Heat treatment is a critical metallurgy process involving heating and cooling materials to alter their physical and mechanical properties. This technique is vital in various industries, including automotive, aerospace, construction, tool and die, and the medical sector. Heat treatment can enhance their hardness, strength, toughness, ductility, and other desirable characteristics by subjecting materials to controlled heating and cooling cycles. This article will explore the basics of heat treatment, the different processes involved, and its wide-ranging applications in modern manufacturing processes.
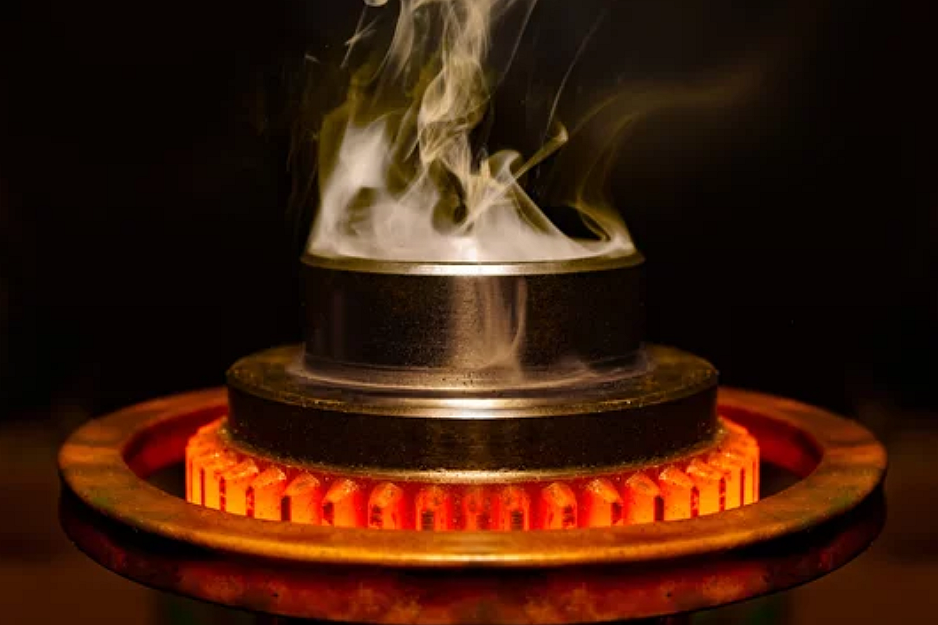
Basics of Heat Treatment
Heat treatment can be defined as a series of controlled heating and cooling operations applied to solid metals and alloys. The primary purpose of heat treatment is to optimize the mechanical properties of a material, such as its hardness, strength, and ductility, to suit specific applications. Several critical parameters influence the heat treatment process, including temperature, heating and cooling rates, and duration. By manipulating these factors, heat treatment can achieve the desired material properties. Different from spraying processes such as Physical Vapor Deposition (PVD) and powder coating, heat treatment is a surface treatment process that changes the mechanical and physical properties of the substrate itself by heating and cooling.
Heat Treatment Processes and Applications
Annealing Process and Applications
Annealing is a widely used heat treatment process that involves heating a material to a specific temperature and then cooling it slowly. Annealing aims to reduce internal stress, improve ductility, and enhance the material's machinability. There are several types of annealing techniques employed in different applications:
1. Full annealing: This type involves heating the material to a temperature above its critical range and allowing it to cool slowly in a furnace. Full annealing helps in achieving maximum softness and refining the grain structure.
2. Process annealing: Process annealing is performed on cold-worked materials to restore their ductility. The material is heated to a temperature below its critical range and then cooled slowly.
3. Stress relief annealing: Stress relief annealing is carried out to minimize residual stresses in a material. The process involves heating the material to a specific temperature and then cooling it slowly to relieve internal stresses.
4. Spheroidizing annealing: Spheroidizing annealing softens high-carbon steels and enhances their machinability. It involves heating the material to a temperature below its critical range and cooling it slowly to produce spherical carbides.
Annealing applications
1. Automotive Industry:
Annealing is extensively used in the automotive industry for heat treatment various components. Engine parts such as crankshafts, connecting rods, and camshafts undergo annealing to enhance their mechanical properties. Annealing helps reduce internal stresses, improve ductility, and refine the grain structure of these components, making them more durable and resistant to wear and fatigue.
2. Aerospace Industry:
In aerospace, annealing plays a crucial role in the heat treatment of materials used in aircraft structures, turbine components, and landing gears. These materials, such as aluminum, titanium, and superalloys, undergo annealing to relieve internal stresses and improve their mechanical properties. Annealing helps enhance the strength, toughness, and resistance to high temperatures, ensuring the reliability and safety of aerospace components.
3. Construction Industry:
Annealing is employed in the construction industry to heat the steel used in structural components. Steel beams, columns, and reinforcement bars are often annealed to improve their strength, ductility, and weldability. Annealing also helps reduce residual stresses formed during the fabrication process, ensuring construction materials' structural integrity and longevity.
4. Tool and Die Industry:
In the tool and die sector, annealing plays a crucial role in the heat treatment of various tooling components. Cutting tools, dies, molds, and punches undergo annealing to improve their hardness, wear resistance, and toughness. Annealing helps refine the microstructure of tool steels, making them more suitable for high-speed machining, forming, and precision applications.
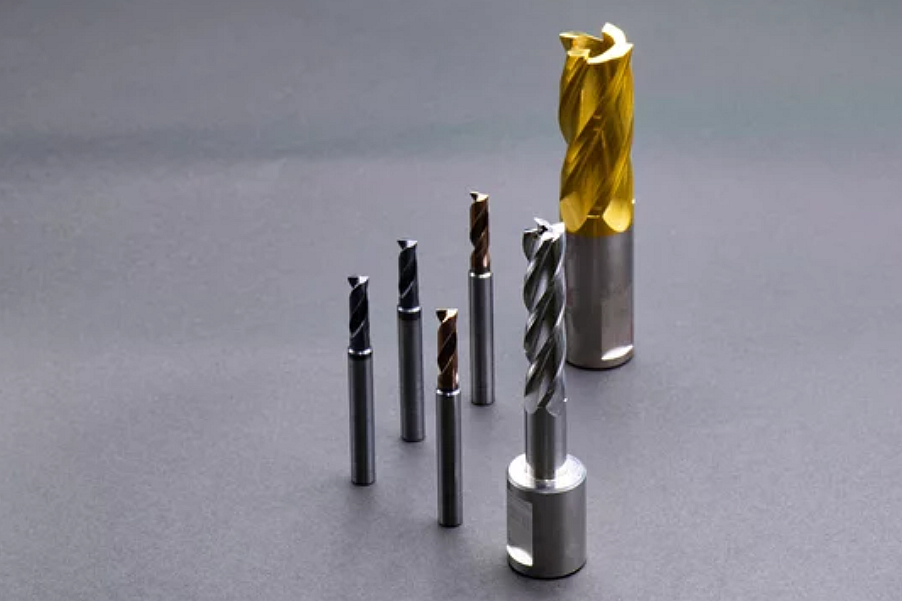
5. Medical Industry:
Annealing is used in the medical industry to heat treatments for implants, surgical instruments, and medical devices. Stainless steel and titanium alloys used in these applications undergo annealing to improve their biocompatibility, corrosion resistance, and mechanical properties. Annealing ensures the implants have the desired strength, ductility, and resistance to wear and fatigue, providing safe and effective medical solutions.
6. Electronics Industry:
In electronics, annealing plays a vital role in the heat treatment of semiconductor materials. Silicon wafers, for example, undergo annealing to remove defects, improve crystal structure, and enhance the electrical properties of the material. Annealing helps optimize the performance and reliability of electronic devices such as transistors, diodes, and integrated circuits.
Hardening Process and Applications
Hardening is a heat treatment process that aims to increase the hardness and strength of a material. It involves heating the material to a specific temperature and then rapidly cooling it, often using a quenching medium such as water, oil, or air. Different hardening techniques are employed based on the desired properties and the type of material being treated:
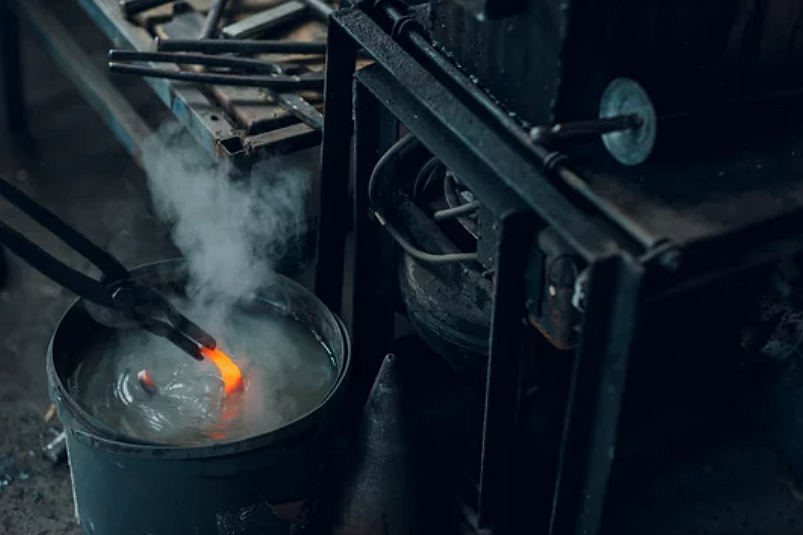
Martensitic Hardening
Martensitic hardening is commonly employed for high-carbon steels. This hardening technique involves heating the material to a temperature above its critical range and then quenching it rapidly to obtain a hard, brittle structure known as martensite. The applications of martensitic hardening are widespread, particularly in industries where high hardness and wear resistance are desired. Some notable applications include:
1. Cutting Tools: Martensitic hardening is extensively used in manufacturing cutting tools such as drills, milling cutters, and lathe tools. These tools require high hardness to withstand the abrasive forces encountered during machining operations.
2. Gear and Bearing Components: Martensitic hardening is crucial for gear and bearing components that operate under high loads and require excellent wear resistance. Hardened gears and bearings can withstand heavy loads and maintain their integrity even under demanding conditions.
3. Blades and Knives: Martensitic hardening is commonly employed in producing blades and knives in various industries, including the culinary, woodworking, and industrial sectors. Hardened blades and knives offer superior cutting performance and durability.
Austempering
Austempering is a hardening technique that involves quenching the material into a bath maintained at a specific temperature. This process results in the formation of a bainitic structure, which offers a balance between hardness and toughness. The applications of austempering include:
1. Automotive Components: Austempering is widely used in the automotive industry to produce crankshafts, camshafts, and axle shafts. These components require high strength, toughness, and fatigue resistance, making them suitable for demanding automotive applications.
2. Machine Components: Austempered steel manufactures gears, shafts, and springs. These components must possess high strength, good fatigue resistance, and shock absorption properties.
3. Railway Components: Austempering produces critical railway components such as axle shafts and suspension system parts. These components must withstand heavy loads, cyclic stresses, and harsh operating conditions.
Induction Hardening
Induction hardening is a surface hardening technique that selectively hardens specific material areas. This process involves using high-frequency induction heating to rapidly heat the material's surface and then quenching it. The applications of induction hardening are found in the following:
1. Automotive Industry: Induction hardening is commonly used to harden various automotive components such as camshafts, crankshafts, and gears. The hardened surfaces provide superior wear resistance and extend the lifespan of these critical components.
2. Machine Tool Industry: Induction hardening is employed in the manufacturing of machine tool components, including guides, ways, and slides. The hardened surfaces minimize friction, reduce wear, and ensure smooth operation and accuracy.
3. Railway Industry: Induction hardening is applied to railway components such as rails and wheels to enhance their wear resistance and extend their service life. The hardened surfaces reduce the wear and tear caused by heavy loads and frequent use.
Flame Hardening
Flame hardening is a surface hardening method that involves heating the material's surface with a high-temperature flame and then quenching it. This process creates a hardened layer while retaining the core's toughness. The applications of flame hardening are found in the following:
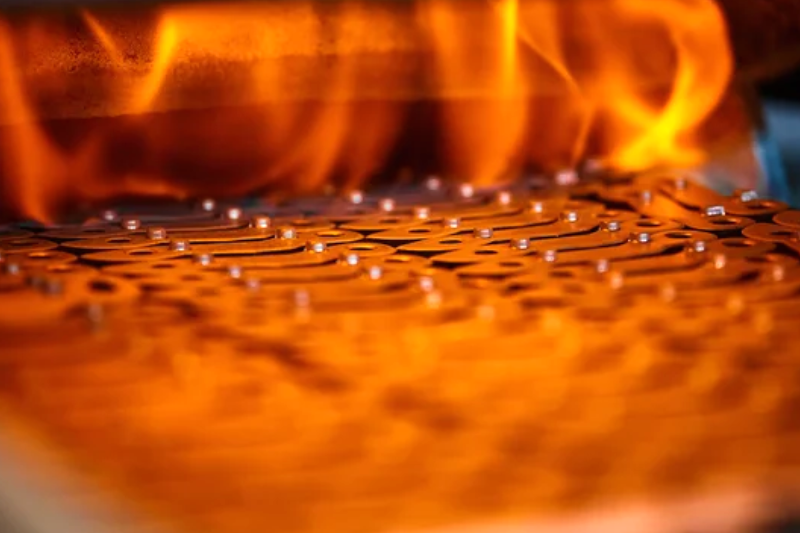
1. Agricultural Machinery: Flame hardening is utilized for the hardening of components used in agricultural machinery, including tillage tools, plowshares, and harrow discs. The hardened surfaces provide excellent wear resistance, ensuring longevity and efficient operation in harsh soil conditions.
2. Mining and Construction Equipment: Flame hardening produces wear-resistant components for mining and construction equipment. Hardened surfaces on parts such as buckets, teeth, and blades withstand the abrasive forces encountered in these demanding applications.
3. Tooling Industry: Flame hardening finds application in manufacturing various tooling components such as dies, punches, and molds. The hardened surfaces enhance the durability and resistance to wear, allowing these tools to withstand repeated use and maintain their sharpness.
Tempering
Tempering is a heat treatment process after hardening to reduce brittleness and improve the material's toughness. It involves reheating the hardened material to a specific temperature and cooling it slowly. Different tempering techniques are employed based on the desired properties:
Low-Temperature Tempering
Low-temperature tempering involves reheating the hardened material to a temperature below 350°C. This process helps reduce brittleness and improve toughness. The applications of low-temperature tempering include:
1. Cutting Tools: Low-temperature tempering is applied to cutting tools such as drills, milling cutters, and taps. It helps improve the toughness of the cutting edges while maintaining a high level of hardness. This combination of properties enhances the tool's ability to withstand high cutting forces and resist chipping or breakage.
2. Springs: Springs, including those used in automotive suspensions or industrial machinery, undergo low-temperature tempering. This process helps increase their flexibility and resistance to fatigue, ensuring they can withstand repeated cycles of compression and extension without failure.
3. Fasteners: Low-temperature tempering is employed for bolts and screws. It helps enhance their toughness, allowing them to withstand high tightening torques and resist brittleness or fracture during service.
Medium-Temperature Tempering
Medium-temperature tempering involves reheating the material between 350°C and 500°C. This tempering technique provides a balance between hardness and toughness. The applications of medium-temperature tempering include:
1. Automotive Components: Medium-temperature tempering is commonly employed in the automotive industry for components such as transmission gears, shafts, and engine parts. It helps achieve the strength, hardness, and toughness necessary for reliable and durable performance.
2. Tool and Die Components: Medium-temperature tempering is used for tool and die components such as punches, dies, and molds. It helps improve their toughness while maintaining sufficient hardness to withstand high working pressures and resist wear.
3. Structural Steel: Medium-temperature tempering is applied to structural steel used in construction and machinery. It helps improve the material's toughness, allowing it to withstand dynamic loads, impact forces, and vibration.
High-Temperature Tempering
High-temperature tempering involves reheating the material to a temperature above 500°C. This process is used to reduce hardness and increase toughness. The applications of high-temperature tempering include:
1. Welded Structures: High-temperature tempering is often used for welded structures to relieve residual stresses that may have formed during welding. This tempering technique helps reduce the risk of cracking or distortion, ensuring the structural integrity of welded components.
2. Springs and Suspension Systems: High-temperature tempering is applied to springs and suspension systems, especially in the automotive and aerospace industries. It helps increase their toughness and resistance to fatigue while maintaining the desired flexibility and load-bearing capacity.
3. Machinery Components: High-temperature tempering is utilized for machinery components subjected to high loads and impact forces. It improves the material's toughness, reducing the risk of brittle fracture or failure under demanding operating conditions.
Case Hardening
Case hardening is a heat treatment process used to create a rigid, wear-resistant outer layer on the surface of a material while maintaining a tough core. It involves introducing carbon, nitrogen, or both into the material's surface and then heat treating it. Different types of case hardening techniques are employed based on the desired characteristics:
Carburizing
Carburizing is a widely used case hardening technique that introduces carbon into the material's surface by exposing it to a carbon-rich atmosphere at high temperatures. This process forms a hard outer layer of high-carbon steel while retaining the core's toughness. The applications of carburizing include:
1. Gears and Gear Components: Carburizing is extensively employed in producing gears and gear components. The hardened outer layer provides excellent wear resistance, ensuring smooth and efficient power transmission in various automotive, aerospace, and industrial machinery industries.
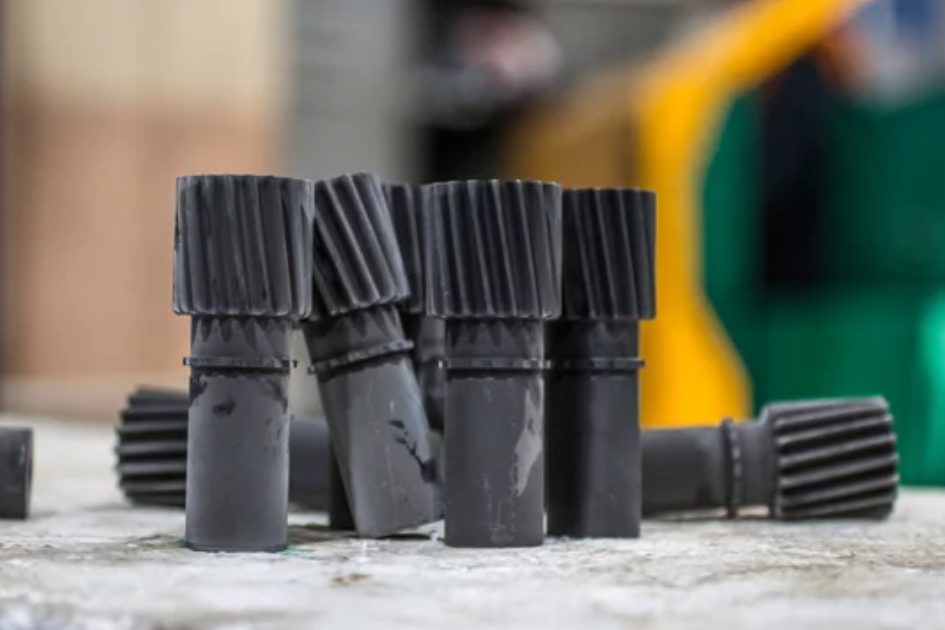
2. Bearings: Carburizing is applied to produce bearing components such as raceways and rolling elements. The hardened surface enhances the bearings' wear resistance and load-bearing capacity, enabling them to withstand high speeds and heavy loads.
3. Tools and Cutting Equipment: Carburizing is utilized to manufacture tools and cutting equipment such as drills, milling cutters, and punches. The hardened surface allows these tools to maintain sharp edges, resist wear, and endure high-speed cutting and machining operations.
Nitriding
Nitriding is a case hardening technique introducing nitrogen into the material's surface. It is commonly used for alloy steels, producing a hard nitride layer that enhances wear resistance. The applications of Nitriding include:
1. Automotive Components: Nitriding is extensively employed in the automotive industry for crankshafts, camshafts, and valves. The nitride layer formed during the process provides exceptional wear resistance, improving the durability and reliability of these critical engine parts.
2. Extrusion Dies: Nitriding is applied to produce extrusion dies in the metalworking industry. The nitride layer increases the die's resistance to abrasion and extends its lifespan, ensuring accurate and high-quality extruded products.
3. Injection Molding Components: Nitriding finds application in manufacturing injection molding components, including molds and inserts. The nitride layer enhances these components' surface hardness and wear resistance, enabling them to withstand the repeated molding cycles and harsh conditions encountered in the plastics industry.
Carbonitriding
Carbonitriding is a case hardening technique introducing carbon and nitrogen into the material's surface. This process combines hardness, wear resistance, and core toughness. The applications of carbonitriding include:
1. Automotive and Motorcycle Components: Carbonitriding is extensively used in the automotive and motorcycle industries for components such as crankshafts, connecting rods, and transmission gears. The carbonitrided surface layer offers superior wear resistance, ensuring reliable performance under high loads and demanding conditions.
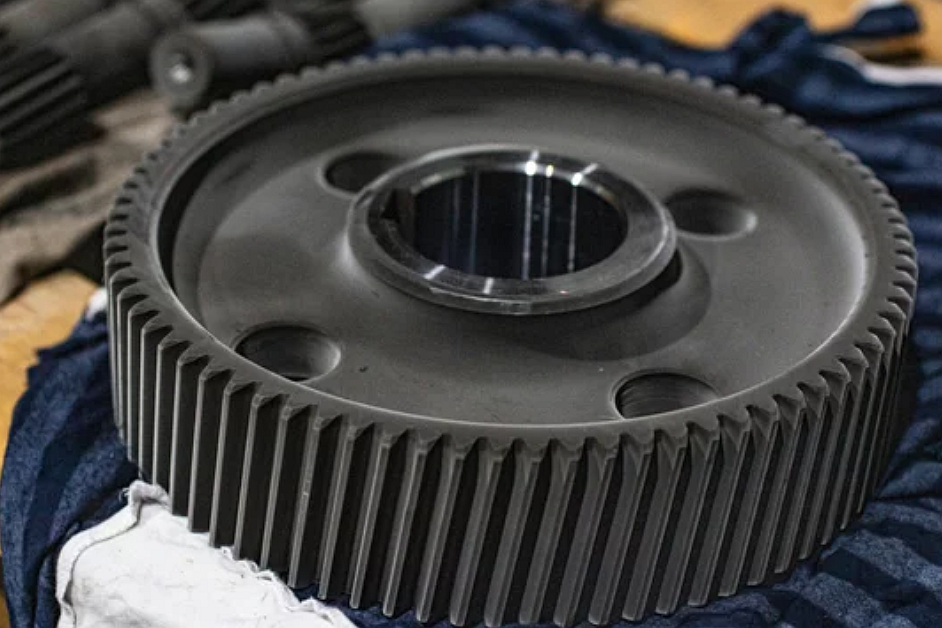
2. Machine Tool Components: Carbonitriding is applied to produce machine tool components such as slides, ways, and guides. The hardened surface provides excellent wear resistance, reducing friction and ensuring precise and smooth movement in machine tools.
3. Surgical Instruments: Carbonitriding finds application in the medical industry for producing surgical instruments. The hardened and wear-resistant surface enhances the durability and performance of instruments used in various surgical procedures.
Other Surface Hardening Processes
Hard anodizing is a surface hardening treatment process for aluminum alloys, which can form a dense aluminum oxide film on the surface of the aluminum alloy substrate. This process can increase the surface hardness of the part and form a variety of colors.
Conclusion
Heat treatment is a fascinating and indispensable process in modern manufacturing. It involves the controlled heating and cooling of materials to optimize their mechanical properties, such as hardness, strength, and ductility. With various processes like annealing, hardening, tempering, and case hardening, heat treatment offers a wide range of possibilities to tailor materials to specific applications. The importance of heat treatment cannot be overstated from the automotive and aerospace industries to the construction, tool and die, and medical sectors. As technology continues to evolve, we can expect further advancements and innovations in heat treatment, opening up new possibilities for the materials and products of the future. So, the next time you encounter a durable, high-performance object, remember that heat treatment might be the secret behind its exceptional qualities.
评论
发表评论