Rapid prototyping refers to various technologies used to fabricate physical prototype models directly from digital data, such as CAD files. Rapid prototyping allows companies to validate concepts, conduct testing, and reduce risk during new product development by enabling accelerated design iteration.
Rapid prototyping services provide an accessible way for companies to take advantage of these technologies without significant in-house capital investment. Many applications across industries leverage rapid prototyping services today.
Design Validation
One of the most common rapid prototyping uses is for early design validation. Seeing and touching a concept brings key insights faster than digital modeling alone. Rapid prototyping lets designers quickly evaluate aesthetic details like shape, surface finish, ergonomics, and color.
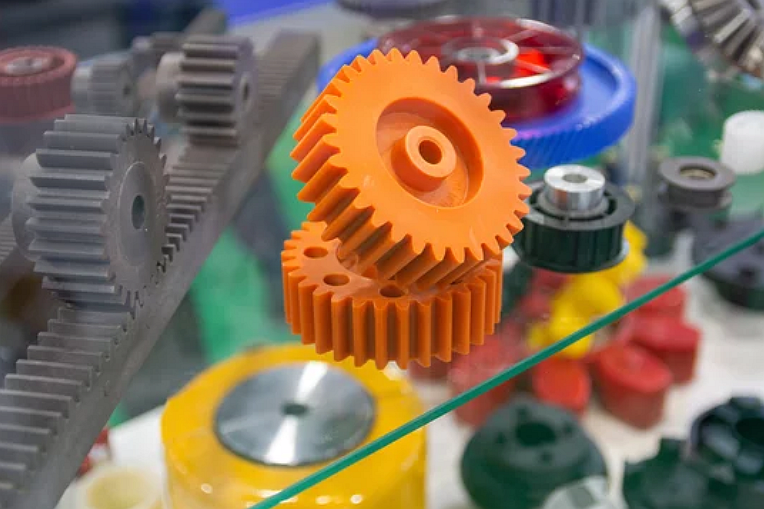
Obtaining physical prototypes early, even if primitive, can reveal design flaws and areas for improvement. Rapid prototyping enables this testing to happen in days or weeks rather than months, making iterations faster and less expensive. Services like 3D printing and CNC machining are popular for early-stage design refinement.
Functional Testing
Beyond aesthetics, physical prototypes enable critical functional testing of new products. Will components fit and work together under real-world conditions? Rapid prototyping services fabricate parts from production-grade materials for this evaluation.
Testing parameters like strength, thermal properties, fluid dynamics, and operability is more effortless with physical prototypes. Rapid tooling can injection mold working plastic parts for ergonomic studies. CNC-machined metal prototypes can undergo cyclic fatigue analysis. Rapid prototyped jigs and fixtures may aid in assembly trials.
Manufacturing Process Development
Developing and proving manufacturing processes is another critical use of rapid prototyping services. Producing prototypes on production intent equipment reveals manufacturability issues early. Rapid tooling can simulate critical aspects of injection molding, thermoforming, blow molding, and other production plastics processes at low volumes.
Sheet metal and CNC machined prototypes help assess fabrication and assembly issues with metal components. 3D printing workflows for metal casting and molding patterns factor in design restrictions needed for manufacturability. Rapid prototyping provides critical learning that optimizes production outcomes.
Market Research/User Testing
Before significant investment in a new product, market research and user testing with prototypes gauges customer interest, help set requirements, and guide design. Rapid prototyping services enable this testing earlier in development when changes are less costly.
3D printing models for design research, focus groups, and crowdsourced evaluation generates customer feedback. Functional prototypes in user trials reveal ergonomic issues. Producing multiple iterations of a design for testing is possible with lower-cost rapid prototyping techniques. The insights gained reduce the risk of product failure down the road.
Patents/Licensing/Investment
Rapid prototyping helps inventors demonstrate concepts when filing patents and pitching to potential licensees or investors. A professional-quality prototype conjugates the inventor's vision, proves functionality, and displays market potential.
Prototypes can help startups test ideas and gain funding to advance development. For universities and research labs pursuing licensing deals, providing potential partners with prototypes shows commercial viability for emerging technologies. Rapid prototyping services enable this with minimal in-house capabilities.
Low-Volume Production
Some rapid prototyping techniques can cost-effectively produce short production runs in lower quantities. While low-volume manufacturing, rapid tooling methods like 3D printed molds for injection molding, vacuum casting, and thermoforming fill gaps between prototyping and full-scale production.
Short-run sheet metal fabrication and CNC machined parts are other rapid prototyping services for bridging volumes under 1000 units. These techniques allow limited market testing and inventory for crowdfunding campaigns or niche products. As volumes grow, processes transfer to mainstream manufacturing.
Customization
Rapid prototyping enables mass customization, where products are tailored to meet individual consumer needs. 3D-printed products like prosthetics, fixtures, jigs, and medical devices are standard. Many consumers seek personalized product designs vs. off-the-shelf versions.
Mass customization can build customer loyalty and attract premium pricing for some products like jewelry, furniture, and footwear. Rapid manufacturing techniques suit low to mid-production volumes with variable designs. Overall, rapid prototyping facilitates the customization trend across many industries.
Education/Research
Rapid prototyping helps bring innovative ideas to reality for teaching and scientific advancement within academia and research institutions. 3D printing workflows make models and experimental apparatus accessible without workshop skills.
Creating prototypes rapidly benefits multidisciplinary projects and accelerates learning. For researchers, quickly iterating experimental designs produces faster insights. Students gain hands-on exposure to real-world engineering challenges. In general, rapid prototyping eases invention and expands opportunity.
In summary, rapid prototyping services are used across many industries and applications to accelerate new product development, improve designs, reduce risk, engage customers, and spur innovation. The ability to quickly turn digital concepts into physical models unlocks potential that did not exist with traditional manufacturing methods. With today's range of accessible services, the possibilities are endless.
Custom Rapid Prototyping Service
Prototyping a new product design? Forget waiting months for machined aluminum molds - Neway's rapid molding produces ready-to-test parts in just days! Their 3D-printed molds create precise, high-tolerance prototypes that mimic the look, feel, and functionality of accurate production plastics. Plus, Neway's team diligently guides you from concept through completion. Neway is the clear solution for rapid, responsive, cost-effective rapid molding.
评论
发表评论