In the fast-evolving world of manufacturing, prototyping plays a pivotal role in ensuring the successful development of new products. Two prominent methods that have gained immense popularity are CNC machining prototyping and 3D printing prototyping. These techniques are at the forefront of innovation, enabling production engineers like those at Neway to create functional prototypes with precision and efficiency. This article delves into the intricacies of CNC machining and 3D printing prototyping, highlighting their respective strengths and applications and how Neway's expertise positions them as leaders in the field.
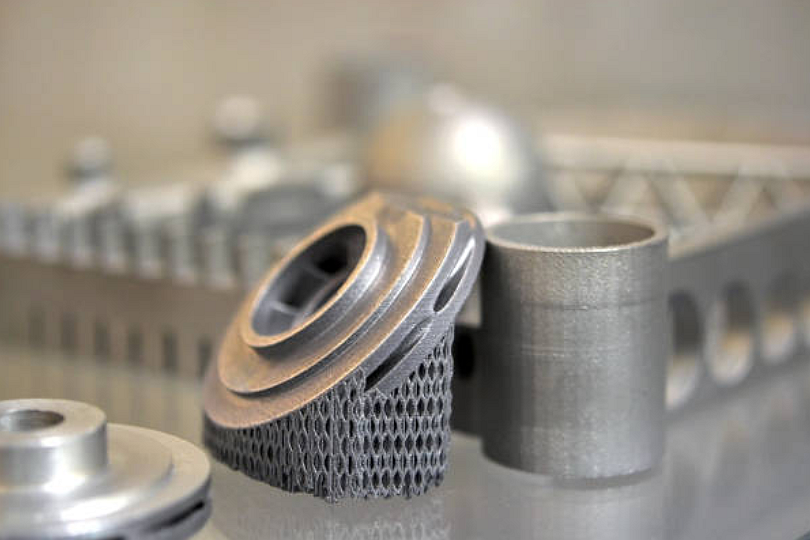
Precision and Accuracy
CNC machining can readily hold tolerances of ±0.005" or tighter, enabling highly accurate functional prototypes. 3D printing has lower precision, typically ±0.030" or more deviation. Precision depends on the 3D printing process used.
Surface Finish
CNC machined parts can achieve fine surface finishes of RA 10-25 microinches or better. The layered nature of 3D printing results in visible layer steps on surfaces, requiring secondary finishing. However, some processes like SLA can deliver smooth surface quality.
Production Materials
CNC machining uses the same industrial materials as final production components, including metals, plastics, composites, alloys, etc. 3D printing uses proprietary materials with limited strength and thermal properties.
Part Strength and Durability
CNC machined prototypes match the mechanical properties of the final production materials, allowing functional testing under real-world conditions. 3D printed parts are weaker and have lower heat tolerance, limiting test applications.
Complex Geometries
CNC machining handles complex 3D contours, shapes, internal features, and intricate details well. Many complex geometries can only be 3D printed with support structures that require removal later.
Part Size Capabilities
CNC machining can fabricate massive prototypes without size limitations. Maximum part size is limited for most 3D printers, often under one cubic foot build volume.
Design Iteration Speed
Both technologies allow fast design iterations, with 3D printing having the edge for speedy prints of concepts. CNC machining requires CAM programming but enables functional metal prototypes.
Production Volumes
CNC machining is ideal for hundreds or thousands of prototypes and low-moderate production volumes. It needs economy of scale for mass production runs. 3D printing is strictly a low-volume process.
Post-Processing Requirements
Minimal post-processing is needed for CNC machined parts compared to 3D printed prototypes. Printed parts often require support removal, sanding, and smoothing before use.
Assembly Requirements
3D-printed prototypes usually need to be joined together with adhesives or fasteners. CNC machined parts can be consolidated into single components, minimizing assembly.
Cost Factors
CNC machining has higher upfront costs but lower per-part costs at volume. 3D printing has low startup costs but very high per-part costs at volume due to the additive process.
Design Guidelines
CNC machining requires design adaptations like avoiding thin walls and minor features. 3D printing design for additive manufacturing guidelines must also be followed.
Appearance
CNC machined parts have an industrial "machined" look though polishing can enhance cosmetics. 3D printed parts have a distinctive layered stepped appearance.
Lead Times
Standard lead times for CNC machined prototypes range from days to weeks. 3D printing offers speedy turnaround times, from hours to 1-2 days.
Production Readiness
CNC machined prototypes can serve as pre-production components with fidelity close to the final parts. 3D-printed prototypes are generally not production-representative.
Industry Use
CNC machining is widely used across industrial sectors. Aerospace, automotive, and medical rely heavily on 3D printing for prototypes due to limited runs.
Design Flexibility
Both methods enable significant design flexibility. CNC machining makes changes fast by editing CAD files. 3D printing requires re-printing modified design files.
Part Consolidation
Consolidating assemblies into single parts is far easier with CNC machining versus 3D printing processes. Multi-material printing helps improve consolidation.
CNC machining surpasses 3D printing for high-precision functional prototypes in production-grade materials. But 3D printing enables high-speed concept iterations earlier in design processes. The two technologies are complementary based on the prototyping stage, quality, and quantity requirements.
评论
发表评论