Laser cutting has become invaluable for rapid prototyping or producing low or medium parts across various industries. However, not all laser cutting services offer the same quality, capabilities, or reliability. Selecting the right partner is crucial to achieving success with your laser-cutting projects. This comprehensive guide will overview the essential precautions and considerations when researching and vetting potential laser-cutting suppliers.
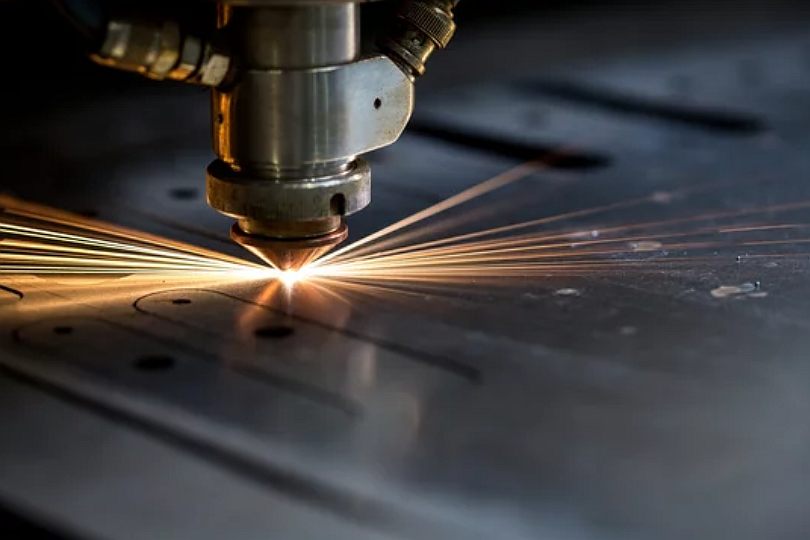
Assessing Laser Cutting Capabilities
When assessing the laser-cutting supply capabilities. The first step is understanding the types of materials and part geometries you require so that capabilities can be matched accordingly. Provide the prospective vendor with detailed information on the following:
Material type and thickness – Will you need cutting of metals, plastics, wood, or other materials? What thickness range? Can the lasers cut reflective metals like copper or aluminum?
Tolerance requirements – Do your parts demand precision tolerances of ±0.005" or tighter? What level of repeatability is needed?
Feature sizes – Will micro details like small holes or fine lines be required? How small?
Cut edge quality – Is a smooth polished edge finish needed, or will an as-cut finish suffice?
Flatness – Do parts need to remain flat after cutting without a warpage?
Volume requirements – What production volumes are estimated over what timeframe? One-offs, small batches, or high volume?
Secondary operations – Will you need additional fabrication like metal bending service, welding service, and surface treatments such as powder coatings?
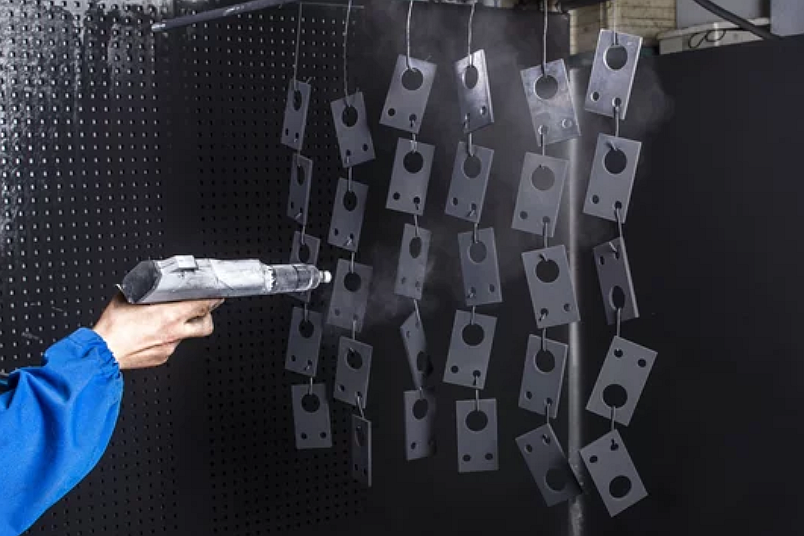
The suppliers should be able to clearly explain their capabilities in these areas or refer you to trusted partners if certain services are outsourced. If specifications fall outside their equipment's capabilities, they will advise accordingly. Upfront honesty is vital.
Vetting Laser Cutting Technology
You'll want to understand the models and ages of lasers utilized. Opt for newer machines as laser technology improves constantly. Key laser traits that affect tolerances and cutting ability include:
Laser power – Higher wattages allow thicker material cutting but reduce precision. Ensure power is matched appropriately.
Beam mode – Some modes offer improved edge quality or faster speeds but may compromise on tight-tolerance cutting.
Spot size – Smaller focal spots enable finer feature details but come at higher costs.
Positioning accuracy – Higher precision stages and linear encoders increase accuracy.
Cutting head – Lens type affects focus range and gas delivery options. Make sure suitable for the required materials.
A mix of CO2 and fiber lasers is ideal for covering metal and non-metal materials. Refrain from assuming all laser-cutting machines have identical capabilities. Avoid vendors utilizing outdated or low-end equipment unsuited for your parts.
Assessing Cost Factors
Request detailed pricing information applicable to your project volumes and materials. Typical factors influencing costs include:
Material – More exotic or hard-to-cut metals are more costly. Intricate plastics can also be pricier.
Sheet size – Laser cutting one large sheet is more efficient than multiple small pieces.
Cut time – Complexity, precision needs, and material impact cut time, which affects the cost per part.
Secondary operations – Adding bending, tapping, welding, etc., increases costs.
Setups – Moving sheets on/off machines between jobs adds labor costs.
Tolerances – Extremely tight tolerances under 0.005" reduce cutting speeds.
Order volume – Higher volumes achieve economies of scale.
Ideally, you want transparent pricing with no hidden fees. It allows for optimizing the design to balance cost versus part performance.
Qualifications and Experience
Find out what experience and credentials the laser cutting company and its personnel hold. Key areas to explore include:
Years in business – Longer history signals stability and accumulated expertise. The finished brand case for studying means trusted and experienced.
Staff training – Formal education and certifications indicate professionalism.
Industry experience – Specialization in your sector (aerospace, medical ISO 13485, etc) is ideal.
Continual improvement – Ask about lean initiatives, quality programs, and technology investments.
Certifications – ISO, AS9100, and other standards reflect a commitment to following strict procedures.
Memberships – Affiliations like the LIA and FMA are a positive sign.
You want assurance you're partnering with an innovative firm staffed by certified experts versus an unqualified shop with high turnover. Refrain from assuming all vendors share the same level of professionalism.
Quality Assurance and Process Control
A rigorous quality system is required to achieve consistent laser-cutting results. Probe the vendor on:
Inspection processes – Ask how material, in-process, and final parts are inspected. Gauge R&R metrics?
Software used – Does their CAD/CAM software automatically flag potential programming issues? Are optimal cut parameters calculated?
Calibration procedures – How often are machines calibrated? What mechanisms verify positioning accuracy?
Control of cut variables – How are beam power, focal point, gas pressure, and other factors controlled and optimized?
Staff training – Do operators receive extensive initial training with ongoing skills certification?
You want assurances appropriate quality plans are religiously followed for your parts. Refrain from assuming all vendors adhere to the same standards.
Lead Time and Scheduling
Understand typical lead times for the types of parts you require. How far in advance is capacity scheduling done? Is shift work or overtime used to meet urgent lead times? How will they accommodate unexpected priority projects?
Other key scheduling considerations:
Material lead times: Advanced planning is needed for exotic metals or plastics.
Part programming: Will your CAD files need extensive reformatting to generate viable cut paths?
Secondary operations: Outsourcing steps like welding or plating extend turnaround times.
Test parts: Initial sample runs to verify programs will add days.
Fixturing: Unique fixtures take time to design and produce.
Realistic commitments on delivery require deep production planning experience. Never take lead time estimates at face value.
Why Neway for Laser Cutting Service
"When I needed complex sheet metal parts laser cut for a new product design, I chose Neway based on a colleague's recommendation - and I'm so glad I did! Their laser cutting expertise was immediately obvious, producing intricate part geometries and holes down to just a few thousandths of an inch. Their rapid turnaround time in getting prototypes delivered has been even more impressive. I'm excited to partner with Neway to move these components into production." - John S., Aerospace Company CEO.
评论
发表评论