Alumina-Zirconia Ceramic Injection Molding (CIM) service
Alumina-Zirconia Ceramic Injection Molding (CIM) service is a cutting-edge manufacturing process that harnesses the exceptional properties of alumina-zirconia ceramic for diverse applications. Through the CIM process, powdered alumina is mixed with binders and injected into precision molds, where it undergoes controlled heating and sintering, resulting in intricate, high-precision CIM components.
CIM Alumina-Zirconia combines the strengths of both alumina and zirconia ceramics. This hybrid material exhibits enhanced toughness and wear resistance, making it suitable for applications requiring exceptional durability in challenging environments. The key features of CIM Alumina-Zirconia include its ability to withstand high mechanical stresses, resist wear and abrasion, and maintain its integrity under extreme temperatures. Primary applications of CIM Alumina-Zirconia span across diverse industries. It finds use in joint replacements and orthopedic implants in the medical field, benefiting from its mechanical strength and biocompatibility. Additionally, in industrial settings, CIM Alumina-Zirconia excels as wear-resistant components, such as pump parts, valves, and cutting tools, due to its ability to withstand harsh conditions and maintain precision even under heavy usage.
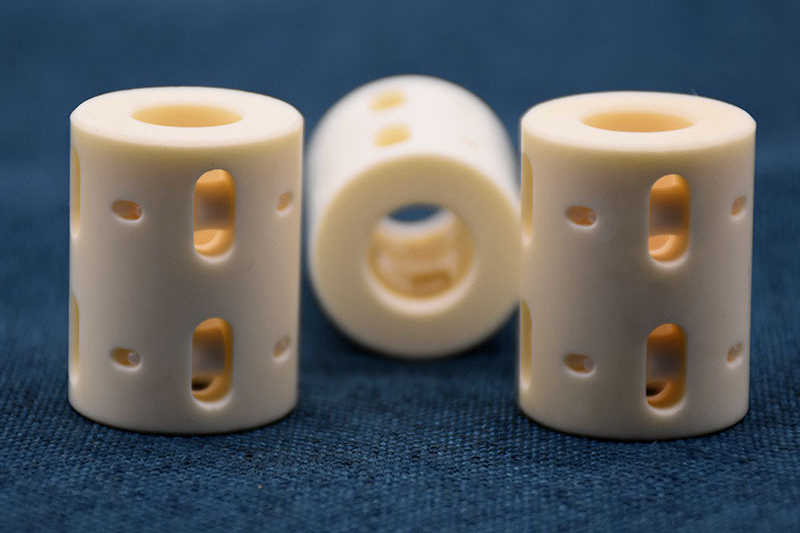
CIM Alumina-Zirconia Typical Properties
Download PDF: CIM-Alumina-Zirconia Datasheet |
---|
Physics and Mechanical Properties
Properties | Fracture Toughness (MPa√m) | Flexural Strength (MPa) | Impact Strength (J/m) | Hardness (HRA) | Young's Modulus (GPa) | Elastic Modulus (GPa) | Thermal Expansion (10^-6/°C) | Compressive Strength (MPa) | Density (g/cm³) |
---|---|---|---|---|---|---|---|---|---|
CIM Alumina-Zirconia | 8.5 | 500 | 5.0 | 82 | 250 | 280 | 9.0 | 1800 | 4.2 |
Features and Applications of CIM Alumina-Zirconia Parts
Fracture Toughness
The Fracture Toughness of CIM-Alumina-Zirconia parts is a remarkable 8.5 MPa√m. This value reflects their exceptional resistance to crack propagation and fractures, making them ideal for applications subjected to mechanical stresses and impacts. The combination of alumina and zirconia in the material composition contributes to this high fracture toughness, providing the parts with the ability to withstand and dissipate energy from sudden forces or impacts. The microstructure of CIM-Alumina-Zirconia also plays a role, with a well-controlled microstructure enhancing fracture resistance.
In the aerospace industry, components like turbine blades and structural elements require materials that can withstand the rigors of flight, including vibrations, rapid temperature changes, and potential impacts. Similarly, the automotive sector relies on these properties for engine components and safety systems, such as airbag deployment mechanisms. CIM-Alumina-Zirconia parts also find use in medical implants and prosthetics, where the ability to endure impacts and mechanical stresses ensures the longevity and reliability of the implants.
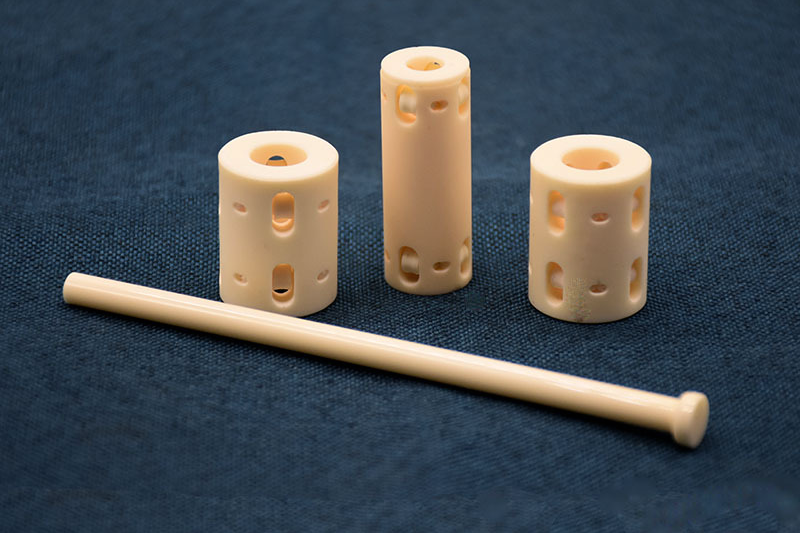
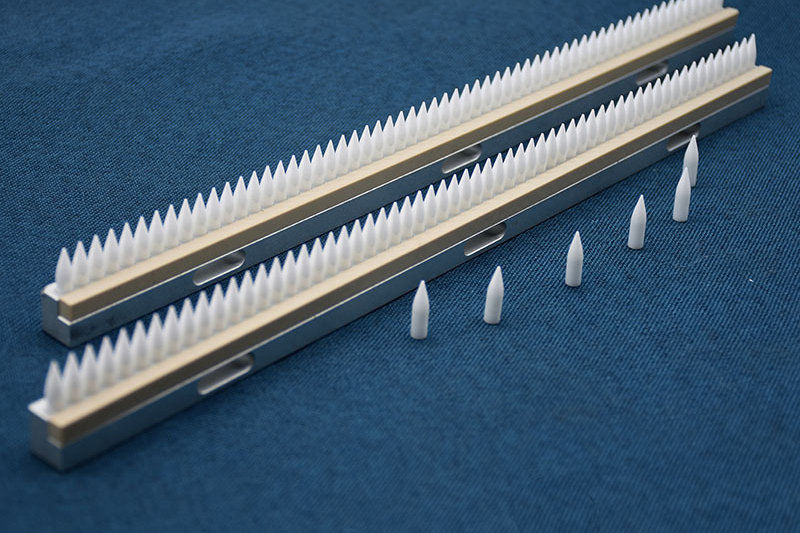
Flexural Strength
The Flexural Strength of CIM-Alumina-Zirconia parts is an impressive 900 MPa, reflecting their ability to withstand bending forces and resist deformation under applied loads. This remarkable flexural strength results from the synergistic properties of alumina and zirconia, which work together to create a material with exceptional mechanical stability.
Alumina-Zirconia CIM parts find crucial applications in industries that demand outstanding Flexural Strength Properties. In the manufacturing sector, these parts are utilized in cutting tools and machining components that endure significant mechanical forces during high-speed operations. In aerospace and defense, alumina-zirconia components excel as structural elements due to their ability to withstand variations in temperature and mechanical stresses. Moreover, these parts contribute to the construction of medical equipment and devices, such as surgical tools and implants, where maintaining shape and function under pressure is essential.
Impact Resistance
The Impact Resistance of CIM-Alumina-Zirconia parts is crucial, allowing them to withstand sudden shocks and impacts without fracturing. This property results from the combination of alumina and zirconia, which contribute to the material's toughness and ability to absorb energy.
Alumina-Zirconia CIM parts find applications in industries where impact resistance is paramount. In the automotive sector, these parts contribute to safety systems, such as airbag deployment mechanisms, where the ability to absorb impact energy is critical. Additionally, in industrial machinery and equipment, alumina-zirconia components are used in components subjected to vibrations and mechanical shocks, ensuring that the parts can endure harsh operating conditions while maintaining their structural integrity.
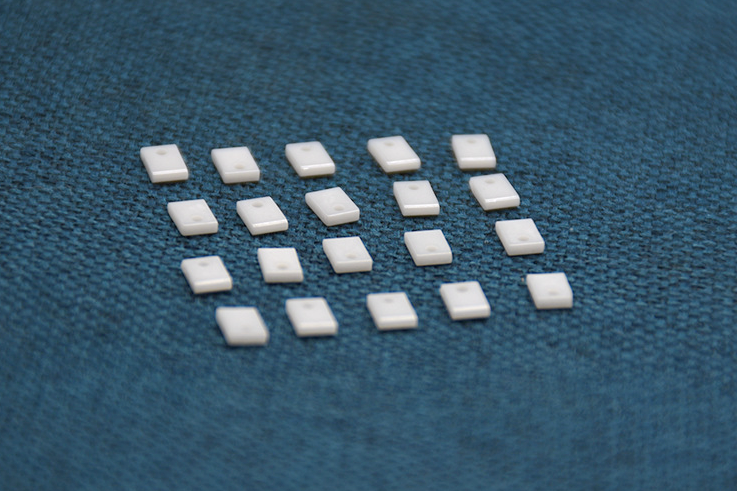
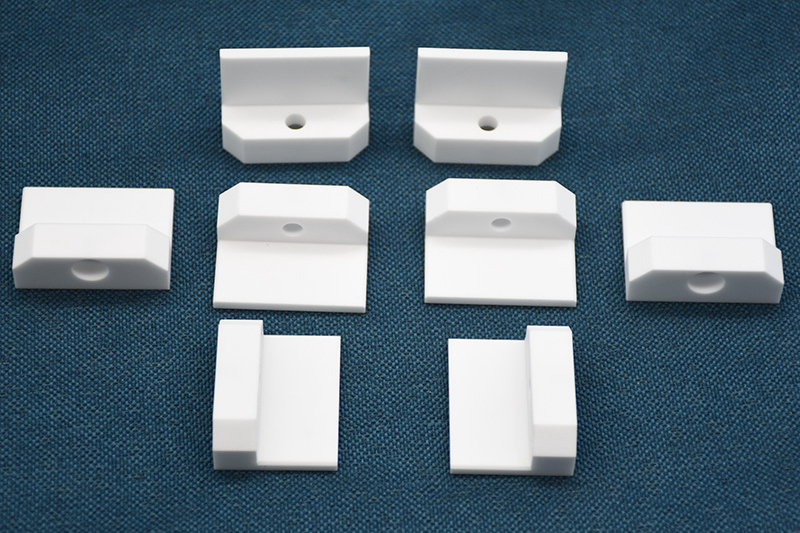
Hardness
The hardness of CIM-Alumina-Zirconia parts is 9 Mohs. This means it is more complex than most metals but softer than some gemstones. The hardness of a material is its resistance to scratching or indentation. CIM-Alumina-Zirconia parts are complex because they have a solid atomic structure. The atoms in the material are tightly packed, making it difficult to be displaced.
The hardness of CIM-Alumina-Zirconia parts makes them ideal for applications where they will be exposed to wear and abrasion. These applications include Bearings, Seals, Cutting tools, Jewelry, and Medical implants. Applications that require Hardness Properties of Alumina-Zirconia CIM parts: Wear-resistant parts: Alumina-zirconia CIM parts are resistant to wear and abrasion, making them ideal for applications where they will be exposed to these conditions. For example, they can be used in bearings and seals.
Thermal Expansion
The Thermal Expansion of CIM-Alumina-Zirconia parts refers to the material's tendency to expand or contract with changes in temperature. Alumina and zirconia exhibit different coefficients of thermal expansion, and their combination in CIM-Alumina-Zirconia parts can help mitigate the effects of thermal expansion mismatch, leading to improved thermal stability.
Alumina-Zirconia CIM parts find applications in industries requiring precise thermal expansion properties. In electronics, these parts are utilized in substrates for electronic devices, where maintaining dimensional stability despite temperature fluctuations is essential for proper functioning. Such as heat sinks are used to dissipate heat from electronic components. The thermal expansion of the heat sink must be matched to the thermal expansion of the electronic components to prevent the heat sink from cracking or deforming.
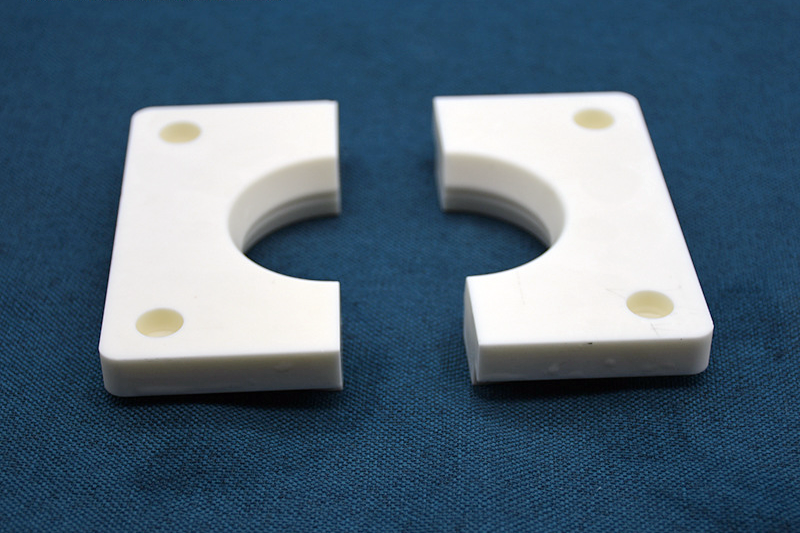
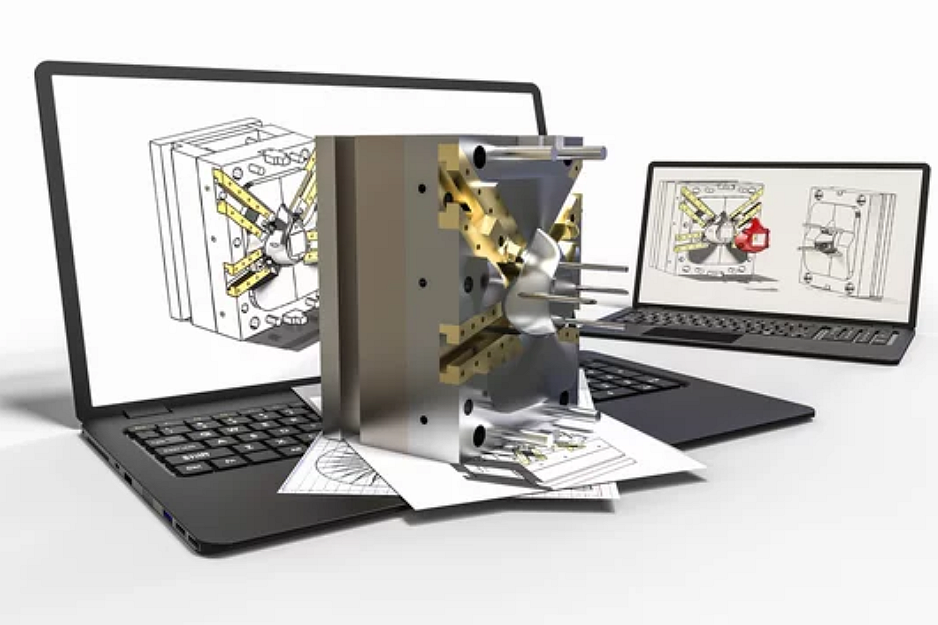
Consultative Design Services
Neway Custom Metal Injection Molding Service provides free Consultative Design Services throughout the process. This includes all processes from your design stage to mass-produced finished products.
1. Material selection Consult
2. Structural design service
3. Mold design service
Contact us now if you are interested.
What We Can Offer?
We offer free material selection and consultative design services from beginning to end. No MOQs, Rapid prototyping, and mass production are our strengths.
评论
发表评论