Magnetic Alloy Metal Injection Molding
Magnetic Alloy Metal Injection Molding (MIM) is a cutting-edge manufacturing process offered by Neway that combines the versatility of plastic injection molding with the superior properties of magnetic alloys. It involves finely powdered MIM magnetic alloy materials, such as MIM-Fe-50Ni, MIM-Fe-3Si, and MIM-Fe-50Co, mixed with a binder to form a feedstock. This feedstock is then injected into molds with high precision. After shaping, the components undergo a debinding and sintering to achieve their final metallic form. MIM enables intricate geometries, exceptional magnetic characteristics, and high production efficiency, making it an ideal solution for various industries.
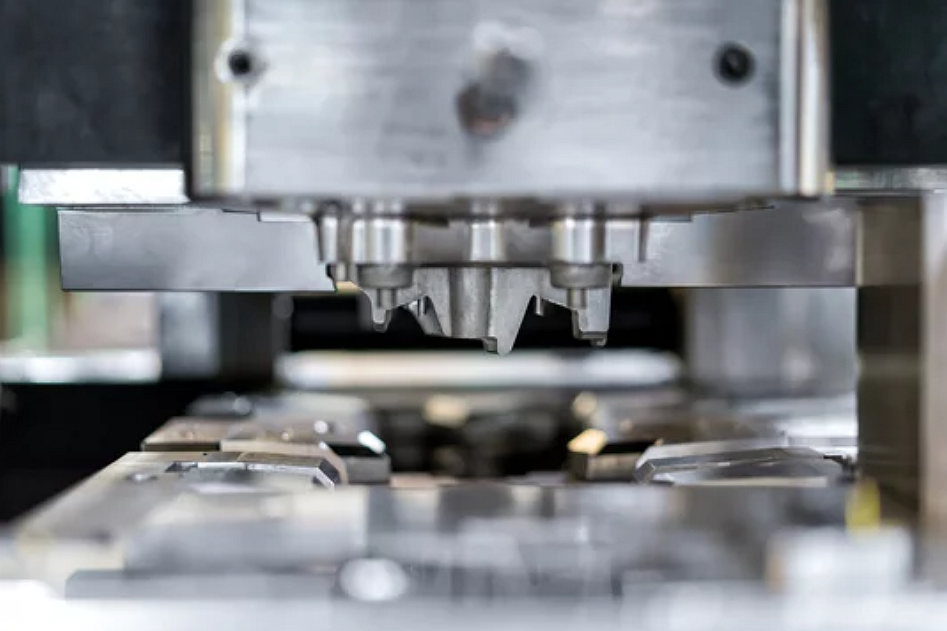
Magnetic Alloy Optional for MIM
MIM-Fe-50Ni
Magnetic Strength: Exhibits high magnetic flux density, ideal for applications requiring strong magnetic properties.
Thermal Stability: Maintains magnetic performance even under varying temperature conditions.
Applications: Suited for sensors, actuators, and motors demanding robust magnetic capabilities.
MIM-Fe-3Si
Corrosion Resistance: Exceptional corrosion resistance, making it suitable for applications in harsh environments.
Magnetic Conductivity: Maintains good magnetic conductivity despite its corrosion-resistant properties.
Applications: Used in magnetic shielding, aerospace components, and other industries requiring magnetic response and corrosion protection.
MIM-Fe-50Co
Temperature Stability: Demonstrates stability in magnetic properties across a wide temperature range.
Magnetic Performance: Provides strong magnetic characteristics combined with high-temperature tolerance.
Applications: Applied in magnetic couplings, medical devices, and other fields requiring reliable performance at elevated temperatures.
MIM-2200 (Fe-2%Ni)
Balanced Properties: Offers a harmonious blend of magnetic response and structural integrity.
Magnetic Permeability: Shows controlled permeability for use in electromagnetic components.
Applications: Utilized in solenoids, transformers, and magnetic cores, a balanced approach to magnetic behavior is crucial.
MIM-430L
Dual Properties: Combines good magnetic response with stainless steel properties.
Versatility: Suitable for applications requiring both magnetism and corrosion resistance.
Applications: Used in electronics, automotive components, and other sectors where a balance of magnetic and stainless characteristics is required.
Magnetic Alloy | Key Features | Applications |
---|---|---|
MIM-Fe-50Ni | High magnetic strength | Sensors, actuators, motors |
MIM-Fe-3Si | Excellent corrosion resistance | Magnetic shielding, aerospace components |
MIM-Fe-50Co | Superior temperature stability | Magnetic couplings, medical devices |
MIM-2200 (Fe-2%Ni) | Balanced magnetic properties and structure | Solenoids, transformers, magnetic cores |
MIM-430L | Good magnetic response and stainless properties | Electronics, automotive components |
MIM-Magnetic Alloy Comparison
Explore a comprehensive comparison of Neway's cutting-edge Magnetic Alloy materials manufactured through Metal Injection Molding (MIM). Discover the distinct properties and applications of MIM-Fe-50Ni, MIM-Fe-3Si, MIM-Fe-50Co, MIM-2200 (Fe-2%Ni), and MIM-430L. Delve into their unique compositions, magnetic strengths, corrosion resistance, and more. Gain insights into how these materials excel in various industries, from sensors and actuators to aerospace components. Uncover the precision and innovation that define Neway's commitment to delivering high-quality solutions for diverse production engineering needs.
Chemical Composition
Magnetic Alloy | Iron (Fe) (%) | Nickel (Ni) (%) | Silicon (Si) (%) | Cobalt (Co) (%) | Chromium (Cr) (%) | Carbon (C) (%) | Manganese (Mn) (%) | Others (%) |
MIM-Fe-50Ni | 50 | 50 | 0.3 | - | - | <0.02 | <0.20 | Balance (Fe) |
MIM-Fe-3Si | 96.5 | - | 3 | - | - | <0.05 | <0.10 | - |
MIM-Fe-50Co | 50 | - | - | 50 | - | <0.02 | <0.10 | Balance (Fe) |
MIM-2200 (Fe-2%Ni) | 98 | 2 | - | - | - | <0.05 | <0.10 | - |
MIM-430L | 80 | - | - | - | 17 | <0.008 | <0.40 | Balance (Fe) |
Physical and Mechanical
Magnetic Alloy | Status | Tensile Strength (MPa) | Yield Strength (MPa) | Impact Strength (J) | Hardness (HRC) | Young's Modulus (GPa) | Poisson's Ratio | Elongation (%) | Density (g/cm³) |
---|---|---|---|---|---|---|---|---|---|
MIM-Fe-50Ni | Sintered | 500 | 300 | 25 | 30 | 160 | 0.29 | 10 | 7.5 |
MIM-Fe-3Si | Sintered | 450 | 250 | 20 | 28 | 140 | 0.30 | 12 | 7.2 |
MIM-Fe-50Co | Sintered | 520 | 320 | 30 | 32 | 175 | 0.28 | 9 | 7.7 |
MIM-2200 (Fe-2%Ni) | Sintered | 480 | 280 | 22 | 29 | 150 | 0.31 | 11 | 7.4 |
MIM-430L | Sintered | 420 | 220 | 18 | 27 | 130 | 0.32 | 14 | 7.0 |
Key Features of MIM-Magnetic Alloy
MIM-Fe-50Ni:
Key Features: High magnetic strength, excellent thermal stability.
Application Examples: Sensors, actuators, and motors requiring robust magnetic properties.
Reasons to Choose: MIM-Fe-50Ni is a top choice for applications demanding solid and stable magnetic performance. Its ability to maintain magnetic strength over varying temperatures ensures reliable operation in diverse environments.
MIM-Fe-3Si:
Key Features: Exceptional corrosion resistance, good magnetic conductivity.
Application Examples: Aerospace components, magnetic shielding in harsh environments.
Reasons to Choose: MIM-Fe-3Si offers a unique combination of corrosion resistance and magnetic properties, making it suitable for applications where both factors are crucial. Its corrosion resistance ensures longevity in challenging conditions.
MIM-Fe-50Co:
Key Features: Superior temperature stability and magnetic solid performance.
Application Examples: Medical devices, magnetic couplings in high-temperature environments.
Reasons to Choose: MIM-Fe-50Co excels in applications requiring consistent magnetic strength at elevated temperatures. Its stability and reliability make it a preferred choice for industries dealing with heat and magnetic interaction.
MIM-2200 (Fe-2%Ni):
Key Features: Balanced magnetic properties and structure.
Application Examples: Solenoids, transformers, electromagnetic components.
Reasons to Choose: MIM-2200 offers a harmonious magnetic response and structural integrity blend. This balance makes it ideal for applications where precise magnetic behavior is essential for optimal performance.
MIM-430L:
Key Features: Combines magnetic response with stainless properties.
Application Examples: Automotive components, electronics.
Reasons to Choose: MIM-430L is chosen for magnetism and corrosion resistance applications. Its versatility makes it an excellent solution for industries where a combination of properties is essential.
How to Select MIM-Magnetic Alloy
Selecting the appropriate MIM-Magnetic Alloy for your Metal Injection Molding (MIM) parts involves carefully assessing your requirements and the properties different alloys offer.
Identify Part Requirements:
Define the essential characteristics your MIM part needs, such as magnetic strength, corrosion resistance, temperature stability, and mechanical properties.
Understand Alloy Properties:
Study the properties of different MIM-Magnetic Alloys, including MIM-Fe-50Ni, MIM-Fe-3Si, MIM-Fe-50Co, MIM-2200 (Fe-2%Ni), and MIM-430L. Consider factors like magnetic strength, corrosion resistance, temperature tolerance, and mechanical behavior.
Match Properties to Requirements:
Compare the properties of each alloy to your part's requirements. Choose an alloy that aligns with the desired characteristics. For instance, select MIM-Fe-50Ni for strong magnetic performance or MIM-Fe-3Si for corrosion resistance.
Consider Manufacturing Process:
Understand the manufacturing process involved in producing MIM parts from each alloy. Ensure that the chosen alloy can be effectively processed using Metal Injection Molding techniques.
Application-Specific Factors:
Evaluate the specific conditions your MIM part will be exposed to, such as temperature variations, corrosive environments, or mechanical stress. Choose an alloy that can withstand these conditions without compromising performance.
Industry Standards and Certifications:
Check if the chosen MIM-Magnetic Alloy meets the industry standards and certifications required for your application. It is crucial, especially for applications in fields like medical devices or aerospace.
Consultation and Expertise:
Seek advice from experts in the field of production engineering or material science. Consult with manufacturers like Neway who specialize in MIM-Magnetic Alloys. They can provide valuable insights based on their experience and knowledge.
Testing and Prototyping:
Conduct testing and prototyping with the selected alloy to validate its performance under real-world conditions. This step can help identify any unforeseen challenges and allow for adjustments if necessary.
Cost Consideration:
Factor in the cost of the alloy, including production and processing expenses. Balance the alloy's benefits with its cost to ensure cost-effectiveness in your application.
Long-Term Viability:
Consider the long-term availability of the chosen alloy. Ensure that the alloy will continue to be produced and supported for the lifespan of your product.
By following these steps, you can confidently select the most suitable MIM-Magnetic Alloy for your MIM parts, ensuring optimal performance, durability, and efficiency in your production engineering endeavors.
Why Choose Neway for Magnetic Alloy MIM Parts
John's Manufacturing was in a fix – they needed precision parts, and they needed them fast. That's when they discovered Neway. With 30 years of experience, Neway's expertise in Metal Injection Molding (MIM), Ceramic Injection Molding (CIM), and plastic injection molding was a game-changer. John's Manufacturing got the needed parts and a fantastic 20% discount on their initial order. The rest, as they say, is history. Join the ranks of satisfied customers with Neway.
评论
发表评论