Cobalt Alloy Metal Injection Molding
Cobalt alloy MIM facilitates the economical production of intricate components with exceptional biocompatibility, wear resistance, and high-temperature strength. Grades like CoCrMo, CoCrW, and MP35N offer superb corrosion protection and bio-functionality for demanding medical device applications.
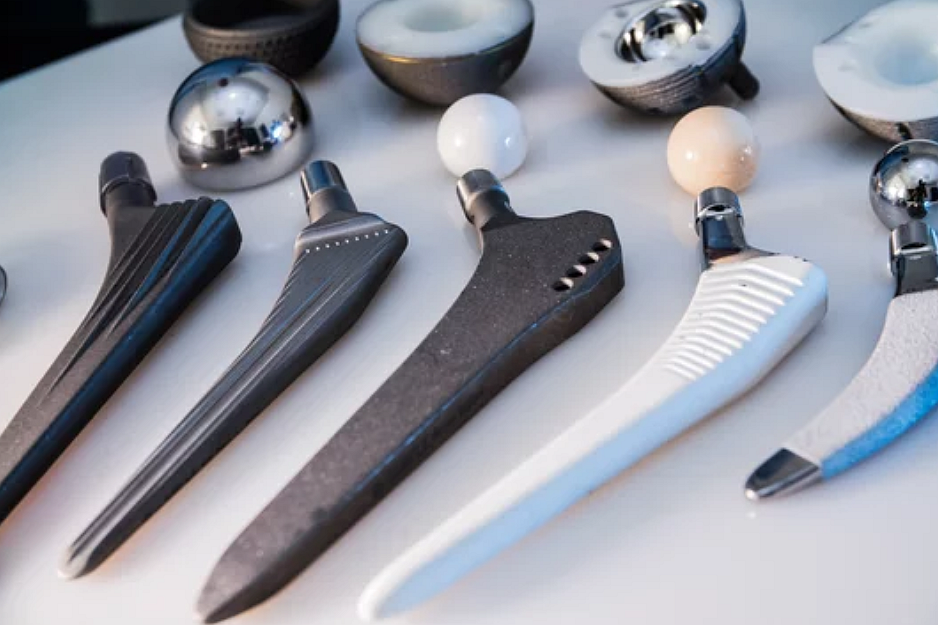
CoNiCrMo enhances strength and corrosion resistance versus CoCr alloys. Haynes 25 provides tremendous high-temperature capabilities up to 1200°C. Stellite 6 delivers outstanding wear performance in high-friction applications. Cobalt alloy metal injection molding provides tailored solutions for biomedical, aerospace, petrochemical, and industrial components needing specialized properties.
Cobalt Alloys Optional for MIM Parts
CoCrMo (ASTM F75) - Cobalt-chromium-molybdenum alloy is often used for orthopedic implants due to its biocompatibility and corrosion resistance. The typical composition is 61% Co, 28% Cr, and 6% Mo. Normally used in medical device components.
CoCrW - Cobalt-chromium-tungsten alloy with excellent high-temperature strength, wear resistance, and biocompatibility. Typical composition is 60% Co, 28% Cr, and 10% W. Used for dental implants and articulating joints.
CoNiCrMo - Nickel is added to cobalt-chromium-molybdenum alloys to increase corrosion resistance further while retaining strength. The composition can be 35% Co, 35% Ni, 20% Cr, and 10% Mo. Used in orthopedics.
MP35N - Multiphase cobalt-nickel-chromium-molybdenum alloy with high strength and outstanding corrosion resistance. Composition is 35% Co, 35% Ni, 20% Cr, 10% Mo. Used for implantable medical devices.
Haynes 25 - Cobalt-nickel-chromium-tungsten alloy with excellent high-temperature strength up to 1200°C. Composition is 55% Co, 20% Cr, 10% Ni, 15% W. Used in aerospace applications.
Stellite 6 - Cobalt-chromium alloy with reasonable wear and corrosion resistance. Composition is 60% Co, 28% Cr with W, Si, and Fe additions. Used for MIM components requiring high wear performance.
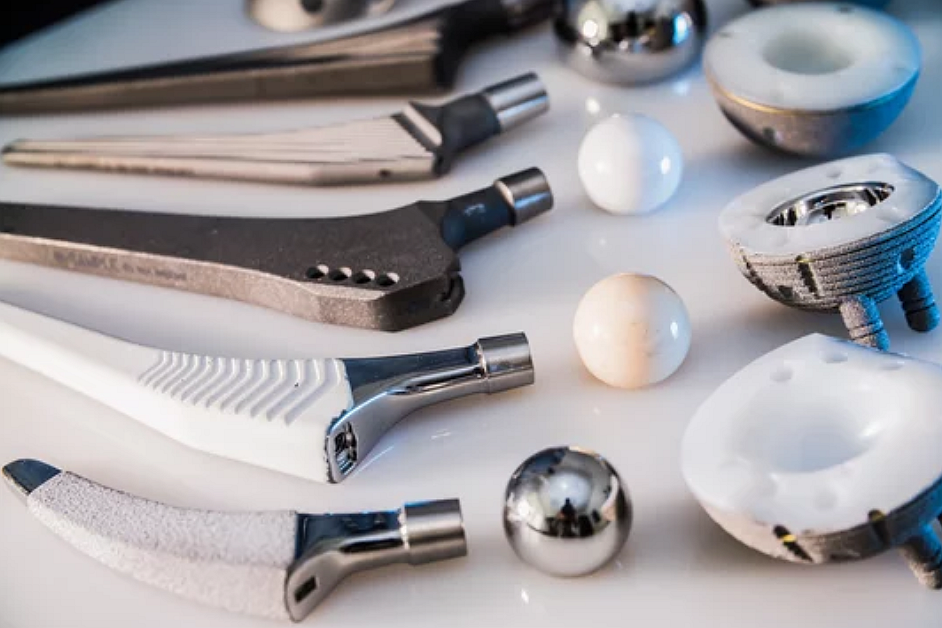
Cobalt Alloy | Key Features | Applications |
---|---|---|
MIM-CoCrMo (ASTM F75) | Biocompatible, excellent wear and corrosion resistance | Medical implants, orthopedic devices |
MIM-CoCrW | High-temperature strength, oxidation resistance | Aerospace components, gas turbine blades |
MIM-CoNiCrMo | High-temperature stability, corrosion resistance | Oil and gas equipment, chemical processing |
MIM-MP35N | Exceptional strength and toughness, biocompatibility | Medical and dental instruments, springs |
MIM-Haynes 25 | High-temperature strength, oxidation resistance | Aerospace components, heat exchangers |
MIM-Stellite 6 | Wear resistance, high-temperature stability | Cutting tools, valves, industrial equipment |
MIM-Cobalt Alloys Comparison
Carefully evaluating and comparing the properties of different MIM cobalt alloys enables identifying the optimal grade for your specific application requirements. By analyzing alloys like CoCrMo, CoCrW, CoNiCrMo, MP35N, Haynes 25, and Stellite 6 across factors including biocompatibility, wear resistance, corrosion protection, high-temperature strength, and machinability, you can match the alloy capabilities to your component needs.
Selecting a cobalt MIM alloy optimized for the intended operating conditions ensures your parts exhibit the targeted functionality, performance, and longevity. The correct cobalt alloy grade also provides design flexibility and cost-effective manufacturing. With in-depth alloy knowledge, you can confidently select a MIM cobalt material that aligns with your application, manufacturability, and budgetary goals.
MIM-Cobalt Alloys Chemical Composition
Alloy | Cobalt (Co) | Chromium (Cr) | Molybdenum (Mo) | Tungsten (W) | Nickel (Ni) | Iron (Fe) | Silicon (Si) | Manganese (Mn) | Carbon (C) |
---|---|---|---|---|---|---|---|---|---|
MIM-CoCrMo (ASTM F75) | 61% | 28% | 6% | - | - | 3% max | 1% max | 1% max | 0.35% max |
MIM-CoCrW | 60% | 28% | - | 10% | - | 1% max | 1% max | - | 0.25% max |
MIM-CoNiCrMo | 35% | 20% | 10% | - | 35% | - | - | - | - |
MIM-MP35N | 35% | 20% | 10% | - | 35% | - | - | - | - |
MIM-Haynes 25 | 55% | 20% | - | 15% | 10% | - | - | - | 0.1% max |
MIM-Stellite 6 | 60% | 28% | - | - | - | 3% max | 1% max | 1% max | 0.25% max |
MIM-Cobalt Alloys Physical and Mechanical
Alloy | Status | Tensile Strength (MPa) | Yield Strength (MPa) | Impact Strength (J) | Hardness (HRC) | Young's Modulus (GPa) | Poisson's Ratio | Elongation (%) | Density (g/cm3) |
---|---|---|---|---|---|---|---|---|---|
MIM-CoCrMo (ASTM F75) | Sintered | 1260 | 1110 | 16 | 43 | 230 | 0.29 | 8 | 8.3 |
MIM-CoCrW | Sintered | 1340 | 1210 | 18 | 44 | 243 | 0.30 | 7 | 8.4 |
MIM-CoNiCrMo | Sintered | 1290 | 1200 | 15 | 48 | 260 | 0.31 | 5 | 8.44 |
MIM-MP35N | Sintered | 1310 | 1220 | 14 | 47 | 248 | 0.33 | 6 | 8.46 |
MIM-Haynes 25 | Sintered | 1150 | 1050 | 12 | 45 | 218 | 0.29 | 10 | 8.9 |
MIM-Stellite 6 | Sintered | 980 | 840 | 10 | 39 | 205 | 0.30 | 7 | 8.2 |
Key Features and Applications of Cobalt Alloys MIM Parts
MIM-CoCrMo (ASTM F75):
Key Features: Biocompatible, excellent wear and corrosion resistance, high strength.
Application Examples: Medical implants (hips, knees), dental prosthetics, orthopedic devices.
Reasons to Choose: ASTM F75's biocompatibility and resistance to wear and corrosion make it an excellent choice for medical and orthopedic applications.
MIM-CoCrW:
Key Features: High-temperature strength, oxidation resistance, excellent mechanical properties.
Application Examples: Aerospace components, gas turbine blades, heat exchangers.
Reasons to Choose: CoCrW's exceptional high-temperature properties and mechanical strength are essential for demanding aerospace and heat-exchanging applications.
MIM-CoNiCrMo:
Key Features: High-temperature stability, corrosion resistance, excellent mechanical properties.
Application Examples: Oil and gas equipment, chemical processing, turbine components.
Reasons to Choose: CoNiCrMo's corrosion resistance and high-temperature stability make it invaluable in corrosive and high-temperature industrial environments.
MIM-MP35N:
Key Features: Exceptional strength and toughness, biocompatibility, excellent corrosion resistance.
Application Examples: Medical and dental instruments, springs, structural components.
Reasons to Choose: MP35N's combination of strength, biocompatibility, and corrosion resistance is ideal for medical devices and critical structural components.
MIM-Haynes 25:
Key Features: High-temperature strength, oxidation resistance, excellent creep resistance.
Application Examples: Aerospace components, heat exchangers, industrial furnaces.
Reasons to Choose: Haynes 25 excels in high-temperature applications, making it a preferred choice for aerospace and industrial furnaces.
MIM-Stellite 6:
Key Features: Wear resistance, high-temperature stability, exceptional hardness.
Application Examples: Cutting tools, valves, pumps, industrial components.
Reasons to Choose: Stellite 6's remarkable wear resistance and hardness make it indispensable for high-temperature and abrasive applications.
How to Select Cobalt Alloys for Your MIM Parts
Define Part Requirements:
Clearly outline the essential properties your MIM part needs, such as mechanical strength, corrosion resistance, wear resistance, and high-temperature stability.
Clearly defining your part's requirements helps set clear expectations and criteria for the desired alloy. It enables you to narrow down your options efficiently.
Understand Cobalt Alloys:
Familiarize yourself with the properties and compositions of available Cobalt Alloys, including MIM-CoCrMo (ASTM F75), MIM-CoCrW, MIM-CoNiCrMo, MIM-MP35N, MIM-Haynes 25, and MIM-Stellite 6.
Knowledge of different Cobalt Alloys empowers you to make informed decisions and choose the alloy that aligns with your part's intended application.
Match Properties to Needs:
Compare the properties of each alloy to the requirements of your part. Choose an alloy that aligns with the desired characteristics, such as wear resistance for cutting tools or biocompatibility for medical instruments.
This step ensures that the chosen alloy's properties align with your part's functional requirements. It prevents over-engineering or underperformance.
Consider Application Factors:
Evaluate the specific conditions your MIM part will encounter, such as temperature variations, corrosive environments, or mechanical stress. Choose an alloy that can perform well under these conditions.
Industry Standards and Regulations:
Ensure that the selected Cobalt Alloy meets industry standards and regulations relevant to your application, especially in medical devices or aerospace industries.
Cobalt Alloys may behave differently under various conditions. Considering application factors helps you avoid premature failure or degradation.
Consult Experts:
Seek advice from experts in materials engineering or production. Engage with manufacturers like Neway, who specialize in Cobalt Alloy MIM parts. Their expertise can provide valuable insights.
Prototype and Testing:
Conduct prototyping and testing with the chosen alloy to validate its performance in real-world conditions. This step helps identify any potential challenges and allows for adjustments.
Testing ensures that the alloy performs as expected and helps you identify any unforeseen challenges that could arise during production.
Cost Analysis:
Evaluate the cost of the chosen alloy, including material expenses and processing costs. Balance the benefits the alloy offers with its overall cost.
Cost-effectiveness is essential for maintaining competitiveness, especially when considering production at scale.
Long-Term Availability:
Ensure the selected Cobalt Alloy will remain available for your product's lifespan. Avoid alloys that might face supply chain challenges in the future.
Ensuring the long-term availability of the chosen alloy safeguards your production from potential disruptions caused by supply chain issues.
Why Use Us In Cobalt Alloy MIM?
As a loyal customer for over a decade, I highly recommend Neway for all your cobalt alloy MIM needs. Their expertise in precision molding and advanced cobalt alloys resulted in innovative solutions for my medical devices. Neway's engineers optimized my product designs for manufacturability and performance. They deliver high-quality components on schedule and budget. Take advantage of their new customer discount and experience their exceptional capabilities!
When MedTech Inc. launched a new orthopedic implant, they chose Neway for design and cobalt alloy MIM manufacturing. Neway optimized the component geometry for precision molding and sintering performance. Their CoCrMo prototypes passed all functional validations, allowing rapid progression to production. MedTech now works exclusively with Neway for all its cobalt MIM needs, benefiting from high quality and responsiveness.
Searching for a trusted partner for cobalt alloy MIM parts? Look no further than Neway! Their three decades of perfecting multi-process molding is invaluable. I suggest giving Neway a try to experience their exceptional service and capabilities first-hand. And enjoy 20% off your initial order! Why not start a conversation about your project with their engineers today?
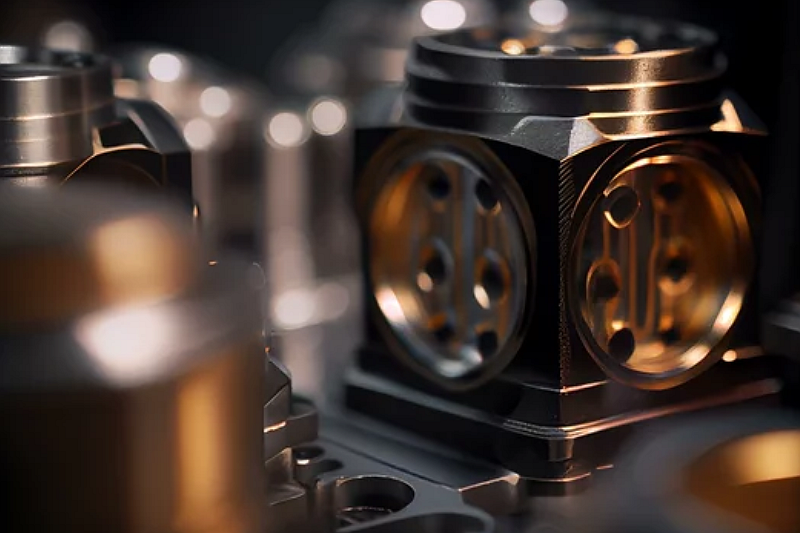
评论
发表评论