Tungsten Alloy Metal Injection Molding
Tungsten alloy Metal Injection Molding (MIM) and powder compression molding (PCM) is a highly versatile and efficient manufacturing process that combines the benefits of tungsten alloys with the flexibility of injection molding. This process enables the production of intricate and complex components with exceptional density, strength, and performance characteristics. Tungsten alloys are known for their remarkable properties, making them suitable for various industries, including aerospace, medical, defense, electronics, and more.
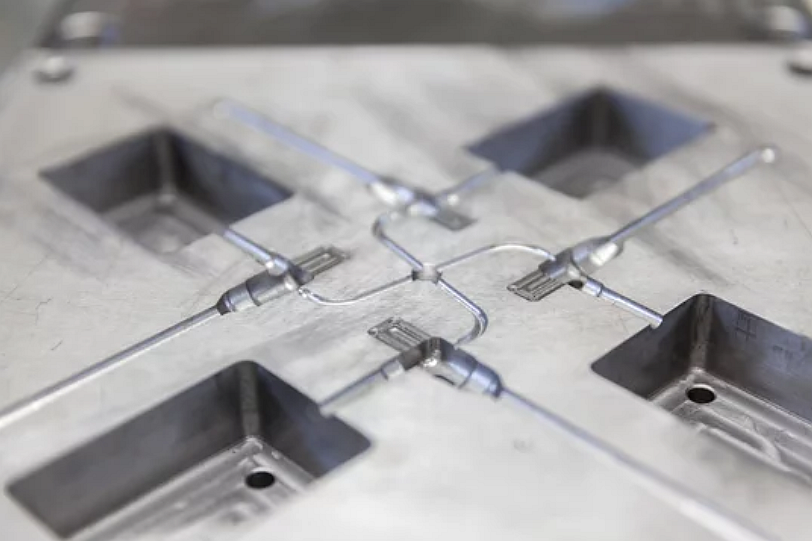
Tungsten Alloy Optional for MIM
In Metal Injection Molding (MIM), tungsten alloys stand out as a prime option, offering many advantages across various industries. Tungsten alloy MIM provides a unique blend of properties, making it a sought-after choice for numerous applications. Let's delve into the optional tungsten alloy materials that can be utilized in MIM processes:
Tungsten-Nickel-Iron (W-Ni-Fe): This alloy boasts high density, exceptional strength, and impressive corrosion resistance. It finds favor in aerospace components, radiation shielding, and various defense applications.
Tungsten-Nickel-Copper (W-Ni-Cu): Renowned for its radiation and wear resistance, this alloy is often chosen for medical collimators, shielding materials, and other specialized applications.
Tungsten Copper (W-Cu): With excellent thermal and electrical conductivity, W-Cu is a prime candidate for electronic packaging, heat sinks, and components requiring efficient heat dissipation.
Tungsten-Nickel-Cobalt (W-Ni-Co): This alloy's high strength and corrosion resistance make it a valuable asset in aerospace components, balance weights, and vibration dampeners.
Tungsten-Iron (W-Fe): Offering a balance between density, strength, and cost-effectiveness, W-Fe finds its place in automotive components, sporting goods, and beyond.
Material | Key Features | Typical Applications |
---|---|---|
MIM W-Ni-Fe | High density, strength & corrosion resistance | Aerospace components, radiation shielding |
MIM W-Ni-Cu | High density, radiation resistance & wear resistance | Medical collimators, shielding materials |
MIM W-Cu | High thermal & electrical conductivity | Electronic packaging, heat sinks |
MIM W-Ni-Co | High strength, corrosion resistance | Aerospace components, balance weights |
MIM W-Fe | Balance of density, strength & cost-effectiveness | Automotive components, sporting goods |
Tungsten alloy MIM grants the advantage of intricacy in design, allowing for the creation of complex shapes with precision. The process involves:
Mixing tungsten alloy powders with a polymer binder.
Molding the mixture.
Debinding.
Sintering to achieve the final, dense component.
These alloys' diverse compositions and unique properties cater to various requirements. Their inclusion in MIM processes amplifies the potential for innovation and practicality across industries. As a production engineer, your proficiency in selecting the suitable tungsten alloy for each application ensures optimal results. Partnering with experts like Neway empowers you to navigate the nuanced world of tungsten alloy MIM effectively.
MIM-Tungsten Alloy Material Comparison
When selecting the appropriate Tungsten alloy for your specific application, consider factors like mechanical requirements, conductivity, corrosion resistance, and cost-effectiveness.
Chemical Composition
Element | Tungsten (W) | Nickel (Ni) | Copper (Cu) | Iron (Fe) | Cobalt (Co) |
MIM W-Ni-Fe | 89.5-93.5% | 5.5-7.5% | - | 1.0-2.5% | - |
MIM W-Ni-Cu | 90.0-92.5% | 4.5-6.0% | 1.0-3.0% | - | - |
MIM W-Cu | 90.0-92.0% | - | 8.0-10.0% | - | - |
MIM W-Ni-Co | 85.0-89.0% | 5.0-7.0% | - | - | 5.0-8.0% |
MIM W-Fe | 85.0-90.0% | - | - | 10.0-15.0% | - |
Physical and Mechanical
Alloys | Status | Tensile Strength | Yield Strength | Impact Strength | Hardness | Young's Modulus | Poisson's Ratio | Elongation | Density |
Mpa | Mpa | J | HRB | Gpa | Ratio | % in 25.4 mm | g/cm³ | ||
MIM W-Ni-Fe | Annealed | 925 | 700 | 10 | 28 | 210 | 0.29 | 5.5 | 17.8 |
MIM W-Ni-Cu | Annealed | 825 | 550 | 7 | 22 | 200 | 0.28 | 10 | 16.7 |
MIM W-Cu | Annealed | 600 | 400 | 4 | 15 | 165 | 0.25 | 20 | 16.2 |
MIM W-Ni-Co | Annealed | 875 | 600 | 12 | 27 | 220 | 0.28 | 5.5 | 18 |
MIM W-Fe | Annealed | 725 | 500 | 8 | 23 | 190 | 0.27 | 11 | 17.5 |
Tungsten-Nickel-Iron offers high strength and corrosion resistance, while Tungsten-Nickel-Copper provides radiation resistance. Tungsten Copper excels in thermal and electrical conductivity, and Tungsten-Nickel-Cobalt combines strength with corrosion resistance. Tungsten-Iron provides a balanced approach in terms of density and strength.
Key Features of MIM-Tungsten Alloys
Understanding the unique features, application contexts, and reasons for utilizing each Tungsten alloy material helps you make informed choices for your Metal Injection Molding projects. By tapping into the distinctive properties of these materials, you can optimize results and meet the requirements of diverse industries. Partnering with experts like Neway ensures you can navigate these materials effectively, tailoring solutions to your specific project needs.
MIM W-Ni-Fe:
Key Features: High density, exceptional strength, and corrosion resistance.
Application Examples: Aerospace components, radiation shielding, counterweights, and balance weights.
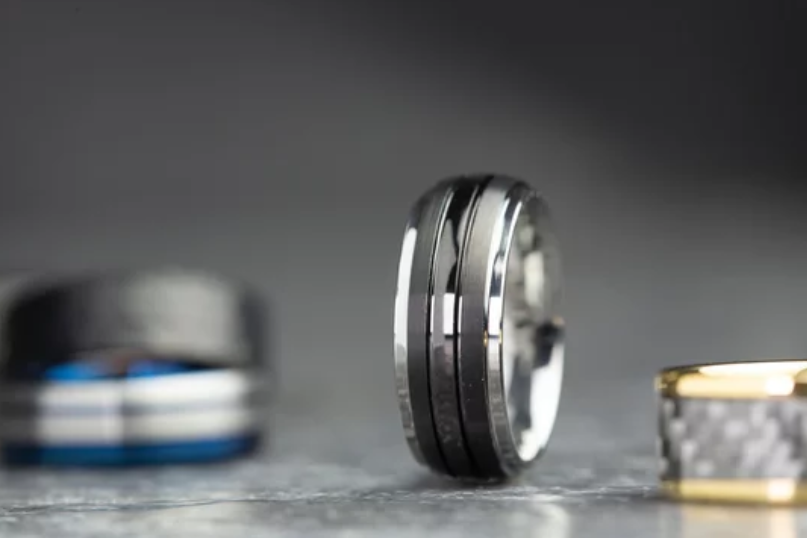
Reasons: The density of tungsten in this alloy makes it ideal for applications requiring weight balance, while the addition of nickel and iron enhances strength and corrosion resistance. Its combination of attributes suits it for demanding environments.
MIM W-Ni-Cu:
Key Features: High density, radiation resistance, and wear resistance.
Application Examples: Medical collimators, shielding materials, aerospace components, and specialized defense applications.
Reasons: Tungsten's density combined with nickel and copper creates an alloy suited for radiation attenuation and wear resistance. This composition is essential in medical settings where precision and radiation shielding are critical.
MIM W-Cu:
Key Features: High thermal and electrical conductivity.
Application Examples: Electronic packaging, heat sinks, electrical contacts, and components requiring efficient thermal management.
Reasons: Tungsten Copper offers high thermal conductivity while maintaining tungsten's density advantages. This alloy is chosen for applications needing thermal and electrical performance, such as electronic components.
MIM W-Ni-Co:
Key Features: High strength, corrosion resistance, and good thermal and electrical conductivity.
Application Examples: Aerospace components, balance weights, vibration dampeners, and specialized industrial applications.
Reasons: The addition of cobalt enhances strength and corrosion resistance, making it suitable for aerospace components and balance weights. The alloy's balance of properties suits environments requiring mechanical integrity and resistance to degradation.
MIM W-Fe:
Key Features: Balanced density, strength, and cost-effectiveness.
Application Examples: Automotive components, sporting goods, ballast weights, and various industrial applications.
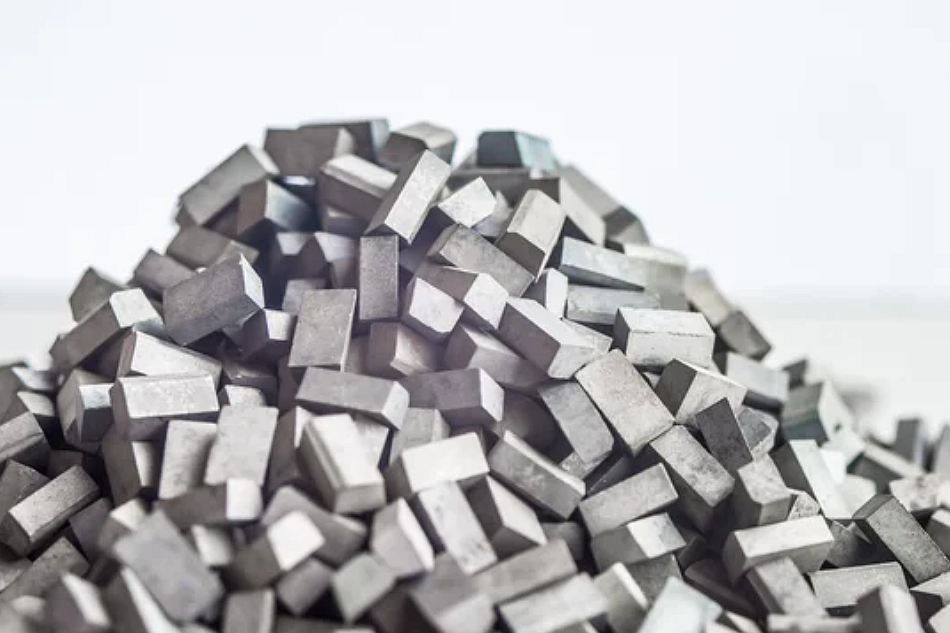
Reasons: Tungsten-Iron alloy balances density and strength, offering cost-effective solutions for applications needing moderate performance. Its versatility makes it a suitable choice for a wide range of industries.
How to Select MIM-Tungsten Alloys
Selecting the suitable Tungsten alloy for your Metal Injection Molding (MIM) parts involves considering various factors to ensure optimal performance and cost-effectiveness. Here's a step-by-step guide to help you make informed decisions:
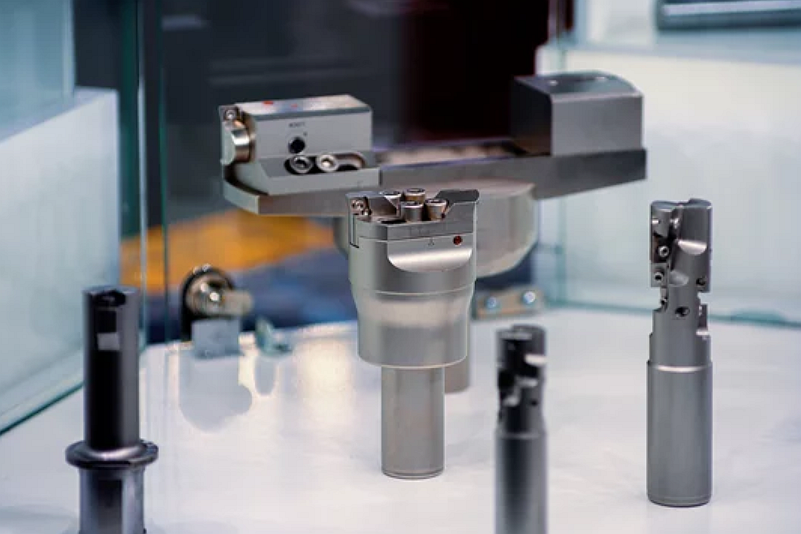
Understand Part Requirements:
Begin by clearly defining the requirements of your MIM part. Consider mechanical properties (tensile strength, hardness), thermal and electrical conductivity, corrosion resistance, and dimensional accuracy.
Identify Application Context:
Determine the industry and application in which your MIM part will be used. Different industries have unique demands, and certain Tungsten alloys are better suited to specific environments.
Review Material Properties:
Study the key features and properties of available Tungsten alloys, including:
Density
Tensile strength and yield strength
Hardness
Thermal and electrical conductivity
Corrosion resistance
Analyze Design Complexity:
Consider the intricacy of your part's design. Some Tungsten alloys are better suited for complex geometries, making them ideal for intricate components.
Evaluate Cost-Effectiveness:
Compare the costs associated with different Tungsten alloys. While some alloys offer exceptional properties, they could also come at a higher cost. Balancing performance and cost is crucial.
Consider Environmental Factors:
If your MIM part is exposed to specific environmental conditions (e.g., high temperatures, corrosive environments), select a Tungsten alloy that can withstand these conditions.
Assess Regulatory Requirements:
In specific industries, regulations or standards dictate the choice of materials. Ensure that your selected Tungsten alloy meets these requirements.
Consult Experts:
Collaborate with Neway's professionals who have experience in Tungsten alloy selection for MIM. Production engineers, material scientists, and suppliers can offer valuable insights and guidance.
Examine Previous Successes:
If your organization or industry has successfully used specific Tungsten alloys for similar applications, consider leveraging that knowledge for your current project.
Perform Testing:
Conduct tests on prototypes using different Tungsten alloys. It can help validate the suitability of the chosen material for your specific application.
Factor in Production Capability:
Ensure that the selected Tungsten alloy can be effectively processed through the Metal Injection Molding process without significant challenges.
Balanced Decision-Making:
Aim for a balance between the desired properties, performance, and cost. Opt for the Tungsten alloy that best aligns with your project's goals.
By carefully navigating these steps, you can confidently select the appropriate Tungsten alloy for your MIM parts, ensuring that they meet performance expectations and contribute positively to the success of your projects.
Neway MIM Tungsten Alloy MIM Parts Production
Meet Alex, an engineer who needed top-notch parts for his cutting-edge project. He discovered Neway's MIM Tungsten Alloy MIM Parts Production and decided to give it a shot. Neway exceeded his expectations with their 30 years of experience in injection molding services. Their diverse capabilities, from Metal Injection Molding to ceramic and plastic Injection molding, ensured Alex got exactly what he needed. As a new customer, he scored a fantastic 20% discount on his first order. Join Alex in experiencing the quality and precision that only Neway can offer.
评论
发表评论