Precision casting service refers to a group of metal casting processes capable of producing dimensionally accurate metal parts with tighter tolerances and better surface finishes than conventional casting methods. The tolerance standards achieved depend on the specific casting process used.
This article mainly discusses the tolerance standards of precision casting services that Neway can provide and can be achieved, including die casting, sand casting, and investment casting.
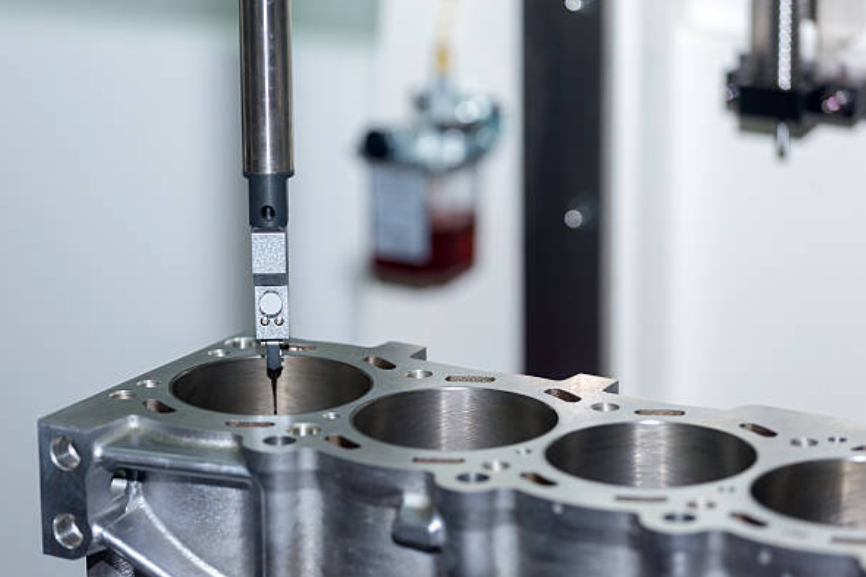
Investment Casting Tolerance Standards
Investment casting service is considered one of the most precise casting processes, capable of tight tolerances down to ±0.005 in (±0.13mm) or even tighter for small castings under four in2. For larger castings, the typical tolerance range is ±0.015 in (±0.38mm) or ±0.5% to ±1% of the nominal dimension.
The wax pattern used in investment casting can be formed to exact dimensions, creating an accurate mold cavity in the ceramic shell. The ceramic shell withstands the forces of molten metal without distortion. Smooth casting surfaces are possible due to the delicate surface finish of the ceramic mold. The directional solidification in the mold also contributes to the process's high dimensional accuracy.
While the base process can reach tolerances of ±0.015 in (±0.38mm), utilizing advanced wax pattern production methods, tighter process controls, and post-casting operations can further improve tolerances. For example, CNC machining wax patterns allows precise patterns. Controlling mold shell thickness, firing temperature, and metal pouring leads to minimal mold distortion. Secondary operations like grinding and machining can achieve ±0.005 in (±0.13mm) tolerance.
Investment Casting Tolerance Standards
Investment Casting Size | Tolerance Standards | ||
Inches | Millimeters | Dimension Tolerance | Dimension Tolerance |
Up to 0.500 | Up to 12.0 | ± .004" | ± 0.10mm |
0.500 to 1.000" | 12.0 to 25.0 | ± .006" | ± 0.15mm |
1.000 to 1.500" | 25.0 to 37.0 | ± .008" | ± 0.20mm |
1.500 to 2.000" | 37.0 to 50.0 | ± .010" | ± 0.25mm |
2.000 to 2.500" | 50.0 to 62.0 | ± .012" | ± 0.30mm |
2.500 to 3.500" | 62.0 to 87.0 | ± .014" | ± 0.35mm |
3.500 to 5.000" | 87.0 to 125.0 | ± .017" | ± 0.40mm |
5.000 to 7.500" | 125.0 to 190.0 | ± .020" | ± 0.50mm |
7.500 to 10.000" | 190.0 to 250.0 | ± .022" | ± 0.57mm |
10.000 to 12.500" | 250.0 to 312.0 | ± .025" | ± 0.60mm |
12.500 to 15.000" | 312.0 to 375.0 | ± .028" | ± 0.70mm |
Each additional inch add | Each additional 25mm add | ± .001" | ± 0.025mm |
Additional Information:
Surface finish to be minimum RMS125√ or better.
Unless otherwise specified: a) Fillet radii to be: .060” MIN. Recommended, .060” MAX. b) Corner radii to be: +/- 0.5 degrees c) Angular tolerance: +/- 0.5 degree
Machining stock 0.040” minimum, if required.
Minimum wall thickness of .030” +/- .010” can be achieved.
Die Casting Tolerance Standards
Die casting service is another metal casting process recognized for its high dimensional accuracy capabilities, owing to reusable metal dies. For small die-cast parts under 1 in (25mm) dimension, tolerance as tight as ±0.005 in (±0.13mm) is possible. The tolerance standards expand for larger parts:
Up to 2 in (50mm): ±0.008 in (±0.20mm)
Up to 4 in (100mm): ±0.015 in (±0.38mm)
Over 4 in: ±0.02 in (±0.51mm)
Generally, ±1% to 2% of the nominal dimension is a standard tolerance benchmark for die-cast parts. Proper die design, precision machining, die spraying techniques, and thermal management are critical to minimize die erosion and distortion during casting. It enables the die to produce castings within tight dimensional standards.
Like investment casting, secondary machining operations can improve die casting tolerances to ±0.005 in (±0.13mm) for high-precision applications like aerospace and automotive components. Die casting is ideal for complex, thin-walled castings like electronic housings, gearboxes, and steering column parts demanding tight tolerances.
Die Casting Size | Tolerance Standards | ||
Millimeter Size | Inch Size | Millimeter Tolerance | Inch Tolerance |
Up to 18 | Up to 0.709" | ± 0.14 | ± 0.0055" |
Over 18 up to 30 | Over 0.709" up to 1.181" | ± 0.27 | ± 0.0106" |
Over 30 up to 50 | Over 1.181" up to 1.969" | ± 0.25 | ± 0.0098" |
Over 50 up to 80 | Over 1.969" up to 3.150" | ± 0.45 | ± 0.0177" |
Over 80 up to 120 | Over 3.150" up to 4.724" | ± 0.6 | ± 0.0236" |
Over 120 up to 180 | Over 4.724" up to 7.087" | ± 0.7 | ± 0.0276" |
Over 180 up to 250 | Over 7.087" up to 9.843" | ± 0.75 | ± 0.0295" |
Over 250 up to 315 | Over 9.843" up to 12.402" | ± 0.8 | ± 0.0315" |
Over 315 up to 400 | Over 12.402" up to 15.748" | ± 0.85 | ± 0.0335" |
Over 400 up to 500 | Over 15.748" up to 19.685" | ± 0.95 | ± 0.0374" |
Over 500 up to 630 | Over 19.685" up to 24.803" | ± 1.1 | ± 0.0433" |
Over 630 up to 800 | Over 24.803" up to 31.496" | ± 1.2 | ± 0.0472" |
Over 800 up to 1000 | Over 31.496" up to 39.370" | ± 1.4 | ± 0.0551" |
Over 1000 up to 1250 | Over 39.370" up to 49.213" | ± 1.6 | ± 0.0630" |
The wall thickness of die-casting parts is generally 2.5~4mm, and parts with a wall thickness of more than 6mm are unsuitable for the die-casting process. Most of the wall thickness of die castings is controlled at 2.0~2.5mm
The fillet radius R of die castings is generally not less than 1mm. The minimum is 0.5mm, and generally, R=1.5mm
The surface roughness of the aluminum alloy die-casting process is generally Ra3.2~6.3
Sand Casting Tolerance Standards
Sand casting service is a lower-cost process than investment and die casting, offering more relaxed tolerance standards, typically ±0.125 in (±3mm) or ±2% of the nominal dimension. The variability stems from molding sand properties, manual mold forming, uneven ramming, and erosion from hot molten metal.
However, process refinements can shrink sand casting tolerance to ±0.06 in the (±1.5mm) range for small to medium castings under 12 (300mm). Chemical bonding processes like sodium silicate bonding help create more complicated, stable molds. Mold coatings prevent metal penetration and burn-on defects. Match plates and tighter process control also improve tolerances.
While not matching investment and die-casting precision, sand casting is significantly cheaper per part for medium to high production runs. When dimensional accuracy in the ±0.06 in (±1.5mm) range is acceptable, sand casting becomes an economical choice for automotive, machinery, and construction parts.
Sand Casting Size | Tolerance Standards | ||
Millimeters | Inches | Dimension Tolerance (mm) | Dimension Tolerance (in) |
0 + to 175 | 0 + to 7.000 | ± 0.53 | ± 0.021 |
175 + to 200 | 7.000 + to 8.000 | ± 0.58 | ± 0.023 |
200 + to 250 | 8.000 + to 10.000 | ± 0.63 | ± 0.025 |
250 + to 300 | 10.000 + to 12.000 | ± 0.68 | ± 0.027 |
300 + to 350 | 12.000 + to 14.000 | ± 0.73 | ± 0.029 |
350 + to 400 | 14.000 + to 16.000 | ± 0.78 | ± 0.031 |
400 + to 450 | 16.000 + to 18.000 | ± 0.83 | ± 0.033 |
450 + to 500 | 18.000 + to 20.000 | ± 0.88 | ± 0.035 |
500 + to 550 | 20.000 + to 22.000 | ± 0.93 | ± 0.037 |
550 + to 600 | 22.000 + to 24.000 | ± 0.98 | ± 0.039 |
600 + to 650 | 24.000 + to 26.000 | ± 1.03 | ± 0.041 |
Each Additional 25mm | Each Additional Inch | ± 0.025mm | ± 0.001" |
Post Processing Tolerance
Non Functional Dimensions
50% Additional Tolerance up to 5.000" .125mm
33% Additional Tolerance above 5.000" .125mm
Wall Thickness Tolerance: ± .008" - ± 0.20mm Straightness/Flatness Tolerance: .004" per in. –0.10mm per 25mm, excluding localized pattern depressions
Angular Tolerance: ± _° UP to 3" – 75mm
Typical Surface Finish
- 80 MICROINCHES
- 2.0 MICROMETRES
We would advise that the above tolerances be incorporated into your drawings immediately. Dimensions requiring close tolerances should be discussed with Neway’s Technical Sales.
Try Us at a 20% Discount
Tired of casting and molding companies that need help getting it right? Break out of the old rut and into Neway's arms! For 30 years, we've been delivering quality castings, molds, and sheet metal that are second to none. Our experience shows in the parts we produce. And just for you newbies, we're offering 20% off your first order so you can free yourself from mediocrity. Give Neway a shot, and we promise you'll never look back!
评论
发表评论