Metal stamping is a manufacturing process that mainly processes and produces small to large-sized parts for sheet metal. Metal stamping service is a versatile, high-speed manufacturing process that produces precise metal components in high volumes. Also known as press working, it works by pressing sheet metal between specialized dies using a stamping press machine. Metal stamping offers many benefits that make it an efficient, economical choice for fabricating metal parts and products:
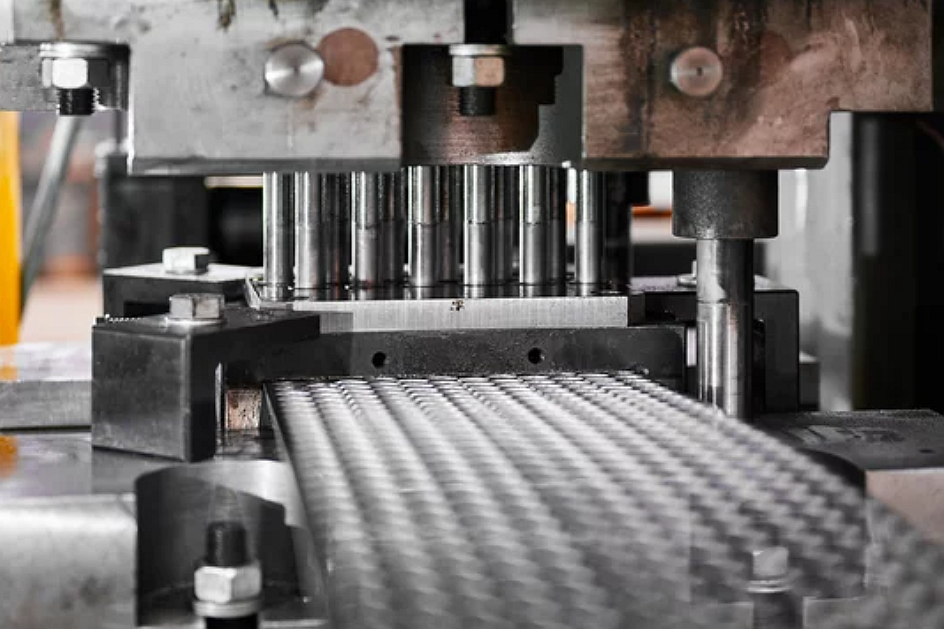
High Productivity
The automated nature of stamping enables very high rates of production. Modern stamping presses can operate at speeds over 1000 strokes per minute, producing hundreds of thousands of stamped parts per day. Multi-station progressive stamping operations maximize throughput. The high speed and output of stamping outpace processes like CNC machining.
Low Costs
Metal stamping is highly cost-effective compared to machining or casting processes, especially for high production volumes. The high hourly output keeps per-part costs very low. After initial die design and build, incremental part costs are just raw material, electricity, and press maintenance. No expensive skilled labor is required. The cost of Stamping aluminum parts is around five times cheaper than CNC machining.
Design Flexibility
Nearly any 2D part profile drawn in CAD software can be stamped, providing enormous design freedom. Modern die design tools and wire EDM allow precision machining for complex profiles. Parts integrating multiple cutouts, forms, beads, and embosses can be stamped in one hit. Flexible tooling modifications enable design revisions.
Material Versatility
Stamping materials use virtually any sheet metal material, including steel, stainless steel, aluminum, copper, brass, etc. Many exotic alloys used in aerospace can also be stamped. Unlike casting and forging, material changeovers are fast, not requiring melted metal. Blank dimensions are adjusted to accommodate different material gauges and strengths.
Precision and Accuracy
Stamping presses produce highly consistent, precise parts within tight tolerances of +/- 0.005 inches when adequately set up. Modern stamping controls micro-adjust ram position, speed, and tonnage during the stroke to optimize production quality. The stability of the process simplifies inspection. Rejected parts are less than 1%.
Superior Strength
The grain flow and work hardening of stamping create components more vital than those made by machining or casting. During stamping, deformation aligns the metal's grain structure along the part contours. It improves mechanical properties like yield strength. Dimensional stability is also excellent.
Streamlined Automation
Metal stamping production lines achieve highly efficient automation. Handling systems automatically feed sheet metal coils into precision blanking presses to cut blanks. Robotic arms then efficiently shuttle these blanks between progressive stamping stations and finishing operations. Automation maximizes output with minimal direct labor.
Rapid Prototyping
Soft prototype tooling produced through 3D printing allows concept stamping tools to be created in days versus weeks for conventional complex tooling. Designs can be quickly evaluated and iterated before committing to complete complex tooling. It allows accelerated product development, testing, and refinement.
Minimal Material Waste
The nesting capabilities of modern blanking die to maximize material utilization from sheet metal coils. Blanks are optimally nested to minimize skeleton scrap waste. Any remaining scrap can be easily recycled. Unlike milling, waterjet, or laser cutting, no material is wasted during stamping.
Superior Consistency
Once tooling is proven out, stamped parts show minimal variability over millions of cycles thanks to the stability and repeatability of the stamping process. Statistical process control continuously verifies critical dimensions to maintain tight tolerances during production runs. Consistency lowers quality control costs.
Scalability and Growth
As product volumes increase, additional stamping presses and operations can be cost-effectively added to the production line. The modular nature of stamping equipment allows production capacity to scale efficiently. Both manual-fed and fully automated systems are expandable.
Reduced Secondary Processing
By designing parts suitably for stamping, the need for additional machining, drilling, tapping, deburring, or finishing after stamping can be minimized or avoided. It reduces costs and lead times. Required secondary operations can often be built into the progressive stamping line.
Suitable for Small to Large Parts
Stamping presses range from small 5 ton benchtop units to massive 4,000 ton presses for automotive body panels and aircraft wings. This wide range means stamping can produce tiny micro-electronics parts to large panels up to 30 feet long. Specialized tooling configurations support virtually any part size.
In summary, the productivity, precision, flexibility, strength, and economy of metal stamping make it an ideal choice for mass-producing components out of sheet metal cost-effectively. It brings significant advantages to any manufacturer needing high-volume fabrication.
Why Choose Us
"As an engineer, I've used over a dozen metal fabricators over the years, but none match the quality and precision of Neway's laser cutting. Their advanced 3kw fiber lasers produce perfect cuts with minimal kerf every time. Their ability to hold extremely tight tolerances, I'm thoroughly impressed with their ability, even on complex internal cutouts. My projects always succeed thanks to Neway's accuracy and expertise." - John S., Aerospace Engineer.
评论
发表评论