Sand casting is a typical manufacturing process for metal parts with complex geometries and low to medium production volumes. It involves creating reusable molds and cores from sand, then pouring molten metal into the cavity to form near-net-shape castings. Custom sand casting services create these molds based on each customer’s unique specifications. But is custom sand casting cost-effective compared to CNC machining service or injection molding service? Here are the key factors to consider:
Lower Initial Costs
The main advantage of custom sand casting is significantly lower tooling costs than die casting service or metal injection molding (MIM). Only a one-time sand mold and core package must be produced per unique part geometry. Once the initial prototypes are approved, rapid iteration and adjustments are possible with sand molds. It avoids the expensive CNC machining of hardened steel tooling. Total upfront costs for simple cast geometries can be under $2,000. Even complex castings with four core boxes stay below $5,000. This economical tooling makes sand casting ideal for lower-volume production runs.
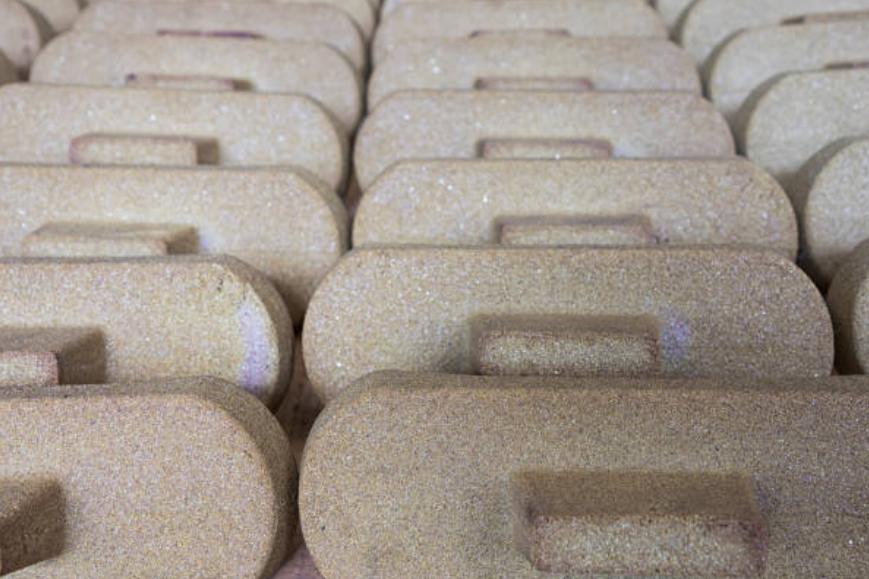
Faster Lead Times
Turnaround time from final 3D CAD models to production samples is much quicker for sand casting compared to tooling-intensive processes. Simple castings can be sampled within 2-3 weeks, while complex multi-core castings take 4-6 weeks on average. Most lead time is spent designing the gating, rising, and molding approach, not producing the tooling itself. It facilitates rapid design verification testing. Depending on the complexity, sand cast molds can be re-used 10-100 times. Repeated orders can ship in 1-2 weeks when combined with the reusable pattern inventory.
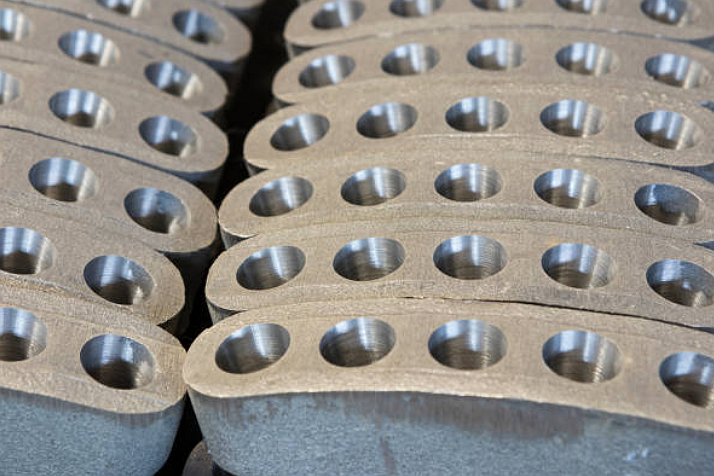
Design Flexibility & Iteration
Tooling and design changes are significant cost drivers for processes like die casting and injection molding where hardened steel tooling is required. But with sand casting, modifications to the cast part geometry can be incorporated by adjusting the sand core design. It avoids the scrapping of expensive tooling when engineering changes occur. Areas prone to porosity or sink can be altered in the mold to improve casting quality. Custom sand casters work interactively with customers through this iterative process until the optimal mold design is achieved.
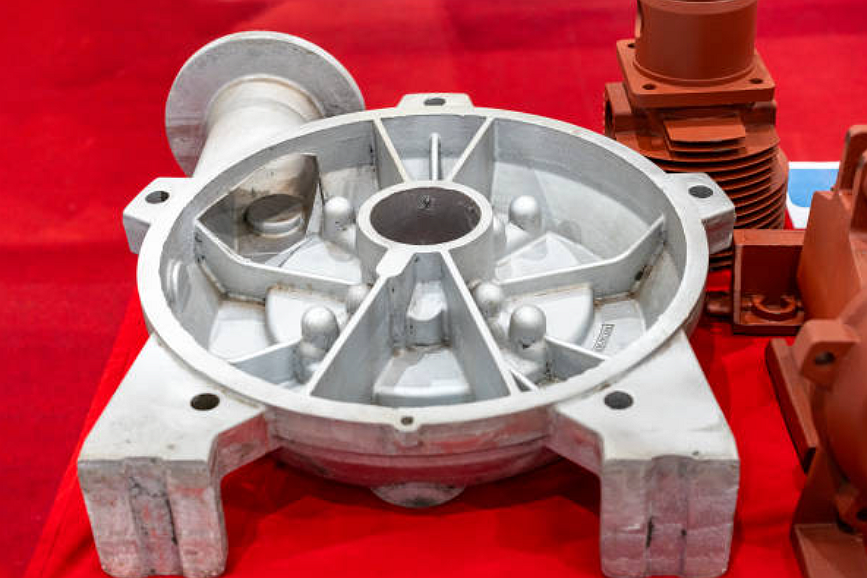
Wide Range of Materials
Sand casting material selection enables nearly any ferrous or non-ferrous alloy to be cast, including steels, stainless steel, cast iron, aluminum, magnesium, zinc, bronze, and copper alloys. Lesser-used exotic alloys are also possible. Only a few alloy restrictions related to crack susceptibility exist. It gives engineers broad latitude when selecting materials for strength, corrosion resistance, high-temperature properties, appearance, machinability, and other needs. The extensive choice of materials surpasses what is available with die casting or MIM processes.
Large Size Capabilities
Sand castings can be produced from ounces up to 50 tons. Upper-size capabilities exceed alternate technologies like investment casting or die casting, where maximum component weights are 1000 pounds and 25 pounds, respectively. Sand casting is routinely used for large equipment housings, machine bases, pulleys, valve bodies, and other oversized parts not practical with other processes. There is also no limit on minimum section thickness, allowing fragile, delicate designs.
Post-Casting Machining
Many sand castings undergo secondary CNC machining or surface treatment to achieve tighter tolerances, improved surface finishes, or complex geometries. Its hybrid approach uses ‘near net shape’ casting; precision machines only require features. Combining casting and machining can be more efficient than pure machining starting from a raw block. Typical machining allowances for sand-cast parts range from 0.100-0.500 inches. Overall costs are decreased compared to pure machining.
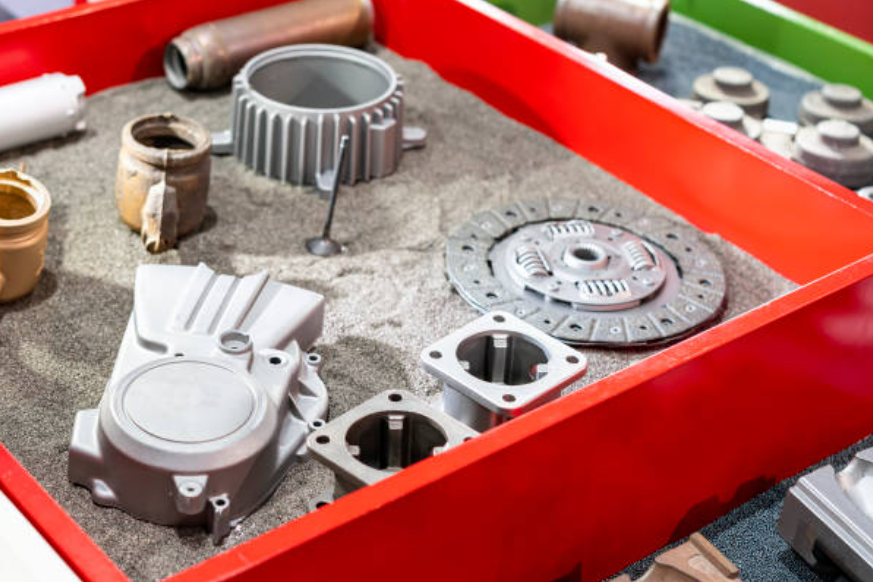
Summary
For low-mid volume complex metal components, custom sand casting provides an ideal balance of upfront costs, lead time, design flexibility, material options, size capabilities, and integration with secondary machining. These benefits make sand casting very cost-competitive, outpacing die casting and MIM for per-part costs at volumes under 1000-5000 units. Manufacturers can get the most cost-effective production process for their specific component requirements by leveraging a qualified sand caster.
Why Choose Neway for Custom Sand Casting?
"Thanks to Neway's custom sand casting expertise, we were able to rapidly prototype our breakthrough power tool design and bring it to market ahead of schedule. Their craftsmen worked tirelessly to deliver flawless castings and injection molded parts that exceeded our strict specifications. And their experience optimizing designs for manufacturability was invaluable. I'm not sure where we'd be today without their partnership in creating this revolutionary product." - Steve J., Acme Power Tools
评论
发表评论