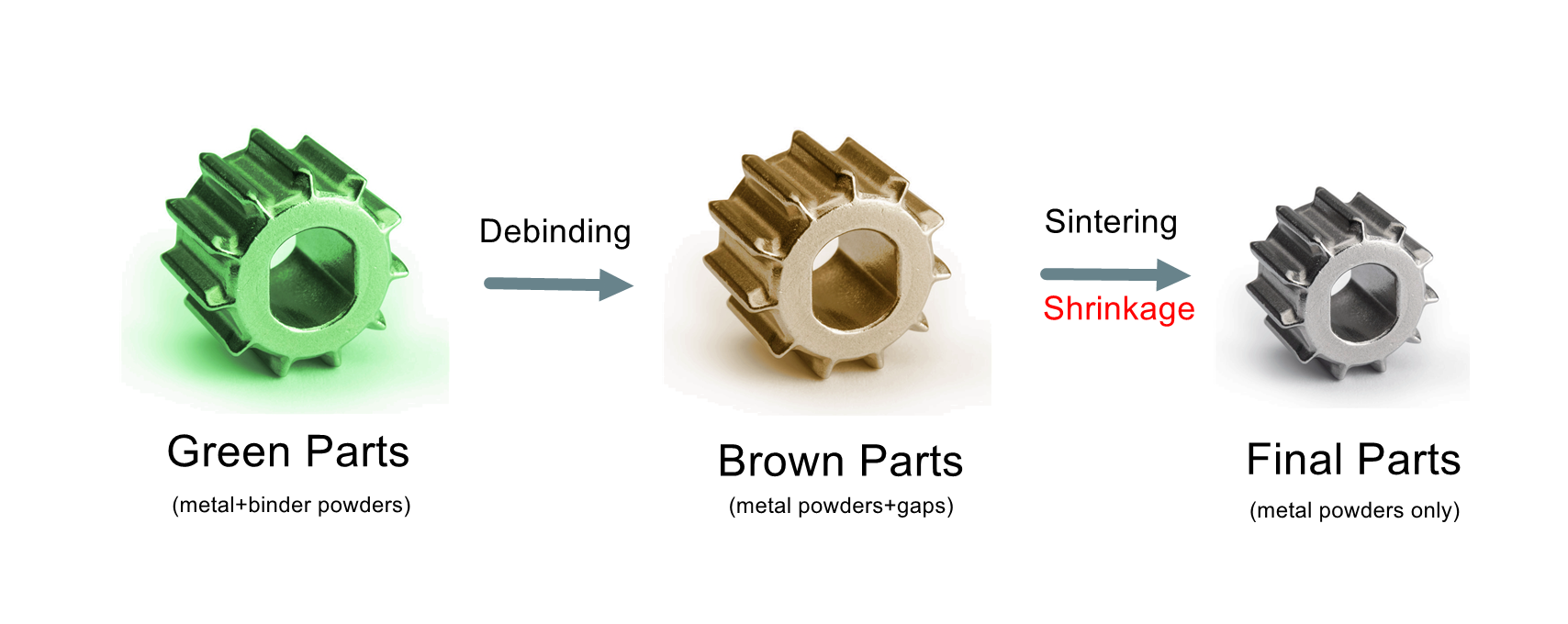
Shape Correction
Due to shrinkage during sintering, the final part may not have the exact dimensions of the mold. Therefore, shape correction processes, such as shape molding, machining, or polishing, may be necessary to achieve the desired dimensions and surface finish.
Advantages of MIM
MIM offers many advantages, making it a preferred choice for manufacturing complex, high-volume metal parts. Let's delve into these advantages and understand how MIM stands out.
High precision
MIM is renowned for its ability to produce parts with high precision. The process can achieve tight tolerances, typically within ±0.3% of the nominal dimension, making it ideal for applications that require high dimensional accuracy. The MIM process can achieve higher precision, especially for parts with relatively small dimensions.
High Complexity
MIM excels at producing complex parts that would be difficult or impossible to manufacture using traditional methods. The process can handle intricate geometries, thin walls, and fine details, providing designers with great design freedom. This is because the shape complexity of metal injection molding comes from the plastic injection molding process. As long as it is a shape that plastic injection molding can produce, metal injection molding can produce it.
Cost-effectiveness Compared to Other Processes
Regarding cost-effectiveness, MIM often outperforms other manufacturing processes, especially for the high-volume production of complex parts. To illustrate this, let's compare MIM with investment casting, another standard method for producing metal parts.
MIM vs. Investment casting
Let's take the production of a 10mm stainless steel 316l cube as an example:
Comparison Aspect | Metal Injection Molding | Investment Casting |
Product 10x10x10mm SS316L cube | 7.85 Gram | 7.85 Gram |
Mold Cost | 2000 usd (High) | 1000 usd (Medium) |
Material Cost | 0.06 usd/pc (Medium) | 0.04 usd/pc (Low) |
Molding Cost | 0.2 USD/pc (Low) | 0.35 USD/ pc (High) |
Other Cost | 0.1 USD/pc | 0.05 USD/pc |
Tolerance | High (0.3%) +/-0.03mm | Medium (0.5%)+/-0.05mm |
Productivity | 4000 pcs per day | 1000 pcs per day |
Total cost | 0.36 USD/pc | 0.44 USD/pc |
It is not difficult to see that the price of the two processes is the same when producing 12,500 10mm cubes, but once more than 12,500 production units, if you use MIM production, you can get better quality and higher precision cubes at a lower price.
As the table shows, while the mold cost for MIM can be higher, the molding cost is significantly lower, making it more cost-effective for high-volume production. Furthermore, MIM offers better tolerance and productivity than investment casting.
Wide Range of MIM Materials Selection
MIM supports a wide range of materials, from steels and stainless steels to rigid materials like tungsten carbide and unique materials like titanium alloys. This allows manufacturers to choose the material that best meets the application's requirements.
Hard Metal and High Melting Point Metal Forming
MIM can form complex and high melting point metals, such as Cobalt Alloys, Tungsten Alloy, and Tool Steel, which can be challenging to process using other methods. This opens up new possibilities for the production of high-performance parts.
Disadvantages of Metal Injection Molding
While MIM offers numerous advantages, it also has certain disadvantages that must be considered. One of the main drawbacks is the higher initial cost, which can be a barrier for low-volume production or companies with limited budgets. Let's break down metal injection molding costs to understand why the initial investment for MIM can be high.
Higher Initial Cost
MIM Mold Cost
The molds used in MIM are complex and require high precision, which makes them expensive to manufacture. However, these molds are durable and can produce many parts, offsetting the high initial cost over time.
MIM Material Cost
The cost of the metal powders used in MIM can be higher than the cost of bulk metals used in other processes. However, MIM offers the advantage of near-net-shape manufacturing, which can reduce material waste and lower the overall cost.
MIM Debinding Cost
Debinding is a critical step in the MIM process and can add to the overall cost. The debinding process requires specialized equipment and can be time-consuming, especially for parts with complex geometries.
MIM Sintering Cost
Sintering is another critical step in the MIM process that can add to the cost. Sintering requires high temperatures and controlled atmospheres, which require energy and specialized equipment. However, sintering is a batch process, so the cost per part decreases with larger batch sizes.
MIM Shaping Cost
Shape correction processes like mold shaping, CNC machining, or fine polishing may be necessary to achieve the desired dimensions and surface finish. These processes can add to the cost, especially for parts with complex geometries or tight tolerances.
MIM Post Process Cost
Post-processing steps, such as heat treatment, polishing, or PVD, can also add to the cost. However, these steps can enhance the properties of the final part and may be necessary to meet the application's requirements.
Despite these costs, MIM can still be cost-effective for the high-volume production of small complex parts, as the high initial cost can be spread over many parts.
MIM Parts Size Limitation
MIM is best suited for small to medium-sized parts. Usually, the size of MIM parts is most suitable for production within 2 inches (50mm). As the porous brown part collapses during sintering and forms the final product, a MIM shrinkage ratio varies from material to material. Neway can have MIM parts with a maximum size of 10 inches (250mm). The process becomes less efficient and more challenging for larger parts due to difficulties in achieving uniform density and handling the parts. However, advancements in MIM technology are gradually overcoming these limitations.
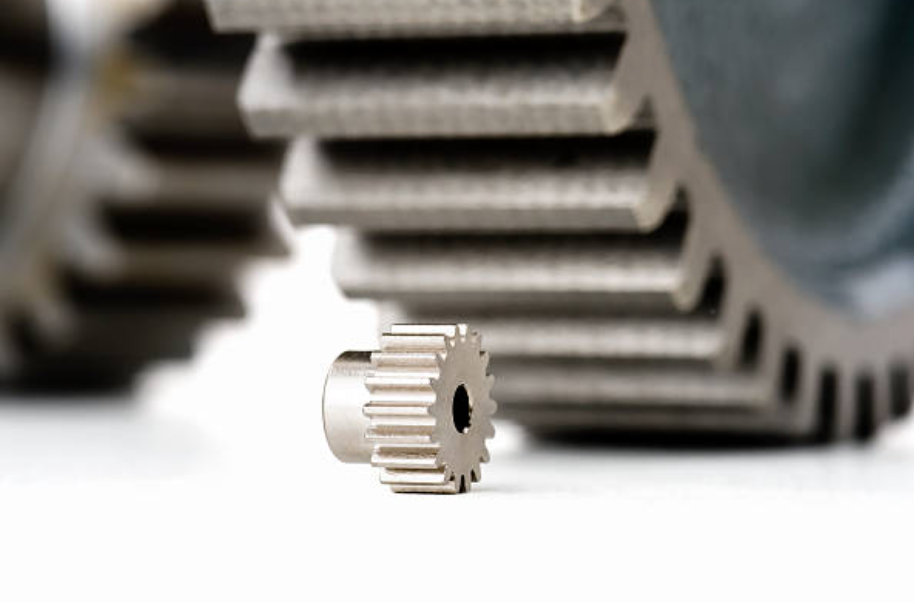
Challenges in the MIM Process
The MIM process involves several complex steps, each of which must be carefully controlled to ensure the quality of the final product. For example, the feedstock must be thoroughly mixed, the molding parameters must be optimized, and the debinding and sintering processes must be carefully controlled. These challenges require a high level of expertise and quality control.
Considerations in MIM Production
Successful implementation of the MIM process requires careful consideration of various factors. These considerations are crucial in determining the MIM parts' quality, performance, and cost-effectiveness. Let's explore these considerations in detail.
Binder Selection
The binder plays a critical role in the MIM process. It facilitates the molding process and is then removed during debinding. The binder must be selected to provide good flow properties during molding and to be easily removed during debinding without leaving any residue that could affect the properties of the final part.
Metal Powder Size
The size of the metal powders used in the feedstock can significantly impact the properties and performance of the MIM parts. Smaller powders can provide higher green strength and better surface finish but can also increase the viscosity of the feedstock, making molding more challenging. Therefore, the powder size must be carefully selected based on the application's requirements.
Mold Design
MIM Mold design is another critical consideration. The mold must be designed to facilitate the flow of the feedstock, minimize the formation of defects, and allow for shrinkage during sintering. The design of the mold can also impact the cost and productivity of the MIM process.
Thin Wall
MIM can produce parts with thin walls, which can be advantageous for reducing weight and material usage. However, having thin walls can be challenging due to the difficulty of filling the mold and achieving uniform density. Therefore, the design of the part and the molding parameters must be carefully optimized.
Taking Neway as an example, if the part you design needs Neway to manufacture it with the MIM process, you need to consider that the thin wall of the MIM part should be at least 0.35mm. If you must use a thinner wall, such as 0.2mm, the thin wall must be capable of post-processing, such as CNC machining
What We Can Offer In MIM?
Neway is a custom parts manufacturer with 30 years of experience. As a Metal Injection Molding (MIM) supplier, we offer one-stop service from design to production:
1. Consultive Design Service: You are welcome to consult our material and design engineers from the beginning of the project. We provide free services, including material selection advice, process advice, structural design advice
2. Mechanical Design And Data Copying: We conduct mechanical design based on the product requirements as you provide or copy parts' data based on your samples and create highly feasible production drawings for production.
3. Rapid Prototyping: Neway can conduct prototype testing through CNC machining, 3D printing, and rapid molding.
4. On-demand Manufacturing: Neway supports on-demand customization without MOQ to minimize the initial cost of product development.
5. Simple Assembly And Testing: Hardware assembly capabilities include basic soldering, fastening, snap-fit, and Interlocking. Prototype testing includes dimensional and tolerance testing, fit and form testing, durability, and wear testing.
评论
发表评论