MIM 316L Metal Injection Molding Service
MIM 316L metal injection molding service combines the high complexity, high precision, and low cost of mass production of plastic injection molding with the excellent physical and chemical properties of 316L-MIM material.
316L MIM parts offer excellent corrosion resistance, strength, and biocompatibility. They are ideal for applications like medical implants, surgical instruments, marine hardware, and chemical processing equipment where durability and corrosion resistance are critical. 316L provides good mechanical properties while maintaining the stainless steel's anti-corrosive benefits.
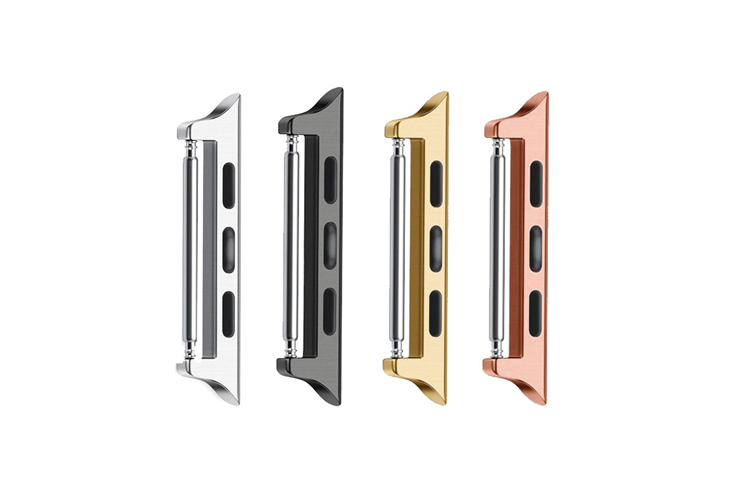
MIM 316L Stainless Steel Typical Properties
MIM 316L Stainless Steel Chemical Composition
Iron (Fe) | Chromium (Cr) | Nickel (Ni) | Molybdenum (Mo) | Manganese (Mn) | Silicon (Si) | Carbon (C) | Phosphorus (P) | Sulfur (S) | |
316L | Balance | 16.5 | 12 | 2.1 | 0.8 | 0.6 | 0.02 | 0.04 | 0.01 |
MIM 316L Stainless Steel Mechanical Properties
Tensile Strength (MPa) | Yield Strength (MPa) | Impact Strength (J) | Hardness (HRB) | Young's Modulus (GPa) | Poisson's Ratio | Elongation (%) | Density (g/cm3) | |
---|---|---|---|---|---|---|---|---|
MIM 316L | 550 | 300 | 130 | 80 | 190 | 0.29 | 40 | 7.9 |
Key Features And Applications of 316L Metal-Injected Parts
Corrosion-Resistant Properties
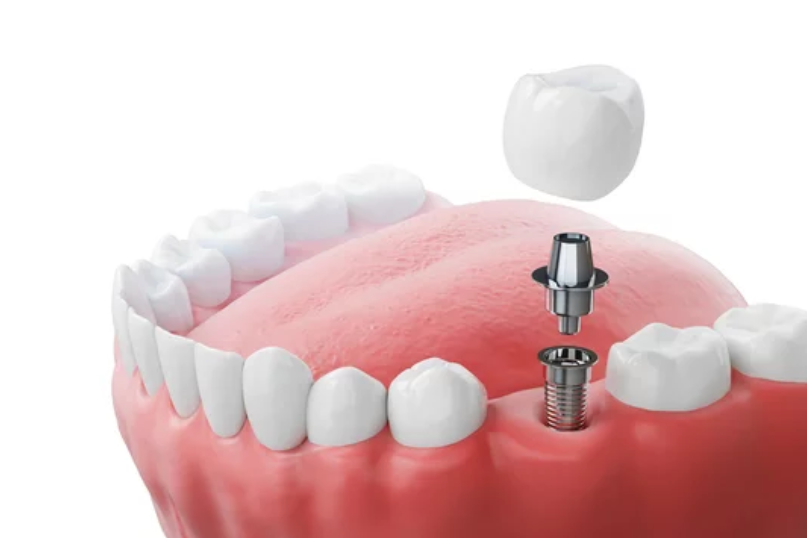
316L stainless steel's corrosion resistance stems from forming a thin, protective layer of chromium oxide on the surface when exposed to oxygen. This passive layer is a barrier, preventing direct contact between the metal and corrosive agents. Additionally, including molybdenum enhances the alloy's resistance to pitting and crevice corrosion, which can occur in chloride-rich environments. This combination of elements creates a robust shield against various corrosive media, including acids, chlorides, and seawater.
316L Metal-Injected Parts are widely used in marine equipment such as valves, pumps, propellers, and underwater structures. Chemical Processing reactors, pipes, tanks, valves, aerospace components, Etc
Weldability
The weldability of 316L-MIM (Metal Injection Molding) Parts is excellent, primarily due to the composition and characteristics of 316L stainless steel. The low carbon content in 316L stainless steel minimizes the risk of sensitization and intergranular corrosion after welding, a common concern in stainless steel. This property makes 316L-MIM Parts less susceptible to weakening at the weld joints. Additionally, the presence of molybdenum enhances the alloy's resistance to corrosion, including pitting and crevice corrosion, even after welding processes. This combination of low carbon content and alloying elements contributes to the weldability of 316L-MIM Parts, making them well-suited for various welding applications.
316L Metal-Injected Parts are used in structural fabrication, Piping Systems, and Automotive parts, particularly in exhaust systems and components that require welding for assembly.
Biocompatibility
The biocompatibility of 316L-MIM (Metal Injection Molding) Parts refers to their ability to interact with living tissues without causing adverse reactions. In medical and healthcare applications, 316L stainless steel exhibits excellent biocompatibility. This property makes 316L-MIM Parts suitable for use within the human body for extended periods without triggering immune responses or harmful effects. The biocompatibility of 316L-MIM Parts is attributed to the alloy's composition, which includes elements like chromium and nickel that contribute to its corrosion resistance and inert behavior within biological environments.
The typical applications include medical Implants such as orthopedic implants (hip and knee replacements), dental implants, and cardiac implants like stents. Surgical Instruments, Dental Prosthetics, Medical Devices
Polishing Properties
316L MIM parts can be highly polished for aesthetics. Metal injection molded 316L parts can be polished and ground for a high-gloss finish. PVD (physical vapor deposition) can obtain various color coatings. This makes 316L MIM parts usable parts for aesthetic purposes.
The typical applications include watch cases, watch bands, and jewelry.
Why Neway for 316L Metal Injection Molding Service
When I needed precision parts for my medical device project, I turned to Neway's 316L Metal Injection Molding (MIM) service. Their 30 years of expertise in custom injection molding assured me of quality. The MIM process they offered ensured intricate designs without compromising material integrity. Their tempting 20% discount for first-time customers made the decision even more accessible. Neway exceeded my expectations with their professionalism and dedication to timely delivering top-notch parts.
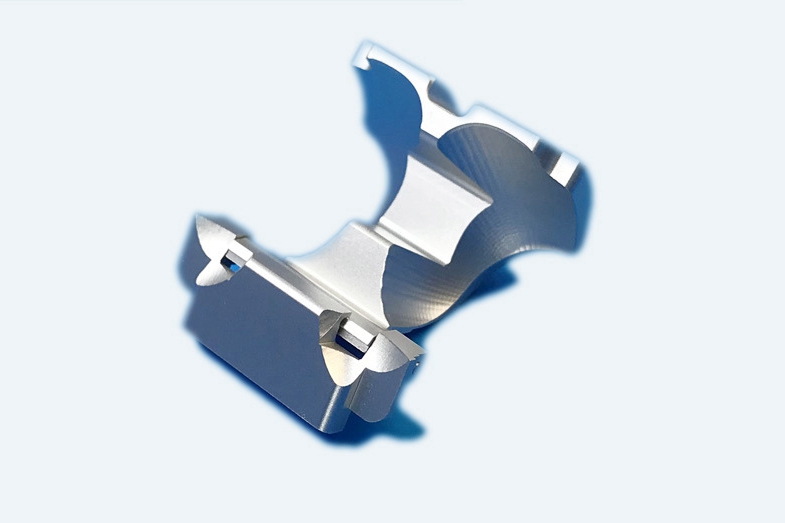
评论
发表评论