Zinc Die Casting Products
Zinc die casting is a popular manufacturing process used to produce a wide range of products, including watch frames and watch cases. The process offers several advantages, such as high dimensional accuracy, excellent surface finish, and the ability to create complex shapes with intricate details.
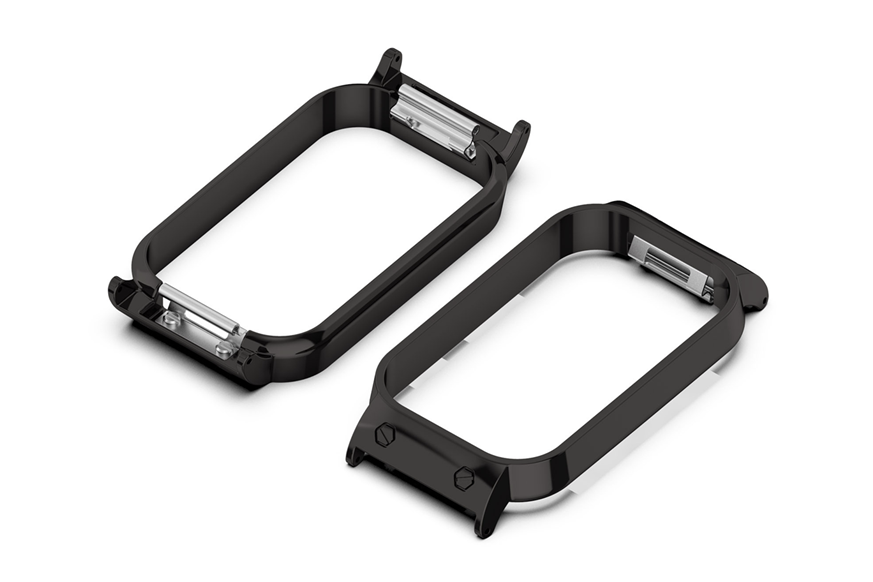
Cast Zinc Watch Frame
Watch Frame Design
The production of a cast zinc watch frame starts with the design phase. Parts designers use computer-aided design (CAD) software to create a detailed model of the watch frame. This model serves as the basis for the subsequent steps in the manufacturing process.
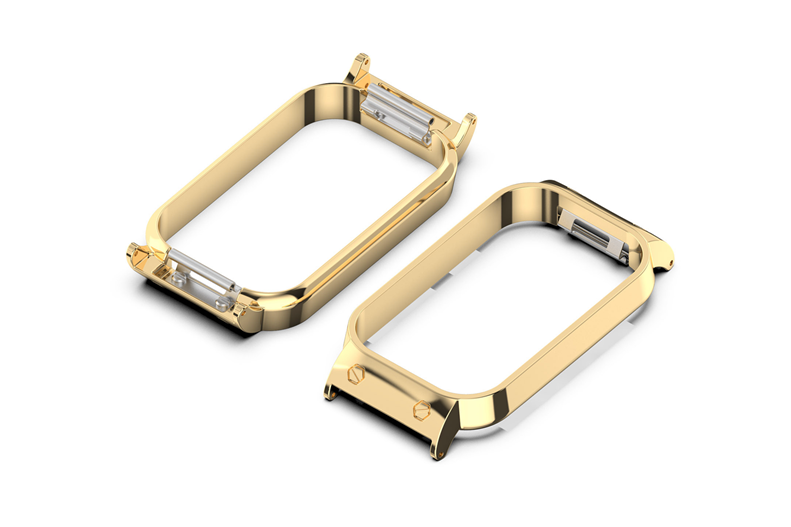
Zinc Cast Mold Preparation
Once the design is finalized, a mold is created. The mold is typically made of high-quality steel and consists of two halves, the "die," which are precisely machined to mirror the desired shape of the watch frame. The mold design incorporates runners and gates, allowing the molten zinc alloy to flow into the mold cavity.
Before the casting process begins, the die casting machine is prepared. The mold is securely installed within the machine, and any residue or contaminants are thoroughly cleaned to ensure the integrity of the casting.
Next, the zinc alloy, which typically combines zinc, aluminum, and copper, is melted in a furnace or melting pot. The temperature is carefully controlled to reach the appropriate range for the specific alloy. Once molten, the zinc alloy is maintained at the desired temperature throughout the casting process.
Injection Molding
The molten zinc alloy is then injected into the mold under high pressure. The pressure is necessary to ensure that the molten metal fills the mold cavity and captures all the intricate details of the watch frame design. The high-pressure injection also helps to minimize any potential porosity or voids in the cast part.
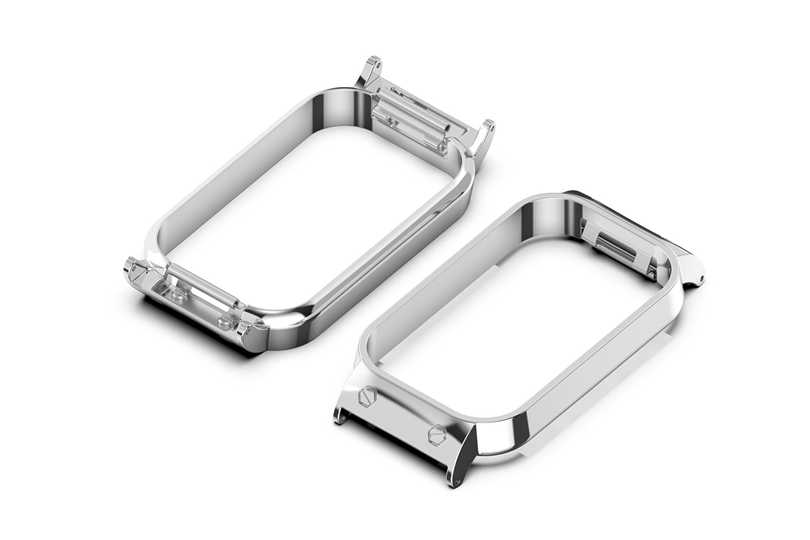
As the molten zinc alloy cools down, it solidifies within the mold, taking on the shape of the watch frame. Natural cooling or cooling systems, such as water channels or air jets, can facilitate the cooling process. Rapid cooling helps to reduce cycle times and enhance productivity.
The mold is opened once the casting has solidified and cooled sufficiently, and the newly formed cast zinc watch frame is ejected. The ejected part may have excess material or imperfections, such as flash or rough edges. These are trimmed or removed through various post-processing techniques to achieve the desired final shape and appearance.
Post Processing
The cast zinc watch frame then undergoes additional finishing processes, such as CNC machining, deburring, polishing, or surface treatments. Deburring removes any remaining rough edges or burrs from the casting, while polishing enhances the surface's smoothness and appearance. Surface treatments, such as plating, coating, or painting, can provide decorative finishes, improve corrosion resistance, or enhance durability.
Quality Inspection
It undergoes rigorous inspections and quality control checks to ensure the quality and accuracy of the cast zinc watch frame. Measurements, visual inspections, and functional tests are performed to verify dimensional accuracy, surface finish, and overall product integrity. This helps ensure that the watch frame meets the required specifications and standards.
Benefits of Die-cast Metal Watch Shell:
A die-cast metal watch shell, often called a watch case, is crucial in housing and protecting the watch's movement and dial. Die-casting offers an efficient and precise manufacturing method for producing watch cases with intricate designs and complex shapes.
Utilizing the die-casting process, a molten metal, such as a zinc alloy, is injected under high pressure into a specially designed mold cavity. This allows for directly replicating detailed features, including recesses, textures, and engravings, onto the watch case.
Zinc Alloy Casting Design Complexity
Zinc alloys are commonly used in die casting due to their favorable properties for manufacturing applications. Zamak is a popular zinc alloy for casting, consisting primarily of zinc, with varying compositions of aluminum, magnesium, and copper.
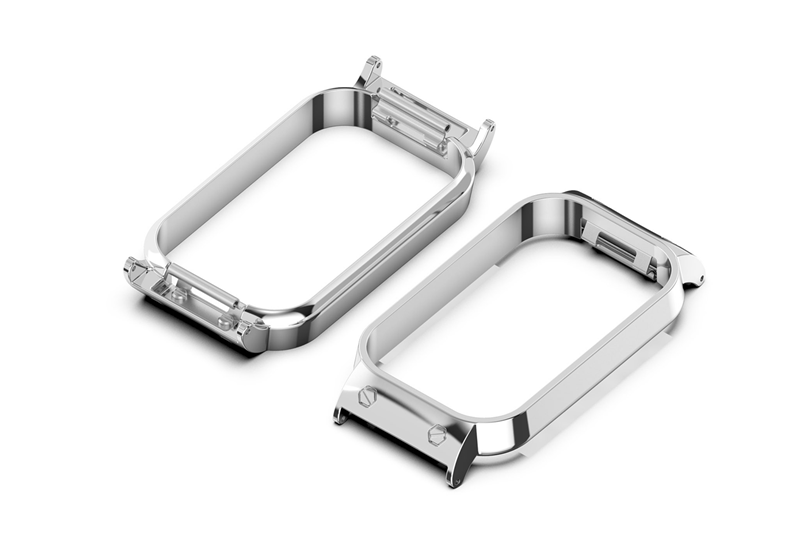
Zamak alloys offer several desirable characteristics for watch case production. They have excellent fluidity when molten, allowing intricate details to be reproduced accurately. Zamak alloys have low melting points, contributing to energy efficiency during the casting process. Furthermore, these alloys exhibit good dimensional stability, ensuring the watch case maintains its shape and form over time.
Zinc Alloy Strength Properties
While zinc is not as vital as other metals, such as steel or titanium, zinc alloys used in die casting, including Zamak, possess sufficient strength for watch case applications. The mechanical properties of zinc alloys can be further enhanced through alloy composition adjustments and heat treatment processes, enabling the production of robust and durable watch cases.
Watch Case Customization Properties
Die casting offers the advantage of creating custom watch cases tailored to specific design requirements. Manufacturers can leverage the versatility of the die-casting process to produce watch cases in various shapes, sizes, and finishes. Customization options extend to the incorporation of intricate patterns, logos, or personalized engravings, allowing for the creation of unique and distinctive timepieces.
The ability to produce custom watch cases through die casting gives watchmakers the freedom to differentiate their products in the market. It enables the creation of limited-edition timepieces or collaborations with artists, designers, or brands seeking to showcase their unique aesthetic vision.
Die-cast metal watch cases provide a protective housing for watch movements and a canvas for creativity, craftsmanship, and brand identity. The precise manufacturing process ensures that custom watch cases are manufactured with high dimensional accuracy, facilitating the seamless integration of other watch components during assembly.
In conclusion, die-cast metal watch cases produced using zinc alloys offer many advantages. They enable the creation of custom watch cases with intricate designs, excellent dimensional accuracy, and robust strength. The versatility of zinc alloys, coupled with the flexibility of the die-casting process, empowers watch manufacturers to produce unique timepieces that reflect their brand identity and meet the preferences of discerning customers.
Considerations of die casting a Zinc Watch Frame
When die casting a zinc watch frame or watch case, several key considerations come into play to ensure the production of high-quality zinc die casting products.
Material Selection
Choosing the suitable zinc alloy for casting is crucial. Zinc alloys commonly used in die casting include Zamak alloys (Zamak 2, Zamak 3, and Zamak 5) and ZA alloys (like ZA-8, ZA-12, and ZA-27). These alloys offer excellent castability, a good surface finish, and a balance of mechanical properties. Consider the specific requirements of the watch frame, such as strength, corrosion resistance, and desired surface finish, when selecting the appropriate zinc alloy.
Mold Design
The mold design is critical in achieving the desired shape, dimensions, and surface finish of the cast zinc watch frame or watch case. It's essential to work closely with experienced mold designers to ensure that the mold correctly captures the intricate details and features of the custom watch case design. The mold should incorporate considerations like draft angles, parting lines, and ejector pin locations for smooth mold release and minimal defects.
Cooling System
Implementing an efficient cooling system within the mold is vital for controlling the solidification process during die casting. Proper cooling helps prevent defects like shrinkage or porosity by ensuring uniform cooling and solidification of the molten zinc alloy. Effective cooling channels or cooling systems, such as water jackets or heat exchangers, can be integrated into the mold design for optimal temperature control.
Gate and Runner Design
Designing the gating and runner system is vital for correctly filling the mold cavity with the molten zinc alloy. Optimize gate locations, sizes, and designs to facilitate the smooth and uniform flow of the molten metal, minimizing turbulence, air entrapment, or flow marks. Careful consideration of the gating and runner design helps prevent defects and ensures the accurate replication of the custom watch case design.
Injection Parameters
Controlling the injection parameters during the die casting process is crucial for achieving quality castings. Parameters such as injection speed, pressure, and shot size should be optimized to ensure complete mold cavity filling and accurate replication of fine details. The specific alloy being used and the geometry and complexity of the watch frame or watch case should be considered when setting these parameters to avoid defects like cold shuts, flow lines, or flashes.
Thermal Management
Maintaining consistent and controlled temperatures throughout the die casting process is essential. Proper thermal management includes:
Maintaining the right temperature for melting the zinc alloy.
Controlling the mold temperature.
Managing the cooling rate during solidification.
Optimal temperature control helps prevent issues like porosity, thermal stress, or distortion in the final cast zinc watch frame or watch case.
Post-Casting Operations
After the casting process, post-casting operations are performed to refine the cast zinc watch frame or watch case. These operations typically include trimming, deburring, and surface finishing. Trimming involves removing excess material or flash from the casting while deburring focuses on removing sharp edges or burrs. Surface finishing techniques like polishing, buffing, or plating can be applied to achieve the desired aesthetics and surface quality.
Quality Control
A robust quality control process is essential to ensure the cast zinc watch frame or watch case meets the required specifications and standards. Regular inspections and testing are conducted to verify dimensional accuracy, surface finish, and mechanical properties. These checks can include dimensional measurements, visual inspections, and mechanical tests like hardness testing or tensile strength testing.
Customization
Die casting allows customizations to create unique watch cases tailored to specific designs or requirements. Custom watch cases can include intricate details, logos, or specific features to reflect the brand.
Identity or customer preferences. Working closely with designers and manufacturers is crucial to translating custom watch case designs into successful die-cast metal watch shells. The flexibility of the die casting process enables the production of custom watch cases with precision and consistency.
Why Choose Neway
Neway offers a wide range of custom zinc alloy parts and the convenience of other metal plastic parts, including free design, design feasibility assessment, feasibility design mold flow analysis, quick proofing, no MOQ, and a 20% discount for the first order of new customers. Please get in touch with us if you are looking for a reliable non-standard parts manufacturer.
评论
发表评论