MIM 4065 Low Alloy Steel Metal Injection Molding service
Metal injection molding of martensitic 4605 low alloy steel delivers an exceptional combination of high strength, hardness, and corrosion resistance. The alloy contains 17% chromium for good general corrosion performance and molybdenum for enhanced pitting and crevice resistance. Significant carbon and nitrogen additions enable 4605 MIM parts to achieve hardness levels exceeding HRC 60.
The fine, uniform carbide distribution imparted by MIM also provides a refinement in flexibility over conventional 4605 grades. Excellent dimensional stability is maintained during heat treatment. These balanced properties make MIM 4605 suitable for various demanding applications.
With its hardness, strength, corrosion resistance, and excellent manufacturing characteristics, MIM 4605 presents an advanced low alloy steel solution for critical components across industries, including aerospace hydraulic components, measure tool parts, power tool parts, and medical instruments.
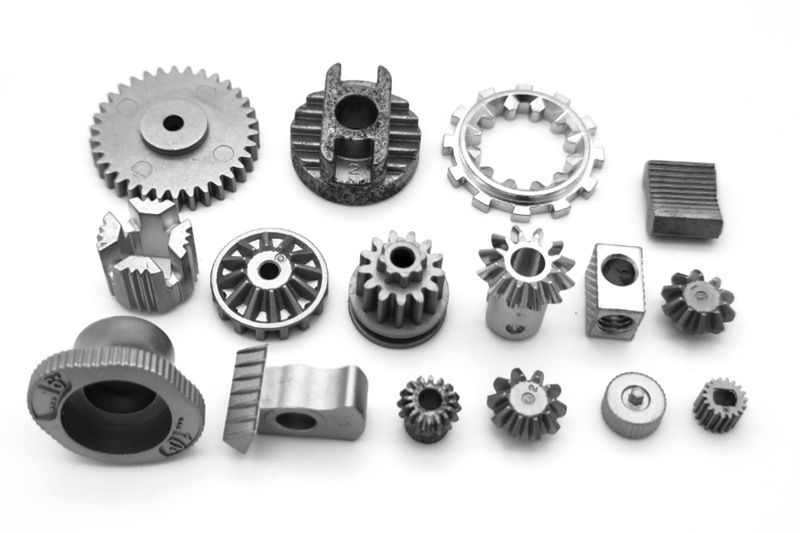
MIM 4065 Low Alloy Steel Typical Properties
Download PDF: MIM-4065 Low Alloy Steel Datasheet |
---|
Chemical Composition
Element | Carbon (C) | Silicon (Si) | Manganese (Mn) | Phosphorus (P) | Sulfur (S) | Chromium (Cr) | Nickel (Ni) | Molybdenum (Mo) | Iron (Fe) |
---|---|---|---|---|---|---|---|---|---|
Weight Percentage | 0.02 | 0.20 | 0.80 | 0.015 | 0.01 | 16.5 | 4.5 | 2.0 | Balance |
Physics and Mechanical Properties
Property | Status | Tensile Strength (MPa) | Yield Strength (MPa) | Impact Strength (J) | Hardness (HRC) | Young's Modulus (GPa) | Poisson's Ratio | Elongation (%) | Density (g/cm³) |
---|---|---|---|---|---|---|---|---|---|
Value | Annealed | 800 | 700 | 40 | 45 | 180 | 0.28 | 10 | 7.7 |
Key Features And Applications of MIM-4065 Parts
Hardness
MIM-4605 low alloy steel can attain excellent hardness levels through heat treatment, typically reaching over 60 HRC. The high carbon and nitrogen contents enable the formation of rigid martensitic microstructures. Specific hardness levels can be tailored based on tempering temperature after solution annealing and quenching.
This outstanding hardness provides maximum resistance to wear, abrasion, erosion, and indentation while maintaining good fracture toughness. Applications benefiting from the hardness of MIM-4605 include aerospace hydraulic valves and fittings, plastic injection molds, power tool components, valves, and medical instruments where hardness is critical.
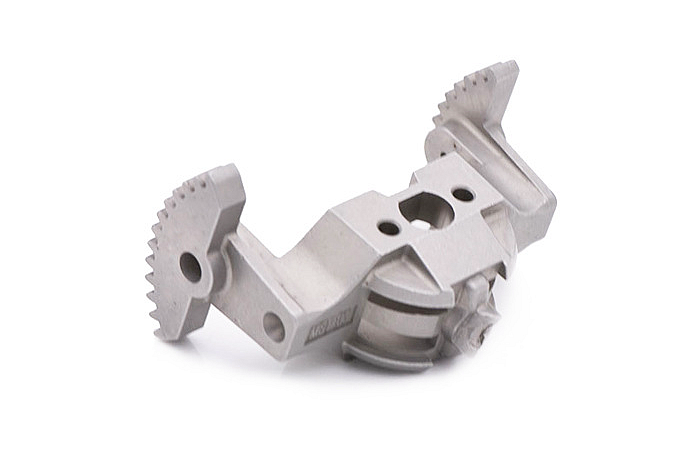
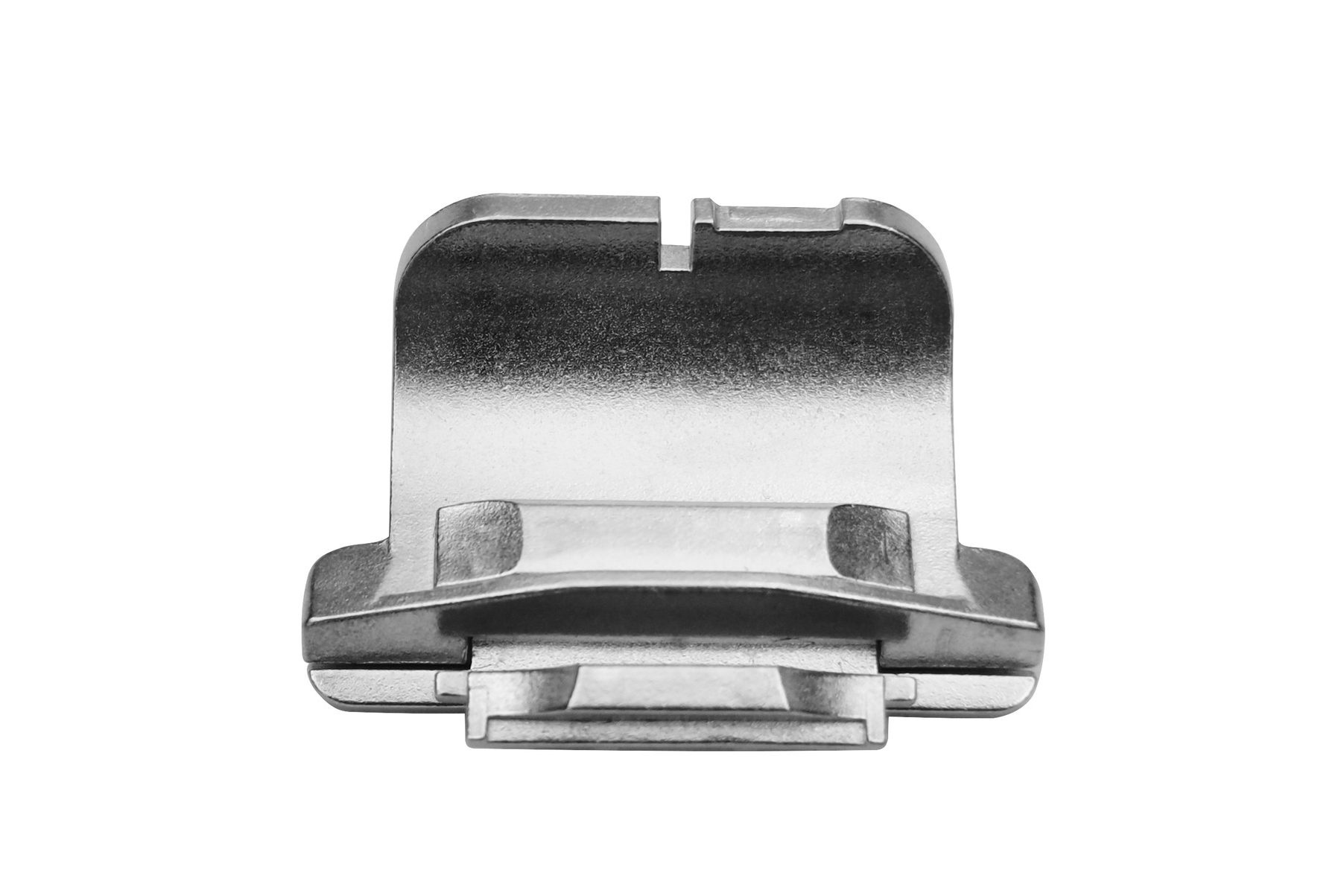
Strength
MIM-4065 low alloy steel offers impressive strength properties, making it suitable for demanding applications. With a tensile strength of around 900 MPa and a yield strength of approximately 800 MPa, MIM-4065 exhibits robust mechanical performance. This high strength is attributed to its martensitic structure and the addition of alloying elements. The combination of exceptional strength and good ductility allows MIM-4065 parts to withstand heavy loads and dynamic stresses without succumbing to deformation or failure.
MIM-4065 low alloy steel finds utility in various applications where strength is a critical requirement. Industries such as automotive, aerospace, and industrial machinery benefit from its high tensile and yield strengths. Components subjected to substantial loads, such as structural parts, fasteners, and gears, rely on MIM-4065's strength to ensure optimal performance under demanding conditions. Moreover, surgical instruments and medical implants, where strength and biocompatibility are essential, also benefit from MIM-4065's mechanical properties.
Corrosion-Resistant
The approximately 16-18% chromium and 2-3% molybdenum content of MIM-4605 imparts good overall corrosion resistance. It performs well in atmospheric and chemical processes environments and against pitting and crevice corrosion attacks. However, MIM-4605 has lower corrosion resistance than austenitic low alloy steel grades. Its corrosion resistance is at the same level as MIM 430. Proper passivation enhances the protective surface film.
MIM-4605 provides sufficient corrosion performance for aerospace, medical, nuclear, chemical processing applications, and other industries where moderate chemical resistance and high hardness and strength are needed. It withstands the operating conditions seen by components like hydraulic valves and fittings, surgical instruments, pumps, and reactors.
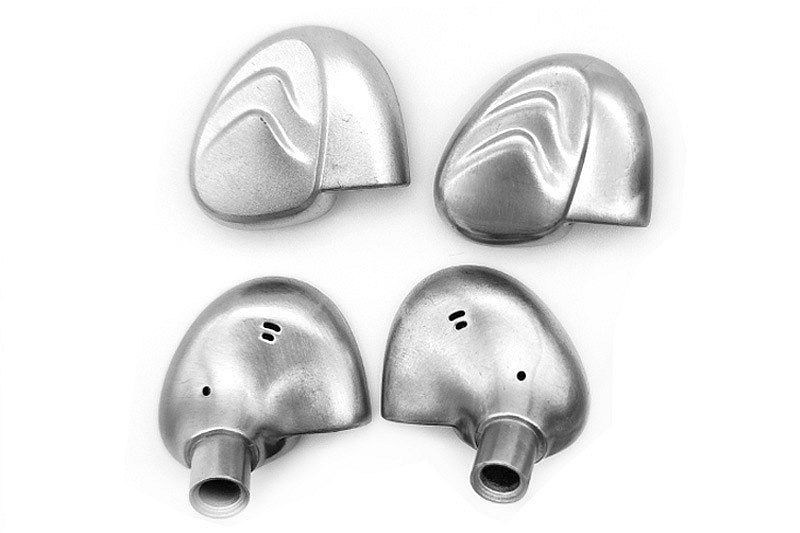
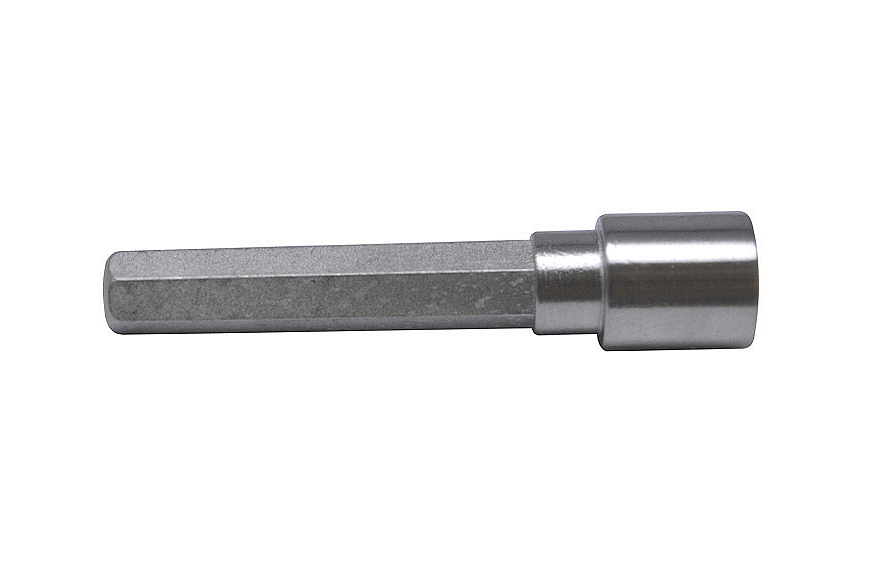
Toughness
MIM-4065 low alloy steel exhibits remarkable toughness, ensuring its suitability for applications requiring resistance to impact and sudden loading. Despite its high strength, MIM-4065 maintains good toughness due to its controlled microstructure and alloy composition. The material's ability to absorb energy without fracturing makes it ideal for components subjected to dynamic forces. This toughness prevents catastrophic failures, enhancing the safety and reliability of MIM-4065 low alloy steel products.
Automotive and aerospace industries utilize this material for brackets, connectors, and safety components, where toughness ensures resistance to collisions and vibrations. Tooling and industrial machinery also benefit from MIM-4065's toughness, as it maintains integrity under operational shocks. Furthermore, medical devices, such as surgical instruments, rely on the material's toughness to withstand handling and potential impact during procedures.
Dimensional Stability
MIM-4065 low alloy steel boasts exceptional dimensional stability, making it a prime choice for applications demanding precise and consistent dimensions. MIM-4065 maintains its form and size during the metal injection molding, minimizing distortion, warping, and shape alterations. This stability arises from its controlled microstructure and minimal residual stress levels, ensuring that components retain accuracy and functionality post-sintering.
In fields where tight tolerances and exact dimensions are paramount, MIM-4065 low alloy steel excels. Electronics industries use this trait for connectors and housings to ensure consistent, reliable connections. Precision tools, like measuring instruments and gauges, benefit from MIM-4065's stability, maintaining precision during use. Automotive and aerospace sectors employ the material for engine and transmission components, guaranteeing seamless fit and peak performance.
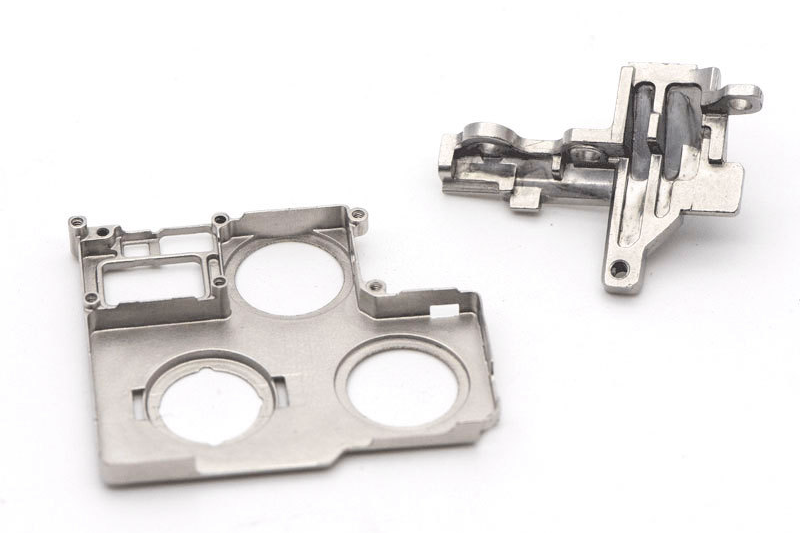
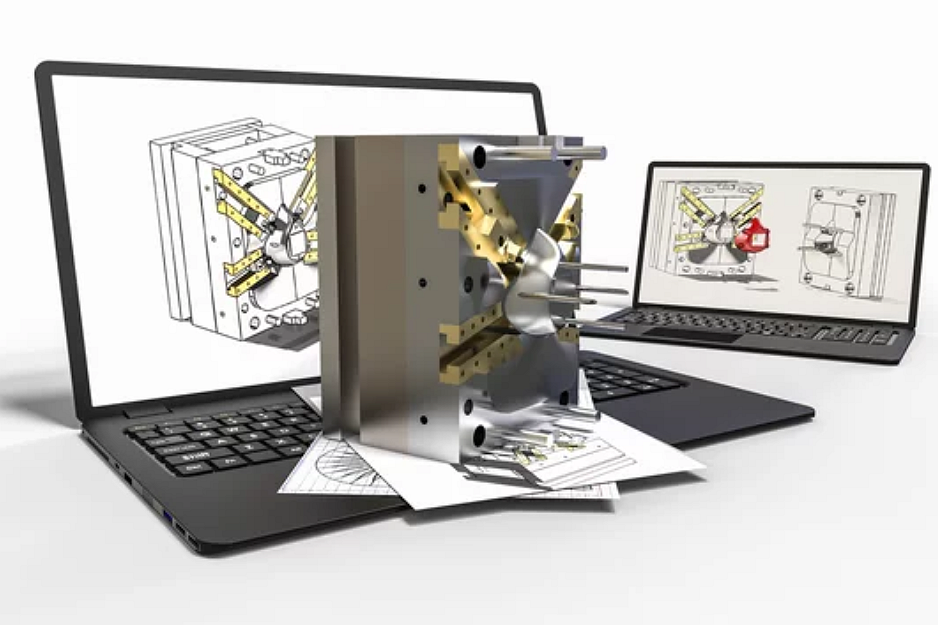
Consultative Design Services
Neway Custom Metal Injection Molding Service provides free Consultative Design Services throughout the process. This includes all processes from your design stage to mass-produced finished products.
1. Material selection Consult
2. Structural design service
3. Mold design service
Contact us now if you are interested.
What We Can Offer?
We offer free material selection and consultative design services from beginning to end. No MOQs, Rapid prototyping, and mass production are our strengths.
评论
发表评论