Ceramic Powder Injection Molding
The ceramic injection molding (CIM) process combines conventional plastic injection molding technology with the capability to obtain a wide range of ceramic properties. The manufacturing process produces complex, net-shape ceramic components with good mechanical properties.
It is suited for small-sized, high-complexity, Multifunctional Ceramic Parts mass production. Contact Neway today to get excellent CIM parts at competitive prices.
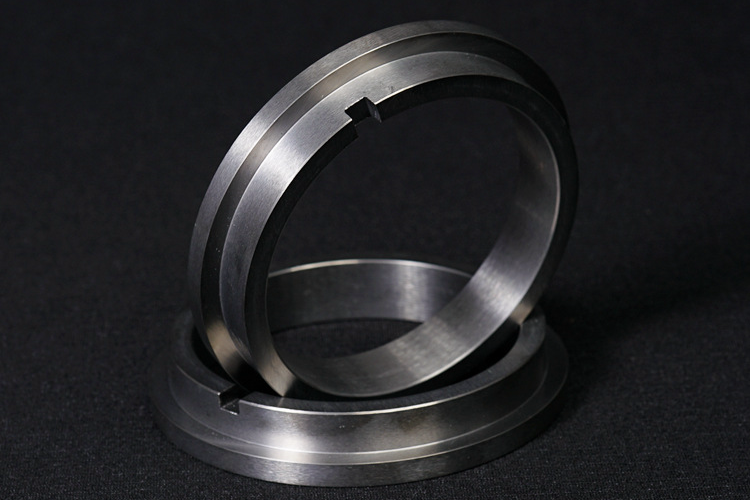
Ceramic Materials Optional for CIM Parts
Alumina (Al2O3) - Most typical material used in CIM. Provides high hardness and wear resistance. Used for industrial components, cutting tools, and bearings.
Zirconia (ZrO2) - Offers high fracture toughness and strength. It is stabilized with yttria. Used for valves, seals, and oxygen sensors.
Alumina-Zirconia - Composites combining properties of alumina and zirconia. Improved strength and toughness.
Silicon Carbide (SiC) - Excellent high-temperature properties. High hardness, strength, and corrosion resistance. Used for automotive and aerospace parts.
Silicon Nitride (Si3N4) - High strength at elevated temps, resistance to thermal shock. Used for gas turbine components, turbocharger rotors.
Boron Carbide - Extremely hard with good chemical resistance. Used for armor, nozzles, and seal rings.
Materials like tungsten carbide, macro (machinable glass ceramic), and PZT (lead zirconate titanate) piezoelectrics can also be used. The choice depends on the required material properties and application. CIM can produce complex parts from a wide range of technical ceramic materials.
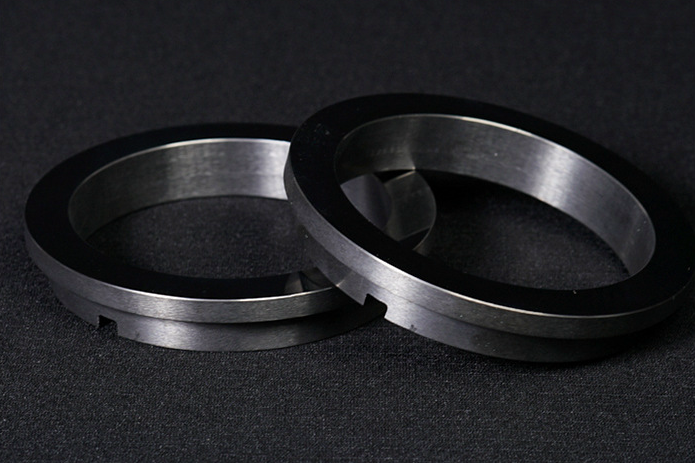
Material | Key Features | Typical Applications |
---|---|---|
Alumina (Al2O3) | High hardness, wear resistance | Cutting tools, bearings |
Zirconia (ZrO2) | High fracture toughness, strength | Valves, seals, sensors |
Alumina-Zirconia | Improved strength and toughness | Structural components |
Silicon Carbide (SiC) | High temperature strength | Automotive, aerospace parts |
Silicon Nitride (Si3N4) | Thermal shock resistance | Turbine components |
Boron Carbide | Extreme hardness, chemical resistance | Armor, nozzles, seal rings |
CIM-Ceramic Materials Comparison
In modern manufacturing, Ceramic Injection Molding (CIM) offers various ceramic materials with unique properties, making material selection a critical decision for optimal part performance. Conducting a CIM-Ceramic Materials Comparison provides invaluable insights into tailoring material properties to specific applications, optimizing performance, and managing costs. This strategic analysis ensures that the selected ceramic material aligns seamlessly with the intricate CIM process, leading to precision-engineered parts with desired characteristics and enhanced competitiveness in industries ranging from electronics to medical devices.
By rigorously evaluating factors such as mechanical strength, thermal stability, chemical resistance, and aesthetic appeal, a materials comparison empowers production engineers to make informed choices that elevate product quality and durability. Moreover, this approach aids in selecting ceramics that can be seamlessly integrated into the CIM process, ensuring efficient manufacturing and high-precision outcomes. Ultimately, a well-executed CIM-Ceramic Materials Comparison enhances the value proposition of Ceramic Injection Molding, offering a gateway to producing cutting-edge components that excel in performance, reliability, and cost-effectiveness.
CIM-Ceramic Materials Chemical Composition
Material | Al2O3 | ZrO2 | Al2O3-ZrO2 | SiC | Si3N4 | B4C |
---|---|---|---|---|---|---|
Alumina (Al2O3) | 99.5% | - | Variable | - | - | - |
Zirconia (ZrO2) | - | 94% | Variable | - | - | - |
Alumina-Zirconia | Varied | Varied | Varied | - | - | - |
Silicon Carbide | - | - | - | 100% SiC | - | - |
Silicon Nitride | - | - | - | - | Si3N4 100% | - |
Boron Carbide | - | - | - | - | - | B4C 100% |
CIM-Ceramic Materials Physical and Mechanical Properties
Material | Tensile Strength (MPa) | Yield Strength (MPa) | Impact Strength (MPa m^1/2) | Hardness (Vickers) | Young's Modulus (GPa) | Poisson's Ratio | Elongation (%) | Density (g/cm^3) |
---|---|---|---|---|---|---|---|---|
Alumina (Al2O3) | 330 | 270 | 5 | 1650 | 370 | 0.22 | 0.1 | 3.9 |
Zirconia (ZrO2) | 900 | 600 | 7 | 1200 | 200 | 0.3 | 0.5 | 6.1 |
Alumina-Zirconia | 500 | 400 | 6 | 1500 | 300 | 0.25 | 0.3 | 4.5 |
Silicon Carbide (SiC) | 400 | 350 | 4 | 2800 | 410 | 0.14 | 0.3 | 3.1 |
Silicon Nitride (Si3N4) | 600 | 480 | 5 | 1500 | 310 | 0.24 | 0.4 | 3.2 |
Boron Carbide | 450 | 350 | 3 | 2800 | 450 | 0.15 | 0.1 | 2.5 |
Key Features and Applications of CIM-Ceramics
1. Alumina (Al2O3):
Key Features: Alumina ceramics exhibit high mechanical strength, excellent electrical insulation properties, and superior thermal conductivity.
Application Examples: Alumina is commonly used for electrical insulators, substrates for electronic components, spark plug insulators, and heat sinks in various industries.
Reasons to Use: Its combination of thermal conductivity and electrical insulation makes alumina ideal for applications where heat dissipation and electrical isolation are crucial. Its stability at high temperatures and mechanical strength further enhance its utility.
2. Zirconia (ZrO2):
Key Features: Zirconia ceramics offer exceptional mechanical strength, wear resistance, and thermal stability. They can also exhibit transformation toughening, improving fracture toughness.
Application Examples: Zirconia is used in cutting tools, bearings, dental implants, and components that require high wear resistance and excellent mechanical performance.
Reasons to Use: Zirconia's exceptional mechanical properties make it suitable for demanding applications where wear resistance and strength are paramount. Its ability to resist thermal shock also extends its usability in high-temperature environments.
3. Alumina-Zirconia:
Key Features: Alumina-zirconia composites combine the desirable properties of both materials, offering a balance between mechanical strength, wear resistance, and thermal stability.
Application Examples: These composites find applications in cutting tools, ball bearings, and components that require toughness and wear resistance.
Reasons to Use: Alumina-zirconia composites leverage the strengths of alumina and zirconia, making them versatile choices for applications that demand a synergistic combination of properties.
4. Silicon Carbide (SiC):
Key Features: Silicon carbide ceramics offer exceptional hardness, chemical inertness, and high thermal conductivity, making them suitable for high-temperature and abrasive environments.
Application Examples: SiC is used in automotive components, mechanical seals, abrasive water jet nozzles, and aerospace applications.
Reasons to Use: SiC's hardness and resistance to wear and corrosion make it an excellent choice for applications where durability in harsh conditions is paramount.
5. Silicon Nitride (Si3N4):
Key Features: Silicon nitride ceramics exhibit high mechanical strength, excellent thermal shock resistance, and good chemical stability.
Application Examples: Si3N4 is used in cutting tools, bearings, gas turbine engine components, and automotive parts.
Reasons to Use: Its high mechanical strength and resistance to thermal shock make silicon nitride suitable for applications subjected to rapid temperature changes and high mechanical stresses.
6. Boron Carbide:
Key Features: Boron carbide ceramics offer exceptional hardness, chemical stability, and lightweight properties.
Application Examples: In nuclear applications, boron carbide is used in armor plates, nozzles for abrasive water jet cutting, and neutron absorbers.
Reasons to Use: Its extreme hardness and lightweight nature make boron carbide an excellent choice for applications that require superior protection and wear resistance without adding significant weight.
Each of these Ceramic Injection Molding materials presents distinct advantages for various applications. The selection of a material depends on the application's specific requirements, including mechanical demands, thermal conditions, and environmental factors. By leveraging the unique properties of these ceramics, manufacturers can create high-performance components tailored to their intended uses.
How to Select ceramic materials for Your CIM Parts
Selecting the suitable ceramic material for your Ceramic Injection Molding (CIM) parts is a critical step that can significantly impact your products' performance, durability, and overall success. Here's a systematic approach to guide you through the process of selecting the most suitable ceramic material for your CIM parts:
1. Define Application Requirements: Start by clearly defining the functional requirements of your CIM parts. Consider factors such as mechanical strength, thermal conductivity, wear resistance, chemical stability, electrical properties, and environmental conditions to which the parts will be exposed. Understanding these requirements is essential in narrowing down your material options.
2. Identify Critical Properties: Based on your application requirements, identify the fundamental properties the ceramic material must possess. For instance, if your CIM parts need to withstand high temperatures, focus on materials with excellent thermal stability. If wear resistance is crucial, prioritize materials known for their mechanical strength and hardness.
3. Research Material Options: Conduct thorough research to identify ceramic materials that align with your identified critical properties. Consider materials like alumina (Al2O3), zirconia (ZrO2), silicon carbide (SiC), silicon nitride (Si3N4), and boron carbide based on their unique characteristics. Research available data, technical specifications, and case studies related to these materials.
4. Evaluate Material Performance: Utilize testing data and material performance charts to compare how different ceramics perform to your application's requirements. Focus on parameters such as tensile strength, hardness, thermal conductivity, chemical resistance, and any specific property relevant to your CIM parts.
5. Consider Processing Requirements: Consider the processing steps involved in CIM, such as injection molding, debinding, and sintering. Some ceramic materials may have specific processing requirements due to their composition or sensitivity to temperature changes. Ensure that the chosen material is compatible with the CIM process.
6. Assess Cost and Availability: Consider the cost of the ceramic material and its availability in the quantities you require. Some high-performance ceramics can be expensive, so finding a balance between material quality and production cost is essential.
7. Analyze Application Examples: Look for real-world application examples where similar ceramic materials have been successfully used. Case studies and success stories can provide valuable insights into how a specific material performs in practical applications like yours.
8. Consult with Experts: Engage with Neway's materials scientists, engineers, or consultants specializing in ceramics. They can provide expert advice on material selection based on your specific needs. Their expertise can help you make well-informed decisions.
9. Prototype and Test: Create prototypes using the selected ceramic material and test them under relevant conditions. This step can provide valuable feedback on how well the material meets your requirements in practice.
10. Optimize Material Choice: Optimize your material choice based on testing results and expert recommendations. Consider how the selected material aligns with performance, processing, cost, and availability factors.
In summary, selecting ceramic materials for your CIM parts involves a comprehensive analysis of application requirements, material properties, processing considerations, cost, and real-world performance. By following a structured approach and leveraging available resources, you can make informed decisions that lead to successful CIM parts with optimal performance and longevity.
Why Choose Neway for CIM Services
Choosing Neway for CIM service was a game-changer for our production needs. With 30 years of experience in custom injection molding, their expertise shone through every step of the process. They delivered top-notch quality from Metal Injection Molding (MIM) to Ceramic Injection Molding (CIM). The 20% discount on our first order made the decision even more accessible. Neway's commitment to excellence has earned our trust and loyalty. - Alfred Melson
Embark on a production journey with Neway's unparalleled CIM service. With over three decades of mastery in custom injection molding, Neway is your seasoned partner. Their offerings span the horizon from Metal Injection Molding (MIM) to Powder Compression Molding (PCM). Embrace the precision of Ceramic Injection Molding (CIM) or delve into the versatility of Plastic Injection Molding. The promise of quality is unwavering, and the first order beckons with a 20% discount. Join hands with Neway and redefine your manufacturing experience.
Mark's Metalworks hit the jackpot when they chose Neway for their CIM needs. With a legacy of 30 years, Neway's injection molding services hit the bullseye. From Metal Injection Molding (MIM) that delivered precision to Ceramic Injection Molding (CIM) that wowed with versatility, every project was a success. Moreover, the 20% discount on the first order sweetened the deal. Mark's Metalworks found not just a service but a partner in Neway.
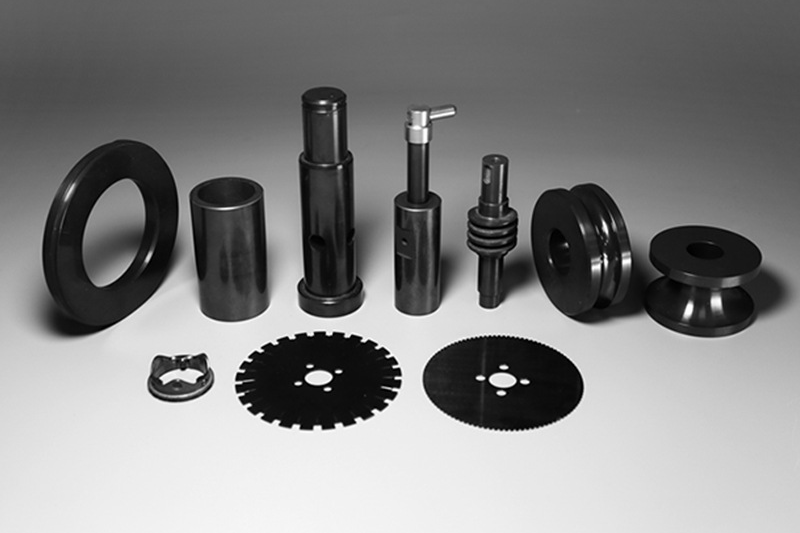
评论
发表评论