Sheet Metal Fabrication
Sheet metal fabrication involves forming and assembling thin, flat sheets of metal stock into final parts or products. Sheet metal is one of the fundamental forms of steel used across many industries, including automotive, aerospace, appliances, electronics, and construction.
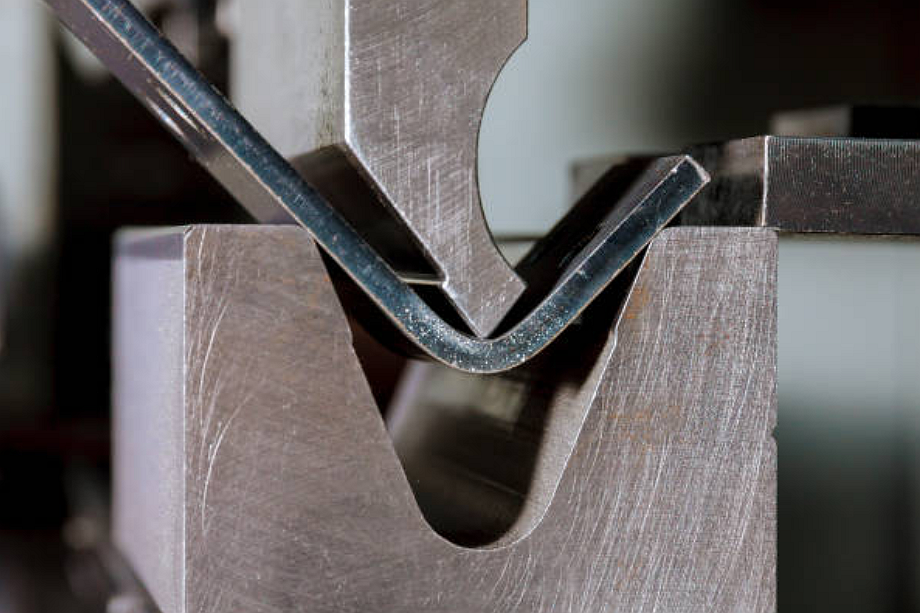
Neway has provided sheet metal fabrication services for over 30 years, including:
Sheet metal laser cutting service
Achieve intricate, complex sheet metal cuts with minimal distortion using Neway precision laser cutting services. We cut steel, aluminum, and copper with fiber lasers up to 6mm thickness with 0.005" tolerance. Get a fast turnaround on your sheet metal laser cutting project.
Metal bending and forming service
Leverage Neway modern press brakes and skilled technicians to bend and form sheet metal into shapes from simple bends to complex curvatures. We can bend steel, stainless, aluminum, and copper to 3/8" thickness. Contact us for your custom metal bending and forming needs.
Our high-speed precision stamping presses and extensive die inventory provide quality sheet metal stamping up to 1/4" thick. We create custom progressive and transfer dies to produce high volumes of stamped parts from aluminum, steel, stainless and more.
Assembly by welding, mechanical fasteners service
Get complete sheet metal assemblies ready for installation. Neway offers comprehensive joining techniques, including MIG, TIG, spot welding, riveting, clinching, and all mechanical fastening methods. Contact us to discuss your sheet metal assembly project requirements.
Finishing with surface treatments service
Enhance the durability, aesthetics, and function of fabricated sheet metal components using Neway's specialty finishing services. This includes powder coating, wet paint, plating, anodizing, printing, and more. We provide complete finishing solutions to meet your specifications.
Sheet Metal Materials
- Steel - Low carbon, HSLA, galvanized, and stainless steel are commonly formed into sheet metal. Steel offers high strength and durability.
- Aluminum - Aluminum and its alloys are lightweight, corrosion-resistant, and quickly formed and welded. Aerospace and automotive applications use aluminum sheet metal.
- Copper - Copper and brass sheets provide excellent conductivity and formability. They are used for electronic enclosures and architectural applications.
- Titanium - Titanium possesses high strength and corrosion resistance for applications like aerospace hulls and structures. It has lower formability than steel or aluminum.
Sheet Metal Thicknesses
Standard sheet metal stock ranges from 0.15 mm to 6 mm in thickness. The thicker the metal, the harder it is to form without defects. Typical thicknesses include:
- 0.15-0.5 mm - Ultra-thin sheets used for light-duty applications, electronics, and precision parts
- 0.5-1.5 mm - For general sheet metal work and applications with moderate forming
- 1.5-3 mm - Thicker sheets for structural panels, enclosures, and heavy-duty fabrication
- 3-6 mm - Very thick sheet used for heavy equipment, armor, truck frames
Sheet Metal Forming Processes
Common ways to form sheet metal into shapes include:
- Bending - V bending, wipe bending, hemming, and seaming to create curved profiles
- Deep Drawing - Presses form sheet into hollow round, square, or complex 3D shapes by controlled stretching
- Roll Forming - Gradually bending sheet through consecutive roller dies to make long profiles
- Stamping - Punching out flat blank shapes from sheets using die sets and presses
- Hydroforming - Using fluid pressure to form complex curved or domed shapes
- Spinning - Rotating sheet metal against a tool to form rounded, seamless hollow shapes
Sheet Metal Cutting Processes
To cut or create holes in sheet metal, processes like these are used:
- Mechanical cutting - Shears, slitters, and saws cut by applying shear forces along the edges
- Laser cutting - A focused laser beam melts and cuts complex profiles with no tooling contact
- Waterjet cutting - A pressurized jet of water erodes through a sheet for intricate shapes
- Punching - Punching presses use shaped dies to punch internal holes and edge cutouts
- CNC machining - Milling, drilling, turning, and grinding removes material with cutting tools
- Etching - Controlled chemical etching masks and selectively removed material
Sheet Metal Joining Techniques
For assembly, standard methods include:
- Welding - Arc, spot, laser, and resistance welding fuse components.
- Mechanical fasteners - Rivets, screws, and bolts allow non-permanent joining and disassembly.
- Adhesives and tapes - Bonding with adhesives creates continuous joins with no fasteners.
- Soldering and brazing - Filler alloys are melted to create strong joints, especially useful on thinner sheets.
- Clinching - Special tools combine mechanical interlocking and low-level material deformation for fast joining.
Sheet Metal Finishing
For aesthetics, protection, and functional enhancement, sheet metal finishing processes include:
- Painting and powder coating - Applied decorative and protective coatings cured through baking.
- Plating - Electroplating or electroless with metals like zinc, nickel, and chrome for corrosion and wear protection.
- Anodizing - Electrolytic oxide layer on aluminum for wear and corrosion resistance.
- Screen printing - Applying graphics, labels, and dials using screened printing inks.
- Embossing - 3D surface textures and patterns pressed into sheets using engraved roller dies.
In summary, sheet metal fabrication transforms flat sheet stock into final products using a variety of cutting, forming, machining, joining, and finishing processes. The methods selected depend on the material, part shapes, production volumes, and functional requirements.
评论
发表评论