Aluminum die casting is a popular manufacturing process for precisely producing metal parts with complex geometries, smooth surfaces, and high dimensional accuracy. In die casting, molten aluminum is injected under high pressure into reusable molds, called dies, to form the desired part shape.
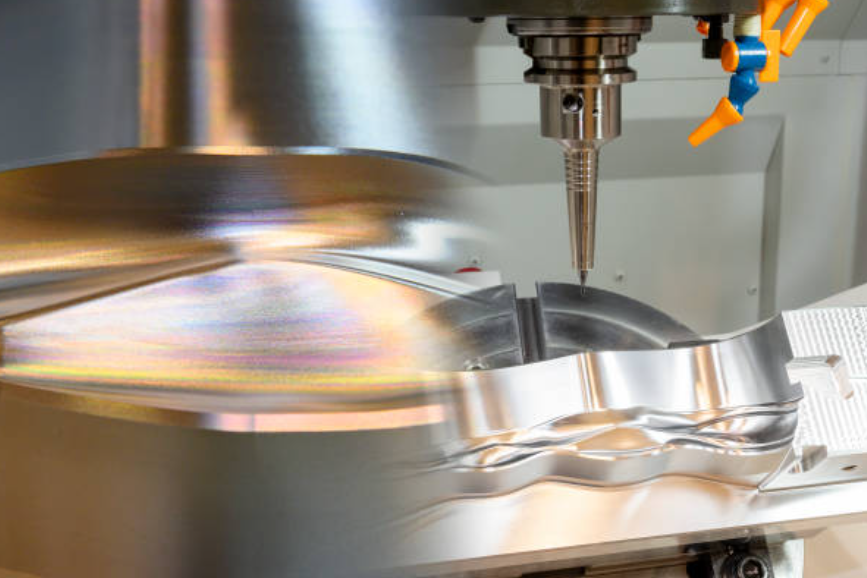
The material used to make the die is crucial for achieving optimal quality, durability, and productivity in aluminum die casting. This article explores the most common and suitable die materials, properties required, critical considerations in die material selection, surface coatings and treatments used, and the steps involved in machining the dies.
Die-casting molds, also called dies, must withstand high pressures, temperatures, and thermal fatigue cycles inherent to the die-casting process. Using materials with suitable properties is crucial for achieving good mold life and performance. This article explores common grades, mechanical properties, heat resistance, hardness, and expected mold life for various tool steel, hot work steel, maraging steel, cobalt-base, and nickel-base alloys used for die-casting. Critical considerations in die material selection, surface coatings and treatments used, and the steps involved in machining the dies.
Desired Properties for Die Casting Dies
The intense conditions of high pressure and heat in aluminum die-casting place considerable demands on the mold material. Desired properties include:
- High hardness and heat resistance to resist erosion and deformation
- High compressive and fatigue strength to withstand clamping forces
- Excellent thermal conductivity to facilitate cooling and solidification
- Sufficient toughness and ductility to resist cracking and fracture
- Excellent machinability and polishability to create smooth cavities
- Dimensional stability across temperature changes
- Corrosion resistance against hot aluminum and gases
Common Die Materials Used
Tool Steels for Die Casting
Tool steels are commonly used for die-casting molds due to their excellent balance of properties, machinability, and cost-effectiveness. Typical grades include:
- A2: Air-hardening tool steel with 5% chromium. Hardness around 60-62 HRC. Good toughness and stability for small to medium die-casting molds.
- A6: Similar to A2 with added vanadium for better wear resistance and stability. Hardness around 62-64 HRC. Used for medium-sized molds.
- D2: A cold work tool steel with 12% chromium and 1% molybdenum. Achieves hardness up to 62 HRC. Higher toughness than A2 but less stable. They are used for small die-casting molds.
- H13: A chromium-molybdenum hot work tool steel. The most commonly used tool is steel for die casting. Hardness around 52-54 HRC. Balance of heat resistance, toughness, and stability. They are used for small to large molds.
Tool steel molds can withstand aluminum die-casting temperatures up to around 700-1000°F. Expected mold life ranges from 50,000 to 200,000 cycles depending on grade and complexity.
Hot Work Tool Steels
Hot work tool steels handle higher die-casting temperatures, maintaining strength and hardness at temperatures exceeding 1000°F. Common grades include:
- H11: Chromium-molybdenum-vanadium alloy. Hardness around 50-52 HRC. Withstands temperatures up to 1400°F. Used for medium-sized aluminum molds.
- H13: The most famous hot work steel. 5% chromium with molybdenum and vanadium additions. Hardness around 52-54 HRC. Maintains strength up to 1500°F. Excellent balance of properties for a wide range of die-casting molds.
- H19: High purity tungsten-molybdenum-vanadium steel. Hardness 55-57 HRC. Resists softening up to 1500°F. They are used for difficult castings with thin walls and complex geometries.
- H21: Modified 4Cr-2Mo-V alloy. Higher hardness at 55-58 HRC with similar heat resistance as H13. Improved wear resistance but lower toughness. They are used for demanding applications.
Hot work steels offer die life from 200,000 up to 500,000 cycles for typical aluminum die-casting applications. Heat resistance allows the casting of higher melting point alloys.
Maraging Steels
Maraging steels are ultra-high strength martensitic steels that achieve remarkable mechanical properties through intermetallic age hardening. Grades include:
- 250: 17Ni-8Co-4Mo-Ti alloy aged to 50-55 HRC. Strength up to 300 ksi. Withstands over 2000°F. Used for highly stressed dies.
- 300: 18Ni-8Co-5Mo-Ti alloy aged to 52-56 HRC. Strength up to 350 ksi. Similar heat resistance. Famous for highly stressed, complex die-casting molds.
- 350: 18.5Ni-8.5Co-4.8Mo-Ti alloy aged to 54-58 HRC. Strength up to 400 ksi. Resists temperatures exceeding 2100°F. They are used for very demanding applications.
Maraging steels offer a mold life of over 500,000-1,000,000 cycles. The ultra-high strengths allow for minimizing die size and weight. However, the high alloy content makes maraging steels expensive.
Cobalt Base Alloys
Cobalt-base alloys offer an excellent combination of high hot hardness, thermal fatigue resistance, and heat resistance. Grades include:
- Stellite 6B: Cobalt-chromium alloy with tungsten, molybdenum, and carbon. Hardness around 52 HRC. Strength maintained beyond 1600°F. Resists thermal shock and metal erosion. Lower cost than nickel alloys. Used for moderately complex dies.
- Stellite 20: Cobalt-chromium alloy modified with tungsten and carbon. Hardness around 40-50 HRC. Withstands over 2000°F. Better erosions resistance but lower strength than Stellite 6B. Used for long production run molds.
- Stellite 21: Cobalt-nickel-chromium alloy aged to 50-54 HRC. Highest strength cobalt alloy with heat resistance to 1800°F. They are used for complex shapes and thin walls.
Satellites offer mold life ranging from 250,000 to over 500,000 cycles under typical aluminum die-casting conditions. The high tungsten content provides excellent thermal properties.
Nickel Base Superalloys
Nickel superalloys offer the ultimate heat resistance and high strength for die-casting applications involving extreme conditions, complex geometries, or aggressive alloys. Grades include:
- Inconel 718: Strengthened Ni-Cr-Fe-Nb alloy aged to 36-45 HRC. Tensile strength over 200 ksi up to 1300°F. Withstands over 2000°F. High toughness. Used for demanding aluminum casting applications.
- Inconel X-750: Precipitation-hardened nickel-chromium alloy with additions of titanium and aluminum. It is aged 40-50 HRC. Strength exceeds 200 ksi at 1500°F. Resists temperatures over 2200°F. They are used for complicated geometries and castings.
- Waspaloy: Hardened Ni-Cr-Co alloy with excellent strength to 1300°F. Aged to about 38-53 HRC depending on the treatment. Thermal fatigue resistance is superior to stainless steel. They are used for complex, thin-wall castings.
Nickel alloy molds offer the most extended die life, often over 1,000,000 cycles. However, both alloy cost and machining difficulty are incredibly high. Their application is usually limited to the most challenging die-casting applications.
Inserts
Inserts of cemented carbides, ceramics like silicon carbide, or diamond composites can be added at high-wear areas. It combines the economy of a steel die with exceptional hardness or heat resistance at critical points.
Die Material Selection Considerations
Factors that influence optimal die material selection include:
- Aluminum alloy - Higher melting point alloys require better heat resistance
- Part size - Larger heavy castings exert more significant stress on the dies
- Part geometry - Thin or conformal parts exert more pressure on the die
- Production volume - Higher volumes amortize the cost of premium die materials
- Part weight - Heavier castings require a more robust die
- Surface finish - More polished surfaces need greater hardness and wear resistance
- Temperature margins - More demanding applications require wider margins
- Economic factors - The die material cost must align with production volume and part value
OEMs work closely with die casters to perform these analyses to determine the most suitable and cost-effective die material.
Die Surface Treatments
In addition to selecting the base die material, various surface treatments can prolong the die life:
- Nitriding - Forms a thin hard nitride layer to resist wear and erosion
- Boriding - Similarly creates a more complex boride layer on the die surface
- Hard chrome plating - Resists wear through a harder chromic coating
- Polishing - The die surface is highly polished to reduce friction and sticking
- Graphitizing - Graphite coating minimizes hot aluminum adhesion
- Oxidizing - Creates an oxide layer to reduce soldering and facilitate release
- Laser treatments - Laser impacts enhance surface microstructure and hardness
The optimal surface treatments depend on the specific aluminum alloy, die material and casting conditions.
Die Manufacturing Process
Quality aluminum die-casting dies are produced through the exact manufacturing steps:
1. CAD of die - 3D CAD design based on part geometry
2. CNC machining - Rough forming of die cavity using CNC mills and drills
3. Heat treatment - Harden and temper the die to desired properties
4. CNC finishing - Fine CNC machining to achieve final die form
5. Polishing - Hand or machine polishing with progressing finer abrasives
6. Surface treatments - Apply special coatings and treatments
7. Assembly - Assemble two die halves into the final die set
8. Testing - Test casting to verify required quality before total production
Precision CNC machining, heat treating, polishing, and surface enhancements are essential to creating durability. Long-life dies for quality, consistent aluminum die-casting production.
评论
发表评论