Introduction to Ceramic Injection Molding
CIM is a sophisticated manufacturing process used across various industries to produce high-precision ceramic parts. Like metal injection molding (MIM) the CIM process combines the capabilities of plastic injection molding and material science, enabling the creation of complex shapes that would be too difficult, expensive, or even impossible to produce using conventional methods.
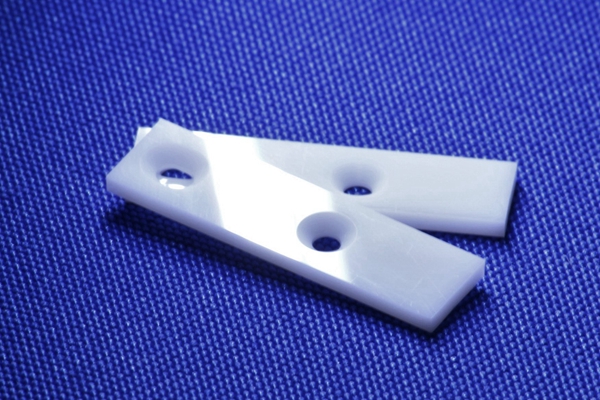
Ceramic Injection Molding Steps
The CIM process involves several stages, each contributing to creating a high-quality ceramic part.
Injection Molding Mold Creating
The ceramic injection molding molds are actually high pressure injection molding molds like a plastic injection molding mold. It is designed and built in-house using CAD/CAM technology, ensuring the ceramic part can be manufactured according to the design drawings. The initial cost of CIM is relatively high due to the presence of injection molds. However, the CIM process is undoubtedly the most cost-effective when producing high-complexity ceramic parts in large quantities.
Ceramic Powder Preparation
The ceramic powder is selected based on the customer's requirements, considering grain size, shape, and distribution factors. The powder is mixed with special binders and additives under carefully monitored conditions to prepare a mixture for injection molding.
Injection molding
Sintered ceramic powders do not have fluidity and injection molding characteristics, but it has fluidity after being mixed with a binder, and its injection molding process is similar to the plastics injection process.
Debinding and Sintering
Binder Removal and Sintering: The binder is removed from the preform through evaporation and an exothermic reaction, leaving only a fraction of the binder behind. The parts sintering in an oxidizing or reducing atmosphere or vacuum. Final collapse to form dense ceramic parts。
Post-Processing
Various processing methods are available for applications that require a certain surface quality or precision that exceed the quality achieved through sintering. Such as CNC machining to create a tight tolerance. Polishing or grinding to form a mirror effect.
The Role of Equipment in CIM
The CIM process requires specialized equipment, including injection molding machines, debinding ovens, and sintering furnaces. These machines play a crucial role in ensuring the production of high-quality ceramic parts.
Injection Molding Machines
These machines are used to fill the raw material into the molds. They require very tight tolerances and wear-resistant components to withstand the abrasive powders.
Debinding Ovens
These ovens remove the binder material from the molded part, leaving behind a pure ceramic part.
Sintering Furnaces
These furnaces heat the part to a high temperature for its final density and strength.
Classification of Ceramic Materials
Ceramic materials, recognized for their elevated melting points, superior hardness, and oxidation resistance, find use in many applications. These are non-metallic inorganic substances derived from either natural or man-made compounds, which are shaped and sintered at high temperatures.
Carbide Ceramics
The main components of cemented carbide ceramics are carbides and binders. The carbides mainly include WC, TiC, TaC, NbC, VC, etc., and the binders are mainly cobalt (Co). Compared with tool steel, cemented carbide has high hardness (up to 87~91HRA), good thermal hardness (excellent wear resistance around 1000°C), and when used as a tool, the cutting speed is 4~7 times higher than that of high speed steel, and the service life is 5 times longer. ~8 times, the disadvantage is that the hardness is too high, brittle, and difficult to be machined, so it is often made into a blade and welded on the tool holder. Carbide is mainly used for machining tools; various molds, including drawing Drawing dies, drawing dies, cold heading dies; various drill bits for mining tools, geological and petroleum development, etc.
Structural Ceramics
The main composition of alumina ceramics is Al2O3, and the available content is more than 45%. Alumina ceramics have various excellent properties. High temperature resistance, generally, can be used for a long time at 1600 ℃, corrosion resistance, high strength, its strength is 2~3 times that of ordinary ceramics, and the highest can reach 5~6 times. Its disadvantage is that it is brittle and cannot accept sudden changes in ambient temperature. It is widely used and can be used as a crucible, engine spark plug, high temperature refractory material, thermocouple casing, sealing ring, etc., and can also be used as a cutting tool and mold.
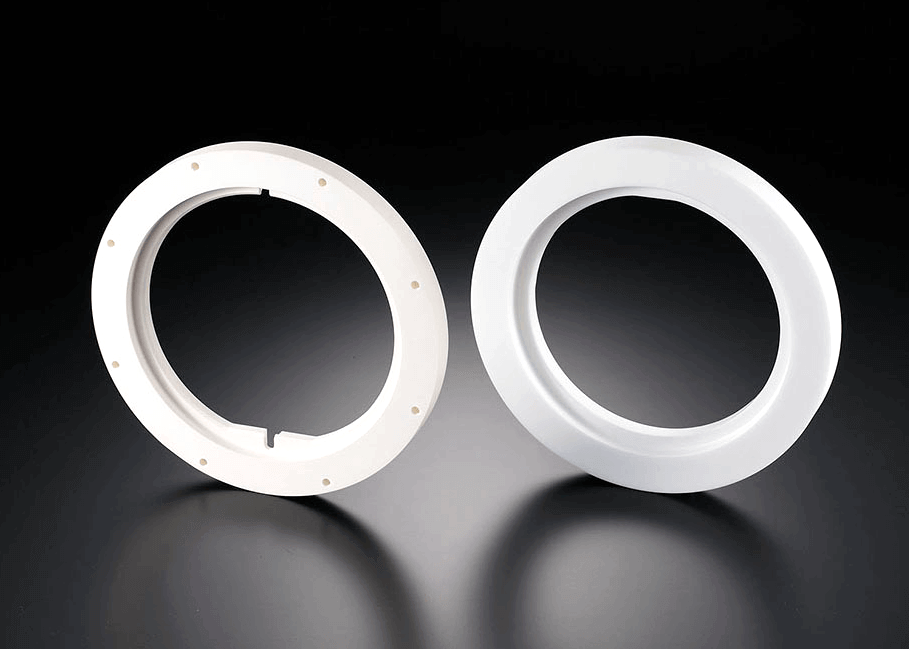
The main component of silicon nitride ceramics is Si3N4, a high-temperature ceramic with high high-temperature strength, hardness, wear resistance, corrosion resistance, and self-lubrication. The coefficient of linear expansion is the smallest among various ceramics, and the service temperature is as high as 1400 ° C. It has excellent corrosion resistance. In addition to hydrofluoric acid, it can resist the corrosion of various acids, alkalis, and metals and has excellent electrical insulation and radiation resistance. They can be used as high temperature bearings, sealing rings used in corrosive media, thermocouple sleeves, and metal cutting tools.
The main component of silicon carbide ceramics is SiC, a high-strength, high-hardness high-temperature-resistant ceramic. It can still maintain high flexural strength when used at 1200 ° C ~ 1400 ° C. It is the ceramic with the highest high-temperature strength. Silicon carbide ceramics also has good thermal conductivity, oxidation resistance, electrical conductivity, and high impact toughness. It is an excellent high-temperature structural material, which can be used for components working at high temperatures, such as rocket tail nozzle, thermocouple casing, furnace tube, etc.; it can be used to make heat exchanger materials at high temperatures by using its high hardness and Wear resistance to make grinding wheels, abrasives, etc.
The main component of hexagonal boron nitride ceramics is BN, and the crystal structure is hexagonal. The structure and performance of hexagonal boron nitride are similar to graphite, called "white graphite." It has low hardness and can be cut with self-lubricating properties. , can be made into self-lubricating high-temperature bearings, glass forming molds, etc.
Functional Ceramics
Functional ceramics usually have unique physical properties and involve many fields. The characteristics and applications of commonly used functional ceramics are shown in the table.
Category | Performance Characteristics | Main Components | Uses |
Dielectric Ceramics | Insulation | Al2O3, Mg2SiO4 | Integrated circuit substrates |
Thermoelectric | PbTiO3, BaTiO3 | Thermistor | |
Piezoelectric | PbTiO3, LiNbO3 | Oscillator | |
High Dielectric | BaTiO3 | Capacitor | |
Optical Ceramics | Fluorescence, Luminescence | Al2O3CrNd Glass | Laser |
Infrared Transparency | CaAs, CdTe | Infrared windows | |
High Transparency | SiO2 | Optical fibers | |
Electrochromic | WO3 | Display | |
Ceramic Magnetics | Soft Magnetic | ZnFe2O, Fe2O3 | Magnetic tape, various high-frequency magnetic cores |
Hard Magnetic | SrO, Fe2O3 | Magnets for audio devices, instruments, and control devices | |
Semiconductor Ceramic | Photoelectric | CdS, Ca2Sx | Solar cells |
Impedance Temperature | VO2, NiO | Temperature sensors | |
Variations | LaB6, BaO | Thermionic emission |
Fine Ceramics
Among ceramic materials, fine ceramics have emerged, which are leading the world of new materials with excellent properties such as high-temperature resistance, super strength, and multi-function. Fine ceramics refer to high-performance ceramics that are sintered with refined high-purity artificially synthesized inorganic compounds as raw materials and sintered by precise control processes, so they are also called advanced ceramics or new ceramics. Many kinds of fine ceramics can be roughly divided into three categories: structural, electronic, and bioceramics.
Electronic Ceramics
Refers to functional ceramics that produce electronic components and structural parts of electronic systems. In addition to mechanical properties such as high hardness, these ceramics can be "indifferent" to changes in the surrounding environment. They have excellent stability, a critical performance for electronic components, and they can withstand high temperatures.
Bioceramics
Bioceramics is a ceramic material used to manufacture the human body's "skeletal-muscle" system to repair or replace human organs or tissues.
Explore the manufacturing of the Mi MIX4 ceramic back shell
The smartphone industry is no stranger to rapid advancements and innovations. One of the most significant transformations we've witnessed is the evolution of smartphone body materials. The materials used in smartphone bodies have significantly evolved from plastic to metal and now to glass and ceramic. This article will explore the Ceramic Injection Molding (CIM) process used in manufacturing the ceramic back shell of the Mi MIX4, a flagship smartphone model from Xiaomi.
Ceramic Smartphone Back Covers: A Blend of Aesthetics and Durability
Ceramic smartphone back covers have been gaining popularity in recent years due to their aesthetic appeal and durability. Xiaomi, a leading player in the smartphone industry, has been at the forefront of this trend. The company introduced the "3D ceramic process" with its flagship model, the Xiaomi 5, which came in two versions - ceramic black and ceramic white.
The Evolution of Smartphone Body Materials: A Journey Towards Innovation
The evolution of smartphone body materials has been swift and significant. We have transitioned from plastic bodies to metal and glass in less than a decade. Recently, ceramic bodies, made possible through the CIM process and the use of a specialized Injection Molding Tool, have gained a larger market share. This evolution is driven by the need for more durable, aesthetically pleasing, and innovative designs.
Xiaomi and Ceramic Technology: Pioneering Change
Xiaomi has played a pivotal role in advancing ceramic technology in the smartphone industry. The company has applied and patented numerous ceramic-related technologies, significantly reducing the cost of ceramic body production. However, the initial investment in the production line was substantial, with only a few percent of the products meeting the quality standards. Despite these challenges, Xiaomi has continued to innovate and improve the manufacturing process of ceramic back covers.
High-Quality Ceramic Parts: The Future of Smartphone Design
Producing high-quality ceramic parts, such as Zirconia and Alumina, has become a crucial aspect of the smartphone industry. These materials are used to produce layered ceramic slabs, which are then used to create the back covers of smartphones. The color ceramic manufacturing process, which includes a complex sintering process, allows for creation of customized ceramic part designs that are both durable and aesthetically pleasing.
Ceramic Injection Molding has revolutionized the smartphone industry, allowing for the production of high-quality, durable, and aesthetically pleasing smartphone back covers. As the industry continues to evolve, we can expect to see more innovations in the design and production of ceramic smartphone parts.
The Manufacturing Process of Ceramic Back Covers
The manufacturing process of ceramic back covers is complex and intricate, involving several stages. One of the key stages is the layering of ceramic slabs.
The layering of Ceramic Slabs
The ceramic back cover of a smartphone is not made from a single piece of ceramic. Instead, it consists of multiple layers of ceramic slabs stacked together. This is particularly true for colored ceramic back covers, where colored ceramic slabs are layered with white ceramic slabs. The white ceramic slabs provide high strength and fracture toughness, ensuring the smartphone back cover is not quickly shattered.
The Role of White and Color Ceramic
The use of white and colored ceramic slabs plays a crucial role in the aesthetic appeal of the smartphone. Before the advent of colored ceramic bodies, black and white were the dominant colors. However, Xiaomi has been investing significant effort in color development in recent years, leading to the introduction of colored ceramic back covers in various hues, including emerald green for the MIX2S (Dunhuang Art Edition) and gemstone blue for the Xiaomi MIX3.
The Sintering Process
The sintering process is another critical stage in manufacturing ceramic back covers. This process involves heating the ceramic slabs at specific temperature ranges for particular durations to increase the ceramic particles' density and reduce the back cover's thickness. The sintering process also helps to eliminate moisture, organic matter, or volatile substances in the ceramic shell, enhancing its density and strength.
The Costs of Ceramic Injection Molding
The initial cost of the CIM process is relatively high, including injection mold cost, injection molding cost, degreasing cost, sintering cost, artificial adult, quality inspection cost, etc.
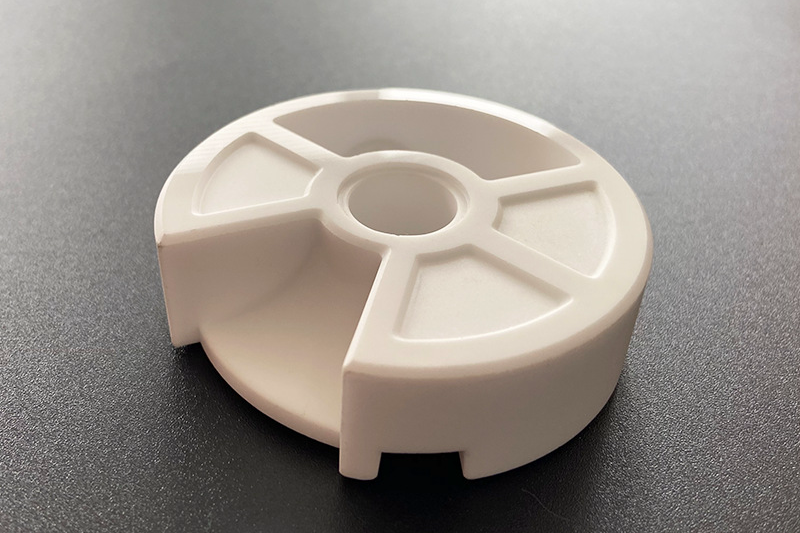
The Future of Ceramic in the Smartphone Industry
Looking ahead, the use of ceramic in the smartphone industry is expected to grow. Ceramics offers several advantages over traditional materials. It does not interfere with electromagnetic waves, making it ideal for wireless communication. Its unique feel and aesthetic appeal also cater to the needs of high-end consumers.
Furthermore, the potential for more color options and designs is vast. Xiaomi has already introduced various color options for its ceramic back covers, and we will likely see even more innovative designs and color combinations in the future.
The Role of Ceramic in Other Electronic Devices
The application of ceramic technology is not limited to smartphones. It can also be used in other electronic devices such as MP3 players, MP4 players, cameras, and smart speakers. As the technology matures and becomes more cost-effective, we can expect to see more electronic devices featuring ceramic components.
Why Choose Neway
For over 30 years, Neway has been a trusted manufacturer of non-standard parts, offering a wide range of services, including metal, ceramic, and plastic injection molding, precision casting, sheet metal processing, and rapid proofing. With our extensive experience and expertise, we consistently deliver exceptional results that meet the highest industry standards. Our commitment to quality, cutting-edge technology, and competitive pricing make us the ideal choice for businesses seeking reliable, cost-effective manufacturing solutions. And as a special promotion for 2023, new customers try Neway with 20% off the first order, providing an excellent opportunity to experience our top-notch service at a reduced cost. Partner with Neway and elevate your manufacturing processes to new heights.
评论
发表评论