Custom Injection molding Service
Custom injection molding is the process of producing plastic, metal, or ceramic parts by injecting molten plastic material, metal powders, or ceramic powders into a mold that has been custom-made to the specifications of a unique part design. Unlike standard, off-the-shelf injection molds, custom molds are engineered and machined to precisely match each new plastic part's required shape, size, geometries, features, and tolerances.
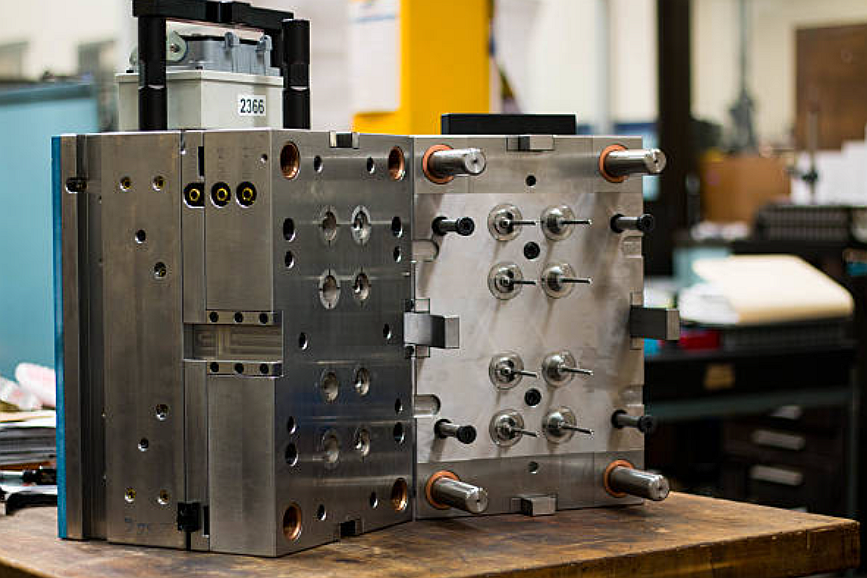
Neway mainly provides the following three kinds of custom injection molding services:
Metal Injection Molding (MIM) Service
Metal injection molding service: Metal injection molding is a versatile manufacturing process that allows the high-volume production of complex, high-precision metal parts. Some of the main benefits of MIM include the ability to produce small, intricate geometries that are difficult with other methods; producing near-net-shape parts to tight tolerances of ±0.3% while minimizing material waste; and the capacity to manufacture small, precision components in high volumes economically. MIM also enables work with various MIM alloys, including stainless steel, titanium, and magnetic alloys. The automation and repeatability of MIM make it an ideal solution for medical, aerospace, automotive, and electronics applications requiring millions of precision small metal parts.
Ceramic Injection Molding (CIM) Service
Ceramic injection molding service: Ceramic injection molding provides a cost-effective method to manufacture high volumes of complex, high-performance ceramic components. CIM's benefits include producing intricate geometries with tight tolerances, minimizing material waste, and achieving superior finishes. CIM enables working with advanced ceramic materials like zirconia, alumina, and macro that would be difficult to machine. The process facilitates mixing varied ceramics to engineer parts with unique mechanical, thermal, and electrical properties. CIM is ideal for automotive, aerospace, and electronics requiring precision, small ceramic components in the millions.
Plastic Injection Molding Service
Plastic injection molding services: Plastic injection molding enables high-volume production of intricate plastic parts with excellent repeatability, efficiency, and precision. Vast material selection, including thermoplastics, thermosets, and elastomers; a variety of finishing options such as textures, colors, and coatings; Injection molding design flexibility, quality, and economical high-volume production, plastic injection molding is ideal for manufacturing precise plastic components and products across many industries. And it has a variety of injection molding types, such as: Insert molding, Overmolding, Multi-shot injection molding, and Gas-Assisted Injection Molding. They have different benefits.
Neway Custom Injection Molding Capabilities
Standard | Metal Injection Molding (MIM/CIM) | Plastic Injection Molding |
Max custom part size | 200×200×80 mm | 2000×2000×500 mm |
7.8×7.8×3.1 in. | 79×79×40 in. | |
Min custom part size | 1×2×2 mm | 1×3×3 mm |
0.04×0.08×0.08 in. | 0.04×0.12×0.12 in. | |
Min wall thickness | 0.4 mm | 0.6 mm |
0.012 in. | 0.02 in. | |
Max wall thickness | 6 mm | 8 mm |
0.2 in. | 0.3 in. | |
Min net weight | 0.1 g | 0.3 g |
Cost-effective Max weight | ≤ 50 g | ≤ 5000 g |
Max net weight | 250 g | 15000 g |
Precision design reference | 0.3 % part size | 0.4 % part size |
Min tolerance | ± 0.02 mm | ± 0.06 mm |
Cost-effective MOQ | N/A | N/A |
评论
发表评论