Precision Advantages of Lasers Cutting
Laser-cutting services offer unparalleled precision capabilities compared to other manufacturing processes. Conventional tools like saws, routers, and mechanical cutters rely on physical contact between the tool and the material. This contract limits how fine of details these tools can create. Conversely, contactless Lasers use focused light energy to transform or remove material. It gives lasers a distinct precision advantage.
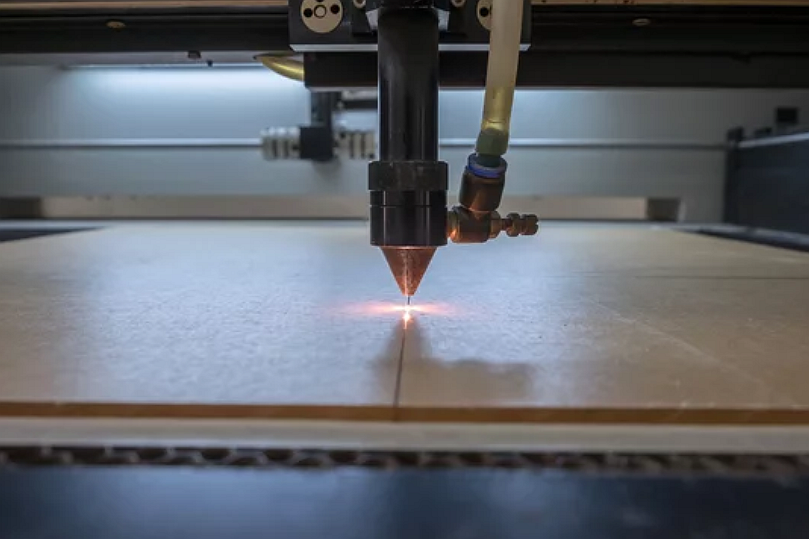
Laser cutting achieves its precision in a few key ways:
The laser beam can be focused down to a narrow diameter, smaller than a human hair. This tiny spot size allows for micron-level accuracy.
No physical cutting force during laser cutting could cause deflection, vibration, or material stress. The laser directs its beam across the material in the programmed path.
No tool wear or erosion during laser cutting would slowly degrade precision.
The net result is ultra-sharp edges, smooth surfaces, and complex geometries.
Laser Cutting Tolerances
So precisely how precise can laser cutting get? Many modern laser systems can achieve tolerances of +/- 0.001 inches or finer. For reference, human hair is about 0.003 inches wide, so laser cutting achieves sub-hairline precision. Optimized laser cutters can have tolerance down to +/- 0.0005 inches. It means intricate patterns or components with strict dimensional requirements can be produced accurately and consistently.
A critical factor in laser cutting precision is the motion system. The axes of movement for the cutting head typically employ precision linear motors or guides like ballscrews. High-performance motion control components like optical encoders and precision-ground bearings maintain micron-level repeatability. It allows the laser head to follow the programmed path within tiny fractions of a millimeter.
Cutting systems that compromise on motion components see a noticeable reduction in achievable precision. So machine builds quality directly impacts cutting tolerance. Reducing travel speeds can also improve precision for demanding applications. It gives the motion system more time to react and follow the path accurately.
Consistent Results and Edge Quality
An important aspect of laser precision is consistency. Laser cutting can hold extraordinarily tight tolerances for one-off jobs and over thousands of production parts. This repeatability comes from the automated, computer-controlled process unique to laser cutting. Once the machine is programmed, there is little variation part-to-part.
Edge quality also benefits from the laser's precise beam. Melting or vaporizing material only in the desired cut path leaves smooth, consistent edges. There is no mechanical deformation or tool marks seen in other cutting processes. For materials like reflective metals, edge roughness can be further improved using nitrogen-assisted laser cutting rather than oxygen. And avoiding oxidation results in cleaner edges.
Laser cutting's automated nature, fine beam size, and no direct contact with the material lead to unmatched precision and consistency. Components can be manufactured within microns of accuracy over unlimited production runs.
Achieving Small Hole Sizes and Intricate Details
In addition to tight cutting tolerances, lasers achieve petite hole sizes and intricate details. Laser drilling techniques can have holes with diameters as little as 0.006 inches. To put this in perspective, the diameter of human hair is over five times larger than the holes achievable by lasers. These micro-holes enable applications like adding cooling airflow to turbine blades or manufacturing sieves and filters with ultra-fine meshes.
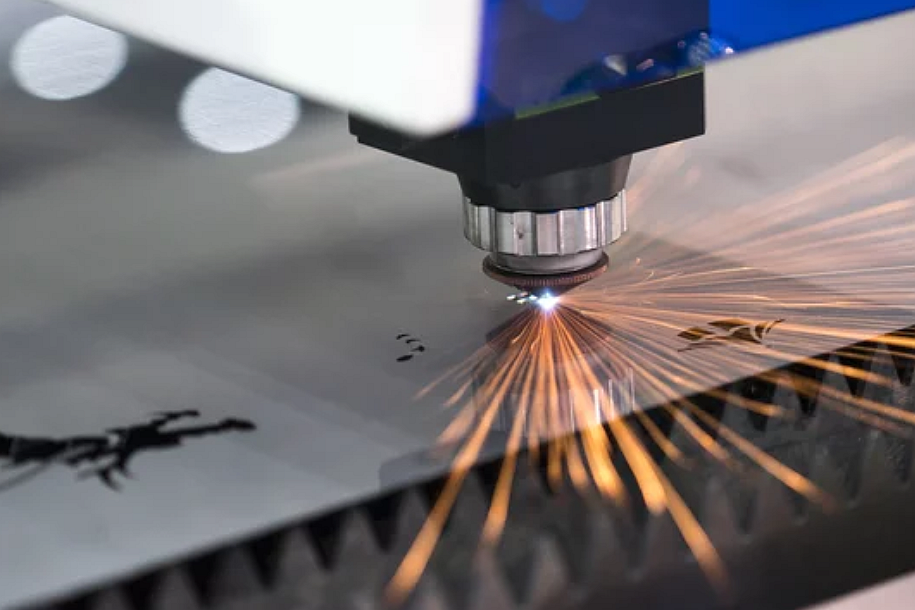
For adding detailed features like small slots, voids, and apertures, the laser's narrow spot size allows for remarkable intricacy. Complex nested cuts, micro tabs, and engraving-quality textures can be laser cut into parts. Walls, meshes, and delicate structures down to 0.5 mm thick can be reliably laser-cut. Photo-etching techniques use laser detail capabilities for things like making stencils for circuit boards. After laser cutting, no post-processing like drilling or machining is needed to achieve small holes or details. It is all done in one operation.
Challenges to Laser Cutting Precision
Of course, reaching the highest levels of precision with laser cutting comes with some challenges. Tighter tolerances mean processing time increases to accommodate slower cutting speeds and more precise motion control. So maximizing precision requires finding the ideal balance of tolerance versus production rate.
The thickness and properties of the cut material also factor into achievable precision. For example, cutting half-inch thick steel plates to acceptable tolerances requires higher power lasers and reduced feed rates than slicing thin sheets. Thermal effects in the material from laser heating can cause deformation issues.
Precision laser cutting requires strict process control. Any variations in the laser beam, assistance gas pressure, machine calibration, or environmental conditions inside the work area can affect cutting tolerance. So maintaining highly tight tolerances involves comprehensive monitoring and quality control procedures.
In summary, while achieving tolerances under 5 microns brings inevitable tradeoffs, the capabilities of precision laser cutting continue to advance. Through refined motion systems, laser beam delivery, and process control, today's state-of-the-art laser cutters push the boundaries of manufacturing precision.
Laser Cutting vs. Other Methods
To better appreciate the precision possible with laser cutting, it is helpful to compare it against some other standard cutting methods and their tolerance capabilities:
Like the CNC milling process, the mechanical cutting process typically holds ~0.005-inch tolerances. They are limited by tool rigidity, erosion, and contact forces.
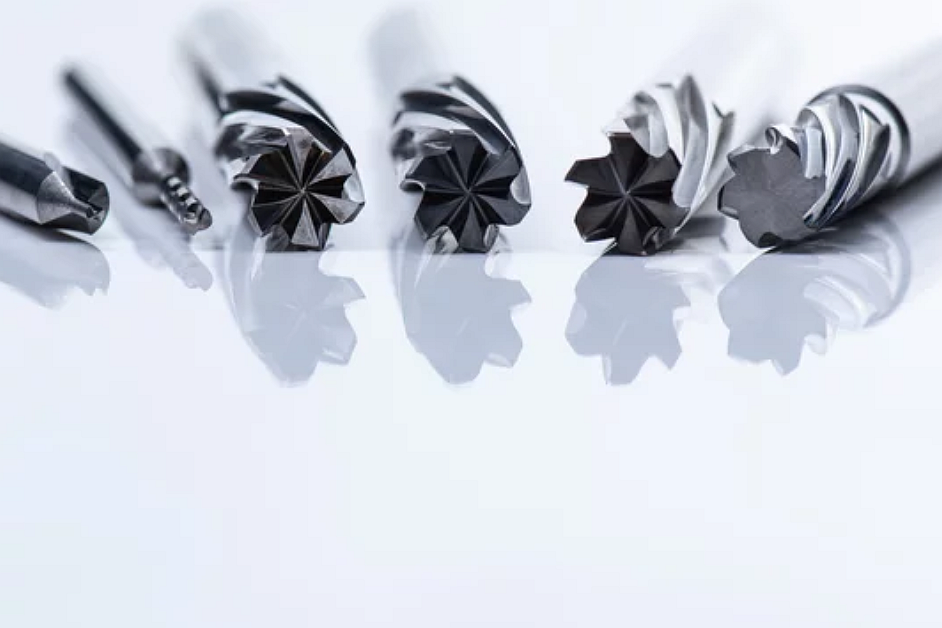
Abrasive waterjet cutting achieves ~0.003-inch tolerances: stream deformation and kerf width limit precision.
Wire EDM process can reach ~0.0001-inch tolerance but has slow cutting speeds. It is limited by wire imprecision.
CNC machining can achieve ~0.0005-inch tolerance. It requires a rigid setup and is tool-based.
Metal stamping service and punching process hold ~0.01-inch tolerances. Limited by die clearances and deformation.
Laser cutting's contactless process and ultra-narrow cut line enable significantly tighter tolerances than traditional fabrication approaches. For most precision cutting applications, the laser is the superior option.
There are some niche cases where other processes hold the advantage. Photo etching can attain finer details than laser for semiconductor production but has limited material options. Diamond turning achieves nanometer-level smoothness for optics and lenses but is prohibitively expensive for most uses.
So while alternatives exist for specific high-end precision needs, laser cutting provides the best balance of high tolerance, versatility, and value for most industries. Continued innovation in laser and motion technology and machine automation will only expand the process's capability.
评论
发表评论