ABS Material Optional for plastic injection molding
ABS is widely used for plastic injection molding due to its excellent flow, dimensional stability, strength, aesthetics, and ease of processing. Proper grade selection ensures ABS plastic meets the application's specific mechanical, thermal, flame retardance, aesthetic, and processing needs. Neway can customize ABS grades. Proper drying is essential before injection molding this hygroscopic material. Here are some critical points on the different grades of ABS plastic available for injection molding:
General purpose ABS - The most common and economical grade. Good all-around mechanical properties and heat resistance. They are used for a wide range of consumer products.
High-impact ABS - Contains higher rubber content to increase impact strength and flexibility. They are used for automotive parts, phone cases, and toys.
High heat ABS - Formulated for increased heat deflection temperatures up to 110°C while retaining impact resistance. Suitable for appliances.
High flow/low shrink ABS - Reduces viscosity and shrinkage rate to assist thin wall designs and precision molding. Useful for electronics.
Flame retardant ABS - Contains fire-suppressing additives to meet UL94 V-0 flammability standards. Used for automotive, aviation, and electronics parts requiring fire resistance.
ABS alloys - Blended with PC, PVC, and PMMA to enhance properties like weathering, chemical resistance, and stiffness.
Colors/effects - Custom ABS grades with stable colorants, metallic/pearlescent effects, and textures. Most aesthetics can be achieved.
Recycled ABS - Reclaimed ABS from electronics waste or injection molding scrap. Lower cost but has appearance and property variations.
ABS nanocomposites - Reinforced with nano-scale additives like organoclays or carbon nanotubes to increase strength and reduce shrinkage.
Injection Molding ABS Grade Comparison
ABS for injection molding has various material grades and properties, such as High impact ABS, High heat ABS, High flow/low shrink ABS, etc. They are also different in application. Consult Neway's material engineer after confirming your product requirements. It Can significantly reduce your production cost; the following are the characteristics of ABS materials commonly used by Neway.
ABS Grade | Tensile Strength (MPa) | Elongation (%) | Hardness (R-scale) | Heat Deflection (°C) |
---|---|---|---|---|
General Purpose ABS | 45 | 25 | 109 | 95 |
High Impact ABS | 40 | >50 | 105 | 90 |
High Heat ABS | 48 | 20 | 112 | 110 |
High Flow/Low Shrink ABS | 42 | 15 | 107 | 85 |
Flame Retardant ABS | 40 | 15 | 105 | 90 |
ABS Alloys | 48 | 60 | 115 | 100 |
Recycled ABS | 35 | 10 | 105 | 80 |
High-impact ABS has the highest elongation and lowest hardness due to higher rubber content.
High-heat ABS has the highest heat deflection temperature. Flame retardant grades have reduced heat resistance.
High flow/low shrink ABS compromises on strength and elongation to improve flow and reduce shrinkage.
ABS alloys enhance specific properties like chemical resistance via blending with other polymers.
Recycled ABS has lower properties due to polymer chain degradation during prior processing and use.
Each ABS grade is formulated to achieve a targeted property profile and meet different application requirements.
Injection Molded ABS Parts Applications
ABS offers versatile performance across many injection molding applications. The optimal grade provides the required properties while balancing performance with economics. According to the properties of different injection molding ABS, Neway lists some typical applications for the different ABS plastic grades used in injection molding:
General Purpose ABS:
General Purpose ABS has various consumer products like appliances, electronics, lego toys, automotive trim, keyboards, and power tools. It offers a good balance of properties and economics.
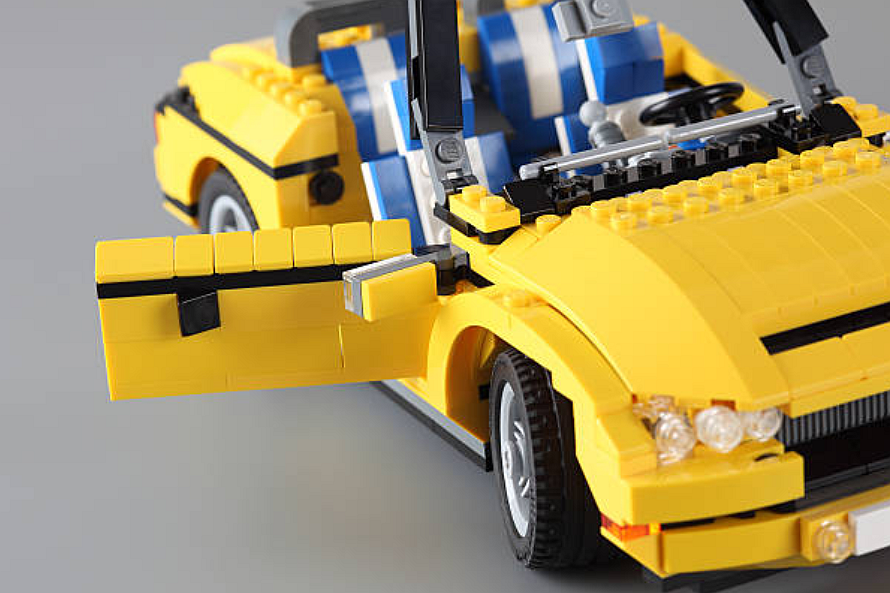
High Impact ABS:
High Impact ABS is mainly used in Automotive interior parts, bumpers, phone/electronics cases, protective equipment, and toys. It Provides added impact, strength, and flexibility.
High Heat ABS:
Household appliances, kitchenware, and enclosures require heat resistance. It Allows thinner walls and proximity to heat sources.
High Flow/Low Shrink ABS:
High Flow/Low Shrink ABS is used in Thin-wall containers, precision electronics, and medical parts. Excellent flow allows thinner walls and intricate details with low shrinkage.
Flame Retardant ABS:
Electronics enclosures, aircraft/aviation components, and construction materials. Meet strict flammability standards for fire safety.
ABS Alloys:
ABS Alloys is best for Automotive parts, enclosures, appliances, and electronics. Blends provide increased chemical, UV, and scratch resistance where needed.
Recycled ABS:
Recycled ABS can produce Non-critical components and parts, prototyping, and concept models. Reduces the use of virgin plastic but has lower and variable properties.
Key Features of Injection Molding ABS Materials
ABS Grade | Key Features |
---|---|
General Purpose ABS | Good all-around properties, economical |
High Impact ABS | Increased impact strength and ductility |
High Heat ABS | Heat resistance up to 110°C |
High Flow/Low Shrink ABS | Enhanced flow, reduced shrinkage |
Flame Retardant ABS | UL94 V-0 rated flammability |
ABS Alloys | Modified properties like UV resistance |
Recycled ABS | Environmental sustainability, cost savings |
In more detail:
General-purpose ABS provides the best balance of mechanical, thermal, and processability properties at a low cost. It is the workhorse ABS grade.
High-impact ABS contains higher rubber content for applications requiring increased impact energy absorption and flexibility.
High-heat ABS is formulated to withstand higher service temperatures while retaining strength.
High flow/low shrink ABS offers more effortless flow into thin-walled sections, intricate molds, and dimensional stability.
Flame retardant ABS meets strict flammability standards for fire safety in electronics, aviation, and building products.
ABS alloys blend ABS with other polymers to further enhance targeted properties like chemical, UV, and scratch resistance.
Recycled ABS reuses plastic from post-consumer waste or manufacturing scrap, reducing environmental impact.
How to Select ABS Grade in Injection Molding
Properly selecting the optimal ABS grade maximizes performance, quality, and economics while meeting all application requirements. Neway listed some tips on how to select the optimal ABS grade for an injection molding application:
Determine essential performance requirements:
Mechanical properties needed (strength, impact resistance, hardness)
Thermal properties like heat deflection temperature
Flammability standards that must be met
Aesthetic needs - gloss, colors, special effects
Consider design and process factors:
Wall thickness and geometry
Tolerance and dimensional stability needs
Production volume and economics
Review general purpose ABS properties to see if they meet needs:
If not, look into modified grades like high heat, high impact, flame retardant
Consider any secondary properties needed:
UV/weathering resistance, chemical resistance, scratch resistance
It may point to an ABS alloy blend
Evaluate recycled ABS if high sustainability is desired:
Property tradeoffs may be acceptable for low-criticality parts
Get ABS grade samples to test if unknowns exist:
Validate performance, process settings, and economics
Collaborate with the material supplier and injection molder:
Leverage their expertise in grade selection for the application
Optimize processing for the selected grade
评论
发表评论