Tool Steel Metal Injection Molding
MIM (Metal Injection Molding) Tool steel is a type of high-carbon steel specifically designed to be used to produce tools, dies, and cutting implements. It possesses exceptional hardness, wear resistance, and toughness, making it suitable for applications where tools are subjected to high stress, repeated impact, and abrasive wear. Tool steel often contains significant alloying elements like chromium, vanadium, tungsten, and molybdenum, contributing to its distinct properties.
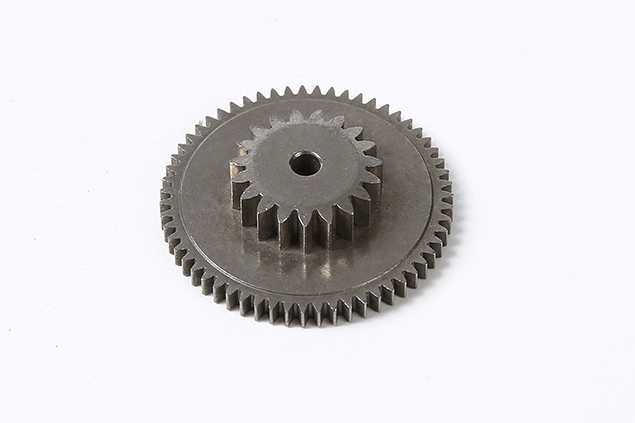
Tool steel metal injection molded parts shine in automotive, medical, aerospace, electronics, industrial machinery, and consumer goods applications. Their intricate shapes, precision, and durability make them indispensable in realms demanding high performance. Tool steel MIM parts carve a niche with advantages encompassing intricate geometries, superior precision, flexible material composition, minimal waste, and cost-effectiveness. Neway's proficiency in metal injection molding and precision casting empowers them to engineer top-notch tool steel MIM parts, fortifying diverse industries with innovation and reliability.
Tool Steels Optional for MIM
Steel Grade | Key Features | Typical Applications |
---|---|---|
A2 | High wear resistance and toughness | Blanking, forming, and trimming dies |
M2 | Excellent heat resistance and wear properties | Cutting tools, drills, and milling cutters |
M4 | High abrasion resistance and impact strength | Cold work applications, punches, and dies |
D2 | Exceptional wear resistance and hardness | Stamping and forming dies, punches |
S7 | High-impact strength and machinability | Chisels, pneumatic tools, shear blades |
H13 | Excellent thermal conductivity and hot hardness | Die casting dies, extrusion tooling |
T15 | Exceptional wear resistance at high temperatures | Metal cutting tools, broaches, and hobs |
Key Features of MIM-Tool Steels
A2:
High wear resistance and toughness.
Suitable for applications involving blanking, forming, and trimming dies.
Excellent dimensional stability and heat treatment response.
Often used for tools subjected to repeated impacts and moderate-to-high wear.
M2:
Exceptional heat resistance and wear properties.
Well-suited for cutting tools, drills, and milling cutters.
High red hardness and excellent retention of hardness at elevated temperatures.
Ideal for metal cutting applications requiring high-speed operation.
M4:
High abrasion resistance and impact strength.
Commonly utilized in cold work applications, such as punches, dies, and cutting tools.
Offers superior wear resistance even under challenging conditions.
Maintains hardness and toughness at both low and elevated temperatures.
D2:
Exceptional wear resistance and hardness.
Frequently used for stamping and forming dies, punches, and similar tools.
Provides excellent edge retention and dimensional stability.
Resistant to abrasion and deformation during prolonged use.
S7:
High impact strength and machinability.
Suited for applications requiring chisels, pneumatic tools, and shear blades.
Offers good toughness and resistance to shock loading.
Provides ease of machining and forging due to its composition.
H13:
Excellent thermal conductivity and hot hardness.
Commonly chosen for die casting dies and extrusion tooling.
Retains its mechanical properties at elevated temperatures.
Offers superior thermal fatigue resistance and wear resistance.
T15:
Exceptional wear resistance at high temperatures.
Well-suited for metal cutting tools, broaches, and hobs.
Exhibits superior red hardness and toughness in high-temperature environments.
Suitable for applications requiring precision cutting and extended tool life.
MIM Tool Steel Material Comparison
Steel Grade | Carbon (C) | Manganese (Mn) | Silicon (Si) | Chromium (Cr) | Molybdenum (Mo) | Vanadium (V) | Other Elements |
---|---|---|---|---|---|---|---|
A2 | 1.00% | 0.80% | 0.30% | 5.00% | 0.90% | 0.20% | - |
M2 | 0.85% | 0.30% | 0.30% | 4.20% | 5.00% | 6.40% | - |
M4 | 1.30% | 0.20% | 0.25% | 4.00% | 4.75% | 5.25% | - |
D2 | 1.55% | 0.40% | 0.40% | 11.50% | 0.85% | 0.20% | - |
S7 | 0.50% | 0.70% | 1.00% | 3.25% | 1.40% | - | - |
H13 | 0.40% | 0.40% | 1.00% | 5.00% | 1.30% | 0.95% | - |
T15 | 1.30% | 0.20% | 0.20% | 4.00% | 9.00% | 4.00% | Cobalt (Co): 5.00% |
Steel Grade | Density (g/cm³) | Hardness (HRC) | Tensile Strength (MPa) | Yield Strength (MPa) | Elongation (%) | Impact Toughness (J/cm²) | Thermal Conductivity (W/m·K) | Coefficient of Thermal Expansion (10^-6/°C) |
---|---|---|---|---|---|---|---|---|
A2 | 7.86 | 60-62 | 700-900 | 500-750 | 8-12 | 12-20 | 25-30 | 11.5-12.5 |
M2 | 8.19 | 65-68 | 800-1200 | 600-1000 | 6-10 | 15-25 | 13-15 | 10.5-11.5 |
M4 | 8.23 | 63-66 | 800-1100 | 600-900 | 8-12 | 16-28 | 13-15 | 11.0-12.0 |
D2 | 7.83 | 60-62 | 600-1200 | 400-900 | 5-10 | 8-18 | 19-24 | 10.5-11.5 |
S7 | 7.83 | 40-50 | 700-1000 | 400-700 | 10-15 | 8-20 | 25-35 | 10.6-11.6 |
H13 | 7.81 | 45-50 | 1500-1900 | 1300-1600 | 5-10 | 20-40 | 25-30 | 10.8-11.8 |
T15 | 8.72 | 65-68 | 1600-2000 | 1300-1600 | 2-5 | 15-25 | 11-13 | 10.4-11.4 |
How to Select MIM Tool Steel
Selecting the appropriate MIM tool steel involves considering various factors to ensure the chosen material meets the specific requirements of your application. Here's a systematic guide to help you select the suitable MIM tool steel:
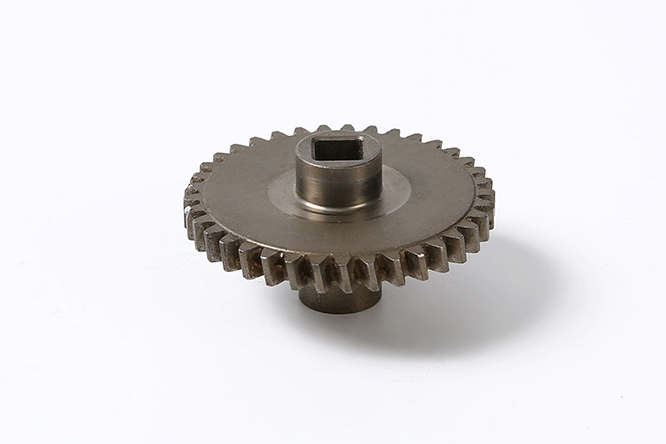
Identify Application Requirements:
Determine the function of the component: Understand whether it needs to withstand wear, impact, high temperatures, or other specific conditions.
Consider load and stress: Analyze the expected mechanical loads and stresses the component will encounter.
Evaluate Mechanical Properties:
Hardness: Choose steel with an appropriate hardness level for the intended application.
Strength: Consider tensile and yield strength requirements based on the load and stress conditions.
Toughness: Evaluate the steel's ability to absorb energy without fracturing, which is crucial for impact resistance.
Consider Wear and Abrasion Resistance:
Assess the type and intensity of wear the component will experience.
Opt for steel with higher wear resistance for friction and abrasive forces applications.
Temperature Resistance:
Determine whether the component will be exposed to elevated temperatures.
Choose steel with suitable heat resistance to prevent deformation or degradation.
Chemical Compatibility:
Evaluate the compatibility of the steel with the environment it will be used in (corrosive, chemically active, etc.).
Dimensional Stability:
Select steel with low thermal expansion and good dimensional stability if tight tolerances are critical.
Tooling and Machinability:
Consider the ease of machining and tooling, especially if post-processing is required.
Neway Tool Steel MIM Parts Manufacturing
Need high-quality custom injection molded parts? Neway should be your go-to source. For 30 years, they've been providing top-notch MIM, CIM, and plastic molding services. I love working with Neway because their engineering team takes the time to know your needs, specifications, and applications. This enables them to craft tailored solutions. No off-the-shelf cookie-cutter parts here! Neway has the expertise to deliver whether you require sturdy steel MIM components, high-temp CIM ceramic parts, or detailed plastic pieces. And if you're a new customer, take advantage of their 20% first-order discount! Give them a shot - I doubt you'll be disappointed.
评论
发表评论