MIM 440C Stainless Steel Metal Injection Molding service
Martensitic 440C stainless steel metal injection molded parts offer exceptional hardness, strength, and corrosion resistance. The high carbon and chromium contents enable excellent wear resistance with the ability to reach hardness levels over HRC 60. However, 440C maintains sufficient toughness and impact strength to avoid brittle behavior. But 440C has a lower ability to withstand dynamic loads.
The fine carbide distribution and refined microstructure from the metal injection molding (MIM) process improve fatigue strength and ductility versus the precision casting process. Post-sintering heat treatment allows ultimate tensile strengths over 2000 MPa to be achieved.
The balanced properties of MIM 440C make it well suited for applications requiring high hardness for wear resistance combined with excellent corrosion performance. Typical uses include:
Plastic injection molds.
High-performance ball bearings.
Valves.
Nozzles exposed to erosion and metal-to-metal wear.
The material is also applied in surgical tools, cutlery, and other applications needing keen, hardened cutting edges.
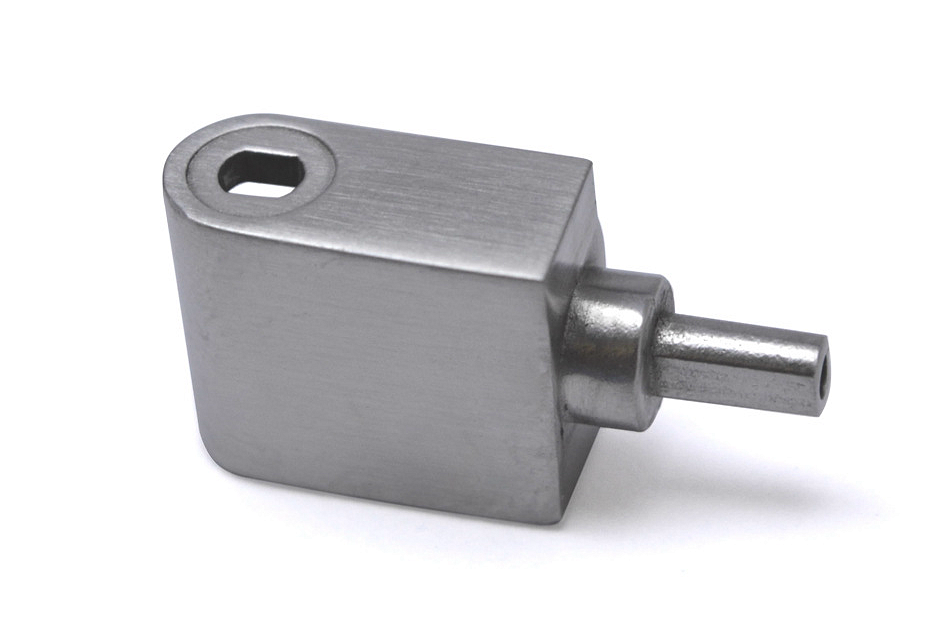
MIM 440C Stainless Steel Typical Properties
Chemical Composition
Carbon (C) | Manganese (Mn) | Phosphorus (P) | Sulfur (S) | Silicon (Si) | Chromium (Cr) | Molybdenum (Mo) | Iron (Fe) | |
---|---|---|---|---|---|---|---|---|
Weight % | 1.05 | 0.75 | 0.03 | 0.03 | 1.0 | 17.0 | 0.75 | Balance |
Physics and Mechanical Properties
Status | Tensile Strength (MPa) | Yield Strength (MPa) | Impact Strength (J) | Hardness (HRC) | Young's Modulus (GPa) | Poisson's Ratio | Elongation (%) | Density (g/cm3) |
---|---|---|---|---|---|---|---|---|
Annealed | 1100 | 850 | 25 | 54 | 200 | 0.27 | 13 | 7.7 |
Key Features And Applications of MIM-440C Parts
Hardness
MIM-440C stainless steel can attain excellent hardness levels through heat treatment and tempering, typically reaching over 60 HRC. The high carbon martensitic structure enables maximum hardness over other stainless grades. Specific hardness levels can be dialed in based on tempering temperature. This outstanding hardness makes MIM-440C ideal for applications requiring wear resistance and long service life.
Typical applications requiring the hardness of 440C stainless MIM include cutting tools, bearings, molds, valves, and medical instruments.
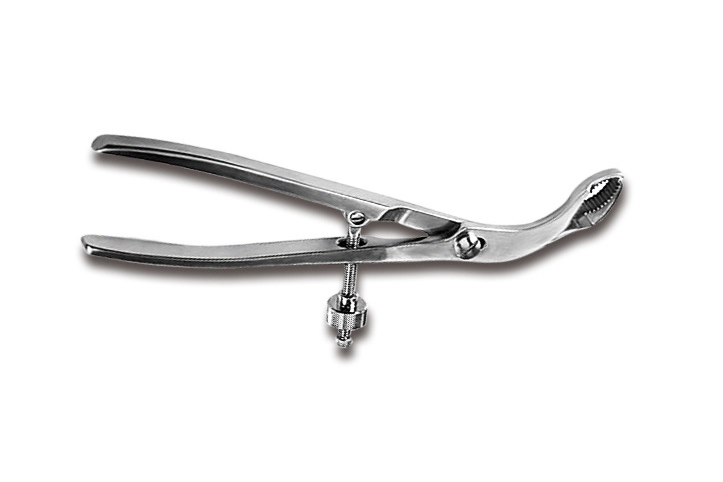
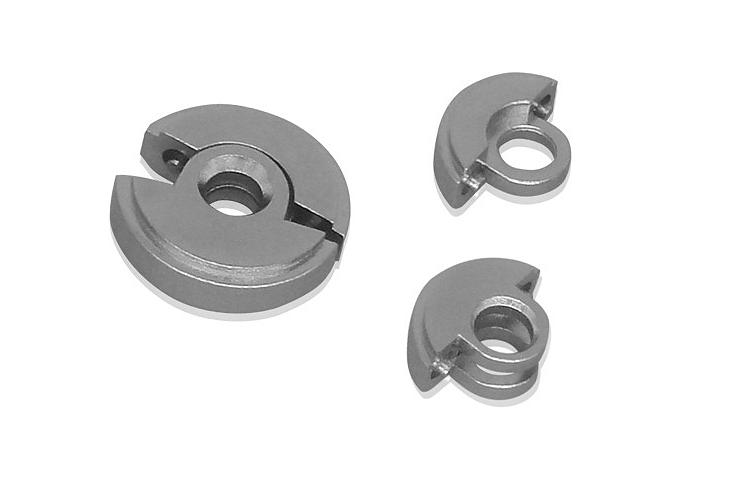
Strength
In the hardened and tempered condition, MIM-440C stainless steel achieves very high strength levels, with tensile strength exceeding 2000 MPa. The high carbon martensitic structure substantially increases strength over other stainless grades. Heat treatment enhances strength through the precipitation of fine carbides. The high strength gives MIM-440C excellent load-bearing capabilities and resistance to failure.
The high strength makes MIM-440C parts well-suited for highly stressed components like lock cores, bearings, powder tool parts, nozzles, surgical instruments, and other highly loaded components needing hardness and durability.
Corrosion-Resistance
MIM-440C stainless steel provides moderate corrosion resistance owing to its 16-18% chromium content. It performs well against atmospheric corrosion and many mild chemical environments. The corrosion resistance is generally less than 300 series austenitic grades but comparable to martensitic 416 and 420 stainless types. However, care must be taken in applications with significant chloride exposure, which can lead to pitting and crevice corrosion.
Proper passivation is recommended to enhance the formation of a protective passive layer on surfaces. Overall, the corrosion resistance of MIM-440C is sufficient for use in applications where limited chemical resistance is needed in combination with high hardness and strength.
The balance of corrosion resistance and mechanical properties makes 440C stainless MIM suitable for injection molds, bearings, valves, medical instruments, and other components needing moderate chemical resistance.
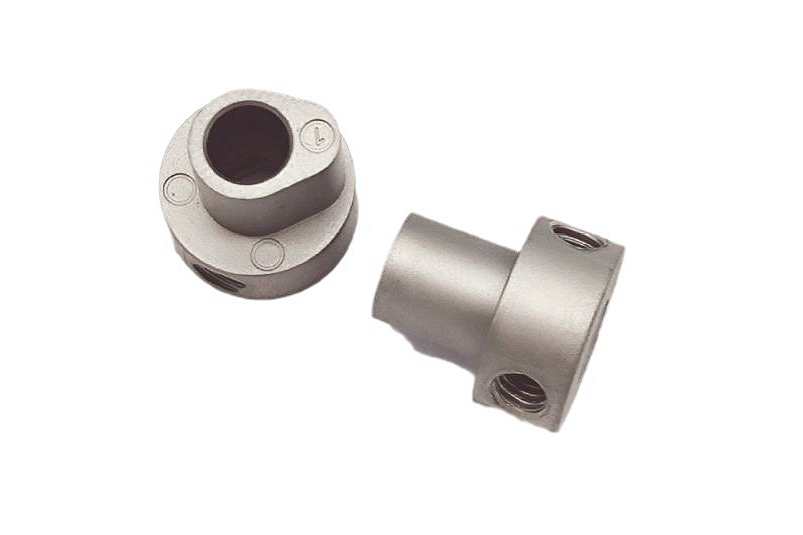
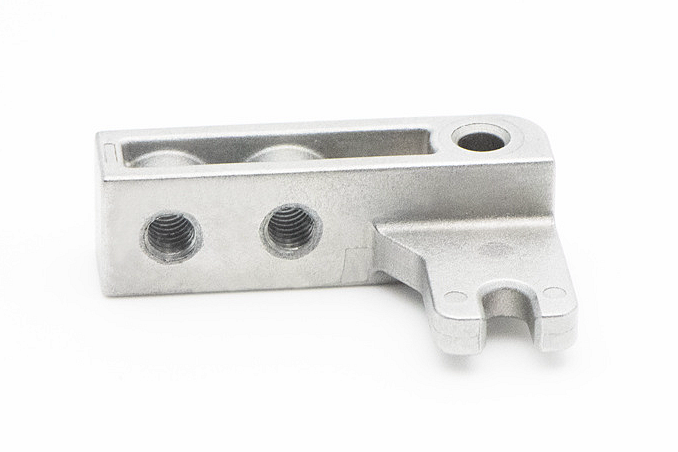
Toughness
Despite its high hardness, MIM-440C maintains sufficient toughness and impact strength to avoid brittle behavior in service. MIM's refined carbide size and distribution increase fracture resistance compared to conventionally processed 440C. Tempering treatment also enhances the toughness. Depending on the condition, typical harpy V-notch impact values range from 25-40 J,
While lower than austenitic grades, the toughness is adequate for most applications involving high stresses and dynamic loading conditions. The balance of hardness and toughness makes MIM-440C suitable for plastic injection molds, bearings, valves, surgical instruments, knives, and other components where resistance to impact damage is needed.
The combination of hardness and sufficient toughness makes 440C stainless MIM suitable for injection molds, bearing parts, valves, power tool parts, and components needing impact resistance.
Dimensional Stability
MIM-440C stainless steel exhibits excellent dimensional stability during heat treatment and tempering processes compared to other high-carbon martensitic grades. Distortion, warpage, and shape changes are minimized. It is attributed to the fine dispersion of carbides and lower residual stress levels from the MIM process.
Dimensional variations are typically held to under 0.5% during hardening and tempering. vThis makes MIM-440C suitable for precision components that cannot tolerate shape changes after sintering. Applications dimensions and geometry must be tightly controlled, benefiting from this ability.
Dimensional stability makes 440C stainless MIM advantageous for high-precision molds, gear racks, measuring tools, instrument accessories, and components needing shape retention.
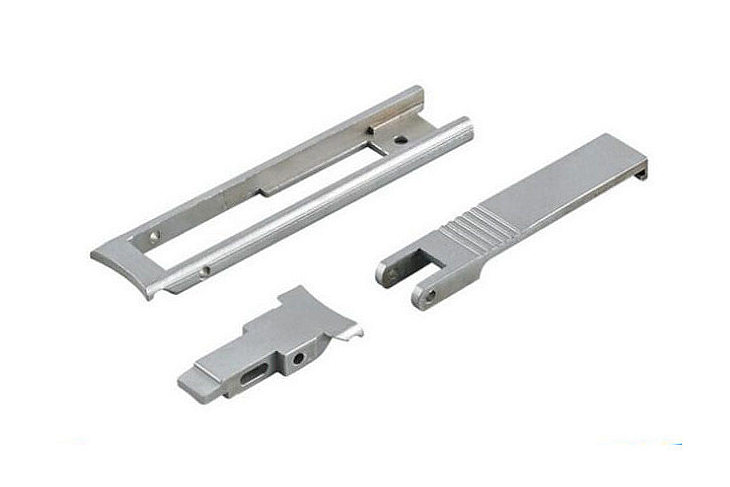
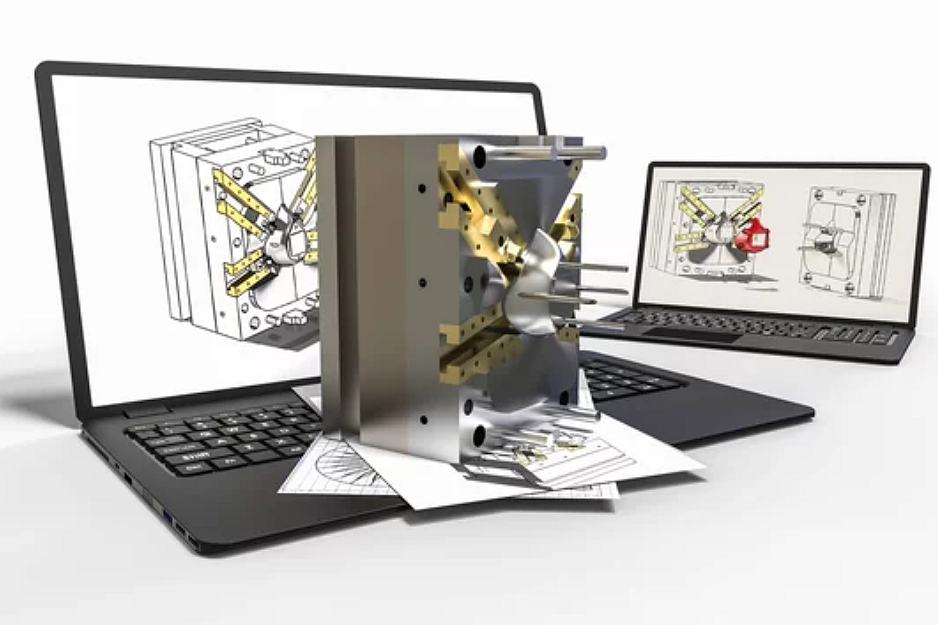
Consultative Design Services
Neway Custom Metal Injection Molding Service provides free Consultative Design Services throughout the process. This includes all processes from your design stage to mass-produced finished products.
1. Material selection Consult
2. Structural design service
3. Mold design service
Contact us now if you are interested.
What We Can Offer?
We offer free material selection and consultative design services from beginning to end. No MOQs, Rapid prototyping, and mass production are our strengths.
"When I needed precision parts with exceptional strength, I turned to Neway's 440C Metal Injection Molding service. The results exceeded my expectations – the parts showcased remarkable wear and corrosion resistance. The team's expertise and dedication truly stood out. Neway's 20% discount for new customers improved the experience!" --- WHS Sondermetalle
When U. Eitner switched to Neway's 440C MIM for their plastic injection molds, tool life tripled compared to machined steel. The exceptional hardness provided durability over 20,000 cycles. According to Acme's engineering manager: "Neway's precision 440C MIM mold inserts performed better than expected. We'll never go back." --- U. Eitner CEO
评论
发表评论