Sheet metal fabrication is a versatile and widely used manufacturing process that shapes and forms flat metal sheets into various components and products. This process has been around for centuries and is a fundamental method in the manufacturing industry. Different metals' malleability, strength, and availability make sheet metal fabrication suitable for various applications in various sectors, including automotive, aerospace, construction, electronics, and more.
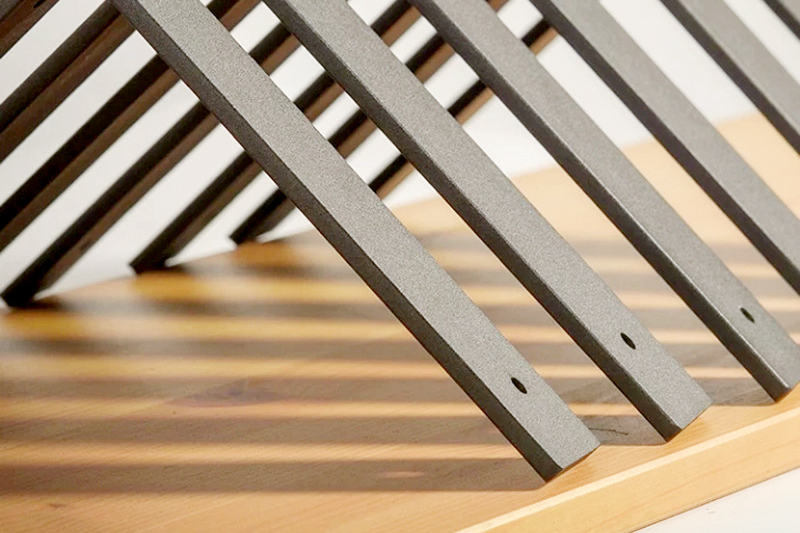
Neway has provided sheet metal fabrication services for over 30 years, including:
Sheet metal laser cutting service
Achieve intricate, complex sheet metal cuts with minimal distortion using Neway precision laser cutting services. We cut steel, aluminum, and copper with fiber lasers up to 6mm thickness with 0.005" tolerance.
Metal bending and forming service
Leverage Neway modern press brakes and skilled technicians to bend and form sheet metal into shapes from simple bends to complex curvatures. We can bend steel, stainless, aluminum, and copper to 3/8" thickness. Contact us for your custom metal bending and forming needs.
Our high-speed precision stamping presses and extensive die inventory provide quality sheet metal stamping up to 1/4" thick. We create custom progressive and transfer dies to produce high volumes of stamped parts from aluminum, steel, stainless and more.
Assembly by welding, mechanical fasteners service
Get complete sheet metal assemblies ready for installation. Neway offers comprehensive joining techniques, including MIG, TIG, spot welding, riveting, clinching, and all mechanical fastening methods. Contact us to discuss your sheet metal assembly project requirements.
Finishing with surface treatments service
Enhance the durability, aesthetics, and function of fabricated sheet metal components using Neway's specialty finishing services. It includes powder coating, wet paint, plating, anodizing, printing, and more. We provide complete finishing solutions to meet your specifications.
Sheet Metal Fabrication Features
Malleability: Sheet metal can be easily bent, stretched, and formed into complex shapes without losing strength, making it ideal for producing intricate designs and precise components, such as equipment casings, brackets, structural components, Etc.
Variety of Metals: Sheet metal comes in different metals, including steel, aluminum, copper, brass, and titanium. Each metal offers unique properties, allowing fabricators to choose the most suitable material for a specific application.
Thickness: Sheet metal can range from extremely thin foils to thicker plates, providing options for different structural requirements and manufacturing processes. Usually, Neway provides sheet metal processing services from 0.3mm to 8mm.
Cost-effective: Compared to other manufacturing methods, sheet metal fabrication is often cost-effective, especially for mass production, due to its relative simplicity and efficiency.
Precision: With modern equipment and techniques, sheet metal fabrication can achieve high levels of precision, ensuring consistency and accuracy in mass production.
Versatility: Sheet metal fabrication can create various products, from small brackets to large enclosures and complex assemblies.
Applications of Sheet Metal Fabrication
Automotive Industry: Sheet metal fabrication is crucial in the automotive sector. It is used to manufacture car bodies, frames, panels, fenders, hoods, and other structural components: the ability to form and weld sheet metal efficiently al lows for lightweight yet robust vehicle designs.
Aerospace Industry: In aerospace, weight is critical, and sheet metal's high strength-to-weight ratio makes it disposable. It fabricates aircraft structures, wings, fuselage components, and engine parts.
Construction: Sheet metal fabrication finds extensive use in the construction industry for roofing, cladding, ductwork, gutters, and architectural components. Its corrosion resistance makes it suitable for outdoor applications.
Electronics: Sheet metal produces electronic enclosures, chassis, brackets, and heatsinks due to its electrical conductivity and electromagnetic shielding properties.
Medical Equipment: The precision and clean appearance of sheet metal components make them suitable for medical equipment manufacturing, including cabinets, trays, and housing for various devices.
Home Appliances: Sheet metal produces ovens, refrigerators, washing machines, and air conditioning units.
Energy and Renewable Resources: The energy sector utilizes sheet metal fabrication to produce wind turbines, solar panels, and power generation equipment components.
Telecommunications: Sheet metal is used in manufacturing communication equipment, racks, enclosures, and satellite dishes.
Examples of Sheet Metal Fabrication Products
Sheet Metal Enclosures: Everyday sheet metal products protect electronic components, machinery, and sensitive instruments from environmental factors and physical damage. Examples include computer cases, control panels, and electrical cabinets.
Brackets and Mounting Plates: Sheet metal brackets and mounting plates support and attach various components in machinery, vehicles, and buildings.
Sheet Metal Panels and Covers: Panels and covers are widely used in the automotive, aerospace, and electronics industries to protect and enclose internal components.
Sheet Metal Stamping: Stamping is a metal fabrication process that involves cutting and forming metal sheets into specific shapes. It produces parts such as gears, washers, and connectors.
HVAC Ductwork: Sheet metal is commonly used in heating, ventilation, and air conditioning (HVAC) systems to create ducts and vents for air distribution.
Signage and Advertising Displays: Sheet metal fabrication creates custom signs, billboards, and promotional displays with intricate designs and lettering.
Automotive Body Panels: Sheet metal forms the body structure of vehicles, including doors, hoods, trunks, and quarter panels.
Cabinets and Shelving Units: Metal cabinets and shelving units are commonly used for storage and organization in industrial, commercial, and residential settings.
Metal Artwork: Sheet metal can be sculpted and manipulated to create artistic pieces and sculptures.
评论
发表评论